Worldwide, commercial greenhouse vegetable producers currently use numerous production systems. Among the more prevalent include lay-flat bag or upright container culture, trough culture, rockwool, vertical culture, nutrient film technique (NFT), and ground (in-soil) culture. Many modifications of these basic production systems are presently in use, and most are appropriate for Florida, except for unamended ground culture.
There are also several minor production systems, including floating systems and aeroponics. Floating systems use a sheet of polystyrene to hold small plastic mesh pots and plants that float on a pool of nutrient solution (https://edis.ifas.ufl.edu/hs184). Aeroponics is a relatively new production system that involves growing plants in a trough or container in which the roots are suspended and sprayed with a nutrient mist.
All greenhouse production systems require the use of similar environmental controls, shade structures, support wires, and general production practices. The major differences are in the irrigation and nutrient delivery methods and controls.
Individual production systems are not necessarily crop specific. All of the major greenhouse vegetable crops can be grown successfully in most systems. No single system is superior to the others. The cost of each system is comparable, and the production from all systems is high when managed properly. A research study conducted at the UF/IFAS Suwannee Valley Agricultural Extension Center showed that there was no significant difference in tomato yield among rockwool, bag, and hydroponic NFT systems (Fig.1). However, the study found that all of these systems produced higher yields than ground culture.
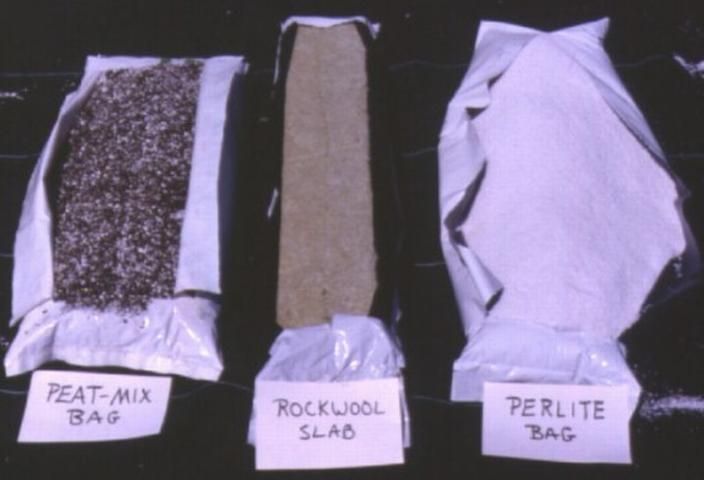
Credit: Bob Hochmuth, UF/IFAS
Lay-Flat Bag and Nursery Container Culture
Bag culture is a production system where greenhouse vegetables are grown in a soilless mix contained in a polyethylene bag. The bag can be sealed around the mix, or it can be an open bag. The closed bags are laid flat on the greenhouse floor with plants growing from planting holes cut along the upper surface of the bag after it is laid flat in place. These are called "lay-flat" bags. The nursery container or "upright" bag system involves growing a single plant in a bag or pot filled with a media mix. In either system, about 1/3–1/2 cubic foot of media mix should be made available for each plant.
Lay-flat bags contain the media, usually peat-based mixes, perlite, coconut coir, or rockwool, in a totally closed bag. Growers can make their own bags, but most often these bags are purchased prepared. Bags are made of 4 mil ultraviolet light-stabilized polyethylene. New bags with media range in cost from $2–$5 each, depending on media, size, and quantity purchased.
Bags are typically laid out in double rows in the greenhouse, and then the drip irrigation lines are installed. Depending on bag size and mix volume, two to three tomato plants can be accommodated in each lay-flat bag. Plants are produced in peat/vermiculite mix or rockwool cubes and transplanted into the bags. An alternative is to grow transplants in "bottomless" or mesh-bottom pots filled with media, which are set into the bags.
Drainage slits are needed in the bottom edge of the bags so that excess solution can be removed. This is one problem with bag culture because methods are needed to collect excess fertilizer solution so that it does not leach into the soil under or around the greenhouse. Other production principles are described under specific crops elsewhere in this handbook.
The use of upright containers, such as upright bags or nursery pots, has become increasingly popular. Media for the containers can be peat/vermiculite, composted sawdust, rockwool, rice hulls, composted pine bark, coconut coir, peanut hulls, or various mixtures of the aforementioned media. Recently, composted pine bark and coconut coir have become popular media choices in Florida because they are readily available and economical options. Bags and nursery pots can be purchased at greenhouse supply houses (most household garbage bags are not strong enough and quickly degrade). The containers are filled with the desired media and placed in single or double rows in the greenhouse, depending on the crop. Transplants are produced in a soilless mix, such as peat/vermiculite/perlite or rockwool, and transplanted into the containers, usually one plant per container.
Containers are irrigated and fertilized through a microirrigation (drip) system in which a polyethylene pipe delivers water and fertilizer down the row of bags. Each container is irrigated from an emitter and piece of spaghetti tubing. Many types of emitters are available. Growers should choose one that will wet the entire container of media. More recently, some growers have successfully adopted using drip tape placed over the top of the open containers. Choosing the appropriate emitter spacing and number of drip tapes per container are both very important decisions in the system design to ensure uniform nutrient solution distribution in the media. Information about fertilizer and water programs is available in other sections of this handbook.
Bag and container culture are easy to do, eliminate the need to sterilize new media, reduce the risk of waterborne Pythium root rots spreading in the house, and provide a "buffer" for water and fertilizer in case of power outages.
Popular Media Choices for Lay-Flat Bags
Rockwool production (Fig.2) was developed in Holland around the mid-1970s and is currently experiencing widespread use among new or expanding greenhouse vegetable operations in Europe, Canada, and, recently, the United States.
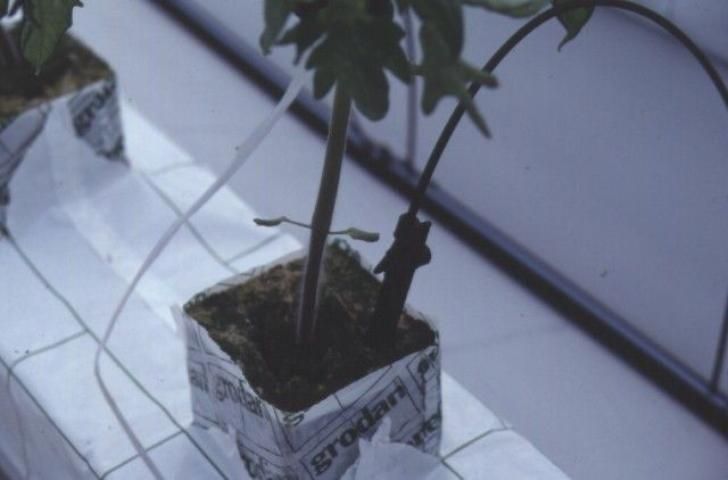
Credit: UF/IFAS
Rockwool is an inert, porous, sterile growing medium made from rocks that are heated at high temperatures and formed into thin fibers. The actual composition is approximately 60% basalt, 20% limestone, and 20% coke.
The resulting fibers can be formed into slabs or bagged as a loose rockwool for bag culture. Small cubes of rockwool are used for starting transplants. Slabs for tomatoes are commonly 3 inches thick, 6–8 inches wide, and 36 inches long. Other sizes are available depending on the crop. Slabs are packaged in white or white-on-black polyethylene sleeves. Rockwool tends to be more expensive per plant than most other soilless media.
Rockwool culture is similar to other lay-flat bag culture in greenhouse layout and operation. Slabs are laid in twin rows and are irrigated by microirrigation with one emitter per plant. Transplants are started in small rockwool cubes, then the cubes are placed in larger transplant blocks, which are approximately 3 inches square. The blocks with the transplant are then placed in the greenhouse on the slabs where the plant will eventually root into the slab media. Two or three tomato plants can be grown per 36-inch slab. It is possible to achieve average populations of two and a half plants per slab by rooting plants over the end-to-end junction of two slabs. Half of the root system is in each slab. The latter population should be sufficient for most tomato cultivars in Florida.
Perlite is a volcanic mineral that is expanded by heating at high temperatures in a furnace. The resulting light-weight granular material makes a good medium with high water-holding capacity. Lay-flat bags, about 0.5 cubic foot in volume, are filled with perlite and can hold up to three tomato plants or two cucumber plants (Fig. 3).
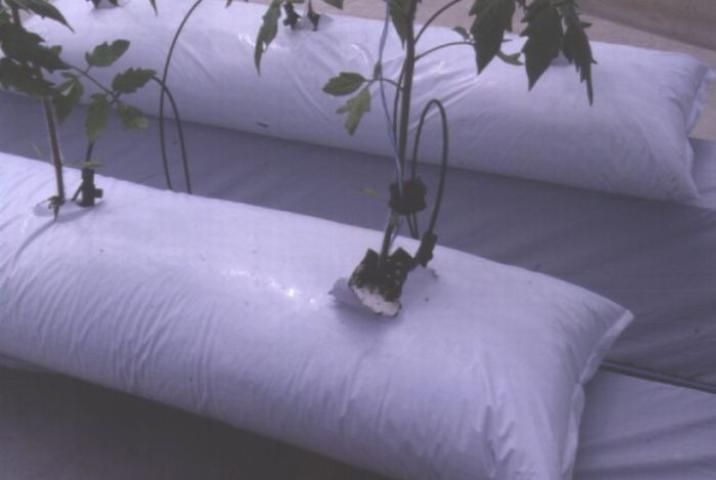
Credit: UF/IFAS
Coconut coir is a renewable by-product of the coconut palm husk industry. Long fibers from the coconut husk are used for brushes, brooms, rope, filters, padding material, and other products. The shorter fibers and the dust or pith remain and make up the product known as coconut coir, sometimes referred to as coconut fiber. Large quantities are available from areas of the world where there is a large coconut industry, such as Sri Lanka, Mexico, and the Philippines. To aid in shipping and handling, coconut coir is typically compressed, dehydrated, and formed into dense blocks or slabs. Once the grower receives the blocks or slabs, the coir is rehydrated and expands into an easy-to-use medium with high moisture-holding capacity. Thin, compressed slabs of coir are shipped inside a sealed lay-flat bag and are easily handled and stored. Once the bags are laid out on the greenhouse floor, irrigation emitters are used to add water to the coir for rehydration and expansion to fill the bag. Coconut coir can be high in soluble salts (sodium and chlorides); therefore, initial leaching with water is recommended.
Perlite and coconut coir lay-flat bags are placed in the greenhouse as described above for rockwool. Seedlings can be started in rockwool cubes or other soilless media and then properly transplanted into the perlite bags. However, if rockwool transplant cubes are planted in perlite, for instance, the cube must be inserted deeply enough to be completely buried in the perlite to prevent the rockwool cube from drying out.
Rockwool, perlite, and coconut coir lay-flat bags are placed so that they rest on a slant toward a trench between the twin rows of bags. Twin rows should be on 5-foot centers. Make slits in the bottom edge of each bag so that leachate drains into the trench and can be removed from the greenhouse. New developments are being made to improve collection of the leachate so it does not seep into the greenhouse ground floor. A trough or channel (Fig. 4) under the slabs is used to collect the leachate, which can then be used for other fertilization purposes (lawn, garden, etc.). Untreated leachate is not reused because of its potential for reintroducing disease organisms. It might be possible to treat the leachate by ultraviolet light, heat, or other methods and reuse it.
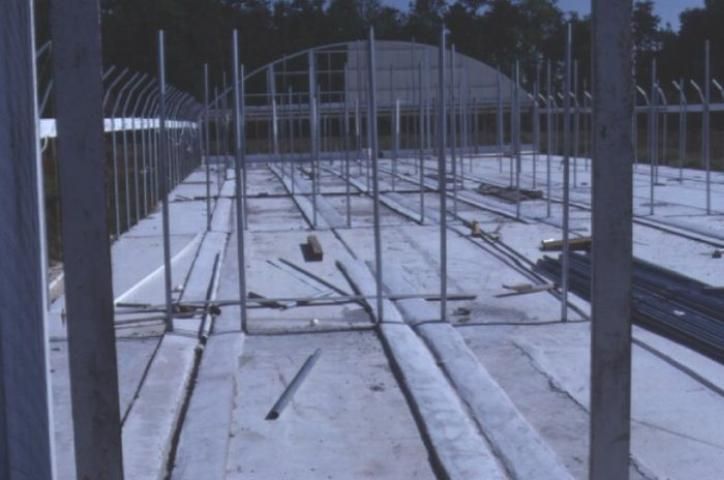
Credit: UF/IFAS
Rockwool, perlite, and coconut coir fertilization is accomplished by fertigation through the drip irrigation system. Fertilizer is applied with each irrigation event. Irrigation scheduling is controlled by a "starter tray" (Fig. 5), a timer, or other automated means. In a standard starter tray, one slab of rockwool and its plants are placed in the tray with the bottom of the polyethylene covering removed from the slab. The bare slab surface interfaces with a capillary mat in the bottom of the tray. A small reservoir collects a portion of the excess nutrient solution. A contact probe in the solution in this reservoir signals a start-up of the irrigation controller as soon as the probe breaks contact with the solution in the reservoir. Growers have used these starter trays for other media-filled bags as well with minor modifications. The controller is preset for a timed irrigation event (e.g., 2 or 3 minutes), and it opens a solenoid valve to start the flow of water and fertilizers. In most systems, water is mixed with fertilizer stock solution in a 1:100 ratio before it is applied to the slabs. Simple proportioning pumps can do this task for most greenhouse operations without the need for complicated injectors. Growers need to be sure, however, that the proportioning pumps used are accurate and resistant to fertilizers and acids.
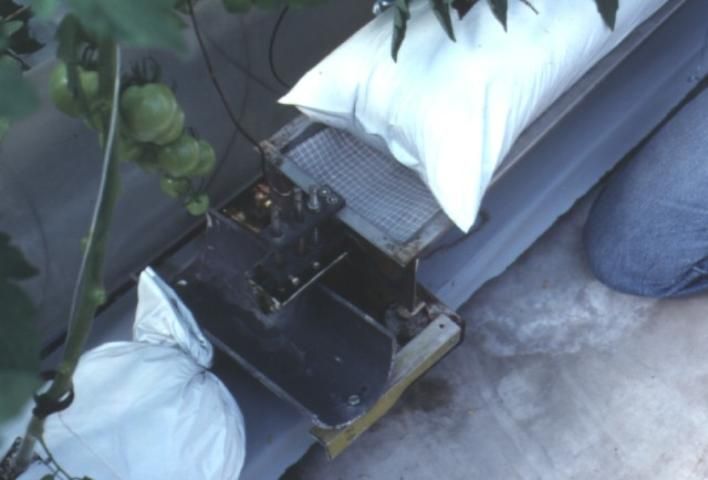
Credit: UF/IFAS
Irrigation frequencies may vary during the season depending on crop demand. Attention needs to be given to the control of soluble salt buildup in the slabs. Fertilizer programs and recipes are presented in the fertilizer section of this handbook. Samples of media solution should be tested regularly for soluble salt level. The soluble salt concentration should not vary more than plus or minus 1.0 millimhos (mmhos) of the applied solution conductivity.
Rockwool slabs and perlite can be reused for up to three seasons. In Florida, slabs should be sterilized between seasons and placed in new sleeves. Slabs that have been crushed or damaged should not be reused.
Rockwool or perlite culture has many advantages over other production systems. Among these are the ease of handling, installation, and media removal. Rockwool and perlite have high water-holding capacities and allow for more precise nutrient control. Each medium is inert, sterile, and offers predictable performance. The media have very high air pore space, which provides for higher oxygen levels and thus better root growth than with the NFT tubes. However, the most important advantage of these systems is that they are not a recirculating system, such as NFT.
Each slab or bag is "containerized," meaning nutrient solution does not flow from one slab or bag to another and back via a sump tank. This closed type of system reduces the risk of spreading a disease pathogen, such as Pythium root rot. This culture also is considerably less labor intensive compared to NFT since the irrigation and fertilization are automatically managed by the starter tray and proportioning pumps.
The major disadvantages of the lay-flat bag system are the need for a leachate collection system and the need to replace the media every one to three cropping seasons. However, these are small prices to pay for substantially reduced root rot potential and more predictable production.
Trough Culture
Alternatives to straight ground culture include growing plants in raised troughs or benches above the soil. The troughs are filled with the same types of soilless mixes as in the bag culture system. Trough culture is less common in Florida greenhouses; however, there are a few operators using media-filled troughs for tomato culture. To take advantage of economical media choices, growers are finding innovative trough culture modifications. One modification uses a trench formed in the soil, covered with nursery fabric, and filled with media such as pine bark.
In the traditional trough system, shallow wooden troughs contain the growing media. The troughs may vary from 6 to 8 inches deep and from 18 to 30 inches wide. The troughs can be plastic lined to facilitate collection of excess nutrient solution. Troughs can be constructed on a slight sideways or lengthways angle or have a V-shaped center to facilitate drainage. Some growers might incorporate a perforated pipe buried in the center of the trench to collect the drainage solution and transport it to a central collection sump. Nutrient solution is not recirculated.
Troughs are filled to the top with the chosen soilless mix and wetted. Some settling will occur and additional mix should be added. Additional mix will be needed between crops to replace that which oxidized or settled during the previous crop.
Cost to construct troughs is moderate since only lumber, polyethylene liners, and drainage pipes are needed, and the useful life might be 15–20 years. Trough culture can be used in greenhouses with concrete or natural ground floors as long as the ground is covered with nursery cloth. Troughs spaced on 5-foot centers can accommodate the same number of plants per greenhouse as any other production system.
Transplants can be produced in the containerized tray method using peat/vermiculite mix, or they can be grown in rockwool cubes. When ready, the plants are set in the troughs in twin rows to achieve the desired plant spacing for the specific crop.
In the trough culture system, irrigation and fertilization are achieved by drip irrigation. Although normally not needed, some fertilizer and lime can be mixed with the media when the troughs are filled or when the media are renewed between crops. In Florida, it is unlikely very much lime would be needed since well water often contains high levels of calcium carbonate. Fertilizer should be supplied with the irrigation water using a nutrient solution formula for the specific crop. Media pH can be as low as 5.0 without danger since there should not be high levels of toxic aluminum present in an organic soilless mix.
Use a drip system that delivers the solution directly to the media via drip tape, emitter, or ring. Growers should avoid the spray-stake types since they can wet the leaves and stems, promoting disease. When fertilizing, caution should be taken against excess buildup of soluble salts in the media. As fertilizer is applied, some salts can accumulate in the media as water is absorbed by the plants or is evaporated from the soil surface. An electrical conductivity of the solution in the media above 3.0 mmhos is indicative of excess soluble salts, and an application of water alone is needed to flush excess salts from the media.
Reusing the media in the troughs year after year comes with some risk of increasing soilborne diseases and other problems, including weeds, if the protected structure is not enclosed. Very few treatments are available to manage certain diseases and other pests. Solarizing the media in the trough between seasons in the summer may be an option in some cases. Irrigation systems, including emitter stakes, and drainage systems will need to be cleaned and disinfested between crops as well.
The major advantages of the trough system include ease of handling once the system is in place. Trough systems are flexible for various cropping decisions (e.g., vegetables, cut flowers, etc.). The system is relatively inexpensive to maintain from one crop season to another. The major disadvantage is disease control in a particular trough since an organism like Pythium could spread the length of a trough. Care also is needed to avoid soluble salt buildup in the media during the season.
Vertical Culture
During the late 1990s and since, hydroponic growers in Florida have greatly increased the use of a wide variety of vertical growing systems. These systems are used in all types of protected culture structures, including greenhouses, high tunnels, and shade structures, but are also widely used in open outdoor systems. For the purposes of this publication, we will include vertical systems with pots that stack on top of each other, bags, or other containers that are mounted in a vertical arrangement, as well as various plastic (PVC) systems that are used in aeroponic culture.
The materials, designs, expense, methods of operation, and risk are very diverse for vertical systems that are based in soilless media or aeroponics. The most widely used vertical system design uses polystyrene pots manufactured specifically for vertical systems that interlock and stack on top of each other. These pots are filled with a soilless medium such as coconut coir, perlite, composted pine bark, or coarse vermiculite. Many of these media have been used successfully alone or in mixes. The nutrient solution is delivered into the top pot and flows from the top pot through each subsequent pot through drainage holes until it has been delivered to all pots in the vertical stack. Managing solution delivery is one of the most important management challenges in vertical culture. The system has proven to be very popular among growers for leafy vegetables, fresh-cut herbs, edible flowers, and strawberries, in particular. More recently, successful production techniques for growing tomato and pepper have been developed.
The idea behind a vertical production system is that it allows a grower to increase the plant population of several crops, including leafy vegetables, in a limited space. Increases in plant population vary from crop to crop; however, most configurations allow for an increase of no more than five to eight times the normal population. Pots are held on a tower rod or pipe in the center of the pots and can often be rotated to provide more uniform exposure to sunlight. Care should be taken to plan proper spacing between towers and not make the stacks too high to avoid excessive shading of the lower pots. Vertical systems generally make labor tasks easier since much of the work can be done without bending over. If these systems are used outdoors, care must be taken to protect against freezes. These upright stacks are very susceptible to freezes since they are well above the ground and cannot easily trap the heat stored in the ground. In areas where freezes are of concern, use a temporary freeze cloth system or a protected structure.
Nutrient Film Technique
Nutrient film technique (NFT) is a type of a water culture system in which roots are continually bathed in a flowing thin film of nutrient solution. True NFT consists of growing plants in a shallow, plastic-lined trough through which a nutrient solution flows continuously or in short on and off cycles. Roots spread out over the width of the 4–12-inch flat-bottomed channels and are continually bathed in a thin film of flowing, oxygenated nutrient solution. Channels are on a slope to allow the nutrient solution to flow from one end of the channel to the other and be collected for return to the sump tank. Nutrient solution is pumped continually from the sump tank back to the channels (Fig. 6). Nutrients are added to the solution as needed, and the solution may be replaced periodically to reduce the buildup of salts and disease organisms.
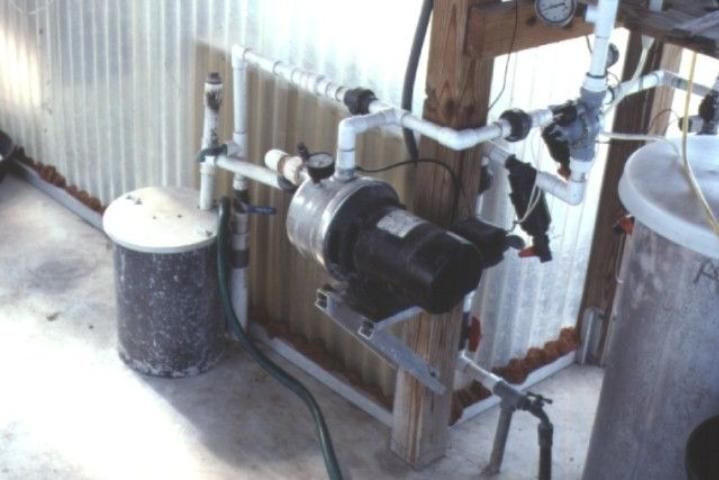
Credit: UF/IFAS
NFT is a very popular and successful way to grow lettuce, basil, and other leafy greens and herbs. However, various modifications of the basic NFT system have been tried for other crops like tomato. One popular system started for hobby greenhouses is to grow plants in a 4-inch PVC tube instead of the wide standard channel for NFT tomato production. The PVC pipe system was popular among some commercial tomato growers in north Florida in the 1980s. The PVC tube is extremely confining to the root system, making continual bathing of the root system impossible because it stops water flow and causes the root systems to flood. Therefore, the flow of nutrient solution is pulsed by a time clock. Programs and schedules for the irrigation events are presented in the irrigation section of this handbook. Even with careful attention to irrigation scheduling to minimize flooding, many growers still have problems with oxygen availability to the roots. Pythium root rot then can attack the roots. Presently, there is no effective legal chemical control for Pythium in these systems. Essentially all PVC tomato growers have since switched to bag or other soilless media culture.
In all NFT or modified NFT systems, channels and plants are arranged in the greenhouse similar to bag or rockwool culture (twin rows, plant spacing, etc.). Care needs to be given to proper channel slope and return system to the sump tank. Some systems call for a 1-inch drop for every 100 inches of channel length. This is probably not enough slope for the NFT PVC tubes. An inch rise for every 20–30 inches might be more appropriate.
NFT systems are expensive to install because of the channels, concrete greenhouse floor, return piping system, sump tank, and sump pumps. Installation might be slightly more expensive than rockwool or bag culture, but the NFT materials represent basically a one-time expense. A high degree of management and expertise is required to optimally operate the system to ensure correct irrigation and fertilization and to prevent root flooding.
Transplants for NFT are usually started in rockwool or foam cubes and placed in the channels at proper spacings. In true NFT, the plastic liner is wrapped around the stems to prevent algae growth in the channel.
Crops adaptable to NFT include tomatoes, cucumbers, and lettuce. Lettuce is particularly adapted to NFT because it is a short-term crop and less subject to damage from root rot. Different channel widths are used for lettuce and other, larger crops.
Major advantages of NFT include the one-time expense for the basic system. The major problem with the NFT systems for long-term crops is the high probability that disease organisms such as Pythium could be recirculated quickly within the greenhouse. This limitation makes NFT systems questionable for large-scale commercial production in Florida. This problem is made worse because of the lack of labeled chemical pesticides for Pythium control. It is also extremely labor intensive to manage the nutrient concentrations and pH of the solution, and there is no water-holding capacity in the event of a power failure. High nutrient solution temperatures in Florida during much of the year make NFT even more challenging in the Sunshine State.
Ground Culture
Ground culture of greenhouse vegetable crops involves growing crops directly in the natural soil under the greenhouse cover. Plants are oriented in double rows, and irrigation is handled through the use of proportioning pumps, injection pumps, or large nutrient storage tanks with sump pumps. Drip or ring emitters are placed at the base of each plant to provide water and nutrients.
Ground culture production of greenhouse vegetable crops is not recommended for Florida conditions. Although many older greenhouse vegetable operations in the United States and Canada used ground production in the 1970s and '80s, most newly constructed greenhouses use one of the more popular soilless production methods.
Insect and disease pressures in Florida would prohibit greenhouse vegetable production for more than a year without extensive and costly fumigation. Northern operations have been successful with ground culture because of the use of large boilers and steam pipes for soil sterilization. In-ground culture for certified organic growers using protected culture with permanent structures is very challenging in Florida and requires significant additions of organic amendments.
In addition, many areas of Florida have sandy soil profiles with fluctuating water tables. Excessive nutrient levels could leach into local groundwater tables or accumulate in the soil surface. The high water table could also cause periodic flooding.
Summary
As mentioned earlier, there is no single production system that is best for everyone. In comparing the most popular systems (bag, container, trough, vertical, rockwool, and NFT), one would find that the installation cost of the bag, trough or container system would be roughly comparable, but rockwool and bags will need to be replaced periodically in those systems. The initial setup cost for vertical systems and NFT will be higher. The NFT systems are fine for leafy vegetables but are highly susceptible to root rot problems for tomato and cucumber, for which there are no chemical pesticide control measures. Modified NFT tube systems that use PVC can be risky because of the potential for low oxygen availability to roots.
The total production of the major systems can be extremely high depending on the level of management. This management level is higher for the NFT and vertical systems as opposed to the lay-flat bag, trough or upright container cultures. In selecting a production system, a grower should weigh both the advantages and disadvantages as they relate to the individual's situation, crop selection, and time management concerns.
More Information
For more information about greenhouse crop production, please visit our website at http://smallfarms.ifas.ufl.edu.
For the other chapters in the Greenhouse Vegetable Production Handbook, see the documents listed below.
Volume 1: Introduction • Financial Considerations • Pre-Construction Considerations • Crop Production • Considerations for Managing Greenhouse Pests • Summary
Volume 2: Physical Greenhouse Design Considerations • Production Systems • Other Design Information Resources
Volume 3: Preface • General Aspects of Plant Growth • Production Systems • Irrigation of Greenhouse Vegetables • Fertilizer Management for Greenhouse Vegetables • Production of Greenhouse Tomatoes • Greenhouse Cucumber Production • Greenhouse Nematode Management • Alternative Greenhouse Crops • Vegetable Insect Identification and Management
Selected Readings
Bauerle, W. L. 1984. Bag Culture Production of Greenhouse Tomatoes. Special Circular 108. Columbus: Ohio State University.
Cooper, A. 1979. The ABC of NFT. London: Grower Books.
Cooper, A. 1982. Nutrient Film Technique. London: Grower Books.
Hochmuth, G. J. (ed.). 1989. Design Suggestions and Greenhouse Management for Rockwool Vegetable Greenhouses in Florida. Bulletin 327. Gainesville: University of Florida Institute of Food and Agricultural Sciences. https://edis.ifas.ufl.edu/cv195.
Johnson, H., G. Hochmuth, and D. Maynard. 1985. Soilless Culture of Greenhouse Vegetables. Circ. 218. Gainesville: University of Florida Institute of Food and Agricultural Sciences.
Jones, J. B. 1983. A Guide for the Hydroponic and Soilless Culture Grower. Portland, OR: Timber Press.
Judd, R. 1982. "Bag Culture." Amer Veg. Grower 30 (11): 42, 44.
Ministry of Agriculture, Fisheries, and Food. 1984. Tomato Production 6. Hydroponic Growing Systems. London: Grower Books.
Resh, H. M. 1978. Hydroponic Food Production. Santa Barbara, CA: Woodbridge.
Savage, A. J. (ed.) 1985. Hydroponics Worldwide: State of the Art in Soilless Crop Production. Honolulu, HI: International Center for Special Studies.
Sheldrake, R. 1981. "Money Bags." Amer. Veg. Grower 29 (11): 15, 34.
Sheldrake, R. 1982. "Back to the Bag." Amer. Veg. Grower 30 (3): 36.
Smith, D. 1987. Rockwool in Horticulture. London: Grower Books.
Taylor, G. A., and R. L. Flannery. 1975. Growing Greenhouse Tomatoes in Trough Culture Using a Peat-Vermiculite Growing Medium. Veg. Crops Offset Series No.33. New Brunswick, NJ: Rutgers University.
Winsor, G. W., R. G. Hurd, and D. Price. 1979. Nutrient film technique. Growers Bulletin No.5. Littlehampton, England: Glasshouse Crops Res. Inst.
Wittwer, S. H., and S. Honma. 1979. Greenhouse Tomatoes, Lettuce, and Cucumbers. East Lansing: Michigan State University Press.