Introduction
Blueberries are grown commercially in Florida for the early-season fresh fruit market. The majority of Florida’s southern highbush blueberry crop is currently harvested by hand to ensure high quality standards for fresh fruit production. However, hand harvesting is the single greatest annual production cost for Florida blueberry growers, and mechanization of berry harvests could greatly reduce production costs. This is particularly important when considering the volume of fruit imported into the United States from countries where labor rates are significantly lower. Also, harvest labor may not be available to Florida growers when they need it, which is an issue mechanization could help address. This publication provides information for commercial blueberry growers interested in adopting machine harvesting.
Along with the significant benefits of machine harvesting, there can be a few challenges.
- If fruit is not firm enough, it can be bruised when it falls from the plant to the harvester catch plates. This can result in lower packouts, an increased risk of postharvest disease, and reduced shelf life.
- If the harvester scales do not close tightly around the crown of the plant (i.e., the base from which all of the canes grow), some of the harvested fruit will fall to the ground and be lost.
- The harvesting equipment can sometimes detach immature fruit along with ripe fruit, especially early in the season or with certain varieties.
- The harvester can damage blueberry plants in some cases by breaking canes or uprooting plants.
- Harvesting equipment can damage weed mat covering on beds.
- Training plants to have a narrow crown and subsequent hand pruning can be costly in supplies and labor.
With newer cultivars that are more suitable for machine harvesting, improving technology, and increasing knowledge and experience with machine harvesting, some Florida growers are incorporating machine harvesting into their overall harvest management plan. When preparing new blueberry fields, growers should consider whether machine harvesting will be part of their harvesting operation. This publication discusses considerations for new field design and early plant establishment if machine harvesting is likely to be used for even a portion of the harvest. For example, some growers hand harvest but may utilize machines to harvest during the later part of the harvest season after berry prices have dropped and/or labor is in short supply.
Machine Harvesting Equipment
In Florida, the most commonly used machine harvesting equipment is an over-the-row, self-propelled harvester (Figure 1). The interior section of the harvester consists of two rotary drum shakers that have several rows of rods and move vertically to dislodge ripe fruit from the blueberry bushes (Figure 2). The fruit falls onto catch plates (Figure 3), then moves onto conveyor belts that transport the fruit to the top of the harvester and into fruit lugs (Figure 4). Operators vary both the speed of the rod movement and the forward movement of the harvester to optimize the detachment of ripe fruit and minimize the release of green fruit. Later in the season harvesters are frequently operated at night, when cooler temperatures allow growers to avoid picking in the heat of the afternoon, which can lead to softer fruit.
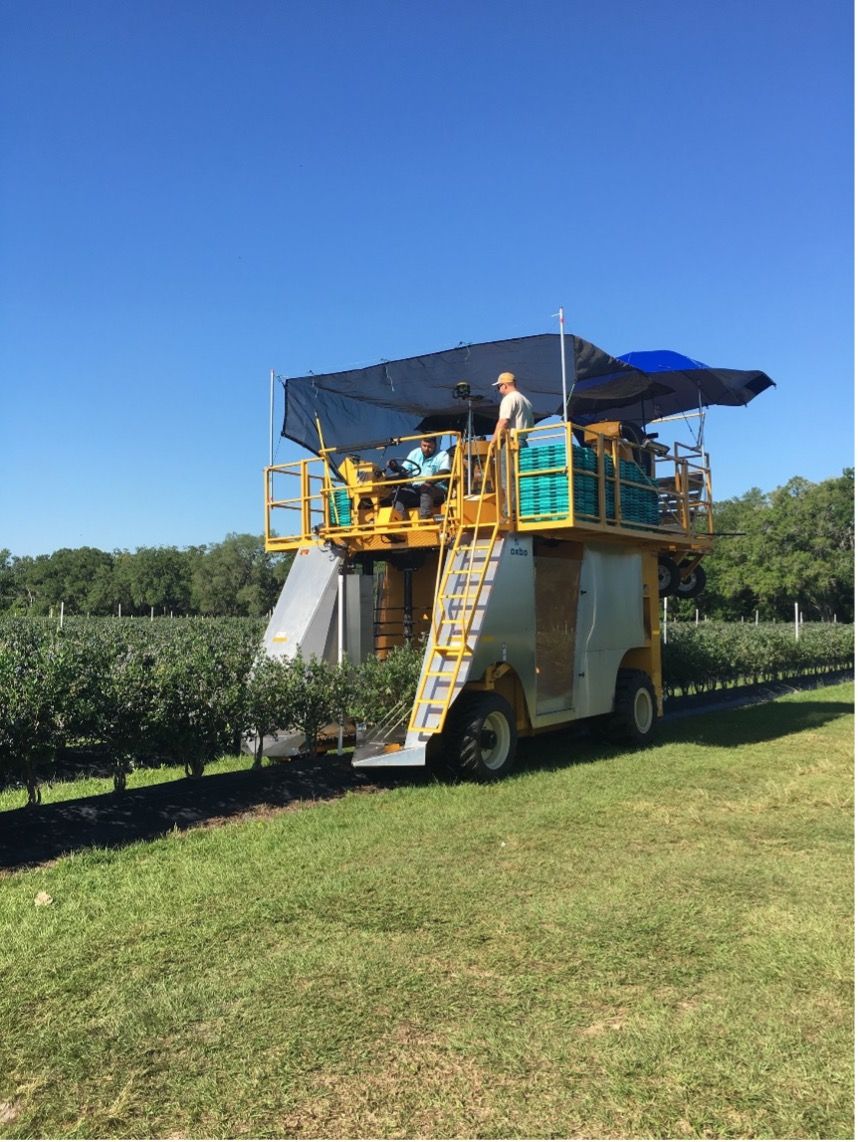
Credit: Doug Phillips, UF/IFAS
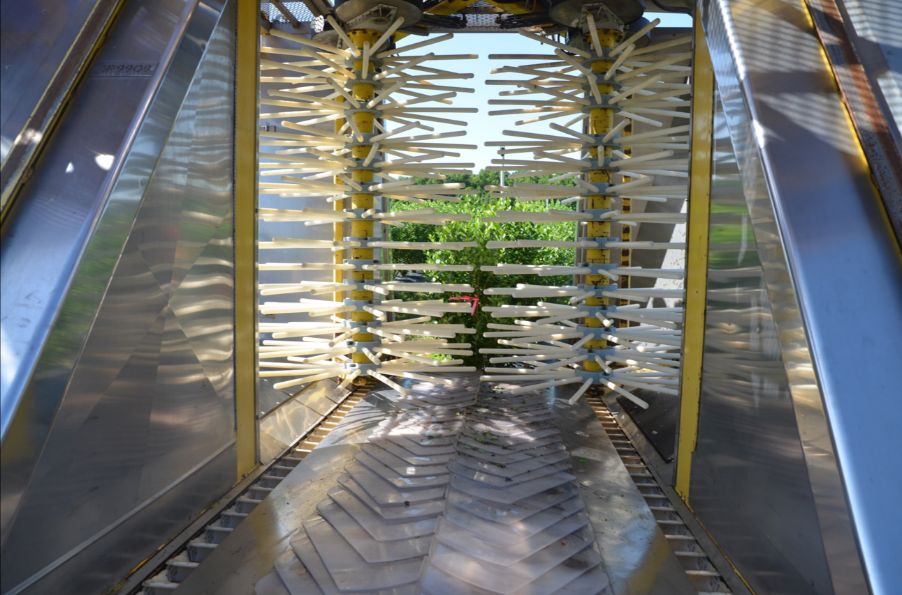
Credit: Jeff Williamson, UF/IFAS
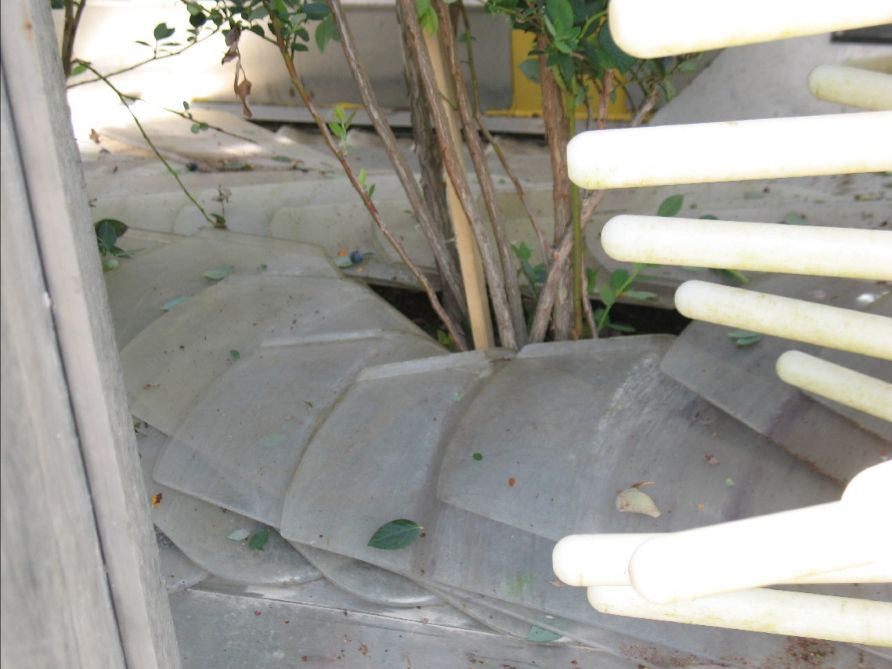
Credit: Jeff Williamson, UF/IFAS
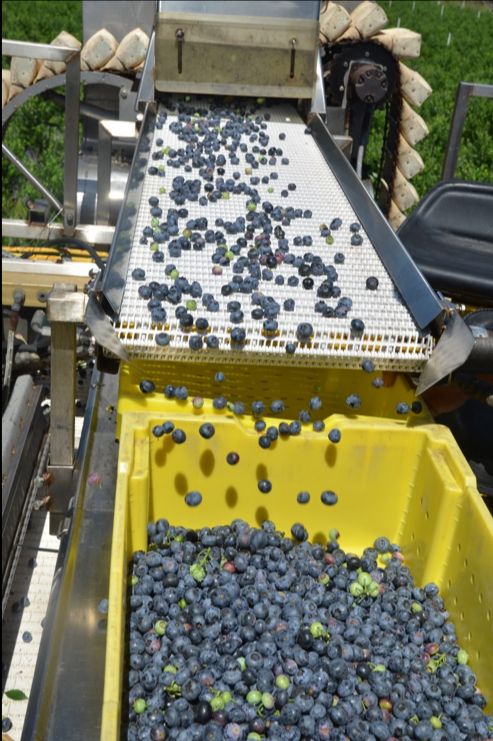
Credit: Jeff Williamson, UF/IFAS
Blueberry Cultivars
One of the most important aspects of machine harvesting is selecting the best cultivars for that system. The UF/IFAS blueberry breeding program determines the best crosses to obtain favorable machine harvesting traits (while maintaining existing desirable traits) and selects the best individuals for advancement and release. Favorable fruit and plant traits for machine harvesting include:
- firm fruit to minimize bruising and related shortened shelf life,
- a narrow crown and open top canopy to accommodate over-the-row harvesters and minimize ground losses,
- lower detachment force required for ripe berries than for green fruit,
- loose fruit clusters,
- a small stem scar to reduce the chance of postharvest disease, and
- a concentrated ripening period and the ability for fruit to remain on the plant without loss of quality, to facilitate fewer machine picks while still harvesting most of the fruit.
Some of these traits have been targets of blueberry breeding programs for many years, including firm fruit, a small picking scar, and a concentrated ripening period. Fruit firmness appears to be the most important characteristic for machine harvesting. In some cases, certain practices have been used to machine harvest less-than-ideal cultivars with firm fruit, such as hand harvesting early in the season to loosen tight fruit clusters or allowing fruit maturity to advance so that the machine does not dislodge large amounts of unripe fruit.
Cultivars previously released from the UF/IFAS blueberry breeding program that have good machine harvesting potential include ‘Colossus’, ‘Farthing’, ‘Keecrisp’, ‘Meadowlark’, ‘Optimus’, and ‘Sentinel’. However, Florida growers have also machine harvested other UF cultivars.
Farm Preparation
Proper bed structure and configuration is important for optimizing machine harvesting. Raised beds bring the catch plates closer to the base of the plant crown. Bed height may vary depending on the equipment used for harvesting. Wide beds should taper off at the edges (shoulders) so that they do not restrict proper adjustment of the catch plates, and beds should be no wider than the lower entrance of the harvesting equipment. Properly shaped beds will allow catch plates to contact the blueberry plant lower on the crown which will minimize dropped fruit, facilitate narrow-crown training, and minimize damage to canes from catch plates during harvest. The composition of the bed is also a consideration. Beds made of native soil with pine bark incorporated (as opposed to beds made solely of pine bark) may do a better job of keeping plants from being loosened in the bed or uprooted when they are shaken by the harvester. This will depend somewhat on the heaviness/clay content of the soil.
Row spacing should be determined based on the equipment that will be used. Most harvesting machines will require a minimum of 9 to 10 ft between row middles. A minimum of 30 ft clearance at the end of rows is generally needed for equipment turn around. However, the exact amount of clearance needed will vary depending on the equipment used. Periodic row breaks (about every 400 ft) may be helpful for unloading fruit from harvesters and transporting it to the packinghouse. In-row plant spacing will depend on the cultivar and plant training system, but in general, a minimum in-row spacing of 3 ft is suggested, which may be a slightly wider spacing than for fields designed solely for hand harvesting. Some growers have commented that it may be better to begin machine harvesting younger plants only after plant canopies touch each other enough to provide support, thus minimizing the possibility that harvesting equipment will uproot younger plants.
Training Plants for Machine Harvesting
After the field has been prepared to facilitate machine harvesting and the right blueberry cultivars have been planted, the plants need to be trained and pruned to accommodate the harvesting equipment. As discussed above, the ideal blueberry cultivar will have a narrow crown to minimize ground loss of harvested fruit (Figure 5). This was historically accomplished by placing cardboard juice or milk cartons with bamboo stakes over the plants for the first two years of establishment (Figure 6). Growers have recently begun to use plastic sleeves and fiberglass stakes (Figure 7), which are more costly. However, the stakes can be reused, and in some cases the plastic sleeves may remain in good enough condition to be reused. In addition to training the plants to have more narrow crowns, the cartons or sleeves can also help protect the young plants from herbicide damage.
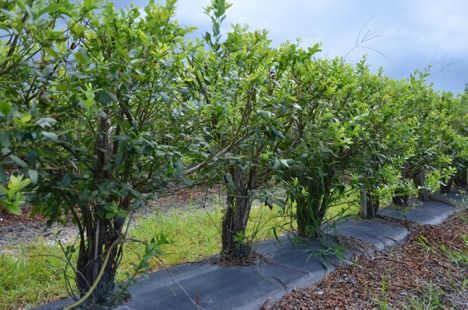
Credit: Jeff Williamson, UF/IFAS
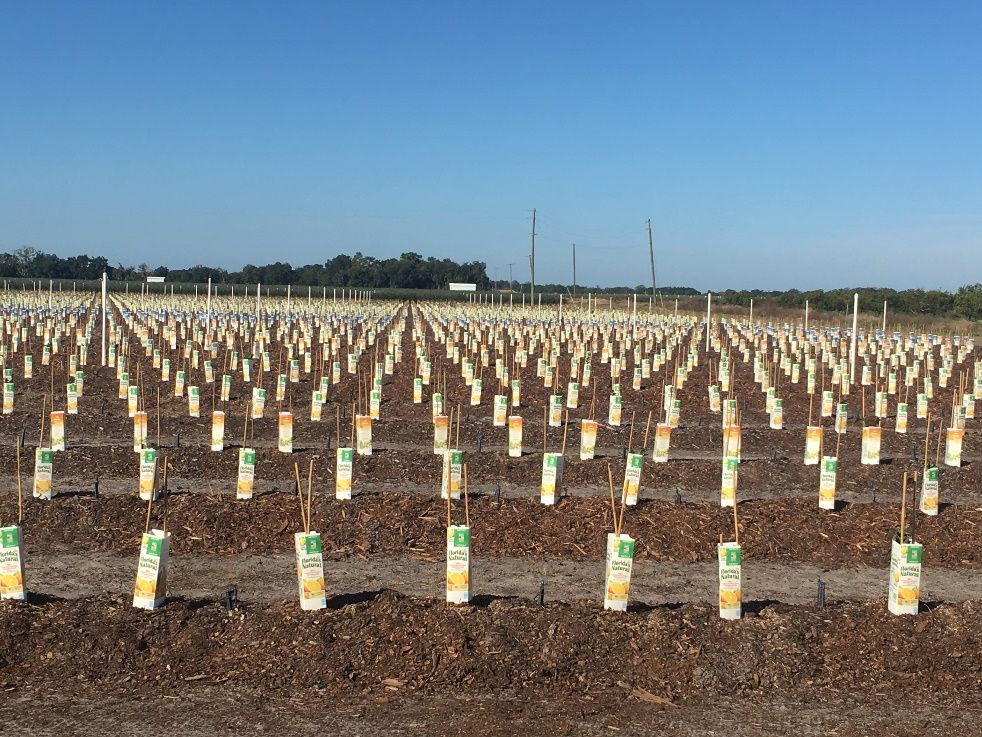
Credit: Doug Phillips, UF/IFAS
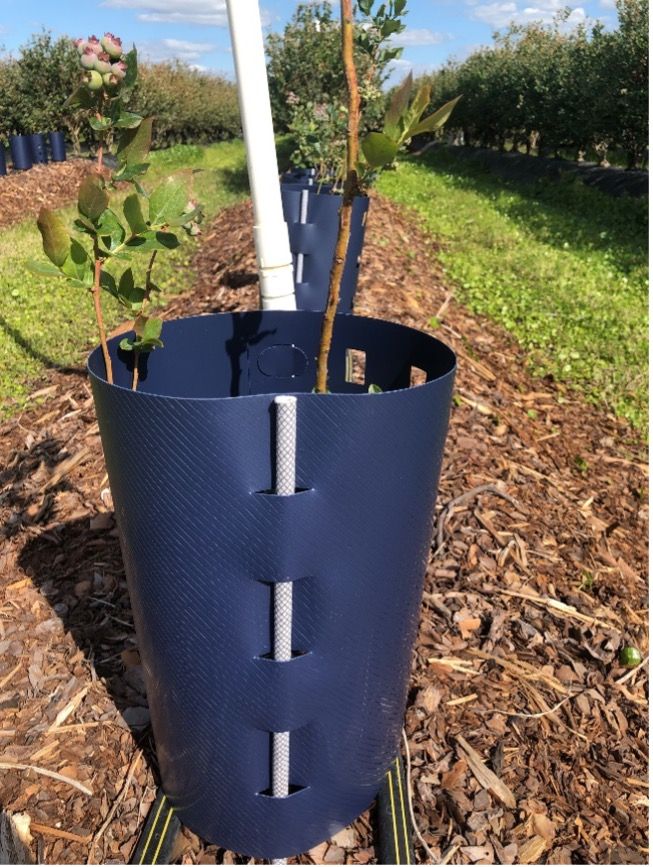
Credit: Doug Phillips, UF/IFAS
In later years, plants may need to be base pruned, removing branches in the lower portion of the plant canopy that could restrict the closure of harvester catch plates. The labor involved in this can be costly. Also, cultivars that are tall or leggy may need to be tipped a few weeks after postharvest hedging so that fruit bearing canes are not taller than the interior compartment of the harvester where rods dislodge the fruit.
Summary
Harvest and postharvest technological innovations have been developed in recent years that may improve the effectiveness of machine harvesting. These include a cushioning on catch plates to minimize fruit damage; packing line color and soft berry sorters to remove under-ripe, damaged, and overripe fruit; and forced air cooling that immediately follows harvest to dry and stabilize fruit. The combination of work by the UF/IFAS blueberry breeding program in developing new cultivars that can be successfully machine harvested, technological innovations in harvesting and packing equipment, and identification of effective cultural practices will facilitate more effective use of machine harvesting of southern highbush blueberry. This will result in significant cost savings potential, helping to maintain the competitiveness and profitability of Florida blueberry growers.
Further Reading
Gallardo, R. K., E. T. Stafne, L. W. DeVetter, Q. Zhang, C. Li, F. Takeda, J. Williamson, W. Q. Yang, W. O. Cline, R. Beaudry, and R. Allen. 2018. “Blueberry Producers’ Attitudes toward Harvest Mechanization for Fresh Market.” HortTechnology 28 (1): 10–16. https://doi.org/10.21273/HORTTECH03872-17
Sargent, S. A., F. Takeda, J. G. Williamson, and A. D. Berry. 2021. “Harvest of Southern Highbush Blueberry with a Modified, Over-the-Row Mechanical Harvester: Use of Soft-Catch Surfaces to Minimize Impact Bruising.” Agronomy 11 (7): 1412–1424. https://doi.org/10.3390/agronomy11071412
DeVetter, L. W., W. Q. Yang, F. Takeda, and J. Chen, 2022. “Harvesting Blueberries: A Guide to Machine Pick Blueberries for Fresh Market.” FS368E. Pullman, Washington: Washington State University Extension. https://s3.wp.wsu.edu/uploads/sites/2181/2022/02/FS368E.pdf