The Importance of Ladder Safety
Ladders are essential for many types of workplace operations. Folding ladders, extension ladders, and built-in ladders are encountered regularly in many types of work. Safe use of ladders is necessary to prevent serious injury or death. In agricultural settings, tripod stepladders (sometimes called orchard ladders) are commonly used in fruit harvesting.
Falls, including falls from ladders, are among the top three causes of workplace-related injury and death (NSC 2021). More than 500,000 people a year are treated for injuries related to falls from ladders—with about 300 deaths. Surprisingly, most deaths related to falls from a ladder involved a fall of fewer than ten feet (CDC 2014). This is a serious concern for both workers and employers. The estimated cost of these injuries each year is $24 billion, which includes the cost of medical and legal services, lost work, liability, and pain and suffering judgments.
For these reasons, the Occupational Safety and Health Administration (OSHA) has established standards for the ladders that workers use in the workplace to help prevent unsafe equipment use and falls or other injuries from ladders. OSHA Standard 1910.23—Ladders covers all categories of workplace ladders, including portable, fixed, and mobile ladders. This publication summarizes the parts of the OSHA Standard 1910.23 that apply to the portable ladders that are frequently used in agricultural operations.
This article is designed for agricultural producers and interested residents who are using portable ladders for work or non-work purposes.
General Employer Responsibilities
The requirements of the standard are the employer’s responsibility. Employers are required to ensure that ladder equipment is in good condition and that employees use ladders safely. Daily safety precautions include the following:
- Ladders may be used only for the purposes for which they were designed.
- Ladders must be inspected before use in each work shift, and more frequently as necessary to identify any visible defects that could cause employee injury.
- Any ladder with structural or other defects must be immediately tagged "Dangerous: Do Not Use" (or with similar language) and removed from service until repairs are completed.
Some ladders are not covered by OSHA Standard 1910.23. These include:
- Ladders used in emergency operations (e.g., firefighting, rescue, and law enforcement operations) or training for these operations.
- Ladders that are designed into or are an integral part of machines or equipment (e.g., the ladders built into large machinery such as harvesters). These ladders are covered by other standards.
OSHA Standard 1910.23 separates ladders into three types: portable ladders, fixed ladders, and mobile ladder stands and mobile ladder stand platforms. This publication includes a summary of the OSHA standard for portable ladders.
Portable Ladders
Portable ladders are those that can be readily moved or carried (OSHA 2016). Portable ladders may be freestanding, folding, or extendable.
Before using a portable ladder, make sure that it meets general structure, structural integrity, and general safety standards (Figure 1). Do not use a portable ladder with single rails.
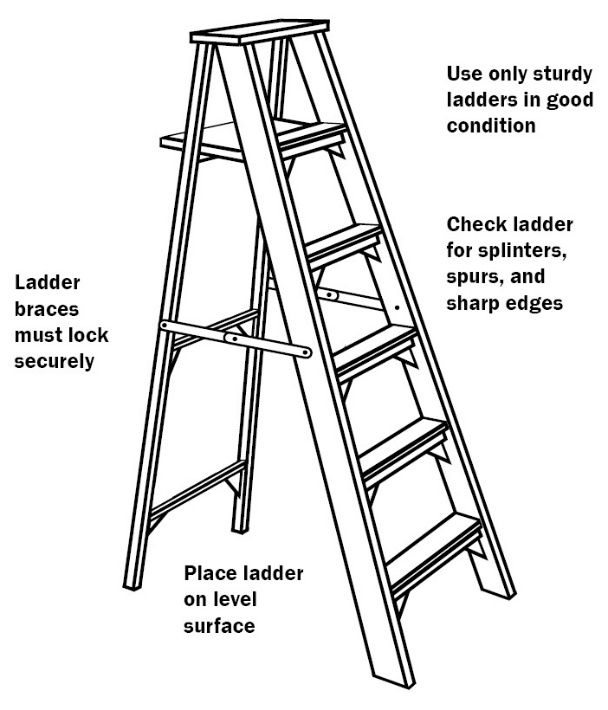
Credit: Charles Brown, University of Florida
Ladder Surfaces
Ladder surfaces must be free of puncture and laceration hazards, such as sharp edges, metal spurs, or splinters. Wooden ladders must not be coated with any material that may obscure structural defects. Metal ladders must be made with corrosion-resistant material or protected against corrosion.
Rungs, Steps, and Cleats: Treads, Spacing, and Width
For all ladders, the employer must ensure that rungs, steps, and cleats are parallel, level, and uniformly spaced when the ladder is in position for use. Rung, step, or cleat means the crosspiece of a ladder on which an employee steps to climb up and down (OSHA 2016). The standard specifies the spacing and width.
Spacing Requirements for Rungs, Steps, and Cleats
The employer must ensure that all ladder rungs, steps, or cleats are evenly spaced between 10 inches (25 cm) and 14 inches (36 cm) measured between the centerlines of the rungs, cleats, and steps.
Spacing Exception: Step Stools
Steps on step stools must be evenly spaced between 8 inches (20 cm) and 12 inches (30 cm) measured between the centerlines of the steps.
Width Requirements for Rungs, Steps, and Cleats
Portable ladder rungs, steps, and cleats must have a minimum clear width of 11.5 inches (29 cm).
Width Exceptions
- Orchard (tripod) ladders: The minimum clear width does not apply to ladders with narrow rungs that are not designed to be stepped on, such as those located at the tapered end of orchard ladders and similar ladders.
- Telecommunication centers: Rungs and steps on rolling ladders used in telecommunication centers must have a minimum clear width of 8 inches (20 cm).
For portable metal ladders: The employer must ensure that rungs and steps of portable metal ladders are corrugated, knurled, dimpled, coated with skid-resistant material, or otherwise treated to minimize the possibility of slipping.
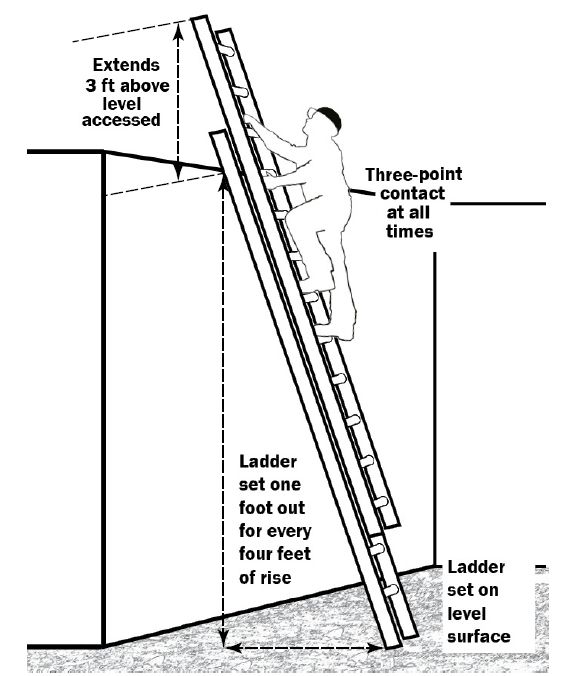
Credit: Credit: Charles Brown, University of Florida
Working Safely with a Portable Ladder
- A portable ladder must lock securely in the open position. Each stepladder or combination ladder used in a stepladder model is equipped with a metal spreader or locking device that securely holds the front and back sections in an open position while the ladder is in use. Tripod or orchard ladders are the exceptions. When using a tripod ladder for harvesting from fruit trees, be sure all three legs of the ladder are stable prior to climbing the ladder (OSHA 2014).
- Set up portable ladders on stable and level surfaces wherever possible. On surfaces that are not stable or level or are slippery, a portable ladder must be secured or stabilized to prevent any movement while in use. Use good judgment about when a surface is not appropriate for a ladder under any circumstances.
- Portable ladders placed in areas where there may be other traffic, such as passageways, doorways, or driveways, must be secured to prevent unintentional movement while in use. Guard the ladder with a temporary barricade, such as a row of traffic cones or caution tape, to keep activities or traffic away from the ladder. If the ladder is not self-supporting, place it so that both side rails are supported, unless the ladder is equipped with a single support attachment.
- Portable ladders used to gain access to an upper landing surface must have side rails that extend at least 3 feet (0.9 m) above the upper landing surface.
- Never stack or assemble ladders to increase their length unless they are specifically designed to do so.
- Never place a ladder on another object to increase its height. Do not place ladders on boxes, barrels, or other unstable bases to obtain additional height.
- Know your portable ladder’s intended maximum load, and do not exceed it. The total maximum load must accommodate the total weight of the employee and all the tools, equipment, and materials (e.g., fruit) the employee is carrying. Remember that stepping down to lower rungs increases the force on the ladder.
- Never move, shift, or extend a ladder while an employee is on it.
- Do not use the top of a stepladder as steps.
References
Centers for Disease Control and Prevention (CDC). 2014. “Occupational Ladder Fall Injuries — United States, 2011.” Morbidity and Mortality Weekly Report 63(16): 341–346. https://www.cdc.gov/mmwr/preview/mmwrhtml/mm6316a2.htm
National Safety Council (NSC). 2021. “Top 10 Preventable Injuries.” Itasca, IL: National Safety Council. https://injuryfacts.nsc.org/all-injuries/deaths-by-demographics/top-10-preventable-injuries/
OSHA. 2014. “Safe Use of Tripod Orchard Ladders.” Accessed March 31, 2022. www.osha.gov/sites/default/files/publications/OSHA3728.pdf
OSHA. 2016. “Walking-Working Surfaces: Scope and Definitions.” Standard Number: 1910.21. https://www.osha.gov/laws-regs/regulations/standardnumber/1910/1910.21
OSHA. 2019. “Walking-Working Surfaces: Ladders.” Standard Number: 1910.23. https://www.osha.gov/laws-regs/regulations/standardnumber/1910/1910.23