This EDIS publication describes the requirements that a pesticide manufacturer must meet in order for the United States Environmental Protection Agency (EPA) to approve the labeling of a new product as required before a pesticide is marketed to the public.
Introduction
No pesticide may be sold in the United States until the EPA has reviewed the manufacturer's application for registration and determined that use of the product does not present an unreasonable risk to humans, wildlife, or the environment. As part of the registration process, the EPA must approve all language that the manufacturer proposes to include in the product labeling.
The EPA reviews the labeling to make sure it contains all information needed for safe and effective use of the pesticide. The EPA also ensures the information provided in the labeling is backed by reliable data, which is submitted by the manufacturer to the EPA. The EPA may require the manufacturer to change the labeling if the information is incomplete or incorrect.
The EPA product manager is the liaison between the EPA and the product registrant. The product manager coordinates the agency's internal review and monitors the status of the registration. The product manager also facilitates discussion among agency scientists and helps resolve any problems that arise during the registration process.
The EPA's policy of delegating to one product manager responsibility for the complete documentation on a specific active ingredient allows the product manager to view the whole picture—i.e., health and safety issues, environmental and wildlife concerns, and product chemistry. Equally important, the product manager facilitates an open line of communication between EPA staff, the registrant, and the public. Public notices of manufacturer registration for EPA labeling are published in The Federal Register.
Only after the EPA has reviewed the labeling and registered the product can a pesticide lawfully be sold for use. If the manufacturer wants to change the information on the labeling after the product and labeling are registered, the EPA must approve the change.
Background of the Label
The valuable information available on an EPA-approved pesticide label is the result of considerable time, effort, and money required to gather the information and ensure it is reliable. The process through which a pesticide manufacturer develops a product and provides the information that ultimately appears on the EPA-approved pesticide label takes a minimum of six years to obtain and costs the registrant millions of dollars.
Chemical companies continually make new compounds and then screen them for possible pesticide use. For every new pesticide that successfully meets the EPA standards, thousands of other compounds are screened, but discarded for various reasons. Once a promising pesticide is discovered, its potential application must be evaluated. If chemical-company researchers believe they have a worthwhile product, and a strong possibility exists for a significant sales market for the product, the company undertakes wide-scale testing and the EPA label-registration process.
In the development and labeling of a pesticide, the manufacturer provides the EPA with extensive data that demonstrates not only that the chemical controls pests as intended, but also that the chemical does not cause unreasonable adverse effects. As many as 140 carefully controlled tests are conducted to determine the effectiveness and safety of each pesticide under a wide range of environmental conditions.
The Testing Process: Toxicity and Toxicology
These tests are designed to determine whether or to what extent a pesticide may be dangerous to humans, wildlife, and other organisms (Figure 1). The tests examine whether the chemical causes long-term, unintended effects, whether the chemical causes skin reactions or other effects. To determine whether these or any other health effects may be related to use of a chemical, researchers administer the pesticide at various dosages to test animals, usually rats and mice. These toxicological tests alone often cost a company several million dollars to complete.
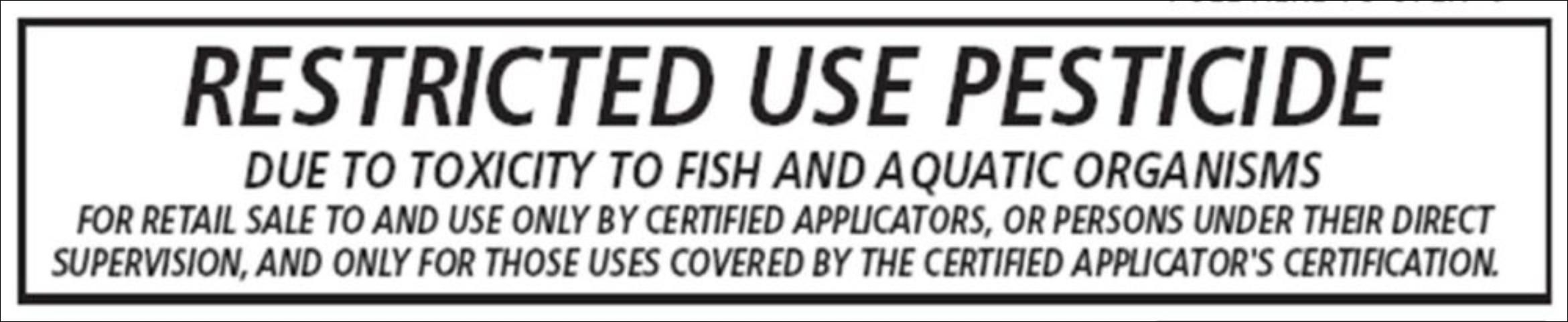
The Testing Process: Efficacy or Performance
Efficacy tests (also called performance tests) determine whether and to what extent the pesticide controls the target pest. The company seeking EPA approval of labelling must provide performance data to show that the pesticide product controls a particular pest or group of pests on one or more hosts or sites, including plants, animals, soil, and structures. The data must show that the pesticide, when used for its intended purpose and according to directions, is a useful product.
The company seeking the EPA approval must provide the EPA with extensive information concerning the pesticide's performance on crop varieties and soil types, as well as information concerning pesticide-application methods and rates and number of required applications. Tests results must show that the target pests are controlled, crops or animals are not injured, yield and/or quality has been improved, and the pesticide definitely provides a worthwhile benefit.
The Testing Process: Degradation, Mobility, and Residues
Tests of pesticide degradation, mobility, and residue examine what happens to the pesticide after it is applied. A series of studies is necessary to determine the amount of time required for the compound to degrade into harmless materials under various conditions. Whether the pesticide moves through the soil into groundwater and whether the pesticide moves into the plant from treated soil is also determined in these tests.
Residue studies are conducted for each method of application on each treated crop or animal. These tests determine how much, if any, of the pesticide residue (its breakdown products) remains on or in the crop or animal at the time of harvest or slaughter. From these data, the EPA determines preharvest intervals and preslaughter intervals — the minimum number of days that must past after the last pesticide application before harvest or slaughter can safely occur.
For each pesticide used on a crop or commodity, the EPA also establishes a residue tolerance — the maximum amount of a pesticide residue that may legally remain on or in food or feed at harvest or slaughter. Tolerances are expressed in parts per million (ppm). For example, the tolerance for carbaryl insecticide on blackberries is 12 ppm while the tolerance for the same insecticide on blueberries is 10 ppm. For poultry, the EPA-allowed tolerance for this insecticide is 5 ppm. Pesticide residues on or in food or feed commodities must not exceed the EPA-established residue tolerances at the time the crop or animal (including meat, milk, and eggs) is ready for market or livestock feeding.
Although specific tolerances are not included on product labels, preharvest intervals and/or preslaughter intervals are often listed on labels of agricultural pesticides (Figure 2). These intervals, set by the EPA, allow time for the pesticide to degrade to a level deemed by the EPA to be safe for human consumption of crops or livestock food products. Adhering to these interval requirements prevents residues greater than the EPA-approved tolerances on food, feed, or animal products. If pesticide residues exceed the tolerance level established by the EPA, or if residues are found on commodities for which the EPA has not determined any tolerance, commodities may be condemned and destroyed.
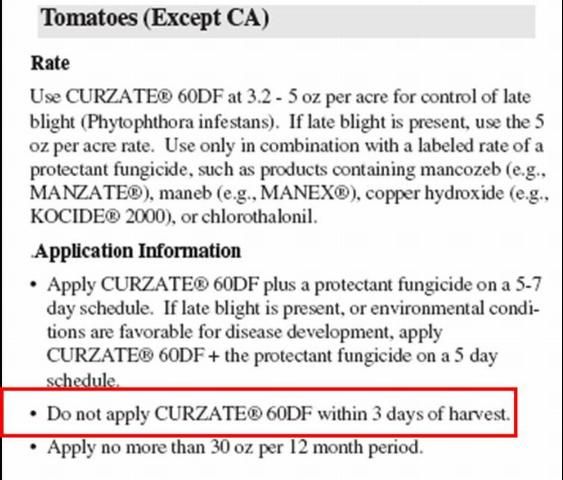
The Testing Process: Effects on Wildlife and the Environment
The company seeking the EPA label must determine the effects of field applications of the pesticide upon wildlife and the environment. Any potentially harmful effects on wildlife and the environment that are recognized during these studies must be included in the environmental-impact statement the pesticide manufacturer submits to the EPA (Figure 3).
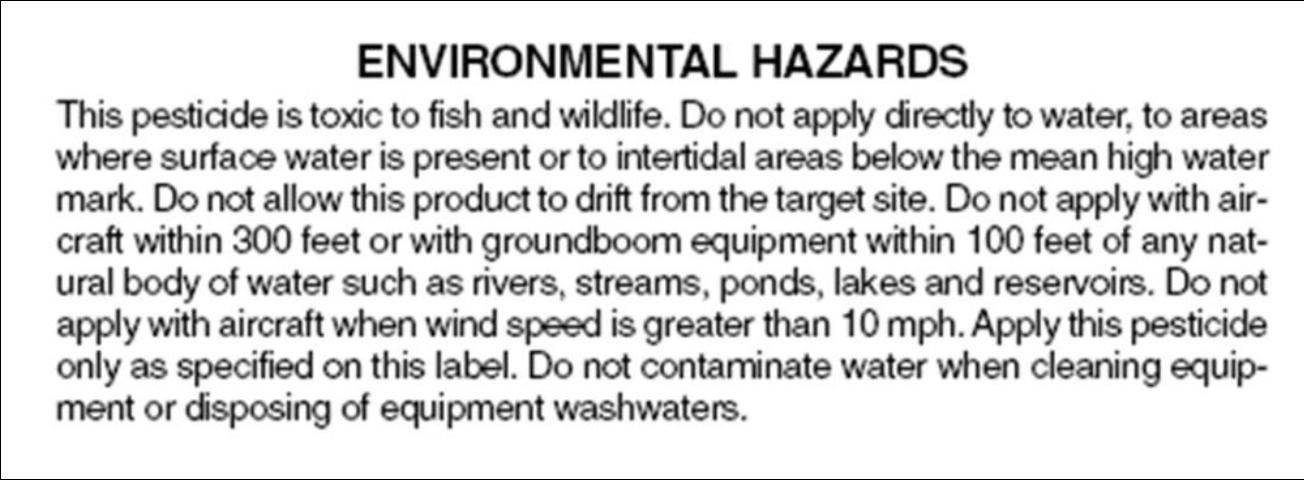
Additional Information
Pesticide labeling series. UF/IFAS publications, https://edis.ifas.ufl.edu/TOPIC_Pesticide_Labeling (accessed April 2008).
UF/IFAS Pesticide Information Office. http://pested.ifas.ufl.edu/ (accessed April 2008).