Introduction
Poorly maintained equipment is prone to failure. Maintenance and cleaning is even more critical for pesticide application equipment. Not only will spray equipment wear faster if cleaning practices are poor, but the potential for nontarget damage from leftover pesticide residue is also greater. For sensitive crops or herbicides that are active at very low use rates, leftover herbicide can be especially damaging. The purpose of this document is to explain why cleaning spray equipment is important and how to maintain spray equipment hygiene.
Routine Maintenance
Sprayer system components that are susceptible to wear if not properly cleaned include hoses, booms, end-caps, screens, strainers, nozzles/tips, tank, and seals.
Hoses can be difficult to clean for several reasons. Hoses made from certain types of rubber can crack and sequester pesticide residues (Cundiff et al. 2017). Mississippi State University research showed that when applicators leave herbicides overnight in rubber hoses, the herbicide can penetrate and reside in the hoses and ultimately become more difficult to remove (Cundiff et al. 2017). In place of rubber, materials such as PVC or polyethylene blends might be more suitable. Furthermore, hoses that sag/bend between connection points can also accumulate pesticide residues.
Flushing a boom thoroughly can be challenging because once the tank is empty, the pump loses its prime and thus lacks pressure to adequately force out all spray solution. Therefore, the tank must be filled with enough clean water to reprime the pump and force out any remaining spray solution. Always consult the label for any clear directions on total water needed. The amount needed for repriming will vary depending on pump size; be sure to know how much it will take ahead of time. Wet boom end caps that have not been removed and cleaned can also build up herbicide residues.
Screens and strainers filter various debris, but dry formulations that have not been adequately agitated often become trapped (Figure 1). Always remove the screens and strainers, inspect them for debris accumulation, and clean if necessary. Checking these after each use is best, and many manufacturers will suggest replacement if output is off by more than 10% from the calibrated output. Similarly, poor sprayer hygiene can result in clogged nozzles if residue sits in the system after use. This ultimately leads to changes in spray/boom pressure, nozzle spray pattern, output, and pesticide performance.
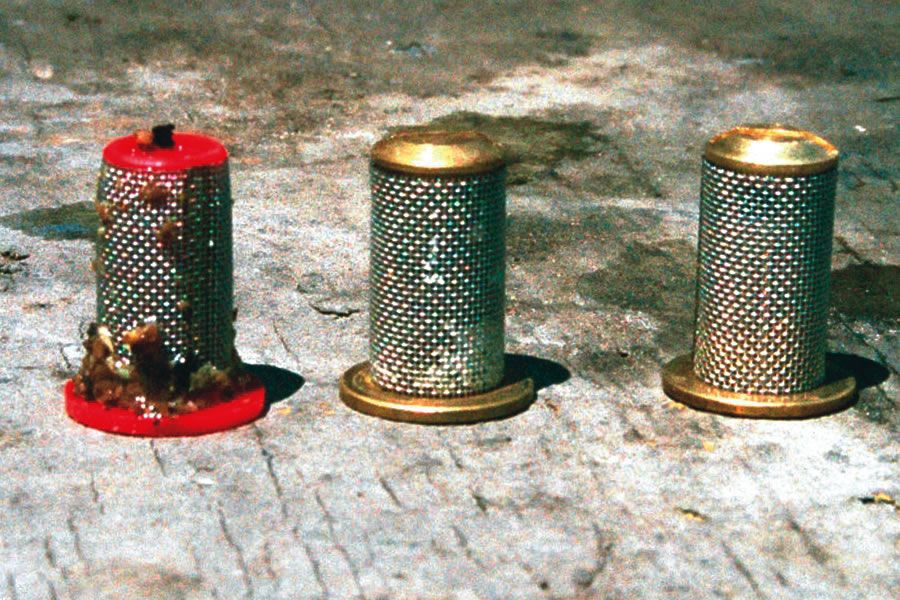
Credit: UF/IFAS Pesticide Information Office
Spray tank design can also influence the amount of residue remaining after use. Ideally, the tank should have a sloped bottom surface with the drain opening slightly above the sump. Therefore, it is difficult to completely drain most spray tanks because some solution will always remain in the “keel” of the tank. Keel volumes range from ounces to tens of gallons depending on the size and configuration of the tank. Diluting this volume is the key to successfully cleaning a sprayer. Furthermore, if the tank contains baffles, residue can accumulate at bases of baffles. The interior surface of the tank is another site of residue collection. Consequently, several commercially available tank-cleaning nozzles that provide 360° coverage of the interior tank surface can be used to rinse these residues.
Cross Contamination
Cross contamination occurs when you spray one crop and then spray another without proper cleanout. This can result in nontarget damage, particularly to sensitive crops. Many crop species are highly sensitive to certain herbicides at very low rates. Even when there are only small amounts of herbicides left in the spray system, significant crop injury can occur.
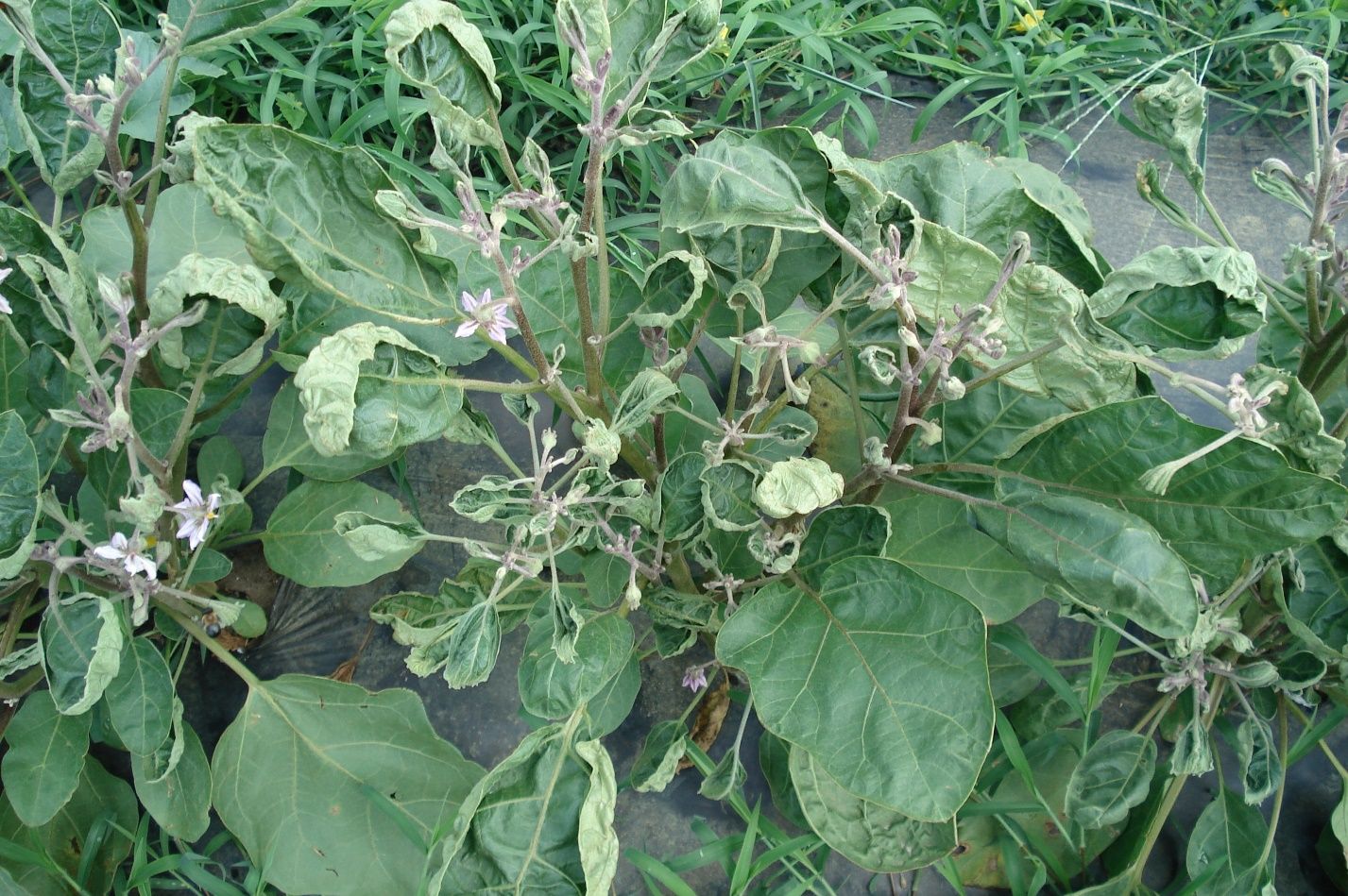
Credit: Dr. Jason Ferrell, UF/IFAS
Because of the extreme sensitivities of certain crops to synthetic auxin herbicides (e.g., 2,4-D, dicamba, triclopyr, etc.), extra care must be taken to clean spray equipment after an auxin herbicide application. This problem has become so prevalent that some growers have even gone so far as to use a dedicated sprayer for auxin herbicide use. In this scenario, sensitive crops would be sprayed with a different sprayer that has never been used for auxin herbicide applications. Managers must be aware of proper sprayer hygiene and sensitivity of all the crops they produce.
How to Properly Clean a Spray System
Sprayer cleaning products perform three basic functions: deactivating the herbicide molecule, increasing the herbicide’s solubility so it can be more easily flushed, and removing any residues that may have penetrated the walls of hoses, tanks, or fittings.
These are general guidelines, but always consult the product label for specific cleaning information. This is especially important for products that will be used on herbicide-tolerant crops.
- Completely spray out mixture from the sprayer immediately after spraying. Do not allow spray mixture to sit overnight.
- Fill sprayer with enough clean water to flush all hoses, booms, and nozzles. Remove end caps of boom (if equipped) where residues can accumulate.
- Inspect and clean all strainers, filters, nozzles, and screens for residue.
- Precisely follow the directions for the tank cleaning agent or the procedures listed on the herbicide product label. Ensure that all surface areas of the tank are washed with cleaning solution.
- Agitate the mixture and recirculate for at least 15 minutes. Charge all pumps, hoses, and nozzles by spraying a small amount of solution through the sprayer; ensure the solution is spraying out of the nozzles.
- Shut off the sprayer, keeping the hoses and nozzles charged.
- Remove and clean all nozzles, screens, and strainers with tank cleaning solution. Drain pump, filters, and lines.
- Completely wash and rinse the outside of the sprayer.
- Refill the tank with clean water and empty. Check all strainers, filters, nozzles, and screens, because this process can free residue from the sprayer.
- Appropriately dispose of all rinsate in compliance with local, state, and federal requirements.
At a minimum, unless otherwise specified by the label, it is best to empty the sprayer and run clean water through at the end of each use. It is always advisable to do a more thorough cleaning anytime you move from one crop to another.
Conclusion
Maintaining equipment is the simplest way to ensure it will perform properly over a sustained period. When working with pesticides it is doubly important, not just for maintaining good working order, but ensuring no cross contamination and avoiding nontarget (sensitive crop species) damage. Many labels will give specific cleanout instructions, so ALWAYS read the entire label. Even when labels don’t specify cleanout procedures, DO NOT let pesticide sit in a spray system overnight. Maintaining your sprayer system is an easy way to ensure it will work properly and make you more effective in your pesticide applications.
Reference
Cundiff, G. T., D. B. Reynolds, and T. C. Mueller. 2017. “Evaluation of Dicamba Persistence among Various Agricultural Hose Types and Cleanout Procedures Using Soybean (Glycine max) as a Bio-indicator.” Weed Science 65 (2): 305–16. https://doi.org/10.1017/wsc.2016.29