Introduction
Energy consumption is often a primary contributor to the cost of operation in aquaculture. All the electrical needs associated with keeping aquatic plants and animals alive on an aquaculture facility contribute to total energy consumption. Even on a moderately sized farm, excessive energy consumption can be a limiting factor in the success of an aquaculture business. Total profitability can be increased by reducing operational costs. Identifying inefficient energy use and implementing energy-efficient technologies can help reduce the total cost of operation. This publication is one in a series that details techniques and methods for reducing energy consumption to decrease operational costs on aquaculture facilities.
In many aquaculture practices, especially finfish culture, water must be moved from one location to another. Pumping water on aquaculture operations often accounts for a significant portion of a facility’s energy use and operational costs. This publication discusses how variable frequency drives (VFDs) can be used to reduce energy consumption of pumps.
Pumping
There are many different types of pumps, but centrifugal pumps are the type most commonly used in aquaculture. Centrifugal pumps use a high-speed rotating impeller to move fluid from the inlet through the outlet. This simple design allows pumps to be offered in many sizes and configurations at low cost. Most electric pumps used in Florida aquaculture facilities are single speed. Single speed pumps limit the user’s ability to adjust pump speed and output depending on desired operating conditions. The flow of water in aquaculture systems that employ single speed pumps is typically controlled by an arrangement of valves. Any excess water flow must be throttled or bypassed back to the sump during times of low demand. When unneeded water flow is recirculated into the sump or throttled excessively with valves, more power is consumed by the pump than necessary. Additionally, some aquaculture systems control pumps with tanks and float switches or pressure switches. This can cause pumps to cycle on and off frequently, leading to increased power consumption and wear on electrical equipment. When being started from a stopped position, electric motors use excessive power during the first few moments. Although some aquaculture systems operate at a continuous capacity, most have varying levels of demand. Since pumps account for a significant portion of energy use in aquaculture, the ability to reduce their output electrically and operate them more efficiently is beneficial.
Unlike single speed pumps, pumps capable of variable speeds allow operators to adjust the speed of a pump to match varying operating conditions electrically. Controlling the flow of a system by adjusting the speed of the pump will generally be more efficient than throttling flow with valves and bypasses. Energy use of a pump can be decreased by reducing the pump’s speed when less than maximum water flow is required. A pump operating for long durations at low speed can consume less energy than a similarly sized single speed pump throttled excessively with valves or frequently cycling on and off. Many variable speed pumps in aquaculture use variable speed drives (VSDs) to adjust pump motor speed electrically. When changing the speed of a pump, flow and pressure will also change. When considering a single speed pump and variable speed pump of similar configuration, both will have a similar maximum output. However, the variable speed pump can be controlled electrically to reduce output.
Electrical Phases
When discussing energy-efficient technology and electric pumps, understanding common types of electrical delivery is necessary. Single phase and three phase electricity are the two types of power delivery found on aquaculture facilities. Single phase electricity is most common and costs less to have delivered by the service provider. Single phase pump motors are usually offered in 120- and 220-volt options and many times can be wired for either voltage. Three phase electricity is common on commercial facilities and is required where electrical loads are large. Three phase electricity delivers power and operates equipment more efficiently. Additionally, three phase equipment and supporting infrastructure are often cheaper. Three phase is available in several high- and low-voltage configurations depending on the service provider’s delivery equipment.
Variable Speed Drives (VSD)
Variable speed drives are devices that regulate the speed and output of electrical motors electrically. Two kinds of VSDs are used in aquaculture: drives used for alternating current (AC) motors and drives used for direct current (DC) motors. VSDs used for DC motors are simply called VSDs; those used for AC motors are called VFDs. Many variable speed aquaculture pumps, especially those of less than three horsepower (hp), use DC permanent-magnet motors and have a DC motor VSD built into the pump controller (Figure 1). A VSD converts AC power into variable DC power to control the speed of the pump motor. These pumps should be considered in smaller recirculating systems that require pumps of about 3 hp or less and in systems where the required flow may vary due to seasonality or production cycles. Since most large single speed pumps currently used in aquaculture are powered by AC motors, we will discuss variable frequency drives (VFDs) for the remainder of this publication. However, it is important to note that other kinds of VSDs exist and can be effective tools for efficient management of electrical equipment.
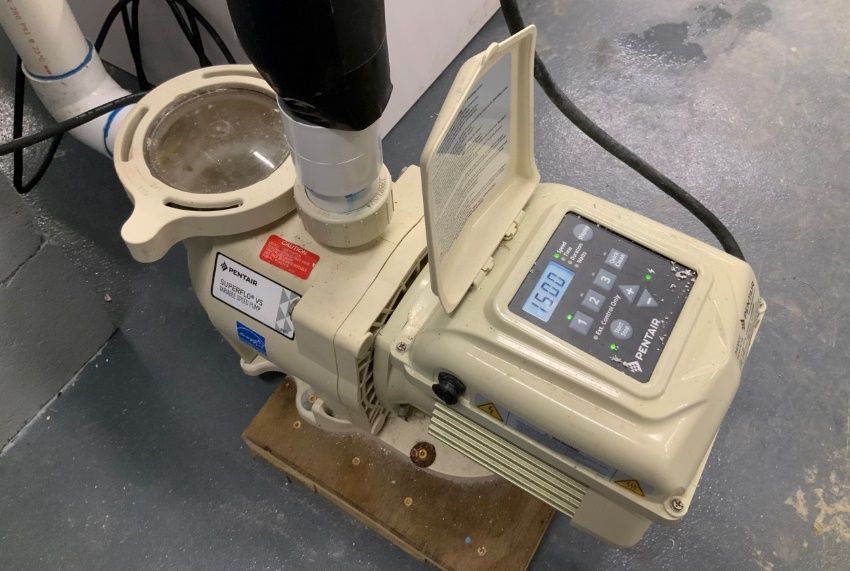
Credit: Micah Alo, UF/IFAS
VFDs can adjust the speed of a pump motor by varying the frequency and voltage powering the motor. They can be operated on single or three phase power but must be used with three phase AC electric motors. In addition, VFDs tend to be most useful on larger-capacity pumps (3 hp or more) and are available in many configurations. VFDs consume small amounts of power to operate; however, by using a VFD to lower a pump’s output during times of low demand, overall energy consumption can be reduced. The pumping system’s specific requirements should be considered when deciding what pump and VFD device is best.
When a VFD is used to reduce a pump’s output, energy consumption of that pump is also decreased. Decreasing the speed of an electric motor by 20% will result in reduction of power consumption by nearly 50%, and decreasing the speed of an electric motor by 50% will reduce power consumption by over 85%. Applying a VFD to a pump to reduce the output of that pump is like applying a smaller pump to the same system. Since many aquaculture systems don’t need to run at maximum capacity full time, energy consumption can be reduced with the use of VFDs. The use of VFDs to control pump output can also reduce the cost of pumping systems by eliminating the need for mechanical components used to regulate flow. Using VFDs can reduce operational costs and may also reduce or streamline overall water use on a facility. When considering that many farms operate numerous pumps, the cumulative savings can be significant.
Using Variable Frequency Drives
Variable frequency drives should be considered in aquaculture systems where the pump runs for extended periods of time and flow requirements may vary 20% plus or minus due to production cycles, seasonality, or management practices. Pumps equipped with VFDs are most useful when pumping water short vertical distances through many pipes and fittings. For example, a VFD may not be beneficial for pumps on residential water wells but can be good for aquaculture systems with large amounts of variable water flow. However, if a pumping system’s flow requirements do not vary, a single speed pump would likely operate more efficiently than a VFD-equipped pump.
Other benefits of VFDs are programable controls that can help relieve management duties otherwise done manually. Most VFDs used for pump control can be configured to control pressure, flow, or water levels automatically using auxiliary sensors. Pressure and flow in aquacultural systems can be automatically maintained using sensors that tell the VFD-equipped pump to speed up or slow down based on water demand. These programable smart features can also protect pumps from cavitation, short circuiting, thermal overloading, and current and voltage overloading.
However, a VFD’s utility and potential savings can be jeopardized by poor installation and mismanagement. Although VFDs can be used to save energy and manage flow, care should be taken to use them properly. An incorrectly sized pump operated by a VFD does not guarantee savings and can be less efficient. Because VFDs canrun pump motors much slower and faster than their originally designed speed, users should not operate the pump beyond its limitations to avoid damaging it. Additionally, VFDs should be installed inmanufacturer-approved locations and enclosures. Mounting locations and enclosures shouldavoid areas where they could become compromised with water or chemical runoff. They should be placed in areas where they will receive ample ventilation for cooling. Ideally, enclosures should be mounted in the shade or inside a climate-controlled building. Electrical wiring from the VFD to the pump motor should also meet the VFD manufacturer requirements. Variablefrequency drives produceelectro-magnetic and radio frequencies that can interfere with nearby low-voltage electronics;using shielded wire helps prevent this from causing issues with motor controls and other vulnerable equipment. Users should routinely check electrical connections andthe integrity of enclosures and clean the VFD with dry compressed air. If installed, operated, and maintained correctly, VFDs can last up to ten years or more.
UF/IFAS Tropical Aquaculture Lab Water Distribution System Evaluation
The UF/IFAS Tropical Aquaculture Lab (TAL) is located on 6.5 acres and has five greenhouses and a large building, each containing multiple aquaculture systems. These aquaculture systems are primarily supplied with treated freshwater by TAL’s main water distribution system. In a study conducted at TAL, water use and energy consumption for the main water distribution system was compared using a single speed pump and a pump fitted with a VFD. Initially, a 3 hp, single phase, single speed pump was controlled using a pressure switch and a series of pressure tanks. To maintain proper pressure in the system, the pump worked to fill the tanks when the pressure and volume of water in the tanks dropped below a minimum value. This caused the pump to cycle on and off frequently, especially during times of low demand. This system was replaced with a 5 hp, three phase pump equipped with a VFD (Figure 2). A pressure transducer is used with the VFD to automatically adjust the speed of the pump based on the pressure in the system. By continually adjusting the speed of the pump, a near-constant pressure can be maintained independent of downstream water demand. Both pumps can provide similar maximum flow and pressure. By applying a VFD-controlled pump to TAL’s main water distribution system, we achieved a decrease in energy use of approximately 60% (Figure 3). A similar result was achieved with TAL’s pond aeration system that supplies air to 48 ornamental fishponds (roughly 30’ wide x 60’ long x 6’ deep). In this instance, two 5 hp, single-phase blowers were replaced with one 15 hp, three phase blower controlled by a VFD. This change resulted in a 25% decrease in energy consumption without sacrificing performance.
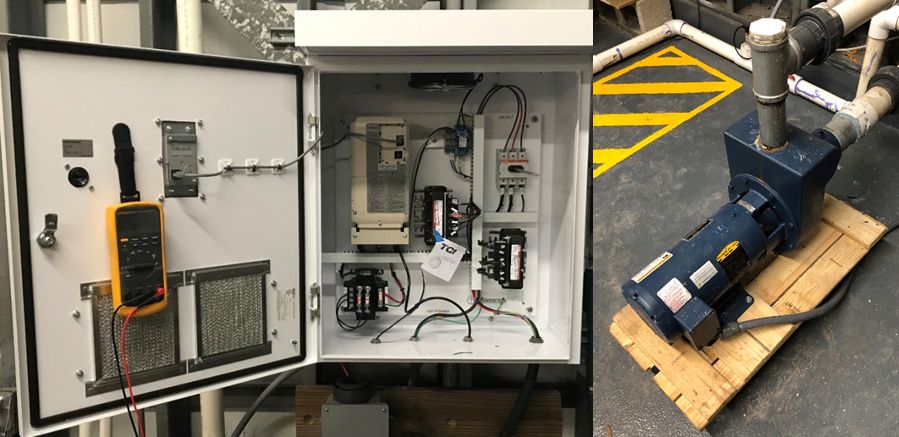
Credit: Jordan Neff, UF/IFAS
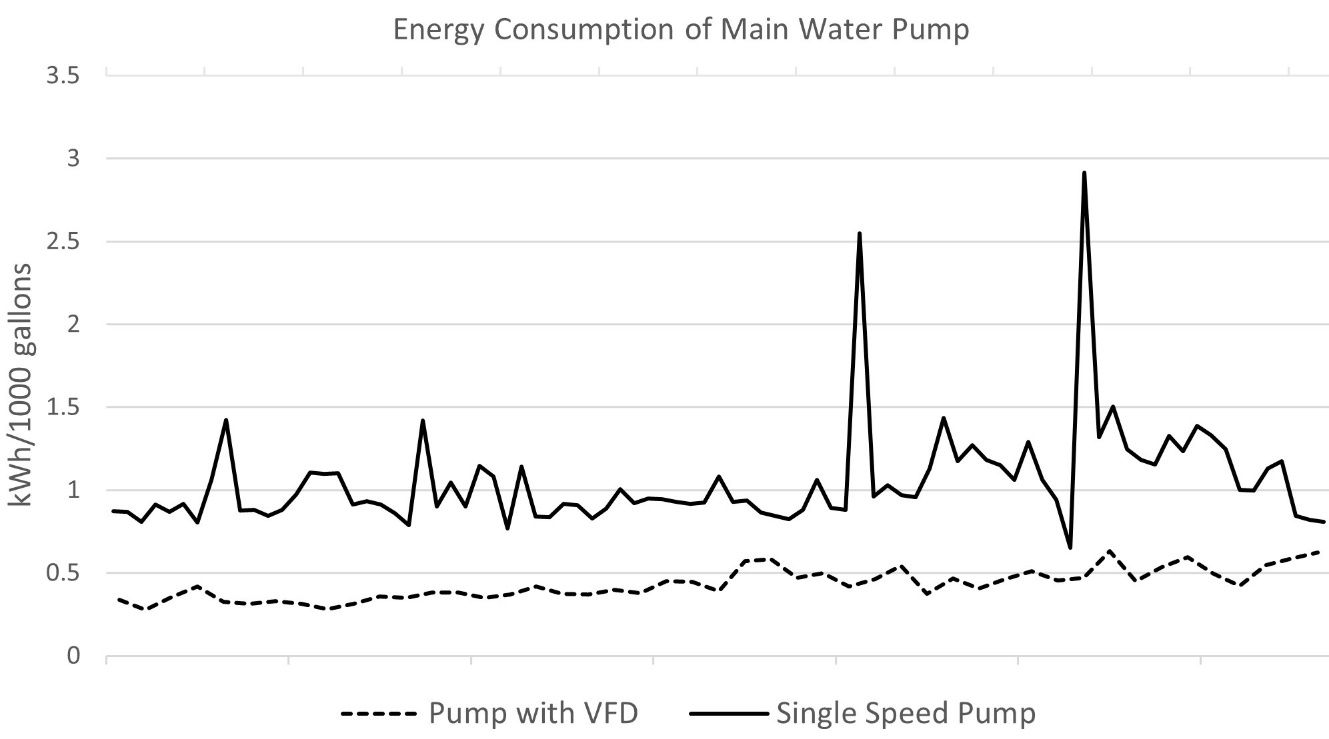
Credit: UF/IFAS
Conclusion
Energy consumption of pumps on aquaculture facilities can contribute to a significant portion of total operational costs. Using VFDs to reduce the output of a pump when less than maximum performance is needed can reduce the energy consumption of the pumping system. Reducing pump motor speed to decrease output will reduce energy consumption. The application of the VFD at TAL demonstrated that significant energy savings can be achieved. Finding ways to decrease energy consumption can benefit both aquaculture producers and utility providers. This publication describes how implementing VFDs in pumping systems can reduce on-farm energy consumption and operational costs.
Recommended Reading
Bankston Jr., J. D., and F. E. Baker. 1994. Selecting the Proper Pump. USDA Southern Regional Aquaculture Center Publication No. 372. https://srac.tamu.edu/fact-sheets/serve/69
Bankston Jr., J. D., and F. E. Baker. 1995. Powering Aquaculture Equipment. USDA Southern Regional Aquaculture Center Publication No. 375. https://srac.tamu.edu/fact-sheets/serve/72