Trickle irrigation is the frequent application of small quantities of water on or below the soil surface. This type of irrigation system delivers water, nutrients, and other chemicals directly to the root zone of the plant. Applied quantities closely match evapotranspiration and nutrient demand. Water is distributed through emitters placed along the water delivery (lateral) pipe in the form of drops, tiny streams, or miniature sprays. Trickle methods include drip, bubbler, and spray irrigation. In some cases, the drip line may be buried under the soil surface, which is called subsurface irrigation. Trickle irrigation systems operate at low pressure; therefore, they require less energy for water pumpage when compared to other irrigation systems. Also, because of their precise application, they conserve water and nutrients when managed well. Primary crops for trickle irrigation in Florida include citrus, vegetables, and ornamentals.
Trickle emitters use small orifices or long flow paths with small diameters to deliver the small flow rates required. Thus, they are subject to clogging by particulate matter, organic growth, or chemical precipitate from the irrigation water. Effective and reliable filtration is required for successful trickle irrigation operation.
Water quality is a major concern in the management of trickle irrigation systems. Clogging of emitters by physical, chemical, and biological contaminants may create a significant problem for the proper maintenance of these irrigation systems.
In Florida, water to be used in trickle irrigation requires filtration and often other forms of treatment. Particulate matter and organic growth can be removed from the water supply using proper filtration. Often, chemical treatment is required to prevent organic growths and/or chemical precipitation in the irrigation system. A variety of filters is available for the removal of physical clogging agents from irrigation water. The choice of filter depends on the origin and quantity of contamination anticipated in the system, as well as the size of the irrigation system. Screen filters should be a primary choice when water is pumped from a well where the only filtration requirement is to remove mineral particulate matter. They are sufficient in the absence of organic contamination. In addition, these filters are usually inexpensive and easy to maintain. To remove both particulate matter and organic growths, media filters (also called sand filters) may be used. Media filters are recommended when large amounts of algae or other organic contaminants are present.
Structure Of The Media Filter
Media filters are well suited for removal of either organic or inorganic particles. Due to their three-dimensional nature, media filters have the ability to entrap large amounts of contaminants. They do not seal off as easily and, therefore, will not clog as often as filters that trap particles on their surface, such as screen filters.
Media filters used in trickle irrigation systems are the pressure type of media filters shown in Figure 1. They consist of fine gravel and sand of selected sizes placed in pressurized tanks. The main body of the tank contains sand, which is the active filtering ingredient. The sand is placed on top of a thin layer of gravel, which separates it from an outlet screen. Sharp-edged sand or crushed rock is recommended for the filtering media since the corners catch soft algal tissue. Crushed granite or silica graded into specific sizes for a particular system are commonly used porous media. The size of particles is very important. Too coarse particles result in poor filtration and possible clogging of the emitting devices, while too fine particles trigger unnecessary frequent backwashing of the filter.
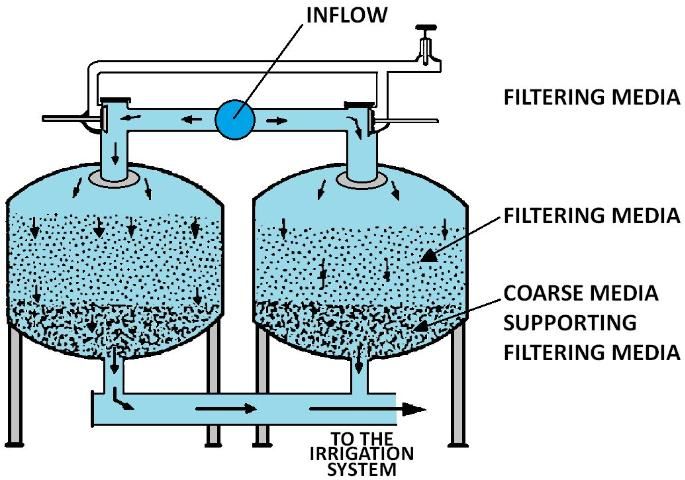
Two factors describe the media used in the filter: Uniformity coefficient and mean effective size. The uniformity coefficient reflects the range of sand sizes within the grade. It is desirable to keep sand particles as uniform in size as possible. The uniform size of filtering media assures better control of the filtration since only particles large enough to clog the emitters should be retained by the filter. Grading in size from fine to coarse causes premature clogging of the filter since even small particles which can be tolerated by the emitters are retained by the nonuniform pores of the media. The uniformity coefficient is represented by the ratio of the size of the screen opening, which will pass 60% of the filter sand, to the screen opening, which will pass 10% of the same sand. For irrigation purposes a uniformity coefficient of 1.5 is considered adequate.
The mean effective sand size is the size of the screen opening, which will pass 10% of the sand sample. It is a measure of the minimum sand size in the grade and, therefore, an indicator of the particle size that will be removed by the media. Some examples of sand media are shown in Table 1. It can also be seen that the quality of filtration increases with a smaller effective size of filtering media.
Flow Through Media Filters
The design flow capacity of a media filter is expressed in gallons per minute of flow per square foot of surface area of the media normal to the direction of flow. The filter should be sized so it can handle the poorest water quality at a given site and provide the required flow for the functioning of the irrigation system. The quality of irrigation water before filtration may vary with the seasons and weather conditions. This is especially true in regard to surface water, but it can also apply to well water in some cases. Table 2 provides data on media filter flow rates for a range of design flow rates per square foot of sand surface. A typical design flow rate for a trickle irrigation system is about 25 gallons per minute per square foot (gpm/sq. ft.). Most systems are designed to allow additional filters to be added in parallel to increase the filtering capacity if required.
Filtration Effectiveness
The effectiveness of a filter is a measure of its ability to remove particles of a certain size. As shown in Figure 2, the effectiveness of filtration increases with a decreasing size of filtering media grain size (larger designation number). However, smaller media sizes will require more frequent cleaning.
Filtration effectiveness is also inversely proportional to the flow rate through the filter. The higher the flow rate, the lower the effectiveness of the media filter. For example, Figure 2 shows that a filter with No. 11 media at a flow rate of 23 gpm/sq. ft. will effectively remove particles of 75 microns (200 mesh). However, the increase in flow rate to 35 gpm will decrease the effectiveness of filtration to 100-micron-sized (140 mesh) particles. Figure 3 shows the increase in pressure differential with time for a typical system. Notice that the pressure loss through a clean filter (circled area in Figure 3) varies between 3 and 8 psi depending on the size of the media and flow rate used. The pressure differential increases with time as contaminants accumulate and partially plug the filter. Figure 3 was developed from field data at one location, hence for a site-specific water quality. Then, this figure should not be used as a guide for filter selection. The slope of all three lines presented in the graph will change depending on the quality of the water. Therefore, the filter manufacturer’s specifications and water quality samples should be used to select a filter based on the application.

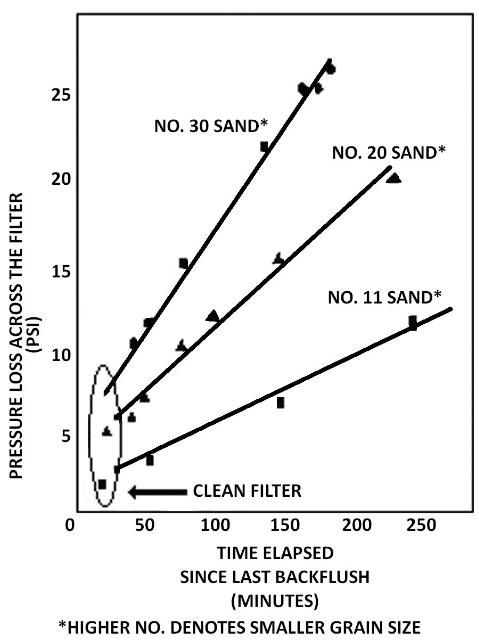
Cleaning Of Media Filters
Media filters are cleaned by backwashing (Figure 4). This operation consists of reversing the direction of water flow in the tank. Clean water is usually supplied from the second tank. The upward flow fluidizes the media and flushes collected contaminants. The backflush water is discharged and does not enter the irrigation system. The backwash flow must be carefully adjusted to provide sufficient cleaning without accidental removal of the media. If flows larger than those recommended are used to backflush the media, it is very likely that the media will be flushed from the filter by the backflow water. Only recommended flow rates for a given media should be used. Table 3 provides the backflush flow rates that are sufficient to backwash a filter.
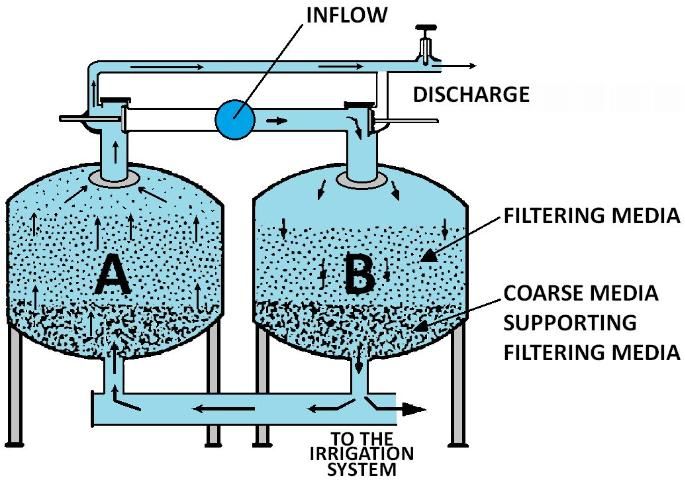
Most media filters are backflushed at prescheduled time intervals or by using automatic devices based on the pressure loss across the filter. For systems in which low quality water requires frequent backflushing, automatic cleaning is necessary to avoid problems. Since the filter is backflushed every time the pressure differential exceeds a predetermined value, large pressure drops in the irrigation system are avoided, maintaining the system's uniformity and efficiency. The pressure differential triggering backflushing depends on the pressure required for the proper functioning of the irrigation system. The irrigation system pump should be able to supply enough pressure to compensate for the pressure drop through the filter just before the filter is washed. Pump capacity must also be adequate to supply enough pressure and flow rate to flush the filter. Also, it is advisable in a large irrigation system to use a number of smaller tanks instead of a few large ones because of the higher backwash flow large tanks require for good cleaning.
Automatic backflush systems will eliminate sudden changes in water quality, which can create problems if a filter is washed only at regular intervals. This is especially important in systems using surface water supplies with changing contamination levels.
Filtering Standards for Trickle Irrigation
The quality of water necessary for a successful operation of an irrigation system depends on the type of trickle emitter used. Emitter manufacturers' recommendations should be used to determine filtration requirements. In the absence of manufacturers' recommendations, a rule of thumb is to filter the water to the equivalent of a 74-micron particle size for drip irrigation. This corresponds to a 200 mesh screen. As shown in Table 1, a media filter with a No. 11, 16, or 20 can provide this degree of filtration. The decision on the media designation number will depend on the emitter passage size and flow rate, water quality, and economic considerations.
Summary
Water supplies for trickle irrigation in Florida often contain organic and inorganic materials that will clog the system if not filtered. Media filters are an efficient form of filtration. They are especially recommended when large amounts of algae or other organic materials are present.
Media filters have the ability to trap large quantities of contaminants and are specifically recommended for organic particles. Proper sizing and design of media filters provide adequate water quality and good performance of the filter. The system must provide a recommended backwash flow for cleaning. Media filters may not be sufficient in some cases where water contains dissolved minerals or organic matter. In these cases, other forms of water treatment and/or additional filtering may be necessary.
Screen filters should be a primary choice when water is pumped from a well where the only filtration requirements are to remove mineral particulate matter. They will be sufficient in the absence of organic contamination, and in addition, they are usually less expensive and easier to maintain than media filters. Table 4 will assist in determining the cause of poor filter performance.
References
ASAE Engineering Practice: ASAE EP405. "Design, Installation, and Performance of Trickle Irrigation Systems." 1984. Amer. Soc. Agric. Engr. - St. Joseph, MI.
Boswell M.J. Hardie Irrigation Design Manual. 1984. James Hardie Irrigation. Laguna Niguel, CA.
Goldberg D., B. Gornat and D. Rimond. Drip Irrigation: Principles, Design and Agricultural Practices. 1976. Drip Irrigation Scientific Publications, Kfar Shmaryahu, Israel.
Jensen M.E. Design and Operation of Farm Irrigation Systems. 1980. Amer. Soc. Agric. Engr. St. Joseph, MI.
Karmeli D., Keller J. Trickle Irrigation Design. 1975. Rain Bird Sprinkler Manufacturing Corporation, Glendora, CA.
Zazueta F.S., A.G. Smajstrla and D.S. Harrison. "Glossary of Trickle Irrigation Terms." 1984. AE-45 Agric. Engineering Fact Sheet - University of Florida.
Yardney Electric Corporation. Water Management Products Division - A New Technology in Water Filtration for Modern Irrigation systems. 1984. Free Flow Filters, Corona, CA.