A greenhouse has one purpose: to provide and maintain the environment that will result in optimum crop production for maximum profit. This includes an environment for work efficiency as well as for crop growth. This publication describes equipment and methods used to control or maintain desirable temperature in a greenhouse during periods when supplemental heat is required. There are many ways effective greenhouse heating can be accomplished, which ultimately depend on the equipment, type of fuel and construction used, and management practices followed. Because each operation usually has unique considerations, it is important to consider the types of plants, level of desired production quality, type(s) of greenhouse(s), and management procedures when selecting and installing a heating system.
Heating Systems
Greenhouse heating systems will be discussed based on the following heat distribution methods, heat source, and fuel used.
Unit Space Heater
Unit space heaters, either floor mounted or supported, are normally fueled with natural or bottled gas or fuel oil and use fans for heat distribution. This system requires a relatively moderate capital investment, is easy to install, and provides an opportunity for easy expansion of facilities. If unit air heaters are used, they should be spaced and directed to blanket the entire area with heated air. The intent is to form a pattern in which each heater is blowing toward the next (Figure 1).
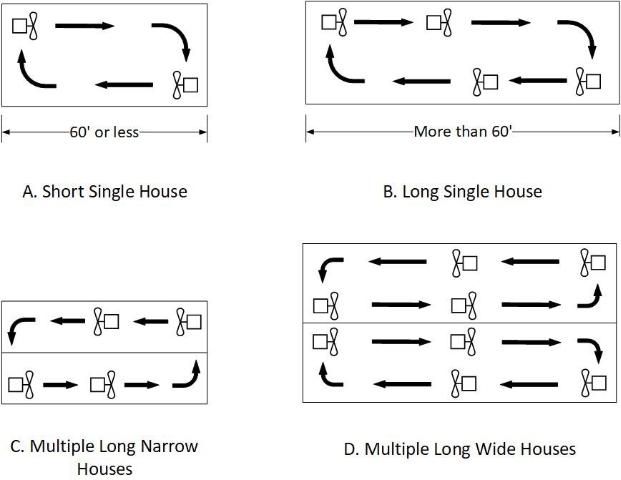
Credit: J. A. Watson, UF/IFAS
It is important to know the possible consequences of the use of unvented or improperly vented gas- or oil-fired units. These units produce carbon dioxide gas, which is necessary for improved plant growth. However, other gases that are harmful to humans (i.e., carbon monoxide) and many plants (i.e., ethylene, sulfur dioxide, and unburned hydrocarbons) are also by-products of combustion. These can cause serious problems if the exhaust gases from unit heaters are not properly vented to the outside (Figure 2) and adequate intake air is not available for combustion. Normal air contains about 400 parts per million of carbon dioxide. Concentrations up to 2,000 parts per million can be used in greenhouses to maximize production. This additional carbon dioxide should come from a commercial carbon dioxide generator (normally using either solid or liquid carbon dioxide), not from combustion. Also, heaters normally operate at night when plants cannot benefit from the carbon dioxide produced due to a lack of light available for photosynthesis. Another by-product of combustion is water vapor. High nighttime concentrations of carbon dioxide and water vapor in a closed greenhouse with a lowered oxygen supply (due to combustion) are generally considered undesirable from a disease control standpoint. Test kits and sensors are available to measure the levels of carbon dioxide in greenhouses. To assure good air movement to the outside through the vent stack, make sure the vent pipe is of adequate size (check the heating unit manufacturer's recommendations) and that it extends at least 48 inches above the highest point of the building. Fresh air intakes sized to accommodate the burner of unit heaters (normally 6–8 inches in diameter) are a necessity in tight greenhouses. Also, proximity to tall buildings or trees that might cause a downdraft to greenhouse ventilation stacks or intakes should be avoided.
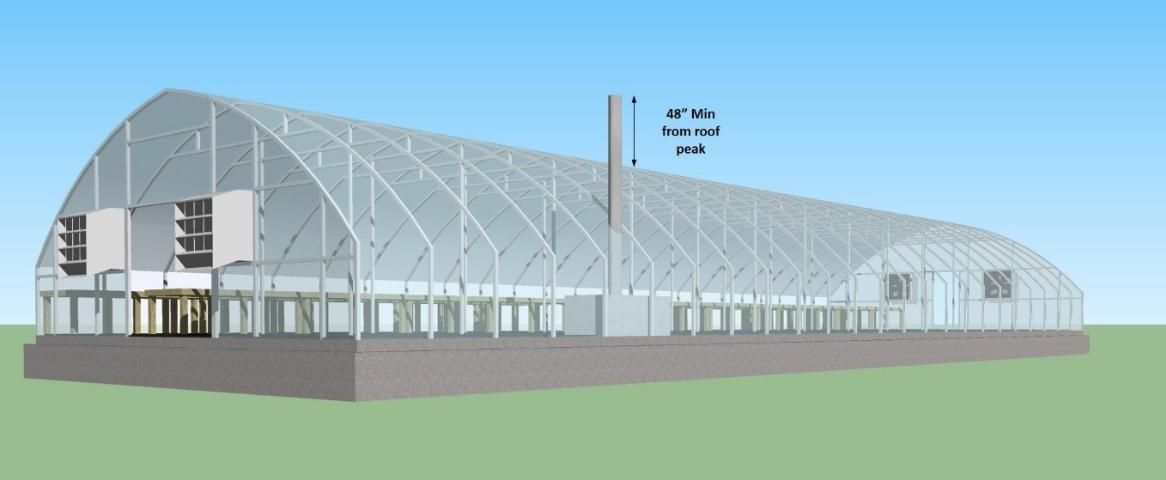
Credit: J. A. Watson, UF/IFAS
Poly-Tube Systems
Convection, poly-tube, or fan-jet systems are frequently used to provide more uniform heat distribution and air movement in greenhouses using unit heaters (Figures 3 and 4). The velocity of air discharged from openings in the tube should not exceed 1,200–1,800 feet per minute (fpm). The volume of the openings (total) should be 1.5–2.0 times the cross-sectional area of the tube.
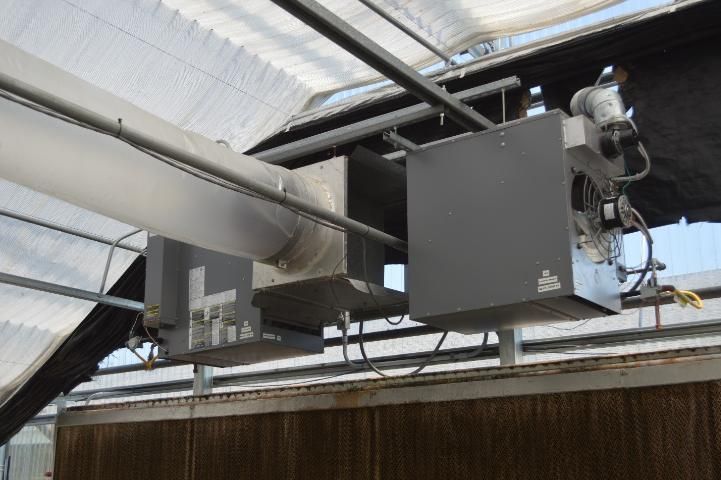
Credit: J. A. Watson, UF/IFAS
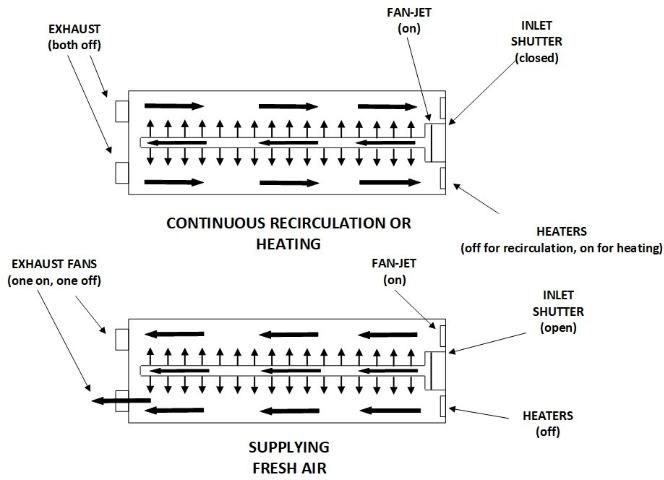
Credit: J. A. Watson, UF/IFAS
Steam Heating System
A steam heating system needs a boiler, valves, traps, and other controls depending on the size and type of boiler used. Steam provides rapid heating and cooling of the steam lines, which may be smooth or finned. When using steam heating, 1/3 of the heat should be distributed overhead, and approximately 2/3 should be distributed along the sidewalls. Lines can also be arranged under benches or with overhead fan-forced unit heaters. A steam system requires a high initial investment and has significant maintenance costs. However, it has a long life expectancy and can allow the use of steam for soil pasteurization. Since steam can be efficiently transported over long distances, steam heating systems are most often used in large greenhouse ranges.
Hot Water Systems
The most common hot water systems use pipes that can be placed in the greenhouse perimeter, under or on top of benches, overhead in the trusses, or under concrete floors. Hot water systems are relatively simple to install and normally require less maintenance than a steam system. They are also slower at heating and cooling pipes, but temperatures are normally more uniform. However, they also have a significant investment cost.
Unit Radiant Heaters
Unit radiant heaters (e.g., the "Salamander" grove heater (return stack) type) that use fuel oil are occasionally used for frost protection (Figure 5). These are not recommended for routine greenhouse heating because they are not thermostatically controlled, making temperature regulation difficult. Also, because they are not vented to the outside of the greenhouse, combustion gases can damage sensitive plant material. These heaters can be used for emergency protection against cold temperatures in southern portions of Florida, but they require close attention when in operation.
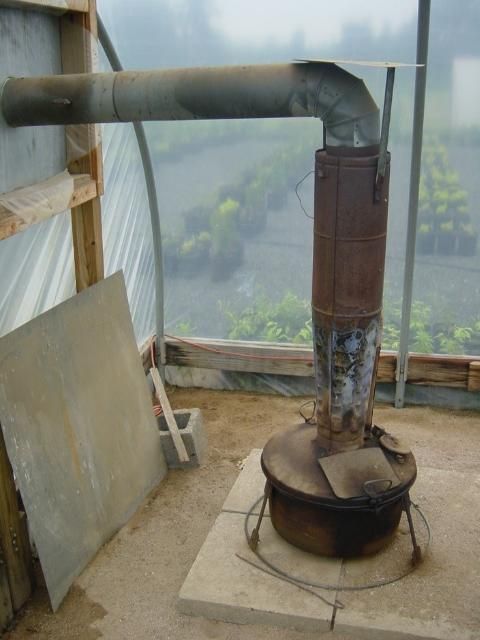
Credit: A. J. Both, Rutgers University
Infrared Heaters
Infrared heaters transfer heat energy to objects in the greenhouse, offering potential energy savings compared to straight air-heating systems. These heaters are often directional, providing uniform heating for a given area inside the structure with some exceptions (e.g., complex canopies such as high-wire tomatoes or roses). The speed at which objects are heated is rapid, because heat is produced almost immediately after turning on the equipment. In addition, infrared heaters keep the surface temperature of plant leaves above air temperature, offering potential advantages for disease management. Exercise caution when operating radiant heaters, because fire can occur if the heater is overturned or if the coils encounter flammable materials. They may also cast undesirable shadows in a greenhouse environment.
Heat Pumps
Heat pumps absorb heat energy from an external area (e.g., outside air, ground, water well, another room) and transfer it into the greenhouse environment, raising the ambient temperature. The process can be reversed in the cooling mode, where heat pumps may transfer the unwanted indoor heat to a cooler area. Heat pumps can operate in extremely cold conditions. However, their efficiency decreases as temperatures drop below freezing, requiring more energy to maintain warm temperatures inside the greenhouse. For maximum efficiency, they should operate year-round, heating in the winter and cooling in the summer. They are compatible with air-duct systems that can evenly distribute warm/cooled air in a greenhouse and are able to provide more uniform growing conditions than other systems. In addition, because heat pumps move heat rather than generate it, they can provide equivalent space conditioning while reducing energy use compared to other heating systems. However, initial expenditures for heat pump systems may outweigh potential energy savings, particularly in states like Florida with relatively short, mild winters.
Solar Radiant Systems
Solar radiant systems provide energy for heating by capturing solar energy and storing it in an insulated tank containing a fluid, typically water, to be used a later time (Figure 6). There are two types of solar radiant systems: indirect and direct. Direct systems operate by heating and storing that fluid for when it is needed. Indirect systems use a fluid for heating and then transfer the energy using a heat exchange to a separate fluid. Indirect systems are better suited to colder climates where fluids may be exposed to freezing outside temperatures; therefore, they are rarely used in areas with warmer climates such as Florida. Although the costs of solar radiant systems have decreased in recent years, these systems may only be practical in the northern parts of Florida.
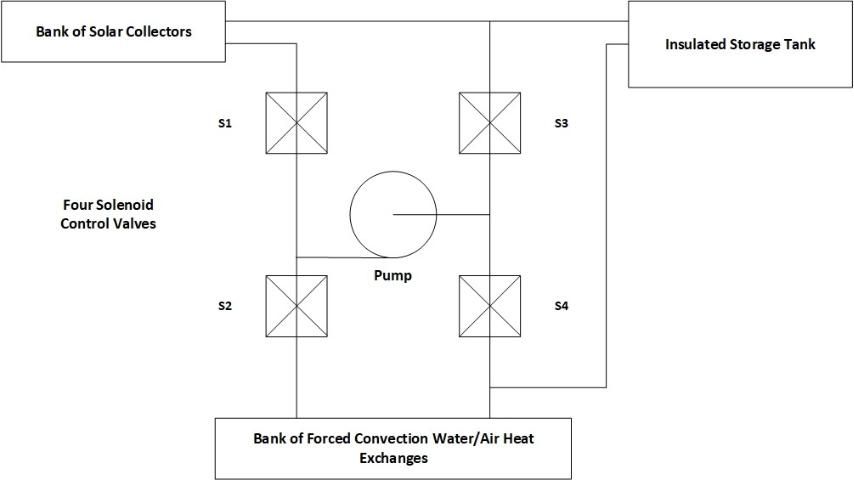
Credit: J. A. Watson, UF/IFAS
Factors to Consider in Selecting a System
A dependable source of heat is necessary for temperature control in greenhouses. The best type of system will depend on many factors, several of which are mentioned above. Operators should consider all factors carefully before investing in heating equipment, since what is best for one operator may not work for another.
Before selecting the type of system to use, it is necessary to calculate the amount of heat that will be required. This value should be based on the most adverse conditions that a grower can reasonably expect to encounter. Occasionally, in central Florida, outside low temperatures can be between 25 and 30°F. North Florida can experience temperatures of 15°F–20°F, while south Florida can have low temperatures around 35°F. The minimum inside temperature depends on the type of plants being grown. Some tropical species cease to grow at 55°F–60°F, and some plants can die if exposed to temperatures of 45°F or below.
Growers must identify the temperatures needed to achieve their objectives, subtract the expected minimum adverse temperature for their location, and obtain the differential in °F for which they need to be prepared.
An easy and fairly accurate method for estimating the amount of heat required is to multiply the surface area of the greenhouse by the maximum temperature difference to be maintained, then to multiply this product by a heat transmission factor that depends on the glazing of the greenhouse structure but is also influenced by the quality and age of construction. A factor of 1.0–1.2 is used if the greenhouse is covered by a single layer of polyethylene film (PE) or rigid plastic. A factor of 1.0 would assume a well-built, tight greenhouse, whereas 1.2 would assume a lower-quality construction with more air leakage. The same will be true for the transmission factors used for other glazing materials.
Wind velocity affects the transmission factor. Heat loss increases with higher wind velocity. Growers must use a factor of 0.75 to 1.0 if the greenhouse is covered with a double layer of PE film with an air space of at least 3/4 inch but not more than 4 inches. A factor between 1.1 and 1.4 must be used if the greenhouse is glass glazed. Add 10% to the values obtained if the greenhouse is in a windy location and has many leaks that allow for air infiltration. For example, a 30 ft x 120 ft gable greenhouse with 6-foot sidewalls will have about 5,750 square feet of surface area through which heat can move. If this greenhouse were covered with rigid plastic and a 40°F temperature difference was to be maintained (65°F at an outside low of 25°F), the heating system would have to supply 5,750 x 40 x 1.2 = 276,000 BTU/hr.
If this greenhouse were very tightly constructed and protected by a wind break of some kind and large glazing panels were used, then growers could use a lower heat transmission factor close to 1.0. The heating input required in this case would be 5,750 x 40 x 1.0 = 230,000 BTU/hr. It should be noted that these heat transmission factors take into consideration factors such as air infiltration and wind effects; therefore, the term as defined herein does not conform to the strict definition of heat transfer coefficient. This BTU/hr figure can be used to determine pipe length in steam and hot water systems, or to size unit heaters. If a central boiler is used, add at least 25% to the heating input requirements for determining boiler size to allow for heat losses in the distribution system. One boiler horsepower equals a heat output of about 33,500 BTU/hr.
Another factor to consider is the efficiency of the heating unit. Most manufacturers of heating equipment show both input and output BTU/hr. Calculations on equipment size must be based on output capacity. The choice of fuel for heating is often a problem of economics, but future availability of fuel sources may be an important consideration. Regardless, the fuel that will provide a dependable source of heat at the lowest cost is generally the one to use (Figure 7).
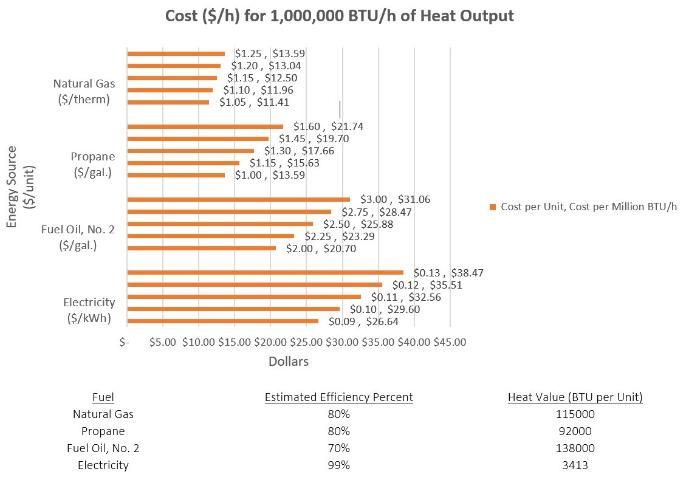
Credit: J. A. Watson, UF/IFAS
In conclusion, the successful heating of greenhouses depends on correct sizing and installation of the heating system, proper controls, and methods of obtaining uniform heat distribution. The type of greenhouse construction, crop-specific requirements, and temperature levels to be maintained are important factors to consider in the selection and design of any greenhouse heating system. For these and other reasons, only those thoroughly familiar with greenhouse heating systems and their application to a grower's specific requirements should be allowed to design and supervise the installation of a heating system.
Recommendations
In general, the following recommendations should be considered.
- The heating system should allow for easy expansion in the future, and it should have enough capacity to offset the heat loss from the greenhouse under severe conditions. Normally, design for temperatures slightly above minimum 15- to 25-year lows, as shown by local weather records.
- Provide an adequate system of automatic controls or be prepared for extensive manual control during severe weather. The most important control in most systems is the thermostat, which is used to control the operation of the heating system. For this reason, the thermostat should be placed at plant level and shielded from direct sunlight. It should also sense "line air." Sensing "line air" is accomplished by placing the thermostat in a small box or enclosure ventilated by a very small capacity fan. Thermostats for greenhouses should be accurate to within at least 2 to 3°F. They must be calibrated against a dependable thermostat several times a year to ensure this degree of accuracy. An inexpensive maximum-minimum record thermometer can easily provide a check on the accuracy of the thermostatic control and is well worth the investment. However, it is not enough to have good control over the heating system. An operator must know what degree of temperature control is necessary for the type of plants being produced. If flowering plants are grown, for example, their flowering is usually timed for certain holiday seasons. Temperature control can be essential to the success of this kind of operation.
- If possible, select a heating system that will allow you to convert from one fuel source to another.