This EDIS document addresses the concern for transporting pesticides that are regarded as hazardous materials by the Secretary of Transportation. This document is specifically written to provide information for those who are in the pest control service industry. A similar EDIS document also exists that addresses the transport of hazardous materials by farmers and ranchers, which can be found at https://edis.ifas.ufl.edu/pi197.
Introduction
Some pesticides are considered by the US Department of Transportation (DOT) to be hazardous materials. A hazardous material is a substance or material which has been determined to be capable of posing an unreasonable risk to health, safety, and property when transported in commerce. Transporting any hazardous material can be risky, so regulations have been established to protect transporting employees, people around them, and the environment. The regulations inform shippers how to package the materials safely and drivers how to load, transport, and unload the material. Shippers and manufacturers communicate the risk by putting hazard warning labels on packages, providing proper shipping papers, emergency response information, and placards on transportation vehicles and vessels.
How do I know if these regulations apply to me?
The first step is to determine whether you are transporting hazardous materials. The DOT is a good source of information because it has identified those hazardous materials and substances that potentially cause an unreasonable risk to health, safety, and property when transported. There are several ways to identify whether the pesticides you transport are hazardous materials:
-
The product's packaging will identify it as a hazardous material. Most noticeably, the packaging will contain one or more diamond-shaped DOT labels. These are known as a "square-on-point;" and there will also be a number listed at the bottom of the point (Figure 1). These numbers represent the DOT hazard classification according to their system (Table 1).
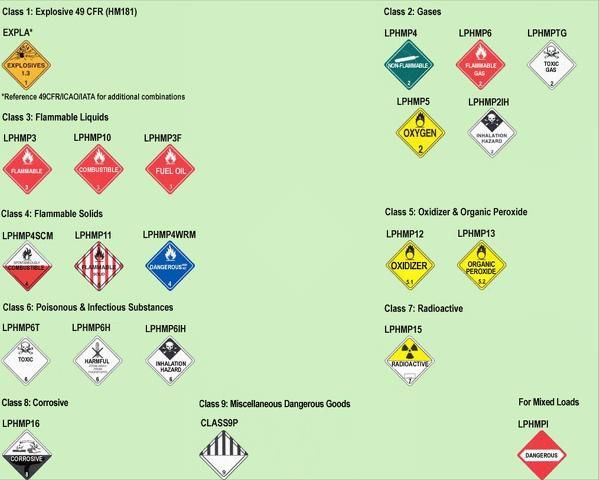
-
Check the "Transportation Information" on the Safety Data Sheet (SDS). See example shown in Figure 2.
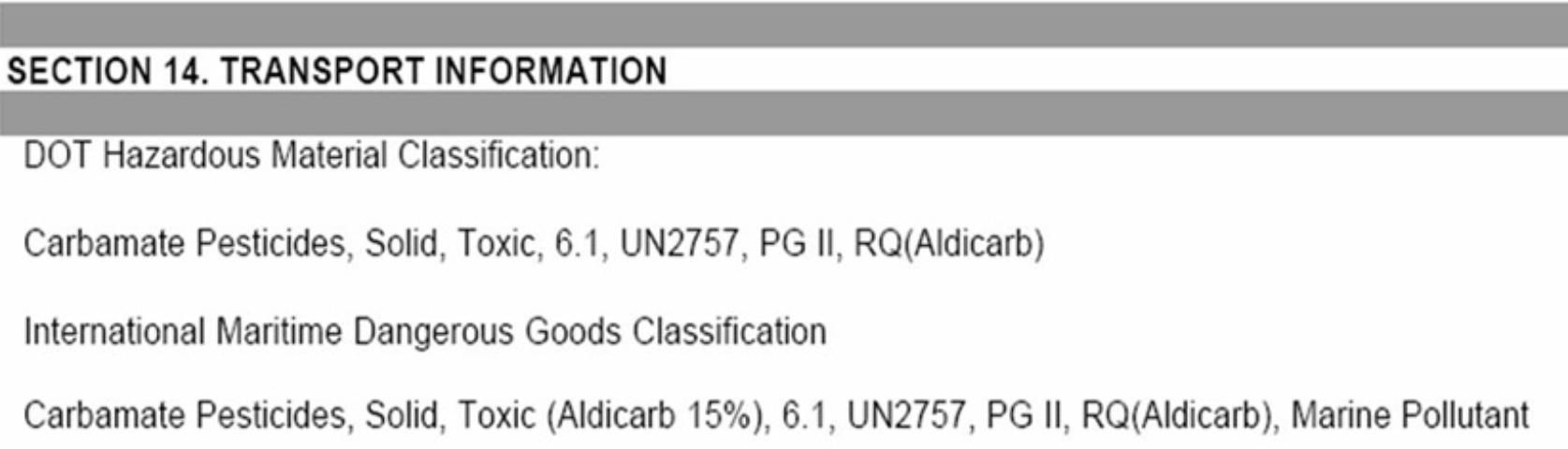
-
Shipments of hazardous materials will have a shipping paper. This is the proper description of the material being transported. It may come in several forms including bills of lading, invoices, or delivery tickets. An example of information that may be seen in a shipping paper is shown in Table 2, and an example of a shipping paper is shown in Table 3. More detailed information on shipping papers is also contained in this document.
What type of driver's license is required for transporting hazardous materials?
If you drive a vehicle that contains a pesticide amount requiring placarding, then a Class "C" Commercial Driver's License is necessary. The driver is also required to have an "H" endorsement with their Commercial Driver's License, which indicates a vehicle used to transport hazardous materials in placardable amounts. Information on Commercial Driver's Licenses may be obtained from the Florida Department of Highway Safety and Motor Vehicles at http://www.flhsmv.gov/.
Even though I transport pesticides classified as hazardous materials, could I be exempt from the DOT regulations?
The DOT regulations are written for the transportation industry. Many companies routinely transport pesticides and fuels for support of their operation. Businesses that transport small quantities of certain hazardous materials may be exempt. This exemption is known as a Material of Trade (MOT) provision. Check for the following concerning the products you are using:
-
There should be a diamond-shaped DOT label on the packaging; if there is no DOT label, then the product is not considered hazardous and does not have to be listed.
-
If you see the diamond-shaped DOT label, make note of the hazard classification number at the bottom of the diamond.
-
Check the capacity of the containers that you transport.
-
If the DOT diamond-shaped label is present, look for the packing group number in the center of the diamond. It will be either:
-
PG I = material poses great danger;
-
PG II = material poses medium danger;
-
PG III = material poses minor danger.
If this information is not on the diamond found on the packaging, it can likely be found on the SDS, the shipping papers provided, the supplier, or the product manufacturer should know.
-
Determine the total weight of the product being transported. Under DOT regulations, a 50-pound bag of product represents 50 pounds regardless of whether the actual amount of active ingredient is much less. Some laws regulate by the amount of active ingredient, not the total weight; this is not the case with the DOT.
Based on the information you obtained from the items listed above, MOT meets any one of the following and is exempt:
-
Class 3, 8, 9, Division 4.1, 5.1, 6.1, or other regulated materials, contained in one package with a capacity of no more than:
-
1 pound or 1 pint for a PG I material;
-
66 pounds or 8 gallons for a PG II, PG III, or other regulated materials; or
-
400 gallons of a diluted mixture not to exceed a 2 percent concentration of a class 9 material;
-
220 pounds of a Division 2.1 or 2.2 material in a cylinder; and
-
A one-ounce package (or less) of a Division 4.3, PG II, or PG III material.
No more than 440 pounds of any hazardous material not specified above may be transported. If all the DOT hazardous materials that you transport fit the previous exceptions, they are considered MOTs and you are exempt from the requirements if the following are also met:
-
Packaging must be leak-proof for liquids and gases and sift-proof for solids.
-
Packages must be securely closed, secured against movement, and protected against damage.
-
Gasoline must be contained in containers approved by DOT or the Occupational Safety and Health Administration (OSHA).
-
Cylinders and pressure vessels must be marked with the proper shipping name and must have the identification number and DOT label attached.
-
A non-bulk package other than a cylinder (including receptacles transported without outer packaging) must be marked with a common name to identify the contents, including the letters "RQ" if it contains a Reportable Quantity of a hazardous substance.
-
A tank that contains a diluted mixture (not more than 2% concentration) of a Class 9 material must be marked on two opposite sides with the 4-digit United Nations (UN) or North America (NA) identification number.
-
The operator of a motor vehicle that contains MOT must be informed of the presence and amount of the hazardous material.
Shipping Papers Details
A shipper who obligates someone else to transport hazardous materials is required to prepare a shipping paper and provide a copy to the vehicle driver. The shipping paper must be with the driver during the transfer of hazardous materials. If more hazardous materials are added later during transport, then the shipping papers must be updated, or an additional paper generated for the added load. If hazardous materials are off-loaded, some companies may keep a running tally of the hazardous materials off-loaded. Although this is not a requirement, it could prove to be useful should a driver need to explain to a DOT inspector or emergency responder why the current load is less than what is listed on the shipping paper. There is no specific format requirement for a shipping paper, but the required criteria are:
-
Hazardous materials must be listed first if non-hazardous materials are on the same load;
-
Hazardous materials must be entered or highlighted in a color that contrasts with any non-hazardous materials listed;
-
Hazardous materials must be identified by an "X" or "RQ" before the proper shipping name in the hazardous materials column. "RQ" is used instead of "X" if a reportable quantity is present in one package.
Vehicle Placarding Requirements
When a vehicle transports any amount of a hazardous material, placards (Figure 1) must be placed on each side, the front, and rear of the vehicle. There are minimum size requirements to meet placard specifications:
-
Each side: 10.8 inches
-
Inner border: must be a solid line ½ inch from the edges
-
Class text and division numbers: 1.6 inches in height
The vehicle DOT registration numbers must be at least 2 inches high, displayed on both sides of the vehicle, and be in a color of contrast to the vehicle.
Who to Call in Case of an Accident
A general sequence of resources:
-
Notify your agency, organization, or home office.
-
Call the emergency response telephone number listed on the shipping paper.
-
Call Chemtrec at 1-800-262-8200.
With each call, provide as much information as possible:
-
Your name, telephone, and fax numbers
-
Location and nature of problem
-
Name and identification number of material(s) involved
-
Shipper/consignee/point of origin
-
Truck number
-
Container type and size
-
Quantity of material transported/released
-
Local conditions, such as weather and proximity to hospitals, schools, and bodies of water
-
Any injuries and exposures
-
Local emergency services that have been notified
Employee Training
Those who work around hazardous materials, including drivers, are required to receive hazardous materials training. The required components of the training include:
-
General awareness
-
Instructions related to the employee's specific job responsibilities
-
Safety training
-
Security awareness
Sources of training resources may be obtained from the US DOT by calling 1-800-HMR49-22. The person offering training must be qualified through experience, possess a commercial drivers license with appropriate endorsements, or have attended an instructor training program. The US DOT also offers training seminars throughout the US at various dates and locations. For information, see https://www.transportation.gov/. Initial training must be completed within 90 days of employment or change in job function. The training must be repeated at least once every three years. Training from a previous employer or source may be used to satisfy the requirements provided that a record of the training is obtained. The training and testing documentation records that an employer must keep on file include the following:
-
Employee's name
-
Completion date of most recent training
-
Training materials (copy, description, or location)
-
Name and address of trainer
-
Certification that the employee was trained and tested
Testing is required, but it is left to the discretion of the employer. There are no DOT specifications for the elements of the test. The test may be written, oral, performance-based, or any combination thereof.
Additional Information
Chemtrec. (CHEMical TRansportation Emergency Center). 1-800-262-8200. http://www.chemtrec.org/Chemtrec/
Fishel, F.M. 2005. Understanding Safety Data Sheet Language. Gainesville: University of Florida Institute of Food and Agricultural Sciences https://edis.ifas.ufl.edu/PI072
Florida Department of Highway Safety and Motor Vehicles. (850) 617-2000. http://www.flhsmv.gov/
Florida Department of Transportation. 866-374-FDOT (3368). http://www.dot.state.fl.us/
Nesheim, O.N. and F.M. Fishel. 2005. Proper Disposal of Pesticide Waste. Gainesville: University of Florida Institute of Food and Agricultural Sciences. https://edis.ifas.ufl.edu/pi010
Office of Hazardous Materials Safety. 2004 Emergency Response Guidebook. http://phmsa.dot.gov/hazmat/library/erg
United States Department of Transportation. 202-366-4000. http://www.dot.gov/