Abstract
Fans are used in processing applications involved with drying, ventilating, heating, cooling, aspirating, elevating, and conveying. Processing and other agricultural activities requiring fans are greatly increasing. Costs are becoming more and more important; therefore, it is necessary that a person be able to select and apply the best fan for any installation, taking economic factors into consideration. This article introduces some important fan properties that you should consider when select a fan, such as types, noise levels, volume flow rates and characteristic curves. Inspection and maintenance guidelines are provided for maintaining the functionality of the fans and minimizing breakdowns.
Fan Definition
A fan is an air pump—a machine that creates a pressure difference and causes air to flow. The impeller does work on the air in giving it both static and kinetic energy that varies ln proportion, depending on the fan type.
Fans have generally been classified as either centrifugal or axial flow, based on the direction of air flow through the impeller. Axial flow fans are generally classified as propeller fans, duct fans, vane axial fans, and disc fans. The propeller fan, essentially an air screw, is used for moving large quantities of air against low static pressures and is most commonly used for general ventilation applications. Centrifugal fans are generally used for moving air against high static pressure, such as experienced in grain drying applications. The propeller fan is the most common fan used for ventilation in greenhouses; however, other types of axial flow fans are also used.
Fan Testing
Fans are tested in accordance with strict requirements of AMCA (Air Moving and Conditioning Association) Standard 210. This standard specifies in detail the procedures and setups to be used in testing the various types of fans. Fans are tested under these standard test conditions so that all fans are rated on an equal basis. Thus, fans of different manufacturers and of different types can be rated and compared using the same basis of testing and obtaining performance data.
Fan Laws
Fan laws relate the performance characteristics of any geometrically similar series of fans. Variables generally involved are fan size, rotational speed, volume flow rate, static pressure, horsepower, and mechanical efficiency. The laws governing fan operation provide a useful tool for determining requirements when changing the volume capacity of a fan is required for a given system. At a new fan rotational speed, the new operating point for a given fan can be determined from the fan laws as follows: volume flow rate (CFM) varies directly as fan speed (N), static pressure (SP) varies as the square of fan speed, and horsepower (HP) varies as the cube of the fan speed.
In equation form, the laws are:
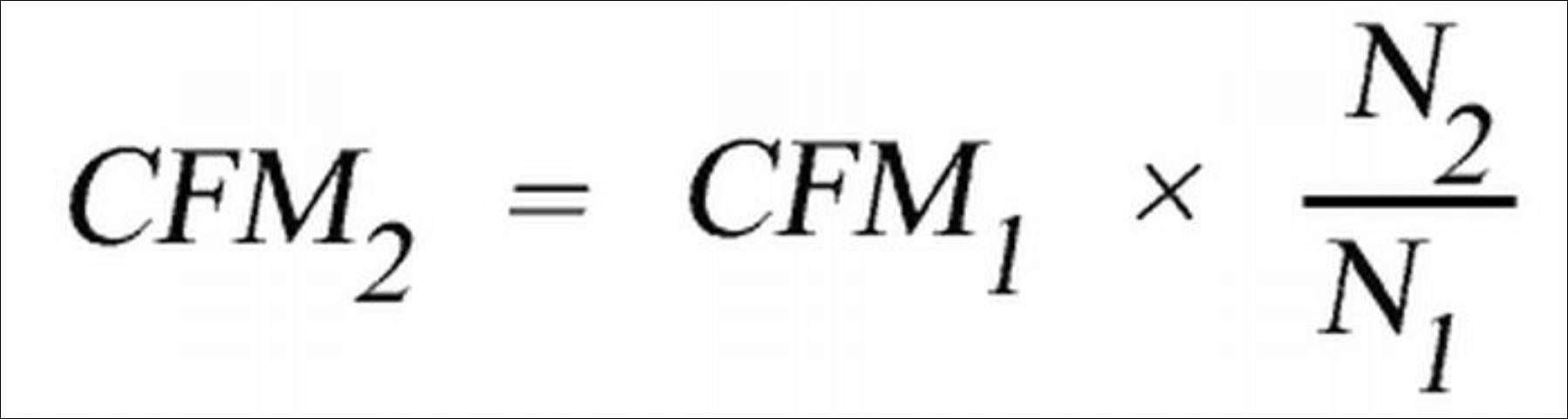
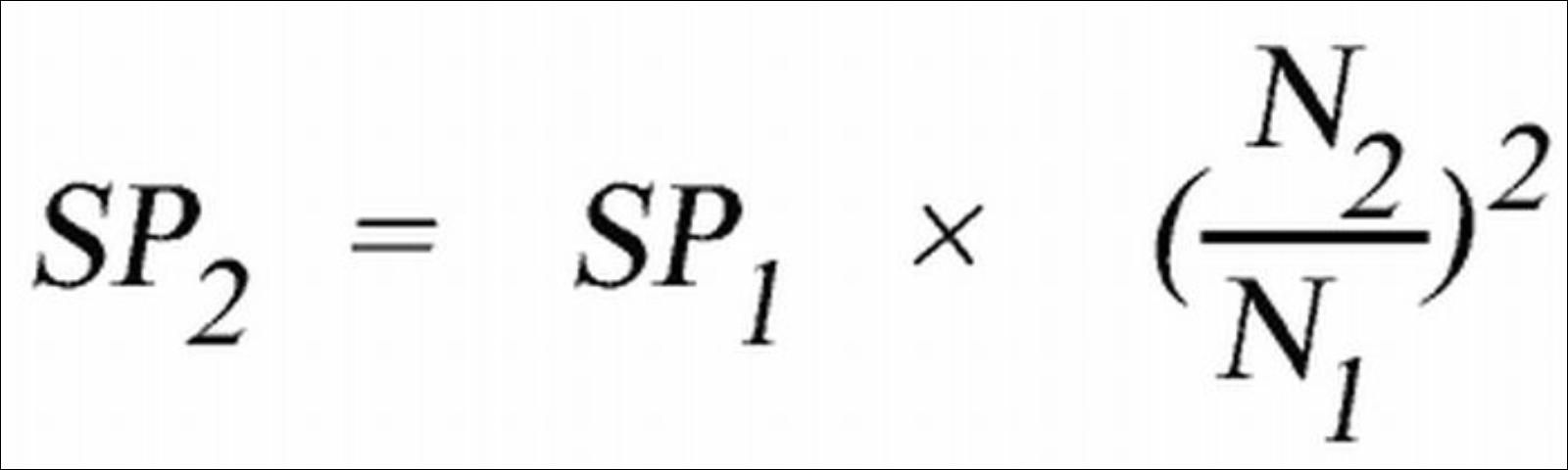
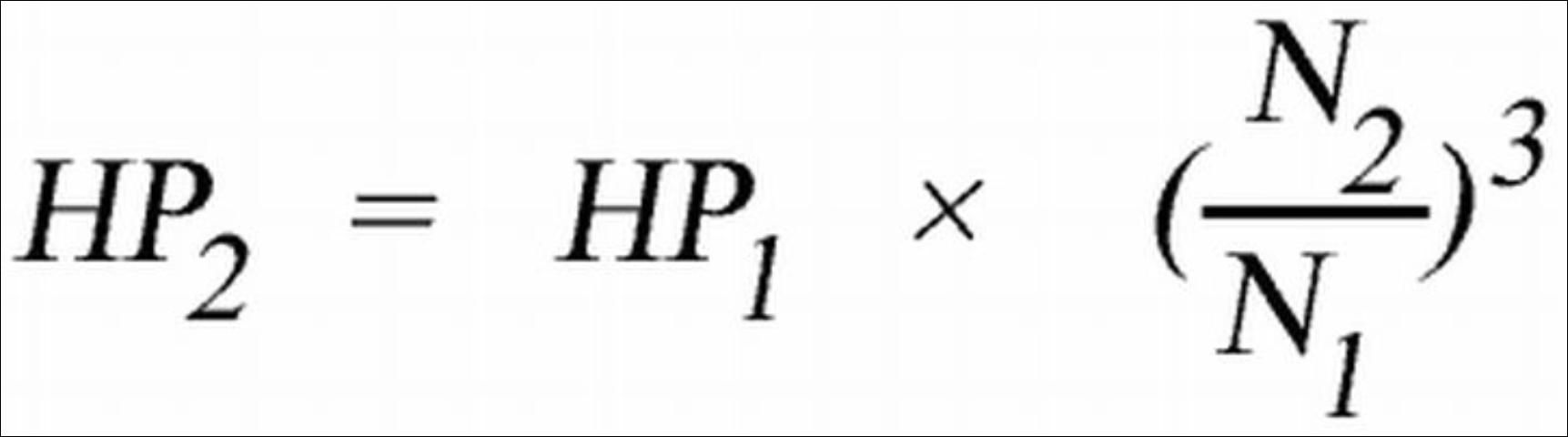
Subscript 2 refers to the new operating point at the new rotational speed N2, while subscript 1 refers to the operating point at the present rotational speed N1.
These laws apply only when all flow conditions are similar. Increasing the speed of a fan causes changes in several important parameters, which may invalidate the fan laws.
Fan Noise
Fan noise is a function of fan design, volume flow rate of air, total pressure, and efficiency. Airstream turbulence is the primary source of airborne fan noise. After making a decision on the proper type of fan for a given application, the best selection of a specific fan must be based on efficiency. The most efficiently operating fan will also be the quietest fan. Low outlet air velocity does not necessarily assure quiet operation. Noise comparisons of different types of fans on the basis of rotational speed is erroneous. The only valid basis for comparison of different fan types is the actual sound power levels generated by the fans when the fans are all producing the required volume flow rate of air at the specified static pressure. Actual fan sound power levels for rated conditions can be obtained from the fan manufacturer as part of the normal fan data.
Fan Selection
When selecting a fan, the following information must be known. These factors will govern the type of fan to be selected and its size:
- Volume of air to be moved per unit time.
- Static pressure—the estimated system resistance and expected variations.
- Space available for installing fans.
- Amount of noise permitted.
- Efficiency—select fan that will deliver required volume at the expected static pressure with the minimum horsepower.
- Economic considerations.
Fan selection is based on the static pressure for a given volume of air that needs to be moved. Although the volume of air desired can be calculated accurately, the static pressure requirement can only be estimated. For most greenhouse applications, the static pressure resistance will be no higher than 0.10 to 0.15 inches of water. However, when using fans as part of an evaporative cooling system, be sure to obtain the static pressure drop across the cooling pad from the manufacturer.
If the actual system pressure requirement for a given volume flow is known, the characteristic curve of a system can be calculated. Air systems are typically turbulent, in which the pressure drop is a function of the velocity squared. Therefore, for most normal systems, this curve is a parabola as shown in Figure 1 with its origin at zero volume, zero pressure, with the pressure varying as the square of the volume (cfm). Thus, if the volume flow through a given system is doubled, then the pressure required will be four times greater.
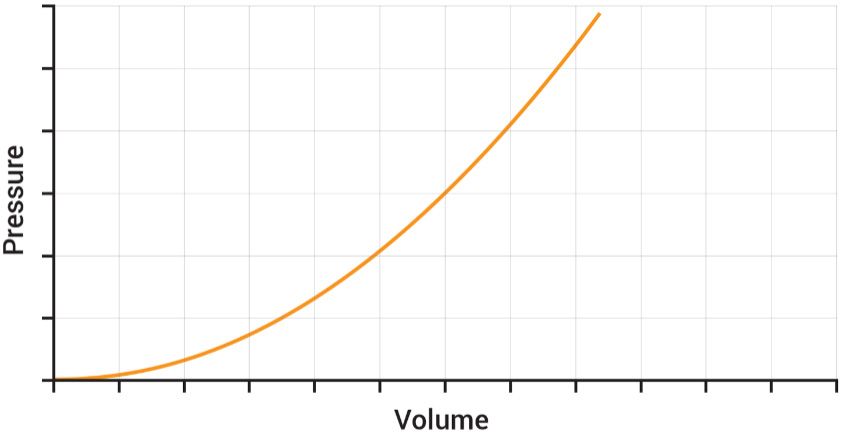
Credit: Jean Pompeo, UF/IFAS
A fan at a given rotational speed has a characteristic pressure-volume curve from wide open volume with no static pressure resistance to block tight with no air movement. A typical fan characteristic curve is shown in Figure 2. When the fan characteristic curve is superimposed on the ventilation system characteristic curve as shown in Figure 3, the intersection of these two curves is the point of operation and is the only point on the system curve at which the fan can operate. Selecting a drive that will allow fan speed to be easily changed within recommmended limits is important because system pressure requirements are never exactly known.
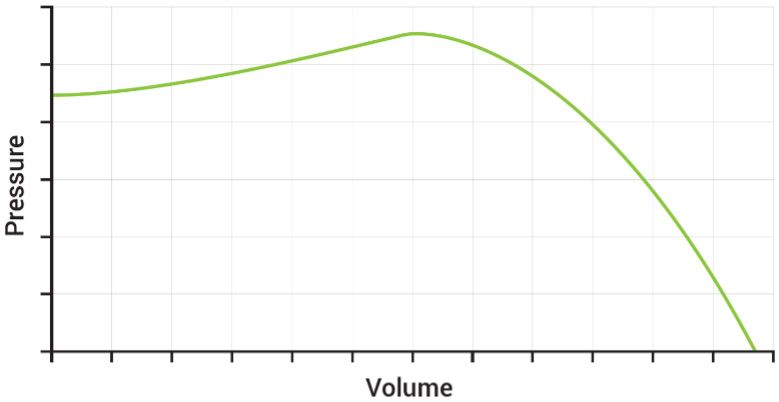
Credit: Jean Pompeo, UF/IFAS
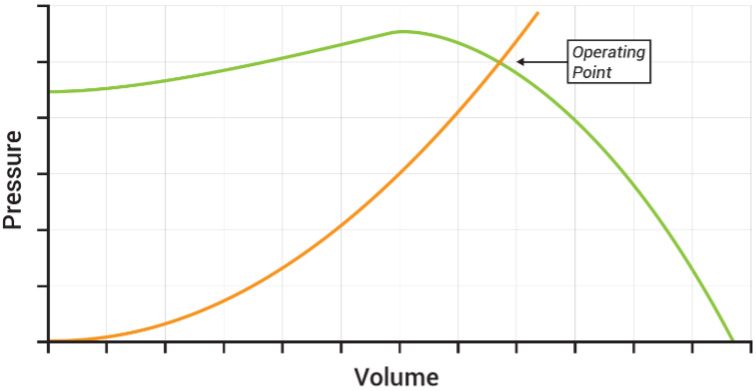
Credit: Jean Pompeo, UF/IFAS
Typical fan characteristic curves are shown in Figure 4 for a centrifugal blower (1), vane-axial fan (2), and propeller fan (3). The curves indicate that as static pressures increase, the volume flow rates decrease when operating to the right of the maximum points (denoted as A in Figure 4). The peak pressure of a fan characteristic curve corresponds to the conditions under which a specific fan will operate most efficiently. Furthermore, this point also corresponds to the operating conditions where the given fan will be the quietest. A fan should never be operated to the left of the peak pressure because the air flow across the fan blades usually becomes unsteady and may produce undesirable pressure fluctuations and noise.
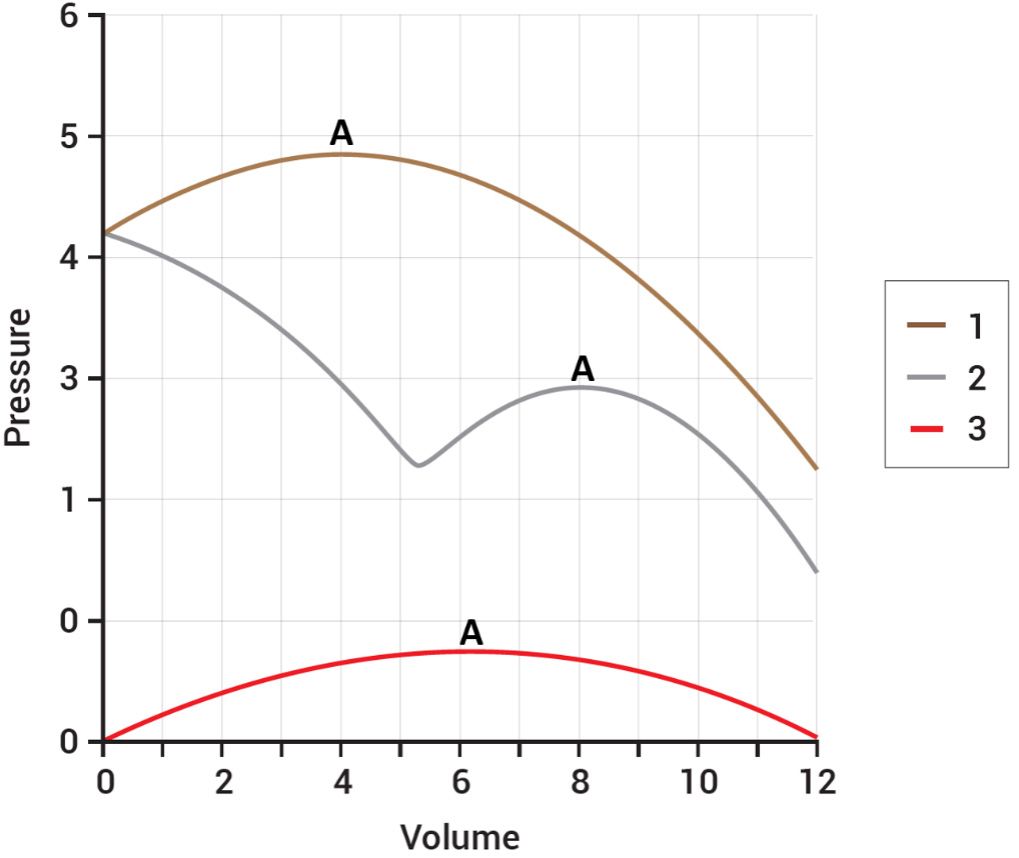
Credit: Jean Pompeo, UF/IFAS
Most fan manufacturers do not supply fan characteristic curves for the fans in their sales literature. However, they do supply fan rating tables that supply the static pressure- volume relationships to the right of the peak pressure. A fan rating table is presented in Table 1 for three different fans that are capable of supplying about 10,000 cfm (cubic feet per minute) of air.
Fan 1 delivers 10,200 cfm at conditions of free air. Free air means there is no static pressure. However, at 1/8 in. static pressure, the air flow rate drops to 9200 cfm and finally to 4300 cfm at 3/8 in static pressure.
Fan 2 supplies 10,200 cfm at l/8 in. static pressure and drops to 7560 cfm at 1/8 in. static pressure.
Fan 3 delivers much more than 10,000 cfm at all static pressures below 3/8 in. Only at 3/8 in. static pressure does Fan 3 deliver 10,400 cfm. If you are selecting a fan to deliver 10,000 cfm for greenhouse ventilation and the expected static pressure in the greenhouse is l/8 in. of water, then the proper choice would be Fan 2. Fan 1 could not deliver enough air at l/8 in. static pressure and Fan 3 would deliver too much air.
Table 2 presents fan rating data from two fans capable of delivering approximately 10,000 cfm at l/8 in. static pressure. For ventilation in a greenhouse, Fan 2 would definitely be superior to Fan 1 in all respects. Fan 2 would be much more efficient because it operates close to its peak pressure whereas Fan 1 would be operating far to the right of its peak pressure. Consequently, Fan 2 would be quieter than Fan 1. Furthermore, Fan 1 would be more expensive than Fan 2 because of its incapabilities that are not being utilized in this application.
Whenever selecting a specific brand of fans, make sure the fan manufacturer tests and rates the fans according to AMCA standards. Otherwise, the performance characteristics supplied with a fan may not be dependable. All reputable fan manufacturers rate their fans in accordance with AMCA standards.
Fan Inspection and Maintenance
Scheduled inspection of fans is recommended. Items checked should include:
- Bearings for over heating (lubricate or replace as required).
- Belt drives for proper tension to prevent slipping.
- Fan wheel for proper rotation.
- Dust accumulations on fan blades, housings, and shutters.
- Weeds and shrubs growing outside the greenhouse that block the fans.
Accumulations on a fan will cause vibrations that can normally be detected when bearing are checked. Dust accumulations must be removed from fans, housings, and shutters on a regular basis to maintain balance of the impeller to prevent excessive vibrations and to move air efficiently. When an impeller is unbalanced, the volume of air moved by the fan can easily be reduced by 30 or 40 percent. Fan rotation is often reversed with repair or alterations to wiring circuits or starters. Since fans do move a fraction of their rated capacity when running backwards, such incorrect operation often goes unnoticed in spite of the much less effective performance of the ventilation system.
Fan Motor Selection
Generally when a fan is selected for a given application according to the guidelines presented earlier, the recommended motor size is supplied by the equipment supplier. For most greenhouse applications where humidities are extremely high at times and where the air can be quite dusty at other times, it is absolutely essential that the specified motor be totally enclosed and have sealed bearings. A totally enclosed motor is required to protect the motor windings from the corrosive effects of the high humidities and dust accumulations that would shorten the service life of the motor.
It is important that the motor be properly matched to the fan. A relatively small motor will not be capable of accelerating the impeller to its intended speed, or the motor may heat up to point where a circuit breaker will trip out or damage to the motor may occur. Too large a motor will be inefficient because of both higher initial and operating costs.