Introduction
Due to increasing marketing and production risks in specialty crop production, a shift toward more protected culture systems such as a high tunnel production system, could help keep specialty crop farms profitable and sustainable in the United States. High tunnel production systems provide low-cost alternatives to greenhouses, allowing producers to grow crops in a partially controlled and shielded environment. Therefore, high tunnels can prevent crops from some potentially damaging extreme weather conditions (Carey et al. 2009). They also enable producers to extend their production season beyond what is normally possible in open-field production systems (Carey et al. 2009; Miles et al. 2012), often commanding higher prices for products available at early or later points in the season and allowing producers to capture new and expanded markets. In addition, the physical protection provided by high tunnels can help producers to improve crop quality and yield through improved climate, water, disease, and nutrient management (O'Connell et al. 2012).
Despite the benefits of using tunnels for specialty crop production and the availability of financial assistance programs such as the United States Department of Agriculture - Natural Resources Conservation Service (USDA-NRCS) Environmental Quality Incentives Program (EQIP) to aid new tunnel producers, the high tunnel production systems have not been widely adopted by specialty crop producers in Florida. Previous research has shown that the profitability of technological innovations is the primary factor that determines agricultural producers' willingness to adopt them (e.g., Pannel et al. 2006; Rogers 2010). To better promote the high tunnel production systems among specialty crop producers, it is important to understand the cost of constructing high tunnels for crop production and how it is affected by various factors. In this paper, we analyzed the cost of constructing high tunnels and caterpillar tunnels in Florida based on the on-station high tunnel research work and examined the major contributors to their establishment costs. The findings of this paper are intended to assist farmers in deciding whether or not to add high tunnel or caterpillar tunnel systems to their farming operations.
Overview of High Tunnels and Caterpillar Tunnels
High tunnels, also referred to as hoop houses, are plastic-covered, passive solar-heated structures used to modify the growing environment (Carey et al. 2009). Compared to greenhouses, the structure of high tunnels is less expensive to build and operate. Consequently, high tunnels also provide less control of the microclimate. While greenhouses can be covered with glass, polycarbonate panels, or plastic films, high tunnels are usually covered with one or two layers of greenhouse-grade plastic. Also, in contrast to greenhouses that often rely on heaters, fans, and cooling pads to control the temperature inside of the structure, high tunnels are usually passively heated and ventilated through simple adjustments of the plastic sidewalls (Grubinger 2015).
High tunnels usually include three structural elements: (1) the main structure, including steel hoops to be covered by plastic, (2) a passive ventilation system through roll-up side curtains (side walls), and (3) end walls that can be managed for farming operation and crop protection. Figure 1 shows an example of typical high tunnel structural components.
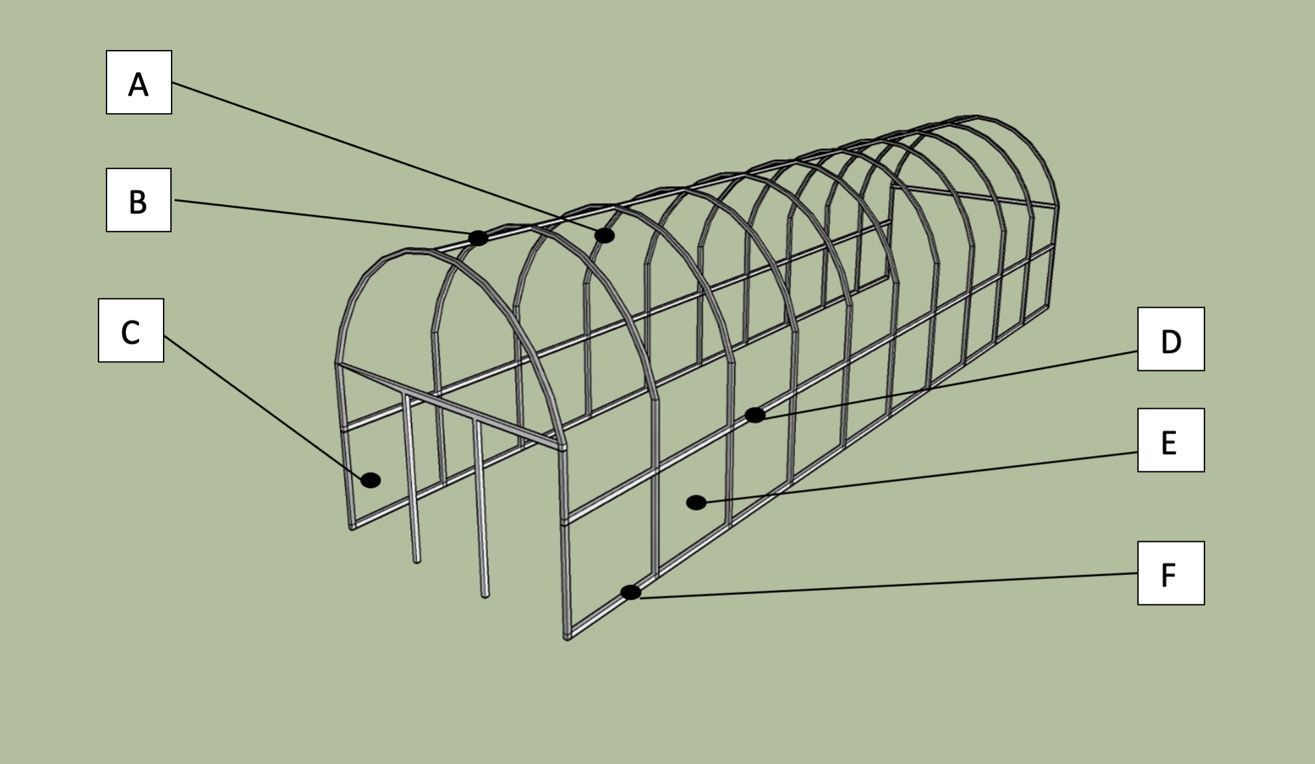
Credit: UF/IFAS
There is no standard size for high tunnels. According to Butler and Bauer (2013), high tunnels usually range from 14 to 28 feet wide, 7 to 12 feet tall at the center, and 48 to 96 feet long, but it is also common to see 30-foot-wide high tunnels. There are three major styles of high tunnels accommodating different crops and environmental conditions (Figure 2).
- Quonset style: It has a rounded steel arch and may not bear heavy snow loads.
- Gothic style: It has a peaked roof that helps shed snow and tends to be taller than the Quonset-style high tunnel to help maintain a more stable temperature during warmer months. It also requires additional bracing to withstand winds.
- Multi-bay style: Typically built side by side to cover more acreage with less exposed surface area. Connecting different spans of arches requires gutters at the roof beams. Because of the large coverage size and sufficient height, it can accommodate tractors and other larger equipment inside the high tunnel.
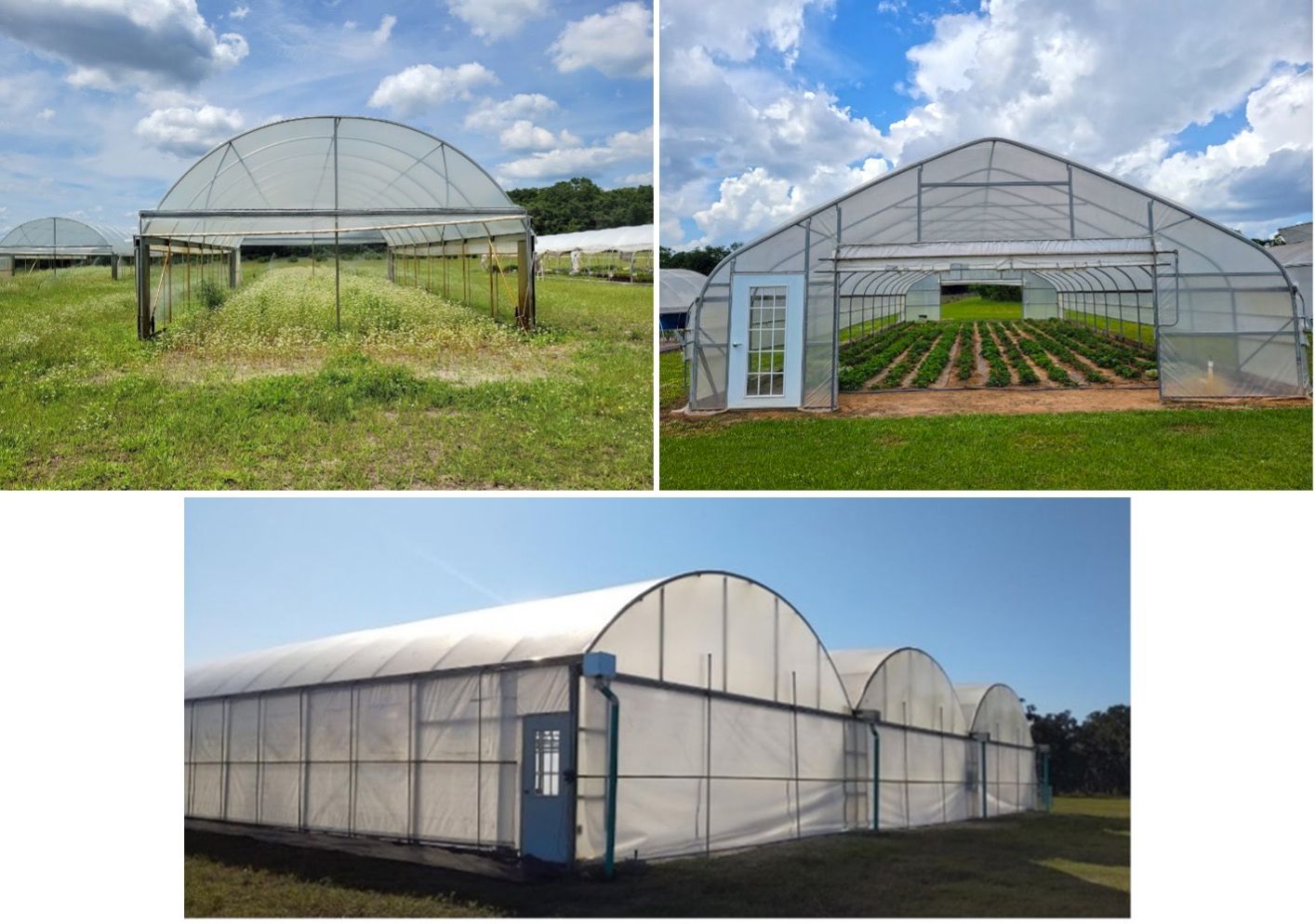
Credit: Xin Zhao, UF/IFAS
Caterpillar tunnels, so named for their resemblance to caterpillars, are inexpensive alternatives to typical high tunnels. Like high tunnels, caterpillar tunnels are structures covered by plastic to create a protected environment for crop production. Unlike high tunnels, caterpillar tunnels do not have built-in end walls and sidewalls. They have cone-shaped ends with extended plastic films that hug the ground at either end.
Since the structure of caterpillar tunnels is usually less stable than that of high tunnels, caterpillar tunnels typically are smaller and are considered temporary/movable. Producers need to manually control the temperature and ventilation by rolling up or removing the plastic covers (Grubinger 2015). Similar to regular high tunnels, there are two common styles of caterpillar tunnels (i.e., Quonset style and Gothic style, Figure 3).
- Quonset style: It has a rounded steel arch.
- Gothic style: It has a peaked roof and requires additional bracing (purlins) to withstand winds.
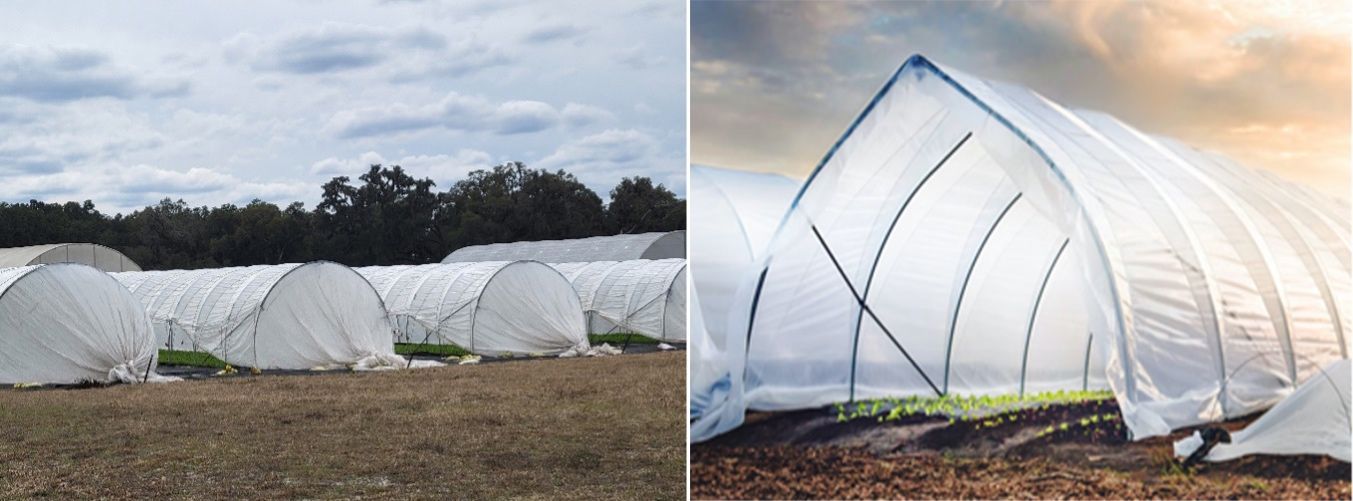
Credit: Left image, Xin Zhao, and right image, Farmers Friend (https://www.farmersfriend.com/caterpillar-tunnel), used with permission
Methods
We estimated the high tunnel establishment cost based on a 3-bay high tunnel installed at the UF/IFAS Plant Science Research and Education Center and the caterpillar tunnel establishment cost based on the data collected from a caterpillar tunnel supplier. The 3-bay high tunnel size is 30 feet × 84 feet for each bay. We analyzed the establishment cost of high tunnels using the invoice we received to build our high tunnels in 2017 from Atlas Greenhouse, a Georgia-based company that supplies high tunnels to Florida. We examined the caterpillar tunnel construction cost using caterpillar tunnel prices collected in 2021 from Farmers Friend, a national caterpillar tunnel supplier that can sell and ship caterpillar tunnel structures to Florida (https://www.farmersfriend.com/caterpillar-tunnel). In addition, an analysis is conducted to investigate how different factors might affect construction costs and to explore potential ways to reduce costs.
Cost Estimates for Constructing High Tunnels and Caterpillar Tunnels
The Estimated Cost of High Tunnels
The estimated total cost of establishing one tunnel (one bay) with the size of 2,520 square feet (30 feet × 84 feet) is $16,929, or $6.72 per square foot if all components of the high tunnel are included. The total cost drops to $15,533/tunnel, or $6.16/square foot, if optional components are removed. Table 1 shows a detailed comparison of the cost to establish a high tunnel using two different options, and Figure 4 breaks down the total establishment cost into the cost of various components of high tunnels.
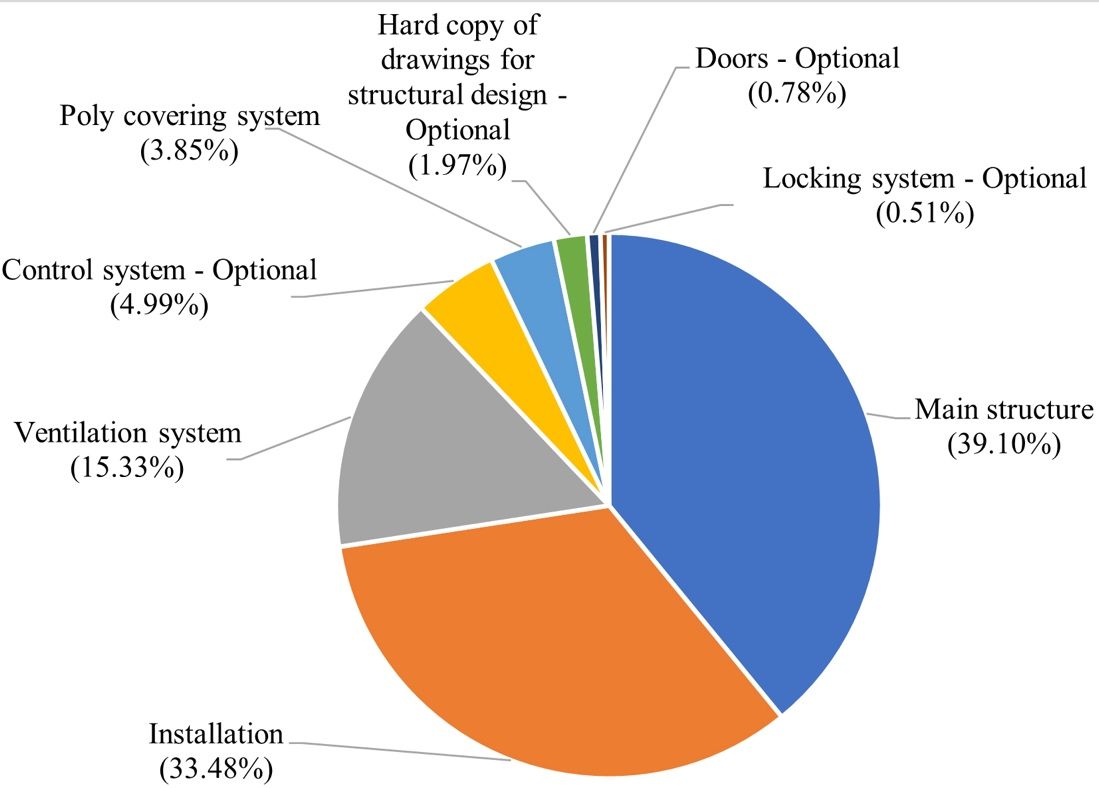
Credit: UF/IFAS
The main structure, including rib, hoop, or arch, is the most expensive part of a high tunnel to build. It costs nearly $6,620/tunnel and accounts for 39.10% of the total construction cost (including both material and labor cost to establish the high tunnel). The second most expensive part is the installation. It accounts for 33.48% of the total construction cost. The third most expensive part is the ventilation system (15.33% of the total construction cost, which is $2,595/tunnel). It involves the installation of an automatic roll-up curtain system (including electric hookups) in high tunnels for ventilation and passive temperature regulation. The control system, which includes wind and rain alarms at each curtain of the high tunnel and the automatic controls to roll up side curtains, is the fourth most expensive part of constructing the high tunnel. It contributes to approximately 5% of the total construction cost ($845/tunnel). The ranks of other parts of the high tunnel in decreasing order of cost are the poly covering system (3.85% of the total construction cost), the hard copy of drawings for structural design (1.97% of the total construction cost), doors (0.78% of the total construction cost), and the locking system (0.51% of the total construction cost). Building a high tunnel that only includes the minimal necessary components (i.e., the main structure, the poly covering system, and the ventilation system) costs $9,866/tunnel for materials and $5,667/tunnel for installation (Table 1).
Table 1. The cost of a high tunnel (30 feet × 84 feet).
Because high tunnels can be used for multiple years of crop production, we estimate the annual depreciation cost of high tunnels in Table 2, which could help producers to calculate the costs and benefits of using high tunnels for their specialty crop production on a year-to-year basis. Column 1 shows the purchase cost of each part of the high tunnel, while column 2 presents the salvage value of each part of the high tunnel. We assume the salvage value of each part of a high tunnel is 10% of its purchase value, following Biship et al. (2010), who estimated high tunnel vegetable production cost in Nevada, and Galinato et al. (2012), who estimated tomato production cost in high tunnels in Washington. To calculate the annual depreciation cost of each component of high tunnels, we use the straight-line annual depreciation method and assume the lifespan of high tunnels for most parts except the poly covering system is 20 years, following the IRS guidelines (IRS 2012). We assume the lifespan of the poly covering system is 4 years, so the maintenance cost of the plastic cover will recur every 4 years for its replacement. At the top section of the table, we calculate the annual depreciation cost of the high tunnel if only the minimal necessary components are included. At the bottom section of the table, we show the annual depreciation cost of high tunnels if building the exact same high tunnel at the UF/IFAS Plant Science Research and Education Unit in Citra, Florida.
Table 2. The annual depreciation cost of a high tunnel with a 20-year lifespan in Florida (30 feet × 84 feet).
Overall, the estimated annual depreciation cost of high tunnels lies in the range of $845/tunnel to $933/tunnel, or between approximately $0.34/square foot and $0.38/square foot per year. The largest portion of the annual depreciation cost comes from the main structure, nearly $298/tunnel per year; followed by the installation (approximately $283/tunnel per year), the poly covering system (approximately $146/tunnel per year), the ventilation system (approximately $117/tunnel per year), the control system (approximately $38/tunnel per year), the doors (approximately $30/tunnel per year), the hard copy of drawings for the structural design (approximately $17/tunnel), and the locking system (approximately $4/tunnel per year).
The estimated cost of caterpillar tunnels
Table 3 shows the estimated establishment cost for caterpillar tunnels. Gothic-style caterpillar tunnels tend to be cheaper than Quonset-style caterpillar tunnels. Establishing a Gothic-style caterpillar tunnel is estimated to cost $2,234/tunnel (1,600 square feet or 16 feet × 100 feet) or $1.39/square foot. When including all possible upgraded options, the estimated cost of establishing a Gothic-style caterpillar tunnel is $4,923/tunnel (or $3.07/square foot). The estimated cost for Quonset-style caterpillar tunnels is in the range of $2,967/tunnel (or $1.85/square foot) and $5,656/tunnel ($3.54/square foot).
Table 3. The cost of a caterpillar tunnel (16 feet × 100 feet).
In terms of different components' contribution to the total establishment cost of the caterpillar tunnel, the main structure is the most expensive part, contributing nearly 50% and 43% of the total establishment cost for Gothic-style caterpillar tunnels and Quonset-style, respectively. The second most expensive component is wind bracing, costing $804. Adding cross bracing in the tunnel costs an additional $585. Increasing bow density costs $296. The labor costs of establishment are small, accounting for less than 2% of the total cost. To estimate the labor cost, we assumed that establishing a caterpillar tunnel (16 feet × 100 feet) usually takes about 10 hours (Shaw 2011; Fraser, 2014). We also calculated the average labor price in Florida as $12.5/hour, based on the labor price for agricultural equipment operators in 2019 and 2020 from the USDA Price Paid Survey (USDA NASS 2022).
Table 4 presents the estimated annual depreciation cost of the caterpillar tunnel. To calculate the annual depreciation cost, we use the straight-line depreciation method and assume the lifespan of caterpillar tunnels is 10 years and their salvage value at the end of 10 years is 10% of their purchase price. The annual depreciation cost of Quonset-style caterpillar tunnels with the size of 1,600 square feet is between $268/tunnel and $420/tunnel per year, while the annual depreciation cost of Gothic-style caterpillar tunnels with the size of 1,600 square feet is between $202/tunnel and $343/tunnel per year.
Table 4. The annual depreciation cost of a caterpillar tunnel with 10 years lifespan in Florida (16 feet × 100 feet)
Conclusions
High tunnels and caterpillar tunnels could increase the sustainability and profitability of specialty crop production. However, constructing a high tunnel requires a significant initial capital investment. The estimated cost of a high tunnel with a size of 2,520 square feet is $16,929 per tunnel ($6.72 per square foot) if building all parts of the tunnel, while it is $15,533 per tunnel ($6.16 per square foot) if only building minimal necessary parts. In contrast, the caterpillar tunnels' initial establishment cost is much lower, ranging from $2,234/tunnel ($1.39/square foot) to $5,656/tunnel ($3.53/square foot) for a tunnel with a size of 1,600 square feet. Hence, caterpillar tunnels are good alternatives to consider for producers who would like to enjoy the benefit of a protected production system but do not want to commit a large investment. In addition, caterpillar tunnels are easy to construct because they require little site preparation and can be constructed almost anywhere on the farm.
Furthermore, the estimated annual depreciation cost of high tunnels ranges from $0.34/square foot to $0.38/square foot. In comparison, the estimated annual depreciation cost of caterpillar tunnels lies in a range between $0.13/square foot and $0.27/square foot. Therefore, caterpillar tunnel systems could be cheaper than high tunnel production systems. However, caterpillar tunnel production systems have limitations too. They have less heavy-duty structures. Therefore, they can be less secure in extreme weather conditions. Moreover, because of their small size, caterpillar tunnels may limit producers' ability to use large machinery in crop production.
It is also worth noting that our estimated cost for high tunnels tends to be high, potentially representing a high cost scenario of establishing high tunnels. For instance, we use an automatic roll-up curtain system with a sensor-based control panel, which is more expensive than a manual roll-up curtain system. In addition, we conducted a survey in 2021 that included 39 Florida producers who used high tunnels. They reported the average cost of their high tunnels is $5.20 per square foot, which is lower than the cost ($6.72 per square foot) of our 3-bay high tunnel at the Plant Science Research and Education Unit in Citra, Florida. However, agricultural producers may face a different cost when building high tunnel structures in their fields. High tunnel costs can vary by type, size, manufacture, and installation date. For example, high tunnel establishment cost significantly increased in the last two years due to high material costs and supply chain issues caused by the COVID-19 pandemic.
Compared to open field production, both high tunnels and caterpillar tunnels require a substantial initial investment to enjoy the potential benefit of a protected production system with a longevity of 10 to 20 years. Many growers may not have the financial ability to afford the cost of establishing these tunnels, despite their willingness to adopt them. Policymakers may develop low-interest or no-interest loan programs and subsidy programs to reduce the financial burden for new high-tunnel adopters. At present, the primary program that provides financial assistance to growers installing high tunnels is the USDA-NRCS EQIP program (USDA NRCS 2022). In addition, using high tunnels in crop production can result in other economic implications for producers, such as property tax (real estate or tangible personal property), the maintenance cost of plastic covers, and electricity cost if electricity is required for any of the automatic controls. Producers need to consider these factors when deciding whether to use protected growing systems in their crop production.
Acknowledgment
This work was supported by the Organic Agriculture Research and Extension Initiative grant no. 2017-51300-26813 from the USDA National Institute of Food and Agriculture.
References
Bishop, C., H. Gatzke, and K. Curtis. 2010. Small Farm Hoop House Production of Vegetables in Desert Climates Costs & Returns. University of Nevada Extension. Available at https://extension.unr.edu/publication.aspx?PubID=2219 Accessed December 5, 2022.
Butler, B., and L. Bauer. 2013. High Tunnel Production: The Basics for Success and Three Case Studies (FS-957). The University of Maryland Extension. Available at https://extension.umd.edu/resource/high-tunnel-production-basics-success-and-three-case-studies-fs-957 Accessed December 30, 2021.
Carey, E. E., L. Jett, W. J. Lamont, T. T. Nennich, M. D. Orzolek, and K. A. Williams. 2009. “Horticultural Crop Production in High Tunnels in the United States: A Snapshot.” HortTechnology 19 (1): 37–43. https://doi.org/10.21273/HORTTECH.19.1.37
Fraser, C. “Caterpillar Madness: Building the Caterpillar Tunnels.” carol cultivates (blog) Available at https://carolcultivates.com/2014/06/caterpillar-madness/, Accessed April 20, 2023.
Galinato, S., C. Miles, S. Ponnaluru. 2012. “2011 Cost Estimates of Producing High-Tunnel Tomatoes in Western Washington (FS090E).” Washington State University Extension. Available at http://ses.wsu.edu/wp-content/uploads/2018/10/FS090E.pdf Accessed December 5, 2022.
Grubinger, V. 2015. “High Tunnels and Other Season Extension Techniques.” SARE Outreach. Available at https://www.sare.org/resources/high-tunnels-and-other-season-extension-techniques Accessed December 30, 2021.
IRS. 2012. Farmer’s Tax Guide. IRS Publication 225. Internal Revenue Service, Washington, D.C. Available at https://www.irs.gov/pub/irs-pdf/p225.pdf Accessed December 30, 2021.
Miles, C., R. Wallace, A. Wszelaki, J. Martin, J. Cowan, T. Walters, and D. Inglis. 2012. “Deterioration of Potentially Biodegradable Alternatives to Black Plastic Mulch in Three Tomato Production Regions.” HortScience 47 (9): 1270–1277. https://doi.org/10.21273/HORTSCI.47.9.1270
USDA NRCS. 2022 High Tunnel Initiative. US Department of Agriculture, Natural Resources Conservation Service. Available at https://www.nrcs.usda.gov/programs-initiatives/eqip-high-tunnel-initiative Accessed December 15, 2022.
O'Connell, S., C. Rivard, M. Peet, C. Harlow, and F. Louws. 2012. “High Tunnel and Field Production of Organic Heirloom Tomatoes: Yield, Fruit Quality, Disease, and Microclimate.” HortScience 47 (9): 1283–1290. https://doi.org/10.21273/HORTSCI.47.9.1283
Pannell, D. J., G. R. Marshall, N. Barr, A. Curtis, F. Vanclay, and R. Wilkinson. 2006. "Understanding and Promoting Adoption of Conservation Practices by Rural Landholders." Animal Production Science 46:1407–1424. https://doi.org/10.1071/EA05037
Rogers, E. M. 2010. Diffusion of innovations. New York, NY: Free Press, A Division of Simon & Schuster, Inc.
Shaw, M. 2011. Experimenting with Caterpillars: Another Option for Season Extension, Cornell Small Farms Program, Available at Experimenting with Caterpillars: Another Option for Season Extension - Cornell Small Farms, Accessed June 30, 2022.
USDA NASS. 2022. Agricultural prices. Available at https://usda.library.cornell.edu/concern/publications/c821gj76b, Accessed December 10, 2022.