Fertigation
The term "fertigation" refers to the application of fertilizers with the irrigation water. Most greenhouse vegetable production systems use this approach to fertilizing the crop. It is most appropriate for those production systems which rely on either hydroponics or on an inert substrate for crop culture. Adding nutrients to the crop with the irrigation water in these systems is a straightforward technique that is easily automated. When done properly, correct levels of nutrients can be supplied to the plants with a minimum of waste.
In any fertigation system, the basic components are: stock tanks for fertilizers, a water source, a method for mixing fertilizer and water in correct proportion, and a pump to move the water and fertilizer mix to the plants. The method in which these components are arranged and used differs depending on the specific cultural system used.
In all systems, it is important to be sure the fertilizer is formulated properly. The grower must mix the correct amount of fertilizer so that the plants will receive the right concentration (ppm) of the various nutrients. Most concentrates can be made up to be diluted 1:100 for ease of operation. Certain nutrients cannot be mixed in concentrated forms with other specific nutrients because insoluble precipitates may form. For example, potassium phosphate will form a precipitate (calcium phosphate) if mixed with calcium nitrate in the same stock tank. Therefore, all fertigation systems that rely on stock solutions will need to have at least two stock tanks. See sections in Volume 3 on fertilizing specific crops for details.
Another tank that is usually needed in Florida is a tank for acid. Most well water in Florida is alkaline and should be acidified before being used for fertigation since precipitates may form. Most often sulfuric, nitric, or phosphoric acids are used for this purpose. The grower can add acid to one of the stocks in concentration high enough to be effective when diluted in the final fertilizer solution, or he can inject acid from a third tank automatically into the final nutrient solution going to the plants.
Any fertilizer delivery system should be designed to facilitate cleaning after each crop. The delivery system should be easily accessed during and after cropping for repairs and for cleaning. The ends of the submains in the greenhouse should be fitted with caps or valves for flushing.
Hydroponic Systems
In a hydroponic system, the final nutrient solution is usually formulated in a large sump tank by mixing enough fertilizer solution from the stocks to achieve the desired concentrations of the various nutrients. The stock solutions can be added to the tank by hand, using some type of measuring container or they can be added automatically by stainless steel pumps calibrated to deliver the correct amount of each stock solution.
The nutrient solution in the sump should be continuously agitated mechanically or by aeration. The solution from the sump tank is circulated through the troughs or pipes in the greenhouse that contain the root systems of the crop. Specific flow rate will depend on crop and stage of growth (see section under individual crops in Volume 3). The nutrient solution then returns by gravity to the sump tank.
The piping system in the greenhouse must be sized correctly in order to deliver enough solution to the troughs or pipes during peak demand periods (Figure1).
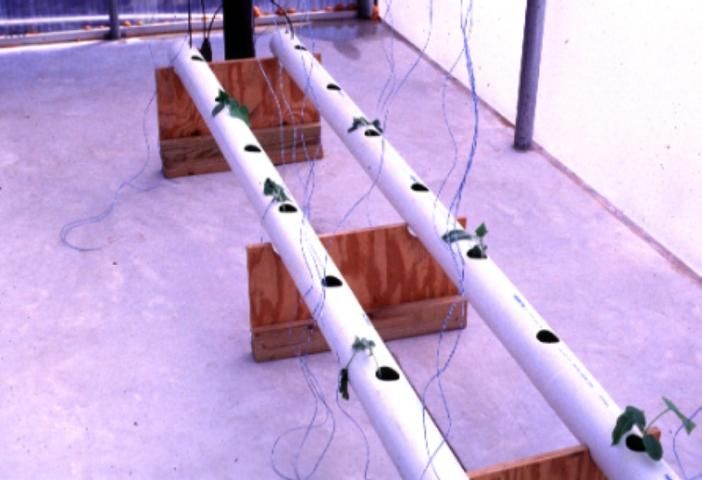
For most hydroponic systems, this will be 1 quart of solution per minute at each emitter. The piping system is usually made from PVC pipe and the emitters are usually polyethylene tubing.
For a typical greenhouse, a 1000-gallon sump is required. Sumps can be constructed of concrete or various plastic materials such as polyethylene or PVC. Highly acidified nutrient solution (pH below 5.0) might cause a slight deterioration of the inside surface of concrete sumps. It is doubtful that the concrete sumps will appreciably affect the pH of the nutrient solution.
Sumps should be located to avoid traffic, for instance in the head house area. Placing sumps below ground level can help keep the nutrient solution cool and reduces the potential for algal growth in the tank. If sumps are placed above the floor inside the greenhouse, they should be located to avoid being heated or shading the crop. The sump should have a tight fitting lid and should not be placed in a position where the lid is in the traffic pattern. Soil and dust entering the sump may carry disease organisms. The opening to the sump should have a neck raised well above the surface of the floor to prevent dust and debris or water from entering sumps from above. Failure to do this is one of the major design flaws in existing hydroponic houses in Florida.
To limit damage from nematodes as well as waterborne fungi, bacteria, and viruses, hydroponic growers should use multiple sumps rather than a centralized system. Nematodes are easily spread within a greenhouse by any means of moving contaminated water, soil, or plant material. Nematodes are aquatic animals, so are especially easily moved in water. Recirculating hydroponic systems are especially vulnerable to nematodes and certain diseases because the entire system can become uniformly infested as soon as nematodes or disease organisms in or on roots anywhere in the system begin reproducing and get into the water. This can be a particularly serious problem because labeled chemical treatments are limited or nonexistent.
Perlite, Peat Bag, or Rockwool Systems
In perlite, peat bag or rockwool culture, the plants are grown in a solid media (perlite-filled bags, compressed rockwool slabs, or loose material made of peat or fiberglass) (Figure 2).
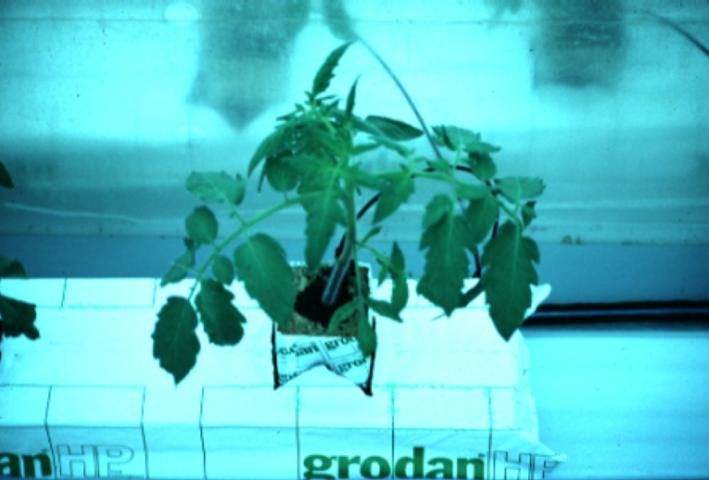
Perlite, peat bag, and rockwool systems are not "closed circuit" systems as in hydroponics. One to several plants grow in each bag or slab and many individual bags or slabs are used in each greenhouse.
Nutrient solution is usually formulated automatically from stock tanks through the use of injector pumps or fertilizer proportioners. For typical greenhouses using perlite, rockwool, or bag culture, fertilizer stock tanks can be 50 gallons in size. During an irrigation event, fertilizer is drawn out of the stock tanks and injected in the correct proportion into the water. The mixture is moved to the greenhouse and applied by individual emitters to each bag or slab. The amount of solution delivered to the plants is important. Too much can cause leaching and waste when the excess drains from the media; inadequate amounts can lead to soluble salt buildup in the media when plants remove water faster than nutrients.
The distribution system consists of polyethylene tubing that runs the length of the house along the rows of plants and supplies the nutrient solution to "spaghetti" tube lines connected to an emitter placed in each bag or slab. Various emitters can be used to deliver the solution to the bags or slabs. Usually the flow rate needs to be from 1 to 4 quarts per hour.
In traditional perlite, peat bag, or rockwool culture systems, excess nutrient solution drains from the bags through slits and into the ground beneath the greenhouse. Although the amount of leachate is usually small, it can present problems over time. This approach to disposal of leachate will probably not be tolerated as it could contribute to potential groundwater contamination. Growers using these production systems are encouraged to install a catchment system so that the excess solution can be recovered.
The catchment systems consist of a simple series of troughs or channels into which the bags or slabs drain. The leachate is recovered in a tank and used for other fertilization needs such as pasture, nursery, lawn, garden, etc. It is not suggested to reuse the leachate in the greenhouse since it could contain pathogens such as the Pythium root rot organism. Re-use might be possible if the leachate is treated to destroy the pathogens. Options for treatment include UV sterilization, filtration, or heat. Work in Europe showed that heat (170°F) would be best.
At least two systems are appropriate for recovering the leachate. One system would be to place the bags or slabs on slanted concrete floors that angle into a center trough between each set of twin rows. Leachate drains into the trough and is directed by inter-connecting channels to a large catchment tank or reservoir. This approach means that some up-front design features need to be considered when the grower is planning a bag or rockwool house.
The other approach would be to place the growing slabs or bags on slanted benches so that the leachate is collected under the slabs or bags into the collecting system and eventually to the holding tank. This approach is appropriate for growers with existing level concrete floors that desire to switch to perlite, peat bag, or rockwool culture. More information on house design is presented in Circular SP110 of the Fla. Coop. Ext. Serv. "Design Suggestions and Greenhouse Management for Vegetable Production in Perlite and Rockwool Media in Florida."
Native Soil Systems
Vegetable production in the native greenhouse floor soil in Florida is not recommended due to potential for disease organism and nematode buildup. Production in the native soil requires sterilization of the soil between crops. This is a large undertaking since an extremely large volume of soil must be sterilized in-place. Re-infestation of the sterile soil is very likely and the long nature of most greenhouse crops makes this possibility more of a reality.
Automatic Controls
For optimum performance of any fertigation system, a certain level of automation should be attempted. Automation can help provide more uniform levels of water and nutrients to the crop. Fluctuations of water and nutrients usually leads to production problems with yield and fruit quality.
The level of automation required by most producers in Florida is reasonably inexpensive. Irrigation in hydroponic systems relies on automated pumping of the nutrient solution to the plants. The pumping cycles are controlled by a simple time clock that can provide timing sequences in minutes, for example, 5 minutes on, 10 minutes off for each 15 period in each hour. The clock should be flexible enough to change the on/off cycles to meet various scheduling demands during the crop cycle. Bag and rockwool culture can be set up on a time clock as well. The media in both of these systems retains a certain amount of nutrient solution that can be drawn upon by the plant between irrigation events. If irrigations were operated solely by a time clock, on certain days the plants would be overwatered. This would happen on cool, cloudy days if the time clock were set to take care of irrigation in the peak demand situations (sunny days). For details, see Volume 3.
To avoid this type of problem, the automated watering in rockwool systems uses a "starting tray" irrigation sensor (Figure 3).
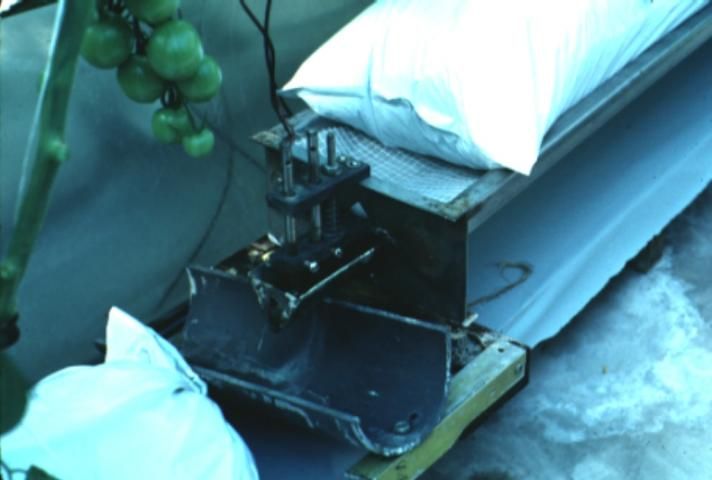
The tray contains one slab that drains into a small trough at the end of the tray. A sensing probe sends a signal to a relay box when the contact between the probe tip and the water in the trough is broken. The relay box signals the irrigation controller (time clock) to open a solenoid and start the irrigation cycle. The length of the irrigation event is preset to deliver the correct amount of water to the slabs. The preset irrigation time interval differs with crop stage and season. Research in Florida shows that this starting tray system can be used for perlite bag culture as well.
In large operations, sensors can be monitored by a greenhouse management computer, the same one that monitors the environmental seasons. The advantage here is the capability to record and store data on fertilizer and water use by the various crops in the operation.
In the future, monitoring systems will be available that measure levels of individual elements in the fertilizer solution as well as pH, temperature, oxygen content, etc. In these systems, the computer will keep track of each nutrient by a specific sensing system (electrodes, ion exchange, etc.) and will control the addition of individual elements to replace those removed by the plant.
More Information
For more information on greenhouse crop production, please visit our website at http://smallfarms.ifas.ufl.edu.
For the other chapters in the Greenhouse Vegetable Production Handbook, see the documents listed below:
Volume 1: Introduction • Financial Considerations • Pre-Construction Considerations • Crop Production • Considerations for Managing Greenhouse Pests • Summary
Volume 2: Physical Greenhouse Design Considerations • Production Systems • Other Design Information Resources
Volume 3: Preface • General Aspects of Plant Growth • Production Systems • Irrigation of Greenhouse Vegetables • Fertilizer Management for Greenhouse Vegetables • Production of Greenhouse Tomatoes • Greenhouse Cucumber Production • Greenhouse Nematode Management • Alternative Greenhouse Crops • Vegetable Insect Identification and Management