Computer control technologies make use of computer systems and other hardware to monitor physical conditions of an environment, make decisions about actions required to modify the environment, and act on devices that will result in changes to the environment. For example, in a greenhouse, a computer can be used to monitor temperature, and turn heaters on and off at appropriate intervals to maintain a constant temperature. Computer controls are particularly useful in systems in which 1) many variables are controlled, 2) there is an large number of devices that must be controlled, 3) frequent or constant attention is required, and 4) labor costs are high.
The State of a System
Environmental systems, such as the biological systems dealt with in agricultural production, are extremely complex in nature. In fact, their complexity is so great that describing and predicting their behavior in physical and mathematical terms may not be possible. In order to manage such a system we must simplify it and describe it in terms of a set of measurable values that are known to have the most important effects on production. Following the greenhouse example, we find that, the quality and quantity of production will depend on solar radiation, humidity, temperature, gas composition of the air, age of the plant, irrigation water quality, nutrition programs, and many other factors. Because it is expensive, sometimes impractical, and sometimes impossible to attempt to control all of these variables, the set of controlled variables is generally restricted to a smaller set, such as, temperature, humidity, and CO2 concentration. Thus, the state of the system at any given time is defined by the magnitudes of a set of important measurable variables. Table 1 lists some variables that are often used to define the state of different agricultural productions systems from a control viewpoint.
Control System
A control system consists of a combination of hardware and software that acts as a supervisor with the purpose of managing the controlled system. This is done by the use of a control loop. A control loop consists of 1) monitoring the state variables, 2) comparing the state variables with their desired or target state, 3) deciding what actions are necessary to change the state of the system, and 4) carrying out the necessary actions. Performing these functions requires a combination of hardware and software that must be implemented for each specific application.
Hardware Components
For the control loop shown in Figure 1, each of the hardware elements is described below.
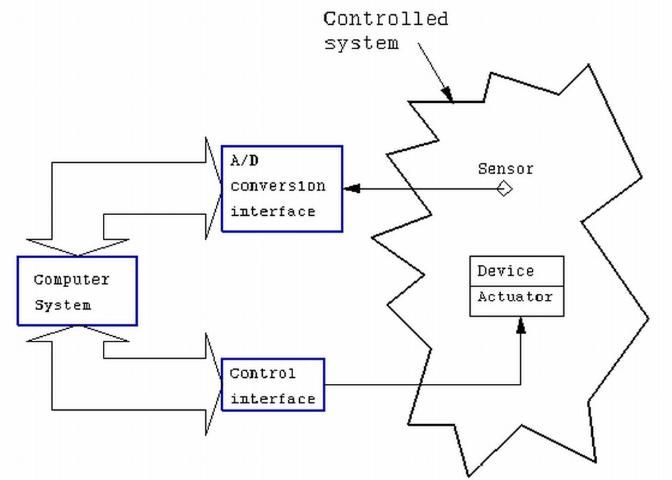
Sensors
A sensor is a device placed in the system that produces an electrical signal directly related to the parameter that is to be measured. In general, there are two types of sensors, continuous and discrete (see Figure 2).
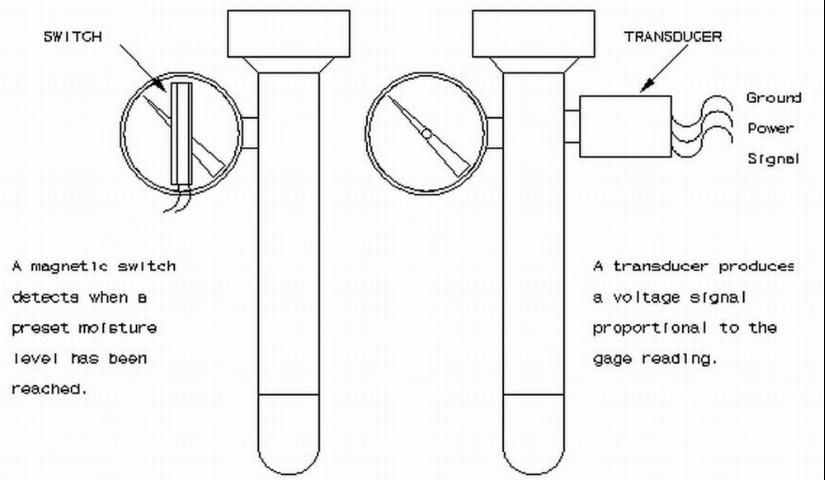
- Continuous. Continuous sensors produce a continuous electrical signal, such as a voltage, current, conductivity, capacitance, or any other measurable electrical property. For example, sensors of different kinds can be used to measure temperature, such as thermistors and thermocouples. A thermocouple will produce a voltage difference that increases as the temperature increases.
Continuous sensors are used where values taken by a state variable are required, for example, to estimate the material that is transferred using a conveyor belt, the speed of the conveyor belt may be required.
2. Discrete. Discrete sensors are basically switches, mechanical or electronic, that indicate whether an on or off condition exists. Discrete sensors are useful for indicating thresholds, such as the opening and closure of devices (vents, doors, alarms, valves, etc.). They can also be used to determine if a threshold of an important state variable has been reached. Some examples of discrete sensors are, a float switch to detect if the level in a storage tank is below a minimum desirable level, a switching tensiometer to detect if soil moisture is above a desired threshold, and a thermostat to indicate if a certain temperature has been reached. When combined with time, pulses from switches can be used to measure rates. For example, to the volume of fuel, water or chemical solution passing through a totalizing flow meter with a magnetically activated switch, or the speed of a rotating flywheel.
Because they provide the basic data that drive an automatic control system, sensors are an extremely important component of the control loop. Understanding the operating principle of a sensor is very important. Sensors many times do not react directly to the variable being measured. For example, when a mercury thermometer is used to measure temperature, temperature is not being measured, rather, a change in volume due to a change in temperature is measured. Because there is a unique relationship between the volume and the temperature the instrument can be directly calibrated to provide temperature readings. The ideal sensor responds only to the "sensed" variable, without responding to any other change in the environment. It is important to understand that sensors always have a degree of inaccuracy associated with them and they may be affected by other parameters besides the "sensed" variable. The classical example is that of soil moisture measurement using electrical conductivity probes. The electrical signal produced by this sensor is closely related to soil moisture, but is greatly affected by temperature and dissolved salts (fertilizers, for example) in the soil. Another important factor related to the sensor is its time response. A sensor must deliver a signal that reflects the state of the system within the frame of time required by the application. Using the soil moisture measurement example, the sensor must be able to "keep up" with the changes in soil moisture that are caused by evapotranspiration. Thus, proper selection of the sensors and understanding the principle of operation is critical to the success of a control system.
A/D interface
Since computer systems work internally with numbers (digits), the electrical signals resulting from the sensors must be converted to digital data (see Figure 3). This is done through specialized hardware referred to as the Analog-to-Digital (A/D) interface. Discrete signals resulting from switch closures and threshold measurements are converted to 0 and 1. Continuous electrical (analog) signals produced by the sensors signals are converted to a number related to the level of the sensed variable. The accuracy of the conversion is affected by the resolution of the conversion equipment. In general, the higher the resolution the better the accuracy. For, example if a pressure sensor produces a voltage signal ranging from 0 to 5 volts for a range of pressure of 10 atmospheres, an 8 bit resolution A/D board will be able to detect a change in voltage of about 5/255 volts which will results in measurable increments of 50/255 atmospheres. If the resolution of the A/D board was 12 bit, the board would be able to detect a change in voltage of about 5/4095 volts or a measurable increment of 50/4095.

Computer system
The A/D conversion hardware is directly connected to the computer system. Given the current state of technology, the computer system may be a PC (personal computer), a minicomputer, or a specially designed machine that is solely dedicated to the control task. The type of machine depends on the type of application, and is greatly affected by factors such as environmental characteristics, complexity of the controlled system, and the speed with which conversions need to take place (controlling a high speed extruder requires much more speed than a golf-course irrigation system). Many agricultural applications can be economically carried out using PCs, as is evident by the increasing number of system integrators and equipment manufactures that are marketing PC-based control systems. Also, many manufacturers of control equipment have designed and manufactured specialized computer control systems.
Control Interface
Using control software, decisions may be made to modify the controlled system. The actual changes are achieved by having devices within the system that will affect the controlled variables. These devices are controlled through actuators that respond to signals from the control interface. The devices may be of the nearly continuous or discrete types. For example, the extension of a robot arm of a citrus harvesting robot requires the use of a continuous signal from the computer, while a fan requires only an on/off (discrete) signal from the computer. In general, any device that can be powered electrically can be controlled by a computer.
Software Components
The software is used to implement procedures as they apply to the controlled system. These procedures are usually very elaborate, but in a well-engineered piece of software, they are transparent to the user. Because the user is more concerned with ease of use and performance of the system, good quality software has an interface that allows easy definition of the characteristics of the system to be controlled and simplifies the assignment of hardware resources. Performance is measured by how well the computer control system maintains the desired state. Figure 4 compares a thermostatically controlled water boiler and a computer controlled one. It is clear that the computer control systems better maintains the desired state of the system.
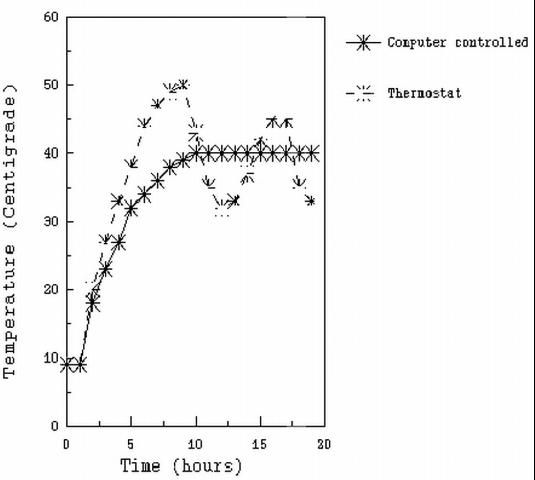
Selecting an Environmental Control System
Assuming that computer control is being contemplated as an aid in managing an environmental system, four general steps can be followed to appropriately select a computer control system.
- Step 1: Identify measurable variables important to production.
It is very important to correctly identify the parameters that are going to be measured by the computer's data acquisition interface, and how they are to be measured. An example set of variables typically used in greenhouse control is shown in Table 2. A similar table can be developed for any other application. The variables to be measured in a control system are limited to those that can be measured in a practical way. In other words, an electronic sensor that can be interfaced with a computer must be readily available, accurate, reliable and low in cost. If a sensor is not available, the variable cannot be incorporated into the control system, even if it is very important. Many times variables that cannot be directly or continuously measured can be controlled in a limited way by the system. For example, fertility levels in nutrient solutions for greenhouse production are difficult to measure continuously, yet the computer can be used to apply a predetermined quantity of nutrient at prespecified intervals. Here the computer is functioning as an elaborate timer, and not as a feedback control system.
Examples os Measurable Variables in Greenhouse Control, Sensors that may be Used, and the Importance of the Measured Variables to Production.
- Step 2: Identify variables that are to be controlled.
Measurable variables that directly affect production can be selected as control or target state variables if they can be affected by some controllable action. These variables are sometimes referred to as set points. For example, the temperature inside a greenhouse can be affected by controlling heaters, fans, or window openings. On the other hand, thermal loads due to solar radiation in animal housing operations cannot be controlled, since they depend on weather alone, and there is usually no mechanism (such as an adjustable thermal screen in a greenhouse) that allows control of this variable. Those variables that cannot be controlled but affect the state of the system are referred to as disturbances. Those variables that are not set points but may be useful in making control decisions are referred to as intermediate variables.
- Step 3: Investigate control strategies.
An important element in considering a control system is the control strategy that is to be followed. The simplest strategy is to use threshold sensors that directly affect actuators to devices. An example is a simple thermostat connected to a furnace. A second control level is a multistage system based on threshold sensors. For example the cooling fans for a broiler production house can be divided into four banks. As the temperature increases one bank may be turned on. With a further increase in temperature a second bank would be powered, and so on. A third control level would include some logic decisions based on other conditions. For example, if it is desired to decrease the moisture content of grain in a bin, air circulation should not be started if the moisture content of the outside air would result in a relative humidity of the air inside the bin that would not produce drying.
More complex control strategies are those based not only on the current values of the controlled variables, but also on the previous history of the system, including the rates at which the system variables are changing, and a knowledge of how energy and mass transfers occur in the system. For example, the fan banks in an animal housing unit could be turned on or off based on the current temperature, how fast the temperature is changing with time, the external radiation and how it is changing, knowledge of how radiation is converted into heat, and how heat is gained or lost through the structure's walls and the ventilation system. Systems that base the control strategy on an understanding of the physics of the system and respond to the unsteady nature of the system are usually referred to as dynamic control systems. Even more advanced, are those strategies that, in addition to the above, implement practical knowledge gathered through experience with the production system and simulations of the effects of the environment on the product. The implementation of many of these strategies requires sound engineering and, in many cases, they are still at a research stage.
- Step 4: Identify the software and the hardware to be used.
It is very important that control system functions are specified before deciding what software and hardware system to purchase. The main differences between a conventional feedback control system and computer based control systems are the power and flexibility that the computer provides. From the users viewpoint these include the ability to: 1) Expand the number of measured variables (input subsystem) and controlled devices (output subsystem) so that growth and changing needs of the production operation can be satisfied in the future, 2) provide a flexible and easy to use interface that allows the user to assign input and output devices, and 3) allow the user to specify important details of the control algorithms that are implemented by the software. Notice that these three points are primarily software related. Hardware must always follow the selection of software, with the hardware required being supported by the software selected. In addition to functional capabilities, the selection of the control hardware should include factors such as reliability, support, previous experiences with the equipment (successes and failures), and cost.
Commercially Available Systems
Computer control systems should not be confused with elaborate timers or dedicated feedback control systems. Computer control systems are usually identifiable because they rely on some type of computer system and the flexibility and power associated with it. When control systems are very elaborate it is best to seek professional advice in selecting a system. Several computer control systems are available commercially for a variety of agricultural applications. It is usually beneficial to study commercially available systems when selecting a computer control system. However, care must be exercised to make sure that the functions served by the system are those that are required by the control application. Studying where the system has been used before and the differences between the environments in which it has been used, and the environment in which it is to be used, usually provides many insights on the commercial system. When using commercially available systems it is often necessary to purchase equipment with a higher capacity than required, however, the advantages of available support and access to the experience of other users far outweighs the extra cost. Figure 5 shows the architecture of a system for computer controlled animal housing.
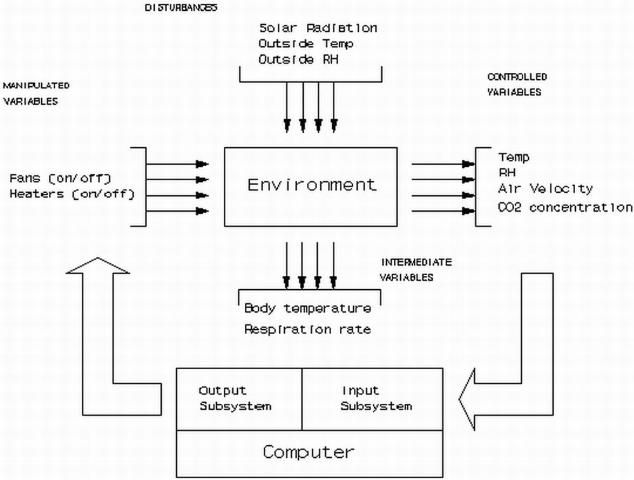
Do-It-Yourself Systems
For many control applications it is possible to develop control systems from off-the-shelf components. This, however, is usually limited to systems that do not require elaborate control algorithms. For example, home computers with powerline modulators have been used successfully for many years in propagation houses for ornamental production and turf management. The basic components of a do-it-yourself system are shown in Figure 6.
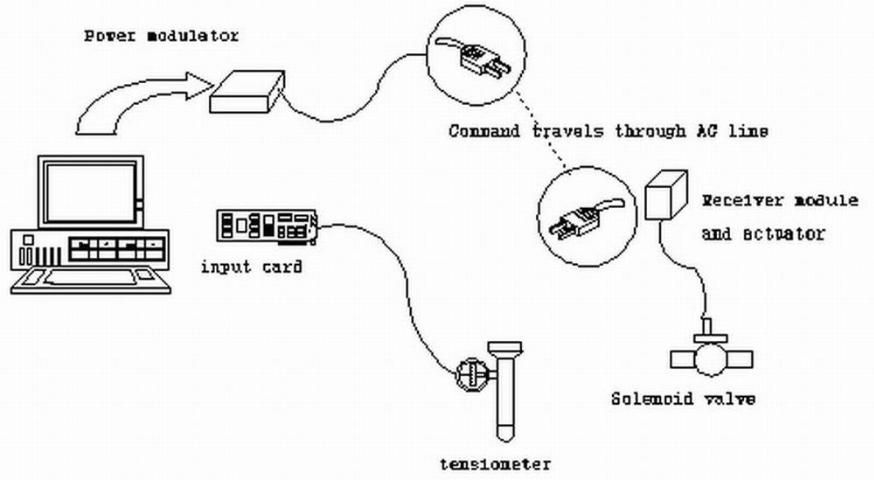
Emerging Technologies
As a result of the increase in power and decrease in cost of personal computers during the late seventies, and the explosion in tools for application development during the eighties, these past 15 years have seen a rapid increase in computer systems that improve design and management capabilities in agriculture related operations. This section looks at some new technologies that are closely related to computer control. These technologies were researched and tested during the last decade, and are likely to find themselves in production agriculture in the future. These areas are that of 1) real-time expert systems, 2) modelling and 3) robotics.
Real-time Expert Systems
Expert systems are the most celebrated result of artificial intelligence technology. An expert system is a computer program that mimics a human expert in finding a solution to a difficult problem. Expert systems can be applied only to well defined problems for which a human expert has a solution. Through a process called knowledge engineering, the expert's knowledge of the problem is expressed as a set of rules. These rules are then used to build the computer program that will emulate the expert. The computer program consists of two parts, the knowledge base and the inference engine. The knowledge base is the set of rules obtained from the human expert by the knowledge engineer and a collection of facts that represent the state of the system. The inference engine applies the rules and user-provided data to reach a diagnostic. Most conventional expert systems query the user for data until they are able to reach one of several possible diagnostics. Unlike conventional expert systems, which as a goal try to reach a diagnostic, real-time expert systems operate with dynamic data and time critical responses. In a real-time expert system most of the input comes from sensors and most of the output goes to effectors. Because of this, real-time expert systems are said to be data driven.
Although many conventional expert systems have been developed for agricultural applications, few have been used widely in production agriculture. An example of a real time expert system application in agriculture is RTES. RTES operates an irrigation system based on soil-moisture sensor input and a set of rules obtained from the system manager and irrigation specialists.
Computer Modeling
The use of computer models to simulate complex environmental systems such as those found in production agriculture have improved by orders of magnitude since the initial attempts 20 years ago. Modelers have been successful in applying models for improving not only agricultural system management, but also for strategic and tactical planning. The number of models that have been developed to date are too numerous to mention here. Collectively, these models include virtually every facet of agricultural production systems.
For various reasons, most models have not achieved broad application in production agriculture. They have been used mostly by scientists who are studying agricultural production systems. During the second half of the last decade concerns on usability and transportability in the use of models have resulted in major efforts that address these issues. An example of these efforts is the International Benchmark Sites Network for Agrotechnology Transfer (IBSNAT). The IBSNAT project consists of 29 sites worldwide that are adapting and implementing models for the integration of new or alternative crops, cultivars, products, and practices into existing farming systems to render them more productive, stable and sustainable. IBSNAT integrates the use of modeling, expert systems, and information management technologies. It is clear that these technologies will be used effectively during this decade.
Robotics
Although the construction of a machine that simulates a human being in its physical and mental attributes is far from being achieved, robotics technology has produced intelligent machines that are able to receive sensory input from the surrounding environment, and manipulate it to achieve prespecified results. Robotics is an area that incorporates the use of real-time expert systems, and control technologies. Agricultural robots have been used mostly under experimental conditions. However, it is clear that given current technology these complex machines can be built. Table 3 shows some examples of agricultural robots that were built during the recent years.
A Look into the Future
Given the state of current technology, it is not difficult to envision a closed agricultural production system in which many of the agricultural operations are automated. All of the elements required to build an "agricultural production machine" exist today. Such a machine could have some of the following capabilities:
- The aerial environment is controlled. Temperature, relative humidity, solar radiation, and gas composition are adjusted according to the crop's stage of growth to insure the product will be of the required quality at a given market window, for example greenhouse production of Easter.
- Nutrition is controlled. Nutrition and root environment are controlled by means of a hydroponic solution, for example, hydroponically grown lettuce.
- Pollination (or propagation) is controlled. By maintaining an insect free environment, desired levels of pollination are achieved using mechanical shakers, for example, greenhouse grown winter tomatoes.
- Disease and pest control. Using visual symptom based identification of diseases and pests, control chemicals can be applied. An example is the identification of molds on oranges and aerial application of pesticides using application towers.
- Harvesting and post-harvest. Using visual identification and mobile robots to select, pick, and transport fruit to a machine where grading and packaging take place. A robotics citrus picker, for example, displays this capability.
In addition, all of the actions above could be supported in a knowledge based decision system that incorporates the expert rules in several fields that may include for example 1) basic knowledge of the system, such as, population dynamics, soil-plant-air-water relations, market economics, 2) rules of thumb developed from observation, 3) collection of data on the past behavior of the system, and 4) analysis of long term effects of the actions taken on the system using models, that include not only crop growth and yield estimations but also effects of different market conditions and their effect on profits.
Although the above scenarios may seem far in the future, it is clear that all of the technological components are available, and that they have been independently used, or at least tested at a prototype level. Also, integration of all of these technologies will no doubt encounter problems that will be difficult to overcome. However, it is clear that the technology is evolving in this direction.
Closing Remarks
Given the declining cost of powerful computer systems and associated electronic devices, as well as the present trend towards increasingly powerful and easy to use software, it is clear that computer controlled systems will replace many of the manual and static control systems in use today. Although computer control systems are not without problems, such as the requirement of a high quality electrical source and maintenance, they provide a flexible and precise form of maintaining an environment. In addition, they allow control of complex systems where strong interactions in the controlled variables occur and systems in which traditional control and manual procedures cannot be used. Overall, computer control coupled with sound knowledge about a production system, provides a tool for better management of resources that results in an improved quality and quantity of production.
The introduction of computer control technology in agriculture is likely to rapidly advance in the immediate future. The continuously decreasing costs of hardware and software, the wider acceptance of computer systems in agriculture, and an emerging agricultural control system industry in several areas of agricultural production, will result in reliable control systems that address several aspects of production. Further improvements will be made as less expensive and more reliable sensors are developed for use in agricultural production. The elements of this technology are in use today.