Performance of sprinkler and microirrigation systems can be evaluated by measuring operating pressures, application rates, and uniformity of water application under nursery conditions. Knowledge of these factors is important to determine the causes of poor system performance. This publication will focus on operating pressure and will discuss application rates and uniformity in other publications.
Measuring Operating Pressures in the Irrigation System
It is important to monitor pressures at critical points in an irrigation system. A well-designed and correctly-installed system will have permanent pressure gauges at the critical points such as pump outlet, both sides of the filtration system (Figure 1), and at the inlet to each irrigation zone. The gauges should be checked periodically and replaced as needed. These pressure gauges allow the system manager to monitor the performance of the system and pinpoint any problems as soon as they occur. For example, a drop in pressure at the inlet to the irrigated zone may indicate a broken pipe, too many zones running at the same time, or excessive discharge from the nozzles. The difference in pressure between two sides of the filter can indicate the need for filter cleaning. A significant decrease in pressure through the dirty filter can result in insufficient operating pressures at the irrigation zone. Periodically, operating pressures within each zone should be tested to evaluate system performance.
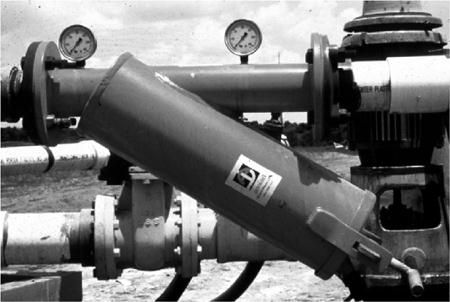
Overhead Irrigation
Irrigation nozzles are designed to operate over a specific range of pressures. The general rule is that the operating pressure of any nozzle in an irrigation system should not deviate by more than 15% from the nozzle pressure specified by the manufacturer. That also means that the difference between the highest and the lowest pressure in the irrigated zone should not exceed 30%. If operating pressures are out of this range, irrigation system uniformity decreases and application rates may not be consistent.
Visual observation of irrigation water distribution during irrigation may give an indication that nozzle pressure is undesirable. If operating pressure is too high, very small droplets are produced and fogging can be observed. High pressure also results in irregular nozzle rotation and increased amounts of water applied near the sprinklers. Conversely, operating pressures that are too low produce a doughnut-shaped water distribution pattern with very little water applied close to the sprinklers.The pressure can be measured at the sprinkler nozzle using a pitot tube attached to a pressure gauge. The pitot tube is placed about 1/8-inch from the nozzle and adjusted until the highest constant pressure can be read. This procedure is illustrated in Figure 2. A pitot tube can be purchased from an irrigation supply company.
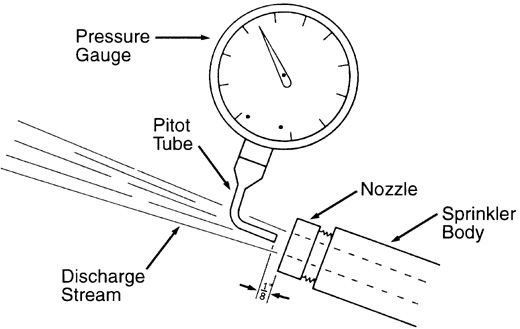
Microirrigation or Low-Volume Irrigation
Operating pressures of microirrigation or low volume systems can be measured using a portable pressure gauge equipped with a flexible tube and a fitting, which allows replacement of an emitter with the pressure gauge. The pressure distribution in a lateral line with more than 10 emitters will not be significantly affected by blocking one emitter while others continue to flow. Portable gauges can be purchased that are equipped with a needle on a flexible tube; for lateral lines constructed of flexible material at least 0.04 inch thick, the needle can be inserted directly into the lateral line. The opening caused by the needle should close when the needle is removed.
Pressure should be measured at both ends of a lateral line to determine pressure losses along the line. For most emitters, it is recommended that the pressure variation not exceed 20% (the difference between the highest and the lowest reading) of the design pressure. This also means that deviation from recommended pressure should be no more that 10% throughout the irrigated zone. The exact percentage depends on the type of the emitter used. Some emitters are more sensitive to pressure changes than others. For example, pressure compensating emitter outputs are less sensitive to pressure changes, and are characterized by a constant flow rate at large pressure ranges. The pressure changes in these systems are less critical as long as they are within the range specified by manufacturer.