Fertilizer Management for Greenhouse Vegetables—Florida Greenhouse Vegetable Production Handbook, Vol 3
Plants require 17 elements for normal growth and reproduction. The objective of a sound fertilizer management program is to supply these required nutrients in ample, but not excessive amounts for optimum crop production. This chapter will present general information on plant nutrition that will be useful irrespective of the particular cultural system e.g., perlite, rockwool, coconut coir, peatmix, or NFT hydroponics used by a grower. Fertilizer programs will be detailed later in the chapter.
General Plant Nutrition
The 17 elements required by all plants are carbon (C), hydrogen (H), oxygen (O), phosphorus (P), potassium (K), nitrogen (N), sulfur (S), calcium (Ca), magnesium (Mg), iron (Fe), boron (B), manganese (Mn), copper (Cu), zinc (Zn), molybdenum (Mo), and chlorine (Cl). Nickel (Ni) was recently (2004) determined to be an essential nutrient for plants.
The elements C, H, and O are supplied largely from air (carbon dioxide (CO2) and oxygen), and water (H2O). The remaining 14 elements, usually referred to as mineral nutrients, are supplied from several sources. Small amounts of these nutrients can be derived from the growing media e.g., peat in a bag or trough culture or from the water in hydroponics. Well water in Florida contains substantial amounts of Ca and S, and smaller amounts of Mg, and Fe. Most of the needed amounts of the 14 mineral elements, however, are supplied by the grower from fertilizers.
The nutrients N, P, K, S, Ca, and Mg are referred to as the macronutrients because they are required in larger quantities by the plant compared to the remaining elements. The other eight elements are referred to as micronutrients because they are required in small amounts, usually a few parts per million (ppm) in the fertilizer solution.
Roles of Elements in Plant Growth
Carbon is "fixed" from CO2 from the atmosphere by photosynthesizing plants. Carbon is a component of all organic compounds such as sugars, proteins, and organic acids. These compounds are used in structural components, enzymatic reactions, and genetic material, among others. The process of respiration degrades organic compounds to provide energy for various plant processes.
The normal level of CO2 in the atmosphere is about 400 ppm. Research on many crops has shown that if the ambient level of CO2 is increased to 800 to 1000 ppm, imporoved plant growth and yield will result. Injection of CO2 is a standard practice in winter greenhouse vegetable production in northern climates. In these climates, high CO2 levels can be maintained because the greenhouses are closed during the winter. In Florida, CO2 injection is not as efficient as in northern climates because of the large amount of ventilation required, even in winter.
If CO2 injection is practiced, the grower should only apply CO2 when the ventilation system is off, furthermore, CO2 should only be injected during daylight because this is when the CO2 can be used by the plant.
Levels of CO2 can be increased by burning natural gas or liquid propane in special CO2 burners, or it can be introduced into the house as CO2 gas. Burners need some means to distribute the CO2 in the house. This is usually accomplished by blowers or circulation fans. The CO2 gas is injected through tubing, usually polyethylene, with emitters spaced along the tubing.
Injection of CO2 will be most effective if the injection is done within the plant canopy where CO2 can readily enter the plant leaves. Growers using CO2 injection should invest in a CO2 monitoring unit so that levels of CO2 do not rise to wasteful levels. Monitoring and control of CO2 injection can be computerized and automated.
Hydrogen also is a component of the organic compounds where we find C. Hydrogen ions are involved in electrochemical reactions to maintain charge balances across cell membranes.
Oxygen is the third element in typical organic molecules such as simple sugars. The presence of O is important for many plant biochemical reactions and to promote healthy root systems for nutrient uptake.
Phosphorus is used in several energy transfer compounds in the plants. A very important function for P is its role in nucleic acids, the building blocks for the genetic code material in plant cells.
Potassium is used as an activator in many enzymatic reactions in the plant. Another role for K in plants occurs in special leaf cells called guardcells found around the stomata. Guard cell turgor (or lack of turgor) controls the degree of opening of the stomata and thus controls the level of gas and water vapor exchange through the stomata. Turgor is largely controlled by K movement in and out of the guard cells.
Nitrogen is a very important element for plant growth and is found in many compounds. These include chlorophyll (the green pigment in plants), amino acids, proteins, nucleic acids, and organic acids.
Sulfur is a component of sulfur-containing amino acids such as methionine. Sulfur also is contained in the sulfhydryl group of certain enzymes.
Calcium is required for calcium pectate for cell wall development. In addition, Ca is used as a cofactor of certain enzymatic reactions. Recently, it has been determined that Ca is involved in the intimate regulation of cell processes mediated by a molecule called calmodulin.
Magnesium plays an important role in plant cells since it appears in the center of the chlorophyll molecule. Certain enzymatic reactions require Mg as a cofactor.
Iron is used in the biochemical reactions that form chlorophyll and is a part of one of the enzymes that is responsible for the reduction of nitrate nitrogen to ammoniacal nitrogen. Other enzyme systems such as catalase and peroxidase also require Fe.
Boron functions in the plant are not well understood. Boron seems to be important for normal meristem development in young parts such as root tips though its role in protein synthesis, development of cell walls, pollen tube growth, and seed production.
Manganese functions in several enzymatic reactions that involve the energy compound adenosine triphosphate (ATP). Manganese also activates several enzymes and is involved with the processes in the electron transport system in photosynthesis.
Copper is a component of several enzymes in plants and is a part of a protein in the electron transport system in photosynthesis.
Zinc is involved in the activation of several enzymes in the plant and is required for the synthesis of indoleacetic acid, a growth regulator.
Molybdenum is a constituent of two enzymes involved in nitrogen metabolism. The most important of these is nitrate reductase.
Chlorine plays a possible role in photosynthesis and might function as a counter ion in K fluxes involved in cell turgor.
Nickel plays a role in plant nutrition as a constituent in several key enzymes important in nitrogen metabolism (urease enzyme) and biological N fixation in legumes. Ni is commonly found in soils and can be added to fertilizers.
Nutrient Deficiencies
Phosphorus is absorbed by the root as H2PO4-1 or HPO4-2 by an active, energy-requiring process. P is very mobile in the plant. Deficiencies therefore show up on the older leaves of the plant because P is translocated out of these leaves to satisfy immediate needs in the new growth. P deficiency shows up as stunting and a reddish coloration resulting from enhanced levels of anthocyanin pigments.
Deficient leaves will have only about 0.1% P by dry matter. Normal most-recently-matured leaves of most vegetables will contain 0.25 to 0.6% P on a dry weight basis. Excess P in the root zone can result in reduced plant growth probably as a result of P retarding the uptake of Zn, Fe, and Cu.
P uptake can be reduced by high pH in the root media or by cold media temperatures. It is important to try to maintain hydroponic solution pH at 5.6 to 6.0 to favor P uptake. Acidification can be accomplished by use of several acids such as sulfuric, nitric, or phosphoric. It is important not to overlime peat media in trough culture. Maintain pH at 5.5 to 6.5. Check the temperature of hydroponic solutions and of peat bags or other solid media. Media temperatures should not fall below 60F for extended periods, especially during seedling or young plant development. Cool media will reduce P uptake by plant roots.
Sometimes petioles and plant leaf midribs on young leaves of full-grown plants show minor purpling. This often occurs in late fall when temperatures are reduced. This is probably not related to P deficiency since it occurs on young leaves. It is probably more related to increased levels of anthocyanin pigment expressed in the leaves under cool temperatures. This will not cause problems and will disappear under warmer conditions.
Potassium is absorbed in large quantities by an active uptake process. Once in the plant, K is very mobile and is transported to young tissues rapidly.
Deficiency symptoms for K show up first on lower leaves as a marginal flecking or mottling. Prolonged deficiency results in necrosis along the leaf margins and the plants can become slightly wilted. Deficient plant leaves usually contain less than 1.5% K. Deficiencies of K lead to blotchy ripening of tomatoes where the fruits fail to produce normal red color in areas on the fruit. Excess levels of K in the media, especially hydroponics and rockwool, could inhibit the uptake of other cations such as Mg or Ca.
Nitrogen can be absorbed by the plant in either the nitrate (NO3) or ammonium (NH4+) forms. The NO3 form is usually the preferred form in which to supply most N to greenhouse crops. The NH4 form seems to be absorbed easier than NO3 at cool temperatures (less than 55F). Uptake of NH4 is best at a media pH near neutrality with uptake reduced as pH is dropped. Uptake of NO3 is best at more acidic pH levels. Highest N uptake by plants usually occurs when both forms of N are present in the media. Presence of NH4 in the media along with NO3 resulted in greatest growth rates in some tests.
The form in which N is absorbed has an effect on the media pH. As NH4 is absorbed, the plant releases H+ ions to maintain electrical balance, and therefore, the pH drops. As NO3 is absorbed, the pH increases due to the presence of increased amounts of OH-ions. Uptake of N, therefore, can explain some of the fluctuations sometimes seen in the pH of the growth media. Nitrogen is a very mobile element in the plant and deficiency symptoms therefore show up first on the lower leaves. Symptoms consist of a general yellowing (chlorosis) of the leaves. On tomatoes, there might be some red coloration to the petioles and leaf veins. If the problem persists, leaves will drop from the plant.
Normal plant leaves contain between 2.0% and 5.0% N on a dry weight basis. Deficiencies of N show up most often where errors are made in fertilizer management that result in insufficient N supply to the crops. More often, there is a problem from excess N application. Plants receiving excess N usually are lush and tender with larger and darker-green leaves. Excess N (especially under warm and sunny conditions) can lead to "bullish" tomato plants. These plants produce thick, leathery leaves that curl under in dramatic fashion producing compact growth.
Sulfur is absorbed mainly in the form of sulfate (SO4). Sulfur is not very mobile in the plant so deficiency generally begins in the younger growth. Deficiency symptoms consist of a general yellowing of the leaves. Deficiencies of N and S appear similar, but N deficiency occurs on the lower leaves; S deficiency occurs on the upper leaves.
Plant leaves usually contain between 0.2% and 0.5% S on a dry weight basis. This range is like that for P. Plants can generally tolerate quite high levels of S in the growing media and this is one reason for the wide use of sulfur-containing materials to supply the nutrients such as Mg and the micronutrients. For this reason, S deficiency is not very common in greenhouse vegetable crops.
Calcium, unlike most elements, is absorbed and transported by a passive mechanism. The transpiration process of the plants is a large factor in the uptake and transport of Ca. Once in the plant, calcium moves toward areas of high transpiration rate such as the rapidly expanding leaves.
Most of the uptake of Ca occurs in a region of the root just behind the root tip. This has practical importance for greenhouse vegetable culture because it means that growers must keep healthy root systems with plenty of actively growing root tips. Root diseases will severely limit calcium uptake by the plant.
Calcium is immobile in the plant; therefore, deficiency symptoms show up first on new growth (Figure 1). Deficiencies of Ca cause necrosis of the new leaves or lead to curled, contorted growth. Examples of this are tip burn of lettuce and cole crops. Blossom-end-rot of tomato also is a calcium-deficiency related disorder (Figure 2). Cells of the tomato fruit deprived of Ca break down causing the well-recognized dark area on the tomato fruit blossom-end. Sometimes this breakdown can occur just inside the skin so that small darkened hard spots form on the inside of the tomato while the outside appears normal. Sometimes the lesion on the outside of the fruit can be sunken or simply consist of darkening of the tissue around the blossom area.
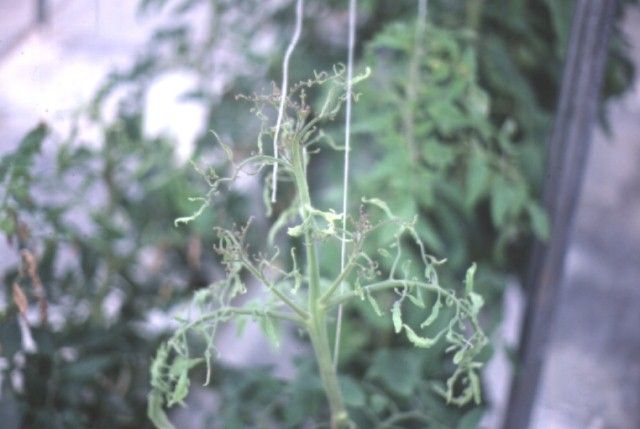
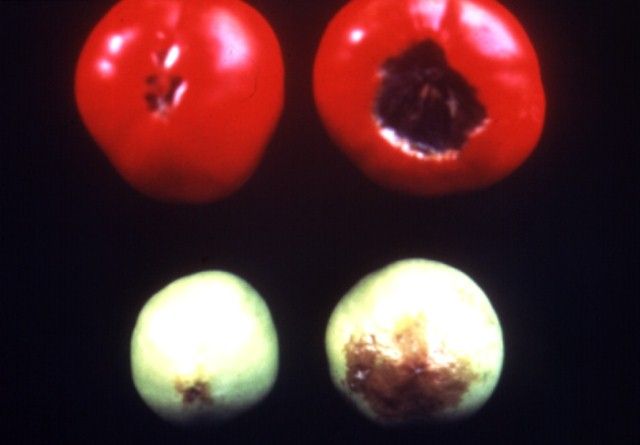
Since Ca movement in the plant is related to transpiration, it follows that environmental conditions that affect transpiration also affect Ca movement. Periods of high humidity can lead to tip burn of lettuce because the leaves are not transpiring rapidly enough to move adequate Ca to the expanding leaf extremities.
Calcium concentrations in normal, most-recently matured leaves will be from 1.0% to 5.0%. Deficiencies, however, can occur temporarily under certain environmental conditions as discussed above. Therefore, it is important to consider irrigation and greenhouse environment control in the overall Ca fertilization program. In addition, uptake of Ca can be affected by other ions such as NH4, Mg, and K. These cations can compete with Ca for uptake by the root. These competing nutrients should not be supplied in excess of what is needed by the plant.
Magnesium is absorbed by the plant in lower quantities than Ca. The absorption of Mg is also highly affected by competing ions such as K, Ca, or NH4. Unlike Ca, Mg is mobile in the plant and deficiencies appear first on the lower leaves.
Deficiency of Mg consists of an interveinal chlorosis which can lead to necrosis of the affected areas. On tomato leaves, advanced Mg deficiency leads to a mild purpling of the affected areas on the leaf.
Mg is usually found in concentrations of 0.2% to 0.8% in normal leaves. Conditions that lead to deficiency include poorly designed fertilizer programs that supply too little Mg or ones that supply excess K, Ca, or NH4.
Iron can be absorbed by an active process as Fe2+ or from iron chelates which are organic molecules containing iron sequestered within the molecule. Uptake of iron is highly dependent on the iron form and adequate uptake depends on the ability of the root to reduce Fe3+ to Fe2+ for uptake. Iron chelates are soluble and aid in keeping Fe in solution for uptake. The uptake of the whole chelate molecule is low and usually Fe is removed from the chelate prior to uptake.
Iron is not mobile in plants and symptoms appear on the new leaves first. Symptoms consist of interveinal chlorosis that may progress to a bleaching and necrosis of the affected leaves. Normal leaves contain 80 ppm to 120 ppm Fe on a dry-weight basis.
Conditions that lead to Fe deficiency are inadequate concentrations of Fe in the nutrient solution, cold media, or alkaline media conditions (pH above 7.0). Fe deficiency is corrected by adding Fe to the fertilizer solution or by foliar sprays of Fe. Usually, one or two sprays of a 25 ppm Fe solution (chelated iron product) will correct a temporary Fe deficiency.
Manganese is absorbed as Mn2+ ions and the uptake is affected by other cations such as Ca and Mg. Manganese is relatively immobile in the plant and symptoms of deficiency show up on the upper leaves.
Deficiency of Mn resembles that of Mg, however, Mg appears on the lower leaves of the plant. Mn deficiency consists of interveinal chlorosis; however the chlorosis is more speckled in appearance compared to magnesium deficiency. Normal concentrations of Mn in leaves ranges from 30 ppm to 125 ppm for most plants. High concentrations of Mn can be toxic to plants. Toxicity consists of marginal leaf necrosis in many plants. Concentrations of Mn on the order of 800 ppm to 1000 ppm can lead to toxicity in many crops. Excess Mn in the nutrient solution reduces uptake of Fe.
Situations that lead to deficiency are mostly related to inadequate Mn supply in the solution or to competition effects of other ions. Toxicity can occur from excess Mn supply or from an acidic media that contains some soil-based material that carries Mn. Solubility of Mn is increased in these soil-based media by low pH.
Zinc uptake is thought to be by an active process and can be affected by the concentration of P in the media. Zn is not highly mobile in plants. Deficiency of Zn results in leaves with interveinal chlorosis. Sometimes Zn deficiency will lead to plants with shortened internodes.
Normal leaves contain about 25 ppm to 50 ppm Zn. High concentrations of Zn can lead to toxicity where root growth is reduced, and leaves are small and chlorotic. Zinc deficiency can be increased by cold, wet growing media or by media with a very high pH or with excessive P.
Copper is absorbed by plants in very small quantities. The uptake process appears to be an active process and it is strongly affected by Zn and pH. Copper (Cu) is not highly mobile in plants, but some Cu can be translocated from older to newer leaves. The normal level of Cu in plants is on the order of 5 to 20 ppm.
Copper deficiency of young leaves leads to chlorosis and some elongation of the leaves. Excess copper, especially in acidic media, can be toxic.
Molybdenum is absorbed as molybdate MoO42- and the uptake can be suppressed by sulfate. Tissue contents of Mo are usually less than 1 ppm.
A deficiency of Mo first appears in the mid leaves and the older leaves. The leaves become chlorotic and the margins roll. Unlike other micronutrients, Mo deficiency occurs mostly under acidic conditions.
Boron uptake by plants is not well understood. Boron (B) is not mobile in the plant and seems to have many uptake and transport features in common with Ca.
Boron deficiency affects the young growing points first, e.g., buds, leaf tips, and margins. Buds develop necrotic areas and leaf tips become chlorotic and eventually die. Tomato leaves and stems become brittle. Normal leaves contain 20 ppm to 40 ppm B while high levels may lead to toxicity. Only small amounts of B are needed by plants and supplying excessive B from fertilizer solutions or from foliar sprays leads to toxicity.
Chlorine deficiency is very rarely observed in crop plants. This is because Cl is needed in very small amounts and Cl is present in the environment in the fertilizers, water, air, and media.
Nickel is absorbed actively and is readily transported in the plant. The Ni concentration is normal plant leaves is about 0.10 to 5 ppm. Deficiency symptoms include leaf tip chlorosis and necrosis.
Sources of Nutrients
Materials used to supply nutrients for greenhouse vegetable production are chosen based on several factors including cost per unit of nutrients, solubility in water, ability to supply multiple nutrients, freedom from contaminants, and ease of handling. The most commonly used fertilizer materials for greenhouses are listed in Table 1. These materials are mostly used to formulate the liquid fertilizer nutrient solution. Examples of calculations to formulate nutrient solutions are presented later in this chapter, and conversion values for these calculations are presented in Table 2.
Pre-mixed fertilizer materials are very popular with many greenhouse operators because they are easy to use. However, they are relatively expensive compared to individual ingredients, and the premixed materials leave little room for making changes in concentrations of individual nutrients. Pre-mixed fertilizers most often supply the basic needs for P, Mg, S, and micronutrients, and part of the N. They also may supply part or all of the K. Calcium nitrate plus potassium nitrate are often used to supply the remaining needs for N and K.
Pre-mixed fertilizers should be purchased from a reputable source that can supply high-quality materials. There is no need to be concerned with the brand names or whether or not the material is a "tomato special" or a "lettuce special." Often, these are simply brand names and really do not mean anything as far as the plant is concerned. For example, tomatoes probably will grow as well on a 4-18-30 "tomato special" as on a generic 4-16-32 used to supply the basic nutrient needs. They are too close for one to have superiority over the other.
Crop Nutrient Requirements
Productive greenhouse vegetable crops need the required amounts of each nutrient, the crop nutrient requirement (CNR), during the season. Plant growth rate determines, to a large degree, the amount of nutrients needed in the nutrient solution during the growth cycle. Generally, it is best to start with moderate amounts of nutrients early in the season and increase the concentrations to those in the formulations in Table 3 as the crop grows. This scheduling is most appropriate for crops grown in some type of solid media such as peat where significant amounts of nutrients can be held by the media. Supplying plants with small amounts of nutrients on a continual basis can be as satisfactory as supplying large amounts in less frequent additions.
This technique of scheduling has not been worked out for greenhouse vegetables in all production systems for Florida. Therefore, the grower should try to stay close to the formulations presented in Table 3. Growers should keep in mind that these formulas are good starting points and that they may need to be modified somewhat depending on growing experience and on specific site water analyses. The water analyses will affect most often the Ca, S, and acid amounts added to the fertilizer. More information is presented in the section that deals with pH control.
Water Quality for Greenhouse Vegetables
In NFT production systems, water is the production media in which the plants grow. For most solid-media cultural systems, water makes up a large portion of the growth media. It is very logical, therefore, that the quality of the production media, the water, be known. This is quite analogous to testing soil for nutrient-supplying capacity in field situations. Without an accurate water test, a grower cannot claim to have a good fertilizer management program and fertilizer may be wasted.
When locating a greenhouse operation, growers should consider both quantity and quality of the water source. Greenhouse crops require as much as 2 quarts of water per plant per day. Maximum requirements will occur when the plants are full-grown and there is high solar radiation and high temperatures. The irrigation system should have the capacity to deliver adequate amounts of water to all parts of the greenhouse. The pump and irrigation delivery system must be designed so that enough water can be delivered to each plant in the house during peak water consumptive periods.
Water quality is determined by the amounts of particulate matter (sand, limestone, organic matter, etc.), amounts of dissolved materials (nutrients and non-nutritional chemicals), and the water pH. These aspects must be determined by a good water analysis such as that conducted by the University of Florida Extension Soil Testing Lab or a competent commercial lab.
In most Florida situations, the lab should check the electrical conductivity (EC), hydrogen ion concentration (pH), sulfate (SO4) concentration, water hardness, sodium (Na) concentration, chloride (Cl) concentration, iron (Fe) concentration, and bicarbonate (HCO3) concentration. Hardness is relative to the Ca and Mg concentrations in the water and determination of these two nutrients will help the grower in calculating the Ca and Mg fertilizer program.
Electrical conductivity, measured as decisiemens per meter (dS.m-1) is an estimate of the total soluble salt content of the water. Water with an EC value greater than 1.5 dS.m-1 (same as 1.5 mmhos per centimeter [mmhos.cm-1]) is considered to be poor quality for most greenhouse crops. Specific salts present in the poor-quality water could accumulate in the growing media and reduce the growth of the crop. High soluble salt concentrations can reduce growth because the ions contributing to high EC could compete with fertilizer nutrients for plant uptake. In addition, high EC conditions reduce the ease with which the plant obtains water from the salty media. Water from deep wells along the coastal areas of Florida is becoming more saline from saltwater intrusion into the wells. Prospective greenhouse growers along the coast should be aware of this potential problem.
Calcium concentrations of 50 ppm Ca or higher are quite common in Florida well water. Magnesium concentrations are not as high, usually less than a few ppm. Very high concentrations of Ca and Mg and high bicarbonates could lead to precipitation of calcium and magnesium carbonates and clogging of irrigation system emitters.
Iron concentrations in some Florida wells are relatively high (0.5 ppm or more). Concentrations higher than 0.5 ppm could lead to iron precipitates resulting in plugging of irrigation emitters.
High concentrations of sulfur in well water are generally not harmful from a plant nutrition point of view. However, high S concentration can lead to buildup of sulfur-bacteria in the irrigation lines that could clog the emitters.
Bicarbonate (HCO3-1) concentrations are often in excess of desirable levels. High concentrations (above 30 ppm to 60 ppm) are related to increased pH values. Over time, high HCO3-1 can lead to increasing pH values in the growth media. Also, high HCO3-1 can lead to the precipitation of carbonates of Ca and Mg. Because of the potential problems associated with high HCO3-1 levels, it is recommended that water with high HCO3-1 amounts be acidified to pH 5.6 to 6.0 with nitric, phosphoric, or sulfuric acids.
Media Reaction, pH
The pH of the media refers to the concentration of hydrogen ions (H+) in the media solution. The concentration is determined by a pH electrode or can be approximated by a pH color-strip paper dipped into the solution. The pH of the media solution is important because certain plant nutrition aspects are influenced by pH such as solubility of essential elements. Most elements are absorbed best from a media with a pH of 5.5 to 6.5.
Media pH above 7.0 results in reduced micronutrient and phosphorus solubility. Extremely acidic pH can lead to micronutrient toxicities especially on soil-based media if manganese and aluminum are present.
Media pH values can change with time depending on uptake of certain macronutrients. For example, uptake of nitrate (NO3-1) can lead to an increase in solution pH. This is because the plant attempts to maintain an electrical charge balance across membranes; therefore, a hydroxyl (OH-) ion is exuded upon NO3- uptake.
Absorption of K+ has the opposite effect since H+ is exchanged resulting in acidification of the media. This rapid changing of media pH is most prevalent in hydroponics and rockwool compared to solid media culture because there is no buffering capacity in the former. Therefore, nutrient solutions need to be replaced periodically or acids or bases need to be added to restore proper pH levels.
Most well water in Florida has a relatively high pH value due usually to high bicarbonate (HCO3-1) levels. Water analyses should determine the levels of bicarbonate so that amounts of an acid to use to reduce the pH can be determined. More information is presented in the section on water quality.
Formulating and Mixing Stock Nutrient Solutions
Nutrient solutions are only as good as the quality of the ingredients and the time put into the formulations. Fertilizer materials should be of high quality and purchased from a reputable source. If the grower is using pre-mixed fertilizer, it is important to make sure the fertilizer blend has a tag that shows the analysis of the fertilizer, the sources used, and the company's name. The blend should be registered in the state of Florida so that the grower has recourse in case of problems with the fertilizer.
An accurate set of scales must be used to weigh out each material because different materials have different densities. Therefore, the volume method will not be accurate unless the measuring scoop is calibrated for each fertilizer material.
When mixing the fertilizer solutions, hot water will speed up the time for dissolution of the fertilizer. For small batches, mechanical stirring is satisfactory. For large batches, it might be better to invest in an electrical agitator or make up one from an old variable speed drill and a paddle welded onto a long-shank bit.
It is best to work in small batches (volumes), mixing them first, and then dumping each into a larger stock tank. For most small greenhouse operations (1 to 2 houses), stock tanks of 25 to 50 gallons are satisfactory. Replenishment of stock tanks for perlite or rockwool will depend on time of year and growth rate of the crop, and will vary from a few days to once every 10 days, depending on tank size. In NFT systems, replacement is more regular through the season due to the need for routine flushing of the sump tank.
In most production systems, at least two stock tanks are needed (Figure 3). This is because certain fertilizer sources when mixed together in concentrated form will lead to insoluble precipitates. The most common of these are calcium phosphate (from mixing calcium nitrate and phosphorus materials) and calcium sulfate (from mixing calcium nitrate and magnesium sulfate). Most production situations can get by with two stocks, one contains potassium nitrate, calcium nitrate, and iron chelate, and the other contains the phosphorus source, magnesium sulfate, micronutrients, and potassium chloride, or might contain some of the potassium nitrate as well (Figure 4).
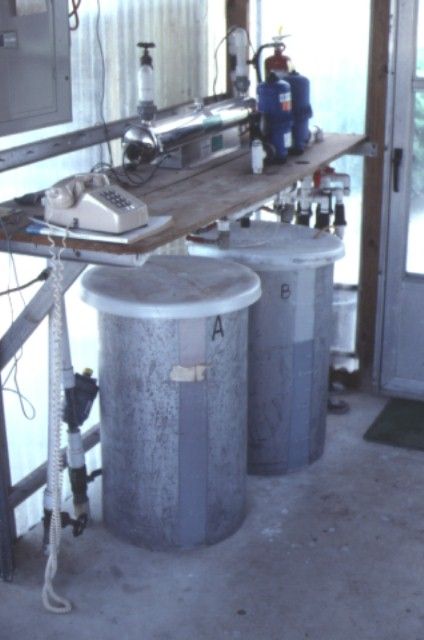
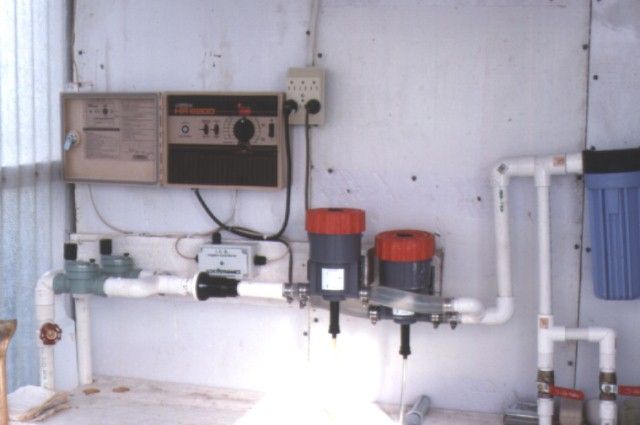
Once the small batches are added to the stock, the total volume of the stock tank is brought to the desired level and stirred. After the stocks have settled for a while (few hours), the solution will become clear, but a sludge will often form in the bottom of the calcium/potassium nitrate tank. This sludge is from certain additives in some fertilizer materials to prevent caking and dust. These materials are not soluble and will settle to the bottom of the tank. Therefore, the stock tanks will need to be rinsed periodically to remove this sludge. This problem can be alleviated by using technical grade fertilizer salts or clear (decanted) fertilizer solutions, such as liquid calcium nitrate.
Accurate calculations of the amounts of fertilizer materials to dissolve to achieve the desired concentrations of individual nutrients in the final growth nutrient solution are critical to the success of a fertilizer program (Figure 5).
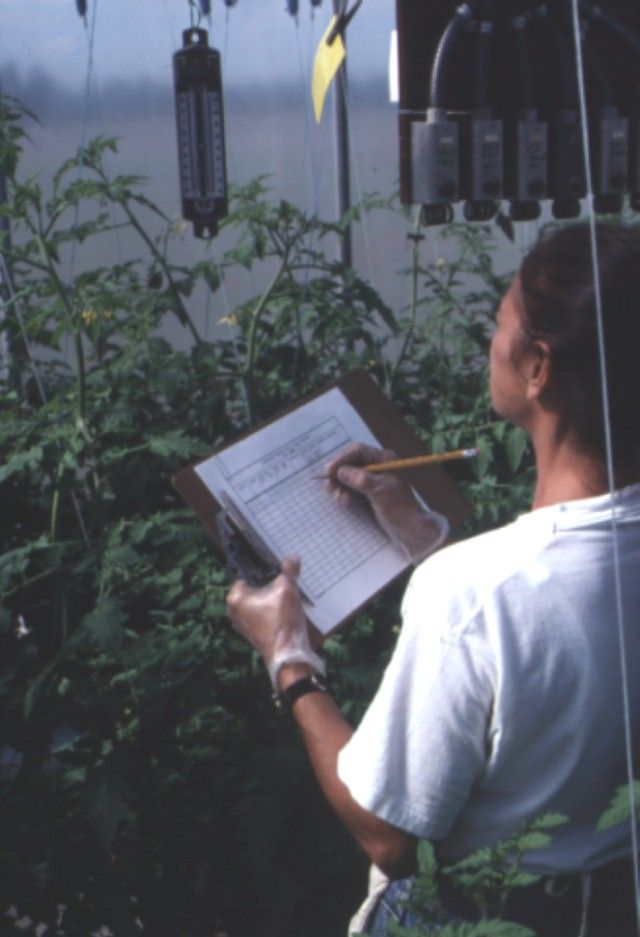
Using pre-mixed materials is satisfactory for the beginner, but experienced growers will find that they can be more efficient, thrifty, and knowledgeable about the crop if they learn to calculate their own formulations. The calculations are not difficult and, once completed, do not require re-working very often. To properly calculate the nutrient concentrations, the volume of the stock and sump tanks, the analysis of the fertilizer (Table 1), and a few equivalences (Table 2) must be known.
The following two examples are for a final nutrient solution applied to the plants that contains 150 ppm Ca, 150 ppm N, and 150 ppm K. The following calculations are used to illustrate a method to derive the amounts of the various fertilizer materials (potassium nitrate (KNO3), calcium nitrate (Ca(NO3)), and potassium sulfate (K2SO4) to be used to make up the desired final nutrient solution that is applied to the plants. A 25-gallon stock tank will be used.
Example A. A 1:100 ratio proportioner or injector in a perlite system or for a NFT system using 1 gal stock for each 100 gal water in the sump tank.
-
Starting with calcium nitrate, since that will be the only fertilizer source containing Ca:
150 ppm Ca = (150 mg Ca) per 1 L nutr. soln
[(150 mg Ca) per 1 L nutr. soln]. ÷ 19.0% Ca in Ca(NO3)2 = (790 mg Ca (NO3)2) per 1 L nutr. soln.
[(790 mg Ca (NO3)2) per 1 L nutr. soln] x 100 (dilution factor) = 79000 mg Ca (NO3)2) per 1 L stock
[(79000 mg Ca(NO3)2) per 1 L stock] ÷ 1000 mg per g = (79.0 gr Ca (NO3)2) per 1 L stock
[(79.0 g Ca (NO3)2) per 1 L stock)] ÷ 454 g per lb = (0.174 lb Ca (NO3)2) per 1 L stock)
[(0.174 lb Ca (NO3)2) per 1 L stock)] x 3.78 L per gal = (0.66 lb Ca (NO3)2) per 1 gal stock)
[(0.66 lb Ca (NO3)2) per 1 gal stock)] x 25 gal in tank = 16.5 lb Ca (NO3)2
16.5 lb Ca (NO3)2 to weigh out and dissolve in 25-gal stock.
Note: Some Ca might be supplied from the well water and this should be determined by a water analysis. The amount of well water Ca can be subtracted from the 150 ppm desired level so that less Ca needs to be derived from Ca(NO3)2. If this is the case, then the lost N will need to be made up from another N source such as ammonium nitrate.
Ca(NO3)2 also supplies N since 15.5% of Ca(NO3)2 is N. Therefore, if 16.5 lb Ca(NO3)2 is dissolved in the stock tank, the following is also provided:
[(16.5 lb Ca(NO3)2) per 25 gal stock] x [(454000 mg per lb) per 3.78 L per gal] = (7491000 mg Ca (NO3)2) per 95 L stock
[(7491000 mg Ca (NO3)2) per 95 L stock] x 15.5% N in Ca (NO3)2 = (1161105 mg N) per 95 L stock
(1161105 mg N) per 95 L = 12,220 ppm N in the stock
12,220 ppm N ÷ 100 (dilution factor = 122 ppm N in the final nutrient solution.
Since 150 ppm N is desired, an additional 28 ppm N from another source such as KNO3 is needed.
2. Using KNO3 (13% N and 44% K2O) and similar calculations, 4.5 lb KNO3 is required in the stock tank to achieve the desired N concentration. However, KNO3 also supplies K since it is 44% K2O. K is expressed as K2O and to convert from K2O to K, multiply by 0.83.
If 4.5 lb of KNO3 is added then: 4.5 lb x 44% K2O in KNO3 x .83 = 1.64 lb K in 25 gal stock.
This 4.5 lb of KNO3 supplies 79 ppm K in final nutrient solution. (The reader should try these calculations).
3. Since 150 ppm K is needed in the final solution and 79 ppm K is coming from KN03, the difference (7l ppm) can be made up from K2SO4 which is 50% K2O (Table 1).
71 ppm K = (71 mg K) per 1 L stock
[(71 mg K) per 1 L stock] ÷ 0.83 = (85.5 mg K2O) per 1 L stock
[(85.5 mg K2O) per 1 L stock] ÷ 0.50 = (171 mg K2SO4) per 1 L stock
[(171 mg K2SO4) per 1 L stock] ÷ 454 g per lb = (0.038 lb K2SO4) per 1 L stock
[(0.038 lb K2SO4) per 1 L stock] x 3.78 L per gal = (0.143 lb K2SO4) per 1 gal stock
0.143 lb K2SO4 x 25 gal in tank = 3.6 lb K2SO4 dissolved in 25-gal stock.
4. Summary. To get 150 ppm of N, K and Ca in the final nutrient solution, 16.5 lb Ca(NO3)2, 4.5 lb KNO3, and 3.6 lb K2SO4 are dissolved in 25-gallon stocks. The stocks will be diluted 1 part fertilizer stock to 100 parts incoming water to provide the desired nutrient solution for the plants. The K2SO4 needs to go into a different stock tank from the Ca(NO3)2 and KNO3 stock tank to prevent precipitation of the Ca + SO4 as calcium sulfate.
Example B. The grower is going to be using fertilizer from these stocks to add to the sump, (recirculating) NFT tank which is 500 gal in volume. To achieve the desired final concentration, 5 gal of each stock needs to be added to the sump tank. The above stocks were formulated for a 1:100 dilution in order to achieve the 150 ppm desired concentrations. Therefore, 1 gal each stock is needed for every 100 gal of final solution; so 5 gal of each nutrient solution is needed in the sump tank.
Although, only N, Ca, and K examples were used here, similar calculations can be made with other fertilizer materials. The reader can also see that similar calculations can be made for the situation where premixed materials are used. The problem is that once one of the nutrients, N, P, or K is selected to fix the fertilizer calculations on, the other two nutrients are fixed by default. Using premixed materials often results in sacrifices in desired nutrient concentrations of certain nutrients for the convenience of use of the material.
The following formulas are presented as examples of nutrient solutions useful for growing vegetables. Nutrient solution formulas given in terms of the final growing concentrations. To calculate the amounts in lbs of fertilizer for a l00x strength stock tank of volume 25 gal (95L), multiply the amounts in formulas by 0.21 (95 divided by 454).
Table 3. Formula 1. Tomato
Table 4. Formula 2. Cucumber
Table 5. Formula 3. Leafy vegetables
Table 6. Formula 4. Tomato
Table 7. Formula 5. Tomato
Table 8. Formula 6. Micronutrient stock
Measuring Solution Nutrient Concentration
Growers often desire to monitor the nutrient level in the fertilizer solution. This is an excellent practice, but care must be exercised in the methodology used to measure nutrients.
One common, quick and easy (but fault-prone method is to measure the soluble salt or electrical conductance (EC) level. Conductivity meters are used for this, and the measurement is easy and fast (Figure 6). However, this procedure only tells the grower the relative amount of total "salts" in the solution, and it tells the person nothing about each specific nutrient in the solution.
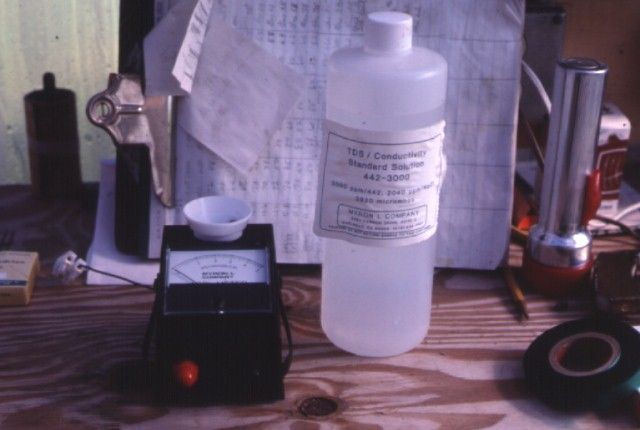
This methodology can get one in trouble if the user is not familiar with other methods, and using other methods to calculate and measure the individual nutrients. For example, suppose the grower was accustomed to maintaining an EC of 2.0 dS m-1 in the nutrient solution when using a high analysis mixed fertilizer. The grower then switches to a lower analysis fertilizer but keeps the EC at 2.0. In this case, the grower's conductivity meter was misleading him relative to the true concentration of nutrients such as N, P, or K, and he may even be in a deficiency situation even though the EC is the same as before.
The use of EC measurements is only helpful in checking total salt concentrations in the solution of a fertilizer program that has been accurately tested and proven. In an NFT system, EC monitoring helps keep the nutrient levels high, but the concentrations of individual nutrients will vary considerably from the desired ppm. For this reason, the nutrient solution is discarded periodically (at least weekly in Florida) and a new solution made. Soluble salt readings also can be helpful in determining probability of salt damage to plants growing in solid media. Raising and lowering of fertilizer solution concentrations based on EC results in across-the-board increases and decreases in nutrients when a change in only one nutrient may be warranted. This practice can lead to deficiencies or toxicities particularly with regard to micronutrients.
The best method to monitor solution concentrations is by direct nutrient analyses for specific nutrients. Concentrations of nutrients for the nutrient solution should be calculated in terms of ppm and the nutrient solution formulated to achieve these concentrations. These concentrations should then be maintained as long as the calculations were correct, the weighing and mixing was accurate, and the injection or mixing from the stock tanks was accurate. Needed changes in concentrations of specific nutrients are made by an adjustment of one fertilizer salt that supplies that specific nutrient.
Fertigation Equipment
In large operations, more than 4 to 6 houses, automation of the fertilizer program will save substantial time and money. Many NFT growers add fertilizer stock to the sump tank by hand; however, this addition can be automated by pumps and controllers to deliver a preset volume of fertilizer. Research is continuing into automated systems that monitor pH and nutrient concentrations in the sump and add only the needed element, acid, or base to maintain programmed concentrations of each nutrient.
Solid-media growers also can automate to varying degrees. The simplest system is one consisting of a time clock that controls a solenoid to water and fertilizer on preset intervals. More sophistication can be achieved with one of various digital controllers or computers to control fertigation time, frequency, and amount according to some parameter (e.g., sunlight, temperature, etc.). Automation of this type could extend to the control of the injectors that would add certain fertilizers or acid materials.
Automation is well within the reach of most growers cost-wise. There are many different systems available to automate greenhouse operations. It is suggested that the grower consult with several sources prior to deciding on a specific system.
Soluble Salt Effects
Excessive amounts of fertilizer in the media can lead to soluble salt burn, especially on young plants or seedlings. Salt burn is the result of damage to the roots by desiccation. High salt concentrations in the media reduce the capability of the roots to take up water. Reduced water uptake is due to the tendency for water to move away from the root toward the higher osmotic potential (salty) area in the media. Tomatoes generally tolerate higher salt conditions than cucumbers, peppers, or lettuce.
High soluble salt levels are especially dangerous in the early fall and late spring seasons because high temperatures and high solar radiation lead to increased water demand by the plants. In general, growers in Florida should not try to explicitly follow fertilizer programs used in northern climates. Northern fertilizer programs tend to rely on levels of fertilizer that often prove to be excessive under Florida conditions.
Damage to roots and plant stems caused by soluble salt burn leads to secondary invasion by pathogenic fungi and resulting rot. Evaporation of water can leave behind dried salt deposits that can clog emitters.
Control of soluble salt damage begins with correct formulation of the nutrient solution. The grower should monitor the EC of the nutrient solution as it is delivered to the plant. This will serve as an indicator that the nutrient solution was likely formulated correctly. Also, the EC of the growing media should be checked to ensure that EC is not building to damaging levels. In NFT, the nutrient solution EC should be kept relatively constant between flush periods by adding fertilizer solution.
In rockwool or perlite, the EC in the slabs or bags should not vary more than 1.0 EC units dS m-1 above or below the EC of the applied nutrient solution. If the EC is greater than 1.0 dS m-1 below, then too much nutrient solution is being added at any one fertigation event. If the EC is 1.0 dS m-1 higher in the media compared to the incoming nutrient solution, then there is not enough nutrient solution being applied at any one application.
Once it is determined that the media EC is too high, the only recourse is to flush the system and apply a new nutrient solution of correct EC and nutrient content. Flushing should be done with water or a weak nutrient solution.
The EC meter should be carefully calibrated using a high-quality conductivity standard. The small hand-held meters in common use require regular calibration to remain accurate. These meters are not error-free or maintenance-free and inaccurate measurements may result if they are not checked once every week or two.
Flushing Sump Tanks
Varying amounts of nutrients are absorbed by plants so that the concentrations of nutrients in the nutrient solution change. The recommended procedure is for growers to determine the required nutrient solution concentrations based on the part per million (ppm) method. The EC can be measured and maintained by daily additions of equal amounts of the two fertilizer stock solutions. However, even though the EC might be maintained, the concentrations of specific nutrients cannot be determined. Therefore, it is recommended that the sump tank be flushed once per week and new solution formulated so that the original nutrient concentrations can be restored. In addition, the weekly flush removes some organic matter and sloughed-off plant debris.
Prior to flushing, the tank volume should be allowed to be drawn down to 100 or 200 gallons to minimize the volume of solution discarded. At the end of the day, the remaining solution can be pumped out and disposed of properly. The sump tank is then filled with water adjusted to pH 5.8 to 6.0 containing 25 to 50 ppm Ca and circulated on same ON-OFF cycle through the night. The Ca is added to keep root tips healthy during the flush period. During the early morning, the tank is emptied and refilled with the complete nutrient solution formulated from the fertilizer stocks. Growers need to be sure that all valves and clocks are checked for proper position and adjustment.
Tissue Analysis
The most helpful manner in which to determine the effectiveness of the fertilizer program is to analyze the plants for nutrient contents. This is done through nutrient analyses of the plant leaves. It is a good practice to get into the habit of periodically checking the nutrient concentrations in the plant leaves. Tissue analyses can help detect deficiencies and toxicities.
Most information used to interpret tissue analysis is based on the most-recently-matured whole leaf. This leaf is the leaf downward from the tip of the plant that is nearly fully expanded. For tomatoes, this leaf is usually the fifth or sixth leaf from the top.
When sampling leaves for analysis, several considerations must be made in addition to the correct leaf to take. Leaves should be collected at random within the house making sure enough are taken. Usually, 15 to 20 leaves will be enough. Collect the whole leaf including the petiole ("leaf stem") which connects the leaf to the main stem of the plant. Clean leaves that are free of pesticide residues should be taken. The leaves are packaged in a paper bag and sent to the laboratory promptly. It might be advantageous to pre-dry the sample before mailing. Leaves can be dried on a screen placed in a non-drafty area in the greenhouse.
When attempting to diagnose a particular suspected nutrient deficiency, leaves should be collected from "good" and "bad" plants. This will help determine the cause of the problem.
Diagnosing nutrient problems cannot be done effectively without accurate and complete fertilizer records. Everything done with regard to fertilizer management should be recorded. Records on fertilizer stock formulations, amounts of nutrients applied, frequency of flushes, volumes of stock and sump tanks, and fertilizer tags should be recorded. This information will be most useful in the diagnostic procedures.
Nutrient sufficiency values and ranges have been established for most vegetable crops. Most of the information is for field vegetables, but some can be found for greenhouse vegetables. Nutrient concentrations should stay slightly above the critical or sufficiency values. There is no need to have tissue concentrations rise high above the sufficiency range. For some nutrients, e.g., micronutrients, toxicity might easily occur. For other nutrients, it would simply be a waste of money. Using mixed fertilizers to raise (or lower) specific nutrients could cause an unwanted change in another nutrient. For example, one would not increase the amount of 4-16-36 fertilizer just to increase the P. An unwanted increase in N or K might result. If changes in specific nutrients are required, then individual-salt fertilizer materials should be used.
In addition to whole-leaf tissue samples addressed above, leaf petiole sap can be analyzed for nitrate-N and K concentrations (Figure 7). Sap analyses are quick and easy and very helpful in spot-checking plant nutrient status. Methods for petiole sap analyses are available in Fla. Coop. Ext. Circ. 1144 "Plant Petiole Sap-Testing For Vegetable Crops". The critical ranges for greenhouse tomato petiole nitrate-N and K concentrations are presented in Table 9.
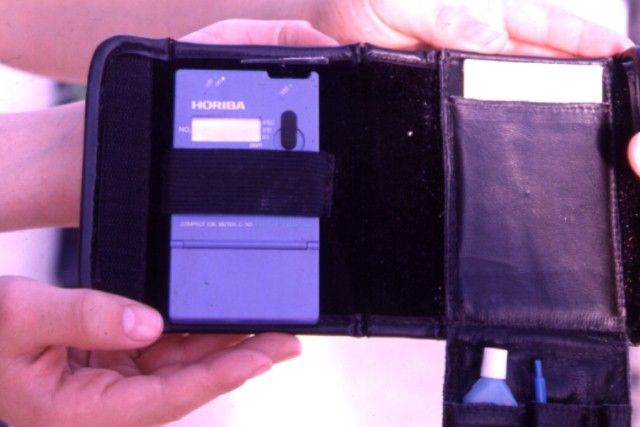
Tissue nutrient values for whole leaves of greenhouse vegetables in Table 10, Table 11, and Table 12 have been summarized from various sources. It should be evident that there is quite a range for acceptable values for tissue nutrient concentrations. The objective of the fertilizer program is to keep the plants within the range and not above or below the range.
Foliar Sprays
Many growers ask about the usefulness of foliar sprays of nutrients or other chemicals such as antitranspirants. In general, these products have not been found to have a place in a well-managed greenhouse.
Fertilizer programs are designed to supply nutrients to the plant via the root systems. Roots are very well adapted to absorbing nutrients and leaves are not. Leaves will absorb a certain amount of nutrients, but for most elements, the uptake is inadequate. The leaf is covered by a waxy covering, the cuticle, and this structure makes it difficult for nutrients and other chemicals to enter the leaf in large amounts.
Often, special miracle products are touted by salesmen for use to prevent "stress" and that routine sprays will improve yield and quality. Plants under stress are most likely to have problems related to temperature or light rather than fertilizer. In many research trials with field vegetables, it has been shown that routine shot-gun foliar sprays do not increase yield or enhance quality. In fact, many studies show decreases in yield from these foliar sprays.
There is a big difference between shot-gun sprays and a foliar nutrient spray to treat a specific deficiency. One situation where a foliar nutrient spray might be recommended is iron deficiency. Sometimes, the upper leaves of a tomato plant may turn yellow, especially after a large number of tomatoes have been set on the plant. Foliar sprays of a solution of 0.5 to 1.0 ml of a 5% Fe solution in 1 gallon of water will usually clear up the problem. Repeated sprays might be needed. Foliar sprays of micronutrients must be done on a diagnosed basis, and care must be exercised to apply the correct amount. Foliar burn can easily occur where care is not exercised.
Other foliar sprays such as growth regulators and antitranspirants have not produced consistently positive results in field vegetables. Healthy plants that are performing normally probably will not respond to a miracle product. In the case of antitranspirants, it is unlikely that they will have a desired effect in a greenhouse. Desiccation is not a problem in most poly-covered greenhouses because they are usually very humid inside and water loss is not a great problem. In addition, for greenhouse situations where CO2 is being injected, then antitranspirants might have a negative effect.
In summary, normal performing plants probably will not respond to extra stimulus from foliar chemicals. Growers could waste money, and might even damage their crop from shotgun foliar products.
Related Literature
These older references may still be available via on-line books sales sources.
Bauerle, W. L. 1984. "Bag culture production of greenhouse tomatoes." Ohio St. Univ. Special Circ. 108. 7pp. https://kb.osu.edu/handle/1811/71842.
Dowgert, Michael. 2022. Rockwool as a Substrate for Hydroponic Growing Systems. https://www.hydrofarm.com/rockwool-as-a-substrate-for-hydroponic-growing-systems.
Gerber, J. M. 1985. Plant growth and nutrient formulas. p 58. In. A. J. Savage (ed.). Hydroponics Worldwide: State of the art in soilless crop production. Int'l Ctr. for Special Studies, Honolulu, Hawaii.
Hochmuth, G. 1988. Unpublished data.
Hochmuth, G. 1990. Nutrient solution formation for hydroponic (rockwool and NFT) tomatoes in Florida. Gainesville: University of Florida Institute of Food and Agricultural Sciences. https://edis.ifas.ufl.edu/publication/CV216
Johnson, H., G. J. Hochmuth, and D. N. Maynard. 1985. Soilless culture of greenhouse vegetables. Gainesville: University of Florida Institute of Food and Agricultural Sciences. https://ufdc.ufl.edu/UF00008515/00001/images/2
Jones, J. B. 1983. A guide for the hydroponic and soilless culture grower. Portland, OR: Timber Press, 124 pp.
Savage, A. J. (ed). 1985. Hydroponics worldwide: state of the art in soilless crop production. Int'l Center for Special Studies, Honolulu, Hawaii. 194 pp.
Smith, D. L. 1987. Rockwool in Horticulture. Grower Books, 50 Doughty St. London, WCIN2LP. 153 pp.
Van Eysinga, J. P., N. L. Roorda, and K. W. Smilde. 1981. Nutritional disorders in glasshouse tomatoes, cucumbers, and lettuce. Center for Agric. Publishing and Documentation, Wageningen, The Netherlands. 130 pp.
Winsor, G., and P. Adams. 1987. Diagnosis of mineral disorders in plants. Vol.3. Glasshouse crops. Her Majesty's Stationery Office, London. 168 pp.
Wittwer, S. H., and S. Honma. 1979. Greenhouse tomatoes, lettuce, and cucumbers. Michigan State Univ. Press. 225 pp.
More Information
For more information on greenhouse crop production, please visit our website at http://smallfarms.ifas.ufl.edu [January 2012].
For the other chapters in the Greenhouse Vegetable Production Handbook, see the documents listed below:
Volume 1: Introduction • Financial Considerations • Pre-Construction Considerations • Crop Production • Considerations for Managing Greenhouse Pests • Summary
Volume 2: Physical Greenhouse Design Considerations • Production Systems • Other Design Information Resources
Volume 3: Preface • General Aspects of Plant Growth • Production Systems • Irrigation of Greenhouse Vegetables • Fertilizer Management for Greenhouse Vegetables • Production of Greenhouse Tomatoes • Greenhouse Cucumber Production • Greenhouse Nematode Management • Alternative Greenhouse Crops • Vegetable Insect Identification and Management Considerations for managing greenhouse pests
Sources of nutrients used to formulate various nutrient solutions for greenhouse vegetables.
Sufficiency ranges for nitrate-N and K concentrations in fresh petiole sap of greenhouse grown tomatoes.
Sufficiency nutrient ranges for greenhouse tomatoes (dried most-recently-matured whole leaves).