Abstract
Greenhouse design considerations are critical in regulating optimal climatic conditions where plants are grown. The structural systems, building components and materials, and machinery equipment play a central role in greenhouse efficiency. Yet, many design considerations vary greatly with region and geography. This article describes greenhouse design considerations specific to Florida’s unique environment. It a includes descriptions of framing types and materials, design load consideration with appropriate resources, heating and cooling systems including materials, computer monitoring systems as well as recommendations for maintenance.
Introduction
A greenhouse is built to maintain an environment that results in the profitable production of high-quality crops. It must also be remembered that workers and equipment must function in this environment.
Planning before construction is vital when building any structure. A short time spent weighing design factors can make large differences in profits and convenience of operation over the lifetime of a structure. Economic and business considerations such as capital availability, interest rates, and whether the operation is wholesale or retail will influence the size and type of building needed. Government regulations and taxing policies can influence the design of the structure. In urban areas, building codes and zoning laws may prohibit certain types of operations, or specify details that must be included in the building design.
The greenhouse must be tailored to the type of crop being produced. It must also provide for the efficient use of labor and machinery within the house. The most desirable location for the house is influenced by land characteristics—elevation, topography, and drainage—and climatic factors such as solar radiation, temperature and wind. Greenhouses located below 40° latitude should be located with a north-south ridge orientation for maximum sunlight to the plants. Ridge and furrow houses should always be orientated north-south to decrease shadows.
The accessibility to needed commercial services should be considered along with the availability of shipping facilities and main roads. The supply of utilities—electricity, water, and fuel—must be considered, and telephone communications and communications between buildings must be planned.
Traffic flow and parking around the greenhouse area require forethought. Cross traffic between customers, suppliers, and production personnel should be avoided. Any plan should look to the future and provide for expansion or changes in the nature of the operation.
Structural Systems
The structure must withstand loads imposed by winds, rain, and use. It should also allow the maximum possible amount of light to reach the crop, house heating and cooling systems, and comply with building codes.
Foliage production structures vary widely in their basic design. Several typical design types are shown in Figure 1. The simplest type is the shade structure composed of shade cloth supported on poles. This type is inexpensive but is only practical in warm climates. It is also susceptible to wind damage.
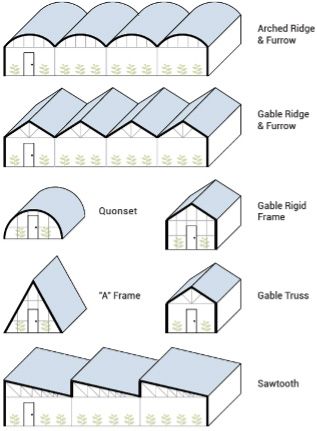
Credit: Jean Pompeo
Heavier structures are needed when cold protection is necessary. The most common type is the ridge and furrow house, which is easy to maintain and heat, and has a long life. Large ridge and furrow designs reduce heat transmission through walls. Problems with air movement may occur with very large ridge and furrow houses. Care must also be taken with the design of gutters, and the extra load of rainwater in the gutters must be considered. A sawtooth house is relatively inexpensive and is easy to ventilate and cool but may experience winter heating problems.
Quonset houses are simple in design, and inexpensive to construct. They are normally covered with externally applied plastic glazing. Strong fasteners at the ends and edges are very important. They provide clear-span interiors with minimal shading, but the curved side wall may place height restrictions on crops unless high foundation supports are used. High foundations increase the potential for wind damage. Quonset houses may suffer from ventilation problems. Structures with post and rafter, ‘A’ frame construction, or trusses are easy to build but require the use of more material than other designs. They have clear span interiors but should be limited to 20-foot widths when wood is used as the building material. This type of construction is normally used with wood frames and plastic film glazing. It requires strong sidewall posts with deep embedment to withstand out rafter forces and wind loads. ‘A’ frame construction uses a collar beam to strengthen the structure, producing wider houses than are possible with post and rafter construction.
Rigid frame construction provides high strength for the amount of material used. It can be used with wood or metal frames and gives a clear span interior. Post and truss designs give large unobstructed floor spaces, but trusses obstruct gable spaces and shade the floor area.
Design Loads
The National Greenhouse Manufacturers Association (NGMA) publishes a standard that gives guidance for the calculation of design loads for greenhouses. The dead load on a structure consists of the weight of the structure itself and the weights of any fixed equipment. Equipment that permanently attached to the structure in a greenhouse, such as fans, suspended heaters and overhead piping, should be considered as dead loads. It is a constant load and can be calculated from the weights of building materials and equipment.
Live loads are temporary loads produced by the operation of the structure. The NGMA suggests a roof live load between 12 and 15 psf. This is the load applied by workers during construction or repair. The NGMA standard gives a method for calculating loads based on roof slope and frame spacing. To account for workers climbing on the roof, the NGMA recommends that roof structural members be designed for a concentrated load of 100 pounds acting at their midspans. Bottom truss joints should also be designed for 100-pound concentrated loads in order to support equipment or hanging plants. Any live load shall be considered as a dead load if it is imposed on the structure for a continuous period of 30 days or more.
Designing for wind loads requires calculation of the forces applied to the main structural frame and also those applied to individual structural components and glazing. These loads are calculated using a formula that gives a design pressure based on the terrain, building height, building exposure, maximum expected 50-year wind velocity, and hazard to life and property if the building fails. Coefficients determined experimentally are used to calculate the fraction of this pressure that acts on a specific structural member.
These loads can be used to calculate design stresses acting on structural members. Allowable stresses for building materials are given in design manuals and specifications published by various organizations. Specification references governing several common materials are listed below.
Aluminum
Aluminum Design Manual. The Aluminum Association. Arlington, VA.
Wood
National Design Specification for Wood Construction. American Wood Council. Leesburg, VA.
Steel
Steel Construction Manual. American Institute of Steel Construction. Chicago, IL.
Cold Formed Steel Design Manual. American Iron and Steel Institute. Washington, DC.
Concrete
Building Code Requirements for Reinforced Concrete. American Concrete Institute. Farmington Hills, MI.
Glass
ASTM C1036 - Standard Specification for Flat Glass. American Society for Testing and Materials (ASTM) International, West Conshohocken, Pennsylvania.
Plastics
Structural Plastics Design Manual, Phase I; Chapters 1 through 4. Federal Highway Administration Publication FHWA-TS79-203.
Structural Plastics Design Manual, Phases 2 and 3; Chapters 5 through 10. FHWA-TS-82-216. Government Printing Office, Washington, DC.
Building Components
Foliage production structures are lightweight with large, exposed surface areas. Winds acting on structures of this kind can produce great uplifting forces. Foundations must be designed to withstand both this uplifting force and the downward gravity load of the structure. The structure must be securely anchored to the foundation to resist uplifting forces.
Frames can be constructed of many different materials arranged in different framing systems. Aluminum frames are long lasting, corrosion resistant, lightweight, and can be prefabricated. They can be permanently glazed and have low maintenance requirements. Aluminum frames have a high initial cost and require the services of experienced personnel during construction. Galvanized steel frames offer high strength and long life at less expense than aluminum frames, although maintenance of steel frames may be higher. Metals are good conductors of heat, and the heat loss through an aluminum or steel frame may be significant. The high strength of metal makes it possible to use small structural elements minimizing shading caused by the frame.
Wood frames have a low initial cost but have high maintenance costs. They are also flammable. Painting wooden frames white will improve lighting conditions within the house. Wood should be pressure treated with preservative to inhibit decay. Creosote and Penta treatments give off fumes toxic to foliage plants and should not be used. Water-borne preservatives such as chromated copper arsenate (CCA) or ammonium copper arsenate (ACA) are the best preservatives to use in foliage production structures.
Several types of glazing materials are used by the greenhouse industry. Glass is an excellent material when its high initial cost can be tolerated. It has a life of 25 years or longer, has low maintenance requirements and transmits light well. It requires skilled labor for construction and has a low impact strength. High strength grades of glass should be used for glazing. Glass is heavy and requires strong framing with large supports that block light.
Synthetic sheets and films have replaced glass as the glazing material used in most greenhouses. The most widely used material is polyethylene film. This material is low in cost, light weight, easy to apply in wide sheets, and has a high light transmittance. Unfortunately, it also has a very short life. Regular grades have a lifetime of only one year. Ultraviolet stabilized grades, which last from four to six years, still require more frequent replacement than most other glazing materials. Common grades of polyethylene are transparent to infrared radiation. New grades are now available that block infrared radiation and reduce greenhouse heat losses.
Other plastic materials have been considered for greenhouse use with some amount of success, but their advantages are usually outweighed by their higher cost compared to polyethylene. Some of those which have been used are polyvinyl chloride films and sheets, polyvinyl fluoride films (Tedlar), polycarbonate sheets, and acrylic sheets.
Fiberglass reinforced plastic (FRP) sheets are used widely for glazing material. They are relatively low in cost, but more expensive than polyethylene. They are lightweight and impact resistant compared to glass. They have a fairly high light transmittance that is slightly less than that of glass or polyethylene, and they are easy to fabricate. FRP sheets degrade when exposed to ultra-violet light. Their ultraviolet resistance is improved by the use of Tedlar coatings and acrylic additions to the polyester resin.
Glazing materials must transmit the maximum of amount of sunlight to the crop while also holding heat gain or loss to a minimum. The use of double layers of film can add insulating value to the glazing system with only a small reduction in light transmittance. When polyethylene film is used, this system is called double poly and utilizes an air space inflated by a small fan to provide good insulating characteristics. When compared to a single layer of polyethylene film, the double poly system can provide reductions of 35 to 40 percent in heat loss with a 10 percent reduction in light transmission. Injection of water, a liquid foam, or lightweight, polystyrene foam beads between two layers of covering have been studied to further improve the thermal resistance of the glazing, however, air inflation is still the most common technique for double covering greenhouses with plastic films.
Rigid, double-walled acrylic and polycarbonate glazing panels are becoming available. They are relatively high in cost and are subject to thermal expansion, requiring that attention be given to edge seals. They do offer good insulating value and can be formed into arched shapes, reducing, or eliminating the need for internal framing members.
Utilities
Alarm systems and backup power systems should be provided for heating and cooling systems. The National Electric Code and local regulations must be followed when wiring all electrical systems. Arrange for a dependable fuel supply in advance of the heating season in case shortages develop. A standby generator may be desirable for many operations.
Heating
The greenhouse heating system balances the heat loss under cold conditions. It must maintain a uniform temperature within the house while producing no harmful fumes. Forced air systems are the most common in new greenhouses. They are relatively inexpensive and have low maintenance requirements. Heated air is supplied by unit heaters or furnaces. Care must be taken to avoid plant damage with exhaust fumes.
Steam and hot water systems have a high initial cost, may be hazardous to operate, and require regular maintenance. However, they are clean and free from toxic fumes.
Solar systems eliminate fuel costs and provide fume-free heat. They have a high initial cost and are often complex and require skill to operate. They are dependent on weather conditions for successful operation.
Further information about heating systems can be found in UF/IFAS Extension Department of Agricultural and Biological Engineering Fact Sheet AE11. The American Society of Agricultural Engineers gives design recommendations for heating, ventilating and cooling systems in ASAE Engineering Practice ASAE EP 406.
Cooling Systems
Greenhouses operating under summer conditions require cooling systems for optimum plant growth and worker efficiency. Ventilation can reduce the inside temperature to close to that of the outside air. Natural ventilation using ridge and side vents is satisfactory for many operations. Cooler outside air enters through side vents and is distributed throughout the structure. The critical factor for cooling greenhouses with roof and side vents is the rate of air exchange by free convection. This exchange rate is influenced by total vent area, windspeed, and the temperature difference between the indoor and outdoor air. A total vent area equivalent to 15 to 30 percent of the floor area is recommended for effective cooling. Vent areas greater than 30 percent result in very little increase in cooling. An air exchange rate of 1 air change per minute is required to maintain a difference of 10°F or less between indoor and outdoor temperatures. The inside temperature of the greenhouse can rise to levels 15°F to 20°F above ambient temperatures when natural convection is used alone.
Forced convection using fans can lower air temperatures 5°F to 10°F below those found in greenhouses cooled by natural convection only. The opening through which the air enters the greenhouse must be relatively large and extend across the entire wall on which it is located, or nonuniform airflow patterns and temperature distributions will result.
Several modifications of forced convection systems can result in more uniform temperature distributions. The use of a convection tube or poly tube is one example. The tube is attached to a fresh air inlet and sealed at the other end. Holes spaced along its entire length distribute air uniformity. A convection tube ventilating system uses about one third of the fan capacity of a standard, forced convection system using fans alone to produce the same results.
A false ceiling of polyethylene or polyester film at eave level is another way of improving ventilation. The poly ceiling lets light through while reducing the volume of air in the greenhouse and keeping the cool airstream down, closer to plant level.
Forced convection alone may not reduce temperatures to the desired levels. Evaporative cooling can be used to produce lower temperatures when this is the case. The most commonly used system of evaporative cooling is the fan and pad system. Water is applied to the pad material as air is being drawn through the pads by fans located on the opposite side of the greenhouse. Evaporative cooling produces two changes in the condition of the air exiting the pads. The air is cooler, and its humidity has been raised. The wet-bulb temperature of the entering air is the limiting factor in the amount of cooling that can be accomplished. As the air travels from the pad to the exhaust fans, a rise in temperature results from the energy that has entered the greenhouse. The maximum temperature rise across the greenhouse should be 7°F to 8°F. Approximate 1/3 gallon per minute of water per foot of pad length should be applied. The fans should have the capacity to provide a minimum of one air change per minute.
One of the most common pad materials is compressed aspen fibers. Aspen pads are relatively inexpensive, but also have disadvantages. They are susceptible to algae infestation which leads to rotting. The pad material compacts with age, resulting in inefficient operation. This requires frequent costly pad replacements. Cellulose paper pad material that has been impregnated with rigidifying saturants, wetting agents, and insoluble salts is being used to help resist rot. Cement impregnated fibers are used as another pad material. There is some limited use of rubberized hog hair pads. Expanded aluminum pads are just coming on the market.
Research has shown that new aspen pads, cement coated pads, and corrugated cellulose pads all produce about the same amount of evaporative cooling. Rubberized hog hair and compacted aspen pads both have low evaporative cooling efficiencies. Florida Cooperative Extension Service Agricultural and Biological Engineering Fact Sheet CIR1135 discusses factors to consider when installing a fan and pad cooling system.
High-pressure mist or fog cooling is another method of greenhouse cooling. Water is sprayed into the air above the plants at a pressure of 500 to 1000 pounds per square inch through low capacity nozzles (1/2 to 3/4 gallon per hour). A fine mist or fog fills the structure and as the droplets evaporate, and fall, they cool the air. The cooling achieved from high-pressure fog or mist is comparable to that obtained from a fan and pad system, but some problems have been experienced with nozzles clogging. Mist or fog systems can provide more uniform temperature distributions than fan and pad systems and also provide uniform high humidity levels.
Ground water can be used as a cooling medium for greenhouses. Ground water temperatures average 74°F in central Florida. Work has been done at the University of Florida Agricultural Engineering Department to evaluate a closed system that uses well water to remove heat from the ventilating air. This system provides lower air temperatures than evaporative pad systems do but may require more power because of the higher volumes of water required to operate the system.
The large quantity of heat that must be removed, dehumidification of the air, the capital investment in equipment, operating costs, and maintenance problems limit the use of mechanical refrigeration in greenhouse cooling. Its only practical application is found in research, where the environmental conditions of small areas must be controlled very accurately.
Shading
Shading is used to control light and lower interior temperatures. Liquid shading provides a coating that blocks the sun’s rays. The main problem with liquid shading compounds is that once applied, their shading density is not easily changed, and they often must be removed in the fall. A liquid shading compound must be designed to diffuse light rays and reflect heat. It must be formulated so that it will not have harmful effects on the glazing material. Several factors to consider when choosing a liquid shading compound are ease of application and removal, effects on the crop, and cost of the material.
Fabric shade cloths can also be used to screen out unwanted amounts of radiation. Shades can be coupled with cloth moving devices to provide movable curtains that offer some amount of control of the house temperature. The shade cloth should be mounted on the exterior side of the glazing for the greatest reduction in the heat load.
Curtains
Interior curtains reduce the thermal conductivity of a structure. They lower energy losses by adding two or more stagnant air layers between the interior of the greenhouse and the glazing. They also reduce infiltration and radiation heat loss. The greatest disadvantages of curtains have been poor mechanical reliability, incomplete sealing after closure, and condensation damage to curtains and plants.
Computer Monitoring Systems
If the environmental needs of the plants are known, computer monitoring, and control systems can be used to provide constant regulation and close control of the greenhouse environment. This precise control results in lower energy costs, and greater productivity by the plant material. Numerous sensors are connected to a central climate control computer to collect environmental data helping to control the production systems, including temperature, humidity, electrical conductivity, pH, carbon dioxide, fogging, shading and external weather conditions. For example, daily light integral (DLI), which is the amount of photosynthetically active radiation (PAR) received each day as a function of light intensity and duration, can be controlled by interpreting historical weather data and real-time external weather data to control the on/off of the supplemental lights and the covering area of the shade clothes in a greenhouse. Researchers are studying how to improve climate control technologies by implementing advanced technologies, such as artificial intelligence (AI), computer vision, the internet of things (IoT), and robotics to provide biofeedback monitoring and control to further boost plant growth and improve resource use efficiencies.
Maintenance
The greenhouse environment is often harmful to building materials and equipment. A regular program of maintenance for all components of the structure is necessary for trouble free operation.
Even a well-designed ventilation system will not function properly without maintenance and care. When a ventilation system is not operating properly, the results can be pockets of stagnant air, inadequate cooling from evaporative cooling pads, high heating expenses, heavy condensation in winter, reduced life and reliability of ventilation equipment, and high repair bills.
The efficiency of evaporative cooling systems can be greatly reduced by compacted cooling pads, improper operation of fans, greenhouse doors remaining open, and insufficient water supply to cooling pads. The air temperature inside the greenhouse increases whenever the efficiency of evaporative cooling is reduced.
Poorly maintained heating systems can result in harmful fumes being released into plant production areas. Improperly sealed houses require more fuel, to heat. Malfunctioning heater fans result in poor heat distribution and dusty or dirty heating pipes lower heater efficiency significantly.
By carrying out a well-planned maintenance program, the greenhouse operation will be safer, more convenient, and more profitable.
Summary
Many factors should be considered when designing any foliage production structure. Balancing economic, horticultural, and engineering considerations will result in the design of a profitable structure that is easy to maintain and operate.