Introduction
Large-scale production of biochar and its utilization as an agricultural amendment is roughly a 2,000-year-old practice that converts organic waste into a soil enhancer that can retain carbon and nutrients, and increase soil biodiversity (Glaser and Birk 2012). Biochar also can be an important tool to increase food security and cropland diversity in areas with severely depleted soils, scarce organic resources, and inadequate water and chemical fertilizer supplies (Lal 2010; Spokas et al. 2012). Biochar amendments also have the potential to improve water quality and availability by increasing soil retention of nutrients and agrochemicals for plant and crop utilization as nutrient leaching is decreased (Bhadha et al. 2017; Glaser et al. 2002). The benefits of biochar production include oil and gas byproducts that can be used for energy production as an option for clean and renewable energy sources (Mohan et al. 2006; Demirbas 2008). When biochar is applied as a soil amendment, the soil-biochar system sequesters carbon by increasing the soil organic carbon pool, reversing the effects of organic matter decomposition by intensive cultivation of soil (Sigua et al. 2014). It is one of the few technologies that is relatively inexpensive, widely applicable, and quickly scalable.
Biochar can be produced in a wide variety of ways; some are complex, while others are relatively simple. Each method is distinguished by different ranges of temperatures, oxygen availability, heating rates, and biomass feedstock, among other factors. Given this variability in pyrolysis processes and the accompanying process conditions, in combination with a wide range of available biomass feedstock, large variability is to be expected in the physico-chemical properties of the biochars, and ultimately in the performance as a soil amendment (Sun et al. 2011; James et al. 2020). Low-temperature slow pyrolysis offers an efficient and sustainable means of converting organic feedstock into biochar. Essentially, in all pyrolytic processes the feedstock is heated between 250°C–800°C, ideally in a low- to no-oxygen environment. The biomass is essentially cooked until various lignin and cellulose products break down to produce hydrogen-rich syngas that can be either combusted or condensed for biocrude collection. The high-carbon product that remains is biochar. The challenge for biochar research is assuring product quality produced from any given feedstock by any given pyrolysis technology and process conditions (Chen et al. 2008). One of the technologies used to generate biochar using gasification is the top-lit updraft (TLUD) gasifier (Saravanakumar et al. 2007). At the University of Florida Everglades Research and Education Center in Belle Glade, FL, a custom designed TLUD was built that can generate biochar from locally acquired feedstock. This publication describes the design of the TLUD gasifier and evaluates the biochar recovery of four locally available feedstocks.
Top-Lit Updraft (TLUD) Gasifier
The design and use of a TLUD gasifier is counter-intuitive; rather than lighting the bottom of the feedstock pile, the pile of feedstock must be ignited on top (Figure 1). The TLUD was made out of 1/8" sheet-iron; it includes a 5' tall chimney with a 30" diameter, capable of holding up to 24.5 ft3 of feedstock. A 4" wheel permanent split capacitor blower fan was housed in an 18" × 18" square box at the bottom of the chimney with a hinged door next to the fan (Figure 2). If the gasification process becomes too hot, resulting in ashing, or too cool, stalling the process, the updraft can be regulated using the fan intake vent (Figure 2g). The box is separated from the chimney by a 1" screened iron mesh, which allows free flow of the draft generated by the fan and prevents the fan from overheating as the burn-line moves from top to bottom. Two custom modifications were made to the original design of the TLUD (Anderson 2009), which helped produce a uniform burn and provided a relatively steady control of temperature. The first was a detachable iron cap with an adjustable snout to control the smoke, and the second was a clamp fitting for an intake gas line. The intake gas used for this study was N2 (99% commercial grade). Once the burn-line reaches the bottom, N2 gas is blown through the chimney, displacing any air (oxygen) and gradually ceasing the gasification. Flushing the system with an inert gas once the feedstock has been completely charred prevents combustion, preserves the char, and increases batch yields.
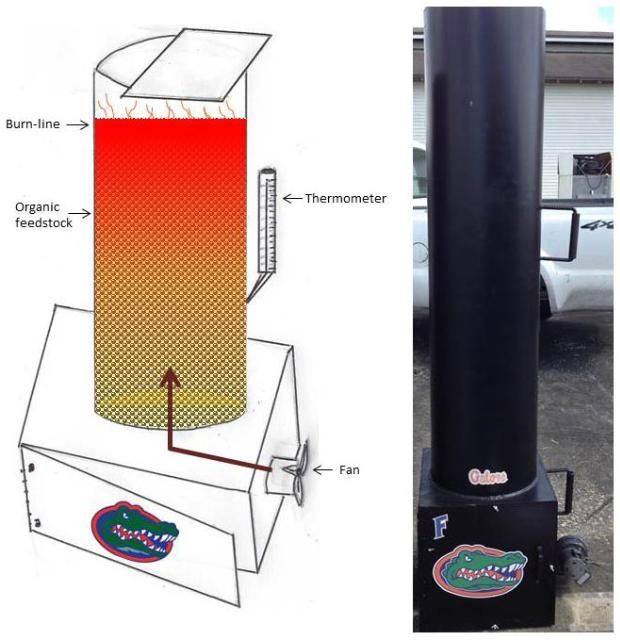
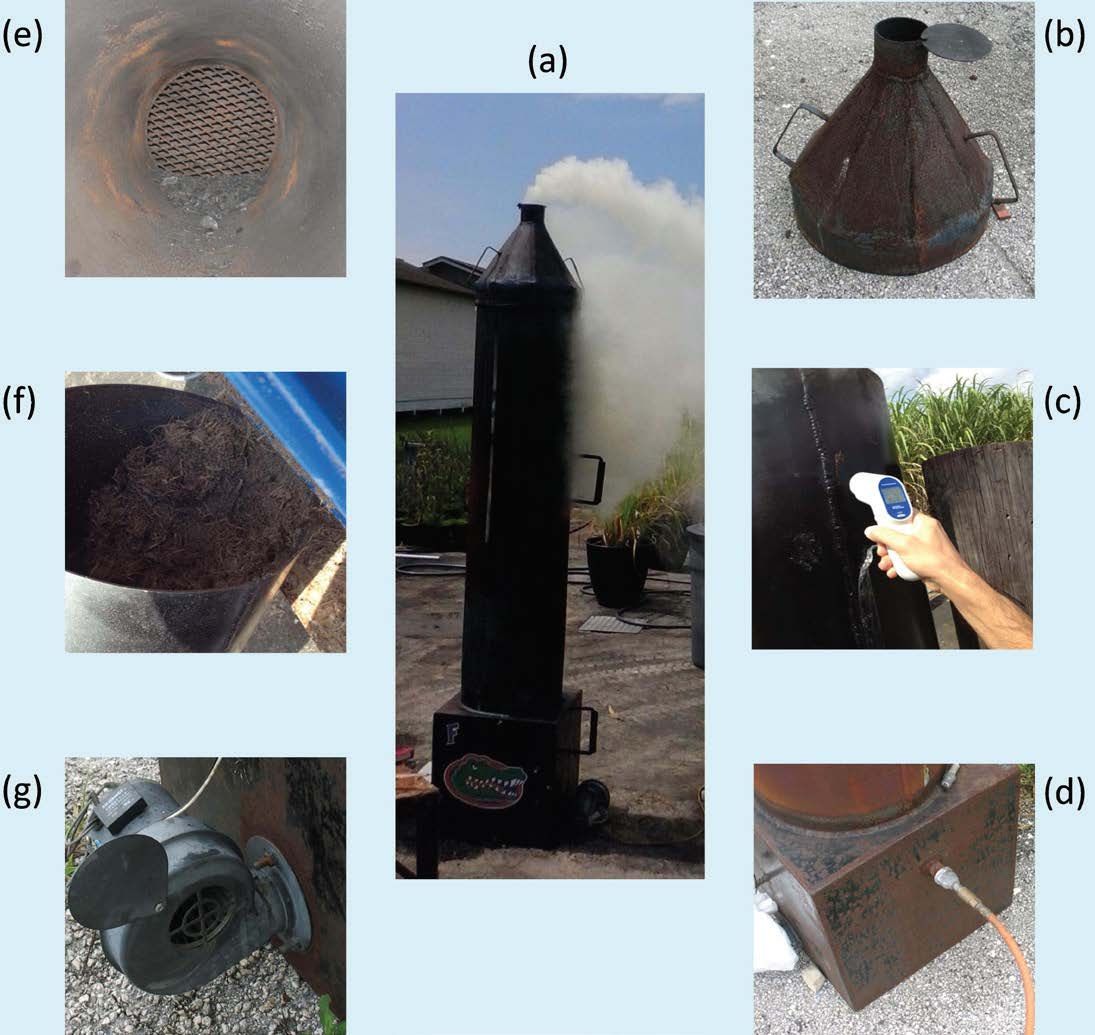
Credit:
Converting Feedstock to Biochar
To test the capability of the TLUD, four organic feedstocks were selected because of their availability near the Everglades Agricultural Area (EAA) and surrounding urban locations. The feedstocks consisted of (i) sugarcane bagasse obtained from the Sugar Cane Growers Cooperative of Florida in Belle Glade, FL; (ii) horse barn shavings with manure from the Palm Beach Polo Golf and Country Club, Wellington, FL, (iii) hardwood yard waste; and (iv) palm fronds from Wellington Solid Waste Authority. All four feedstocks were dried at 50°C for 72 hours prior to being packed into the chimney. Proficiency in starting the gasification, maintaining a steady burn-line, and producing a consistent batch of biochar takes some experience, so multiple batches of feedstocks were cooked. According to Dr. John Gaunt (Director GY Associates and Cornell University), slow pyrolysis is the most effective means of producing biochar with typical biochar yields of 35% to 50% of dried biomass weight, and in terms of efficient conversion of biomass to useful products the TLUD gasifier's performance is at or very near the top among the latest stove designs. Each feedstock must be pre-treated to a desirable moisture content and gasified with the correct updraft volume/velocity. Approximately 75–85 lb. of the dried feedstock was carefully packed into the chimney to minimize any air pockets that could otherwise result in preferential burn. Ronsse et al. (2013) recommend pelletizing the feedstock prior to pyrolysis, as this will ensure a consistent burn by establishing uniform air flow, density, and heating through the feedstock.
Biochar recovery by weight was variable from one batch to another (Figure 3). An average of at least four batches of each feedstock resulted in 17 ±1.8%, 23 ±3.1%, 30 ±7.3% and 33 ±3.8% recovery by weight of bagasse, horse shavings, yard waste, and palm fronds, respectively (± standard deviation). It took approximately 40 to 90 minutes to complete a single batch in the TLUD. After the feedstock was packed into the chimney, the top was dowsed with a little lighter fluid and set alight. A steady flow of air was provided through the chimney by controlling the fan at the bottom. The temperature of the burn-line was monitored using a temperature gun. Once the temperature in the TLUD exceeded 300°C the cap was placed over the chimney. Successful charring can be inferred by observing the smoke blowing out of the cap, often referred to as "syngas." For example, a thick, colored smoke usually means that the feedstock is charring and that the temperature in the chimney is not high enough to ash the feedstock. Igniting the smoke can exemplify the process by showing available energy, denoting that the feedstock has not entirely been consumed. Droplets of oil dripping from the top of the cap also are a sign of charring. While horse shavings generated a distinct pale yellowish-green smoke, palm fronds produced the most oil droplets.
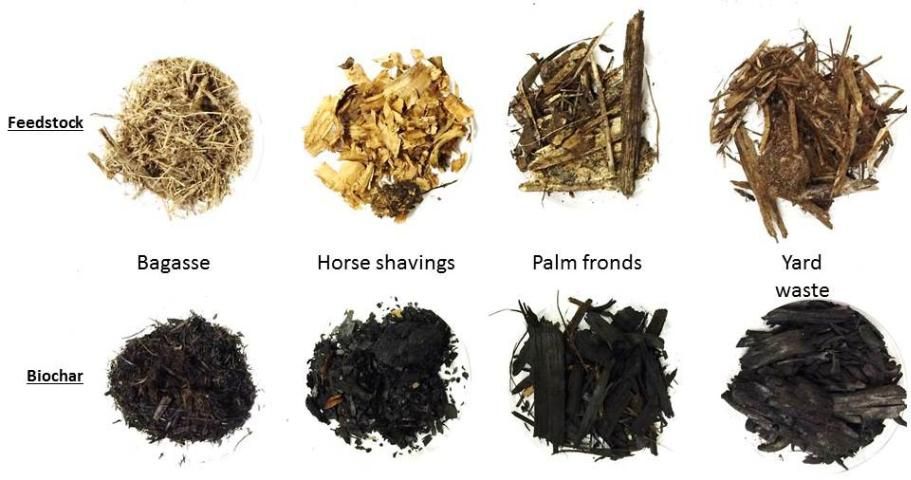
As the burn-line continues to move from top to bottom, the temperature in the chimney can reach over 500°C. Once the burn-line has reached the bottom of the chimney, the charring process is complete and any further combustion inside the chimney is simply ashing the feedstock, which should be avoided. In order to completely cease combustion inside the chimney of the TLUD, N2 gas was injected through the intake line to displace any air (oxygen) from the chimney. The added benefit of injecting N2 gas through the chimney is that it drastically cools the char. While N2 is being blown through the chimney, the outside walls of the TLUD can be sprayed with water to cool it down further.
Applications of Biochar
Research has revealed several encouraging properties of biochar, which have shown that it is more effective to retain nutrients and may have greater potential to improve crop yields than other types of organic matter such as manure and compost (Lehmann et al. 2006; Chan et al. 2008). Biochar can be more stable and resistant to microbial decay (Atkinson and Fitzgerald 2010). It also can provide greater nutrient availability and use efficiency due to the enhancement of soil physiochemical properties that allow a better utilization of nutrients found in the soil or added with fertilization (Lehman and Joseph 2009; Sohi et al. 2009).
Activated carbon is used in a wide variety of applications including medical, chemical, manufacturing, and environmental remediation. The supply of carbon substrate for activated carbon production increasingly is being provided by biochar production. Biochar provides an ideal carbon substrate source to activate and thus "designer chars" can be produced for a wide variety of applications (Novak et al. 2009). To be considered activated, a carbon source needs a high degree of microporosity or reactive molecular sites. These characteristics can give activated biochars the ability to adsorb contaminants in soil and water. Feedstock, thermal conversion, and activation method all can influence the characteristics of the activated biochar. This opens the door to a wide range of potential research into building soils for a defined purpose. The relative simplicity of the TLUD means this also could be an effective means for providing activated carbon sources to growers to use in agricultural production or water purification.
Summary
This report shows that a modified TLUD gasifier is capable of producing biochar from organic feedstock. Up to 33% by weight of biochar can be produced using this method. The quality and consistency of biochar will depend largely on the type of feedstock being used. Operating a TLUD will give growers (agriculture and nursery) the option of converting organic waste into biochar that can be used as either a soil amendment or enhancer. The potential for capture and characterization of syngas and crude oil as byproducts of the TLUD gasifying process is an added incentive which will be explored in the future.
References
Anderson, P. 2009. "CO and PM Emissions from TLUD Cookstoves. Biomass Energy Foundation." Presented at 2009 ETHOS Conference, 23–25 January. Kirkland, WA.
Atkinson, C. J., and J. D. Fitzgerald. 2010. "Potential mechanisms for achieving agricultural benefits from biochar application to temperate soils: A review." Plant Soil 331: 1–18.
Bhadha, J. H., S. Jennewein, and R. Khatiwada. 2017. "Phosphorus sorption behavior of torrefied agricultural byproducts under sonicated versus non-sonicated conditions". Sustainable Agriculture Research 6: 1–11.?
Chan, K.Y., L. V. Zwienten, I. Meszaros, A. Downie, and S. Joseph. 2008. "Agronomic values of greenwaste biochar as a soil amendment." Soil Research 45:629–634.
Chen, B., D. Zhou, and L. Zhu. 2008. "Transitional adsorption and partition of nonpolar and polar aromatic contaminants by biochars of pine needles with different pyrolytic temperatures." Environmental Science & Technology 42: 5137–5143.
Demirbas, A. 2008. "Biofuels sources, biofuel policy, biofuel economy and global biofuel projections." Energy Conversion and Management 49: 2106–2116.
Glaser, B., and J. J. Birk. 2012. "State of the scientific knowledge on properties and genesis of Anthropogenic Dark Earths in Central Amazonia." Geochimica et Cosmochimica Acta 82: 39–51.
James, A. M., Yuan, W., Wang, D., Wang, D. Kumar, A. "The Effect of Gasification Conditions on the Surface Properties of Biochar Produced in a Top-Lit Updraft Gasifier." Applied Sciences 10(2), 688. https://doi.org/10.3390/app10020688
Lal, R. 2010. "Managing soils and ecosystems for mitigating anthropogenic carbon emissions and advancing global food security." BioScience 60: 708–721.
Lehmann, J., and S. Joseph. 2009. Biochar for environmental management: Science and technology. New York: Earthscan Publishers Ltd.
Lehmann, J., J. Gaunt, and M. Rondon. 2006. "Bio-char sequestration in terrestrial ecosystems—A review." Mitigation and Adaptation Strategies for Global Change 11: 403–427.
Novak, J. M., I. Lima, B. Xing, J. W. Gaskin, C. Steiner, K.C. Das, M. Ahmedna, D. Rehrah, D. W. Watts, W. J. Busscher, and H. Schomberg. 2009. "Characterization of designer biochar produced at different temperatures and their effect on a loamy sand." Annals of Environmental Science 3: 195–206.
Ronsse F., S. Van Hecke, D. Dickinson, and W. Prins. 2013. "Production and characterization of slow pyrolysis biochar: influence of feedstock type and pyrolysis conditions." Global Change Biology Bioenergy 5: 104–115.
Saravanakumar, A., T. M. Haridasan, T. B. Reed, and R. K. Baia. 2007. "Experimental investigation and modelling study of long stick wood gasification in a top lit updraft fixed bed gasifier." Fuel 86: 2846–2856.
Sigua, G. C., J. M. Novak, D. W. Watts, K. B. Cantrell, P. D. Schumaker, A. A. Szögi, and M. G. Johnson. 2014. "Carbon mineralization in two Ultisols amended with different sources and particle sizes of pyrolyzed biochar." Chemosphere 103: 313–321.
Spokas, K . A., K. B. Cantrell, J. M. Novak, D. W. Archer, J. A. Ippolito, H. P. Collins, A. A. Boateng, I. M. Lima, M. C. Lamb, A. J. McAloon, R. D. Lentz, and K. A. Nichols. 2012. "Biochar: a synthesis of its agronomic impact beyond carbon sequestration." Journal of Environmental Quality 41: 973–989.
Sohi S., E. Loez-Capel, E. Krull, and R. Bol. 2009 "Biochar's roles in soil and climate change: A review of research needs." CSIRO Land and Water Science Report. Canberra: CSIRO.
Sun, K., M. Keiluweit, M. Kleber, Z. Pan, and B. Xing. 2011. "Sorption of fluorinated herbicides to plant biomass-derived biochars as a function of molecular structure." Bioresource Technology 102: 9897–9903.