Introduction
This publication provides research-based information and analysis for citrus growers who are considering establishing a satsuma grove in north Florida. Its purpose is to serve as a reference and model for growers to create their own enterprise budgets and make financial projections. An enterprise budget estimates revenues, costs, and net returns for a particular crop or farm enterprise to help growers assess the economic viability and risk of an enterprise, compare enterprises, and evaluate production or marketing changes. The budget and financial analysis may assist prospective and current satsuma growers, agricultural consultants, and lenders with planning and decision making. This publication provides a description of the satsuma mandarin, and information about madarin markets, production costs, and potential returns.
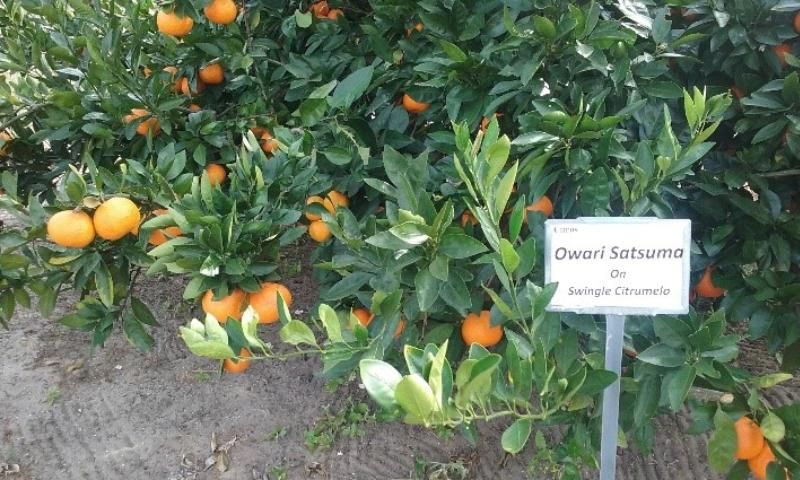
Crop Description
The satsuma mandarin (Citrus unshiu Marcovitch) is a cold-hardy citrus species that has been grown in north Florida since the 1800s. It can tolerate freezing temperatures when cold-acclimated and grafted on trifoliate rootstocks. Although mature dormant trees have survived temperatures as low as 14°F, satsuma trees need cold protection during hard freezes when they are actively growing (Andersen and Brodbeck 2015; Andersen and Ferguson 2015; Andersen et al. 2016).
The satsuma mandarin currently has few major pests in north Florida, but is susceptible to citrus scab and citrus leaf miner. Huanglongbing (HLB; citrus greening) is the most devastating citrus disease worldwide and is impacting groves in south and central Florida. HLB has been detected in some north Florida counties (mostly residential/dooryard trees) and has the potential to severely impact commercial groves in north Florida as it has in other parts of the state (FDACS, personal communication). Otherwise, satsuma is considered a relatively sustainable crop for north Florida (Andersen and Ferguson 2015; Andersen et al. 2016).
More than 100 different satsuma cultivars have been developed. Owari is the primary satsuma cultivar grown commercially in Florida (Andersen and Ferguson 2015).
Markets
Mandarins and other specialty citrus such as tangerines, clementines, and tangelos have strong demand in national markets. The production of tangerines and mandarins nationwide increased 40%, from 16.48 million boxes (1.37 billion pounds) in 2012/13 to 23.12 million boxes (1.87 billion pounds) in 2015/16 (Perez and Plattner 2015; Ferreira and Perez 2017). Another 6% increase is forecast for 2016/17 nationwide. About 93% of the domestic supply of tangerines and mandarins comes from California (Ferreira and Perez 2017). Average on-tree prices received by US growers for fresh tangerines and mandarins in recent years during the months of November and December have ranged from $21.99 per box (about $0.27 per pound) to $34.53 per box (about $0.43 per pound) (Ferreira and Perez 2016).
In Florida, the average on-tree price received by growers for tangerines in 2014/15 was $17.50 per box (about $0.18 per pound), with 69% of production sold fresh (on-tree price of $24.15 per box, or $0.25 per pound) and 31% of production processed (on-tree price of $2.99 per box, or $0.03 per pound) (FDACS 2016). For 2015, USDA-NASS (2016a) reported an average packinghouse door (PHD) price of $27.40 per box ($0.29 per pound) for fresh market tangerines delivered to Florida packinghouses. The average PHD price for tangerines going to processing was $7.19 per box ($0.08 per pound).
Satsumas are a seedless mandarin (seedless citrus can contain up to 6 seeds, but usually no seeds are present) with a loose, easy-to-peel rind and good eating quality. Satsumas do not ship as well as most other citrus, which may limit their distribution through national produce channels. Local and regional markets (direct marketing, or shortened, intermediated channels) may be more promising for Florida satsuma growers, especially those with relatively small volumes. Local, direct markets offer potential for higher prices, but may entail greater marketing costs. Possibilities include farmers' markets, on-farm stores, roadside stands, farm-to-school, gift fruit, and direct sales to retailers. At retail, satsuma prices typically range from $1.00 to $2.00 per pound for 3-lb or 5-lb bags (USDA-AMS 2017).
A marketing plan is important for guiding grove planning, including choice of varieties and plans for harvesting and packing. Sound estimates of selling prices and costs of getting fruit to market are important for assessing financial viability. The budget described in this document includes picking and hauling costs, but does not include packing cost. A grower would need to determine whether a packinghouse within reasonable distance would purchase or custom-pack satsumas at an acceptable price. Another option would be for growers to build their own packinghouses. A well-researched marketing plan and consideration of harvesting labor availability are essential for business planning.
Budget and Profitability Analysis
Overview
The grove budget (Tables 1–8) provides estimated costs to establish and produce satsuma mandarins in north Florida and expected returns over a 30-year period. The budget represents a hypothetical owner-managed farm in north Florida with 10 acres of satsuma mandarin trees. The grove has 145 trees per acre (15' x 20' or 12' x 25' spacing) and a microsprinkler irrigation system that also can be used for freeze protection.
The estimates in this budget are based on information from university trials and crop specialists, equipment and input suppliers, farmers, and other industry sources. This sample budget does not represent any one particular farm, but represents the authors' judgement, based on the information compiled, of what could reasonably be expected for a newly established satsuma grove in north Florida. The potential variability in many of the estimates adds uncertainty and risk. Actual costs and returns for establishing a satsuma grove and producing satsuma mandarins will vary according to a farm's specific circumstances, grower choices, growing conditions, and market opportunities. Prospective and current satsuma growers are encouraged to create their own budgets and to consider the variability and risk that are inherent in agriculture.
Budget information and profitability analyses are presented in Tables 1–8. Table 1 summarizes costs and returns for a mature bearing grove (years 9-30) and includes an annual noncash allocation to recoup the costs incurred for grove establishment (years 1-8). Table 2 shows estimated yield and revenue per acre by grove year, along with harvesting and marketing costs based on the yield quantity. Table 3 provides detail on fixed overhead costs, including infrastructure, facilities, equipment, and general farm overhead. Table 4 lists the labor rates, energy rates, and equipment operating costs used in the budget. Table 5 shows annual grove-care operating costs per acre. Table 6 accumulates grove establishment costs over years 1–8 in order to estimate an appropriate capital recovery charge. Table 7 shows annual cash flow for a 30-year investment analysis. Table 8 contains breakeven and sensitivity analyses.
Budget Summary
Table 1 shows an annual budget summary for a mature bearing grove (years 9–30). Potential annual revenue is estimated at $14,899 per acre. Actual revenue will depend on fruit yields, packout rates, and prices. Annual operating costs are estimated at $2,163 per acre for grove care plus $5,596 per acre for custom harvesting, roadsiding, and hauling to a packinghouse ($7,758 per acre for total annual operating costs).
Annual fixed costs include general farm overhead, fixed production overhead, a land charge, and grove establishment capital recovery. Cash costs represent actual expenditures in a given year. Noncash costs represent capital recovery (depreciation and interest) on fixed assets purchased in previous years or opportunity costs associated with forgoing land rental or interest earnings. General farm overhead and fixed production overhead are estimated at $800 per acre and $1,297 per acre, respectively (cash + noncash). A land charge, reflecting rental opportunity cost for irrigated cropland in north Florida (USDA-NASS 2016b), adds $164 per acre in noncash costs. The costs of establishing and managing the grove over the first eight years are amortized over the remaining years, adding a noncash capital recovery charge of $1,292.
Annual net return over operating costs is estimated at $7,140 per acre. Considering cash costs only (both operating and fixed), the annual net return is estimated at $6,274 per acre. Annual net return over total costs (including cash, noncash, operating, and fixed costs) is estimated at $3,587 per acre. Although the net return over total costs accounts for the opportunity cost of land and capital, it does not include a charge for overall management of the farm. Therefore, the net return over total costs should be interpreted as net return to management and economic profit.
Fruit Yield, Price, and Revenue
Table 2 shows estimated yield and revenue by grove year. Fruit yield per acre depends on tree age and variety, number of trees per acre, grove care, and growing conditions (e.g., pest and disease pressure, rainfall, freeze events). The annual tree replacement rate will affect the age composition of the grove, thus affecting yield per acre. We assume an annual replacement rate of three trees per acre, which is at the low end of the range for south Florida citrus groves (Muraro 2012; Zekri 2015), but more in line with reports by north Florida growers. This budget assumes satsumas are first harvested in year 4, although some growers may start harvesting for market in year 3. Yield is expected to increase each year until year 9. Yield estimates for years 4–8 are based on satsuma yields at the UF/IFAS North Florida Research and Education Center and the UF/IFAS Suwannee Valley Agricultural Extension Center. Although yields will fluctuate from year to year, we assume a constant average yield for years 9–30. The estimated yield per tree for 9-year-old to-30-year-old trees (365 pounds per year) is based on year 9 and year 10 yields obtained from Brown Select and Owari satsumas on P. trifoliate 'Rubidoux' rootstock at the UF/IFAS North Florida Research and Education Center (Andersen and Brodbeck 2015). Annual yield per acre is estimated at 46,631 pounds for a mature, nine-year-old grove.
Revenue from fruit sales depends on the amount of fruit that can be sold to different markets (depending partly on fruit quality) and the price received from each market. Fruit quality may be lower in the first few years of harvest but improve as the trees mature (Fake et al. 2008). This budget assumes that 40% of fruit harvested in year 4 is sold as #1 quality to the fresh market, increasing to 65% by year 9. We assume that about half the remaining harvested fruit can be sold at a lower price as #2 fruit. Some of the harvested fruit are unmarketable culls. Estimated packinghouse door (PHD) prices of $0.45 per pound for #1 fresh fruit and $0.15 per pound for #2 fresh fruit are used in this budget. These estimates are based on a combination of grower feedback and USDA price data. Markets for satsumas in north Florida are not well established. Price expectations are uncertain and will depend on market trends.
We assume the grower pays $0.12 per pound for custom harvesting, roadsiding, and hauling to a packinghouse. That estimate is higher than harvesting costs reported for south and central Florida (Singerman 2015), but communications with growers suggest that $0.12 per pound is more in line with north Florida rates. Because those costs are based on harvested yield, they are shown in Table 2. Annual sales revenue of $14,899 per acre minus harvesting and marketing costs of $5,596 results in an on-tree revenue of $9,303 per acre.
Initial Investment and Fixed Costs
Table 3 lists costs for infrastructure, facilities, equipment, and durable supplies to support production of satsuma mandarins. Infrastructure and facility costs include land preparation, electric hookup, fuel tank, equipment shed, and two wells. Equipment and durable supplies include well pumps and irrigation system, backup generator, utility vehicle, a tractor, and various implements. Initial investment cost for production overhead is estimated at $180,300 for the 10-acre grove ($18,030 per acre).
The cost of purchasing land for the satsuma grove is not included in the budget (it is assumed the grower already owns the land). A new grower should consider that, besides the 10 acres for the satsuma grove, additional space may be needed for buildings, roads, and other infrastructure. Fencing or other wildlife deterrents may be necessary for some growers, but is not included in this budget.
An 8-inch well and 50-horsepower electric pump with variable frequency drive are expected to provide irrigation capacity of at least 500 gallons per minute. Although that flow rate is not necessary for routine irrigation, especially if the grove is divided into zones, 2000 to 3000 gallons per acre per hour (333 to 500 gallons per minute for a 10-acre grove) is recommended for freeze protection (Parsons and Boman 2003). A diesel generator with sufficient capacity to power the 50-horsepower pump and variable frequency drive is included to ensure the irrigation system can run during an electric power outage. Growers may want to consider other options for powering the irrigation system (such as diesel-powered or propane-powered pumping systems). A second 4-inch well is included for a wash station and other general needs. Microsprinkler irrigation is common for citrus groves in Florida (Parsons and Morgan 2003).
Annual ownership cost is estimated for each of the fixed production assets listed in Table 3. The annual ownership cost includes capital recovery (depreciation plus interest), insurance, taxes, fees, and fixed repair costs (independent of use). Capital recovery is considered a noncash cost, whereas insurance, taxes, fees, and fixed repairs are annual cash costs. A real interest rate of 3.65% is used for the analysis (based on a rate quote from an agricultural lender minus the 3-year average inflation rate from the 2013–2015 consumer price index, CPI). Annual noncash ownership cost is estimated at $1,080 per acre, and cash ownership cost is estimated at $217 per acre.
Table 3 also includes general farm overhead, which are costs associated with running a farm business that are not directly associated with satsuma production. These include annual noncash and cash costs estimated at $150 per acre and $650 per acre, respectively.
Operating Rates
Table 4 shows rates for labor, energy, and equipment operating costs. Workers' wage estimates of $11.50 per hour for general agricultural labor and $12.00 per hour for agricultural machine or spray labor are based on 2015 mean wages reported by the Florida Department of Economic Opportunity (FDEO 2016). An additional 41% is estimated for payroll overhead, or employers' share of payroll taxes, workers' compensation insurance, and other possible benefits (O'Connell et al. 2015). Energy rates are estimated from values published by the US Energy Information Administration, the American Petroleum Institute, and local electric utilities.
Equipment operating costs include fuel and lubrication costs, electricity to run equipment, and repairs associated with use. These costs are proportional to the amount of use and are estimated using formulas and parameters provided by agricultural engineering studies (ASABE 2015a, b; Frazier undated). Annual equipment operating costs for a mature 10-acre grove are estimated at $987 for fuel and lubricants, $1,693 for electricity, and $1,540 for equipment repairs. That amounts to $4,220 for the 10-acre grove, or $422 per acre.
Grove-Care Operating Costs
Grove-care operating costs vary with the age of the trees, as well as input prices, growing conditions, and management practices and intensity. Table 5 groups operating costs by activity and by age of the grove. Costs are further broken down by type (labor, equipment, materials, custom). Major grove-care activities include tree planting and replacement, fertilization and soil amendment, weed management, insect/disease management, scouting, pruning, irrigation, and freeze protection.
The grove must be maintained for three years (non-bearing establishment years) before it becomes economical to harvest. Years 4–8 are considered young-bearing years, and years 9 and up are considered mature-bearing years. The budget estimates grove-care operating costs of $3,198 in year 1 (including initial tree planting); $1,445 in Year 2; and $1,500 in Year 3. Average grove-care operating costs are estimated at $1,830 during the young-bearing years and $2,163 during the mature-bearing years.
Monthly interest on operating capital is added to the grove-care costs for mature-bearing years. That assumes a 0.75% interest rate, compounded monthly over a 10-month period, applied to annual grove-care costs. A monthly interest charge is not applied to years 1–8, but an annual interest charge is applied to those years as part of capitalizing grove establishment costs.
Grove Establishment Cost Accumulation
Table 6 accumulates all costs in years 1–8. Those costs include fixed overhead costs, grove-care operating costs, and harvesting and marketing costs. To fully capture all costs in an annual budget for a mature-bearing grove, capital recovery for the establishment years must be included. To accurately estimate capital recovery costs, the time value of money must be considered. Interest opportunity cost, which depends on the interest rate, the annual cash cost, and the number of years it will take the grove to mature, must be built into the analysis. A real interest rate of 3.65% is used for the accumulation of cash costs (based on a rate quote from an agricultural lender minus the 3-year average inflation rate from the 2013–2015 CPI). Annual noncash costs that already include an interest charge are also accumulated but are not charged interest in this accumulation table. To recover grove establishment costs from years 1–8, an annual charge of $1,292 should be applied to the satsuma budget for years 9–30 (reflected in the Table 1 Budget Summary).
Investment Analysis
Table 7 shows a 30-year investment analysis for grove establishment and production of satsuma mandarins. Establishing a satsuma grove is a capital investment with potential returns spread over many years in the future. An investment analysis is used to assess the profitability of an enterprise when costs and returns are spread unevenly over time and to compare rates of return with other investment opportunities. Investment analysis accounts for both the size and timing of cash flows (Kay and Edwards 1999).
This investment analysis provides three metrics: payback period, net present value, and internal rate of return. The payback period is the number of years it takes to accumulate net cash revenues equal to the initial investment cost. Net present value is the sum of discounted net cash flows over the life of the investment (or other multi-year period), minus the initial cost of the investment. Future cash flows are "discounted" to a present value to reflect the time value of money and opportunity cost of capital. A positive net present value indicates that the return on investment is greater than a standard alternative or the cost of capital, reflected by the discount rate. The internal rate of return is the actual rate of return, which is the same as the discount rate that would make the net present value equal zero (Kay and Edwards 1999).
Estimated future costs and returns shown in this analysis do not reflect an overall inflation rate, so a real discount rate (3.65%) is used for the analysis. Cash costs include the initial purchase of infrastructure, facilities, equipment, and durable supplies; annual grove-care operating costs; annual harvesting and marketing costs; annual fixed cash costs; and the periodic replacement of equipment with lifespans less than 30 years. Cash revenues are based on expected sales of satsuma mandarins. The results of the investment analysis for the 10-acre grove show an expected payback period of 12 years, an internal rate of return of 10%, and a net present value of $443,588.
Although this return on investment is favorable, it does not account for any production risks (e.g., pests and diseases) involved with maintaining a citrus grove over a 30-year period. The returns shown in the analysis can be interpreted as potential returns that could be expected if the grower is able to maintain a healthy, productive grove over the 30-year period.
Breakeven and Sensitivity Analysis
Table 8 shows breakeven and sensitivity analyses. Harvest yield and selling price are two sources of uncertainty in a farming operation. A breakeven yield calculation estimates the harvest yield needed to break even (at which revenue just covers costs), given the assumed selling price and costs shown in the budget. A breakeven price calculation estimates the selling price needed to break even, given the assumed yield and costs shown in the budget. The analysis in Table 8 shows the breakeven yield at five different average prices throughout the 30-year period and the breakeven price at five different yields. Estimates are shown for annual breakeven on total costs for a mature grove and for 30-year breakeven, at which the net present value equals zero. Thirty-year breakeven (NPV=0) values are slightly lower because the investment analysis does not include the noncash land charge (opportunity cost) or the noncash component of general farm overhead.
Annual breakeven yields on total costs for a mature grove range from 17,321 pounds at an average price of $0.45 per pound to 81,657 pounds at a price of $0.19 per pound. Annual breakeven prices on total costs for a mature grove range from $0.21 per pound at a yield of 65,283 pounds to $0.32 pound at a yield of 27,979 pounds per acre.
The sensitivity analysis shows the annual net return over total costs per acre for a mature grove. Annual net returns range from –$3757 (negative) to $15,828 (positive) for 40% variations above and below expected price and yield. The range of net returns demonstrates the importance of marketing and average selling price. At an average selling price of $0.45 per pound, a satsuma grove can be profitable even with relatively low yields. However, at an average selling price of $0.19 per pound, no realistic yield could achieve a positive profit. Average price is related to fruit quality and the amount of culled fruit. Even if high-quality fruit can be sold for $0.50 per pound, a 50% cull rate from the harvested yield results in an average selling price of only $0.25 per pound.
These potential variations reflect some degree of market risk (price variation) and production risk (yield variation). This analysis does not consider cost risk, legal risk, or other types of risk. Nor does it consider the possibility of catastrophic loss from a weather event (e.g., hard freeze) or severe disease outbreak (e.g., HLB). Disease and pest pressures create significant risk for satsuma growers. HLB has caused substantial losses to groves in south and central Florida. How quickly and to what extent HLB could affect groves in north Florida is still uncertain. Diversification and enrollment in crop insurance can reduce risk.
Conclusions
The satsuma mandarin has potential to be a profitable crop in north Florida. Although grove establishment represents a sizable investment, returns are favorable based on the costs, yields, and prices assumed in this budget. The analysis assumes the grove will be productive for at least 30 years. With an estimated payback period of 12 years, the grove would need to maintain production for longer than that to achieve a positive return.
Returns depend critically on satsuma prices and packout rates. Citrus packing and processing options in north Florida are limited, and distribution channels are not well established. Returns could be higher or lower than shown in this budget depending on market development. Labor availability and harvesting costs are additional sources of uncertainty for north Florida growers. The possibility of severe freeze events and disease outbreaks represent threats to the profitability of satsuma production in north Florida.
Growers may use this budget as a starting point for their own budgeting and analysis. Actual costs and returns will vary according to each grower's situation and uncertain future circumstances.
Acknowledgments
We gratefully acknowledge funding from a Specialty Crop Block Grant (USDA and FDACS) that supported the initial work on this document. Also, we would like to thank the growers, agricultural input suppliers, and other industry professionals who contributed information that improved this budget. In particular we would like to thank Andy Jackson, Kim Jones, Alicia and Mack Glass, and Travis Murphy for their helpful input.
References
American Society of Agricultural and Biological Engineers (ASABE). 2015a. Agricultural Machinery Management. Publication ASAE EP496.3 FEB2006 (R2015). St. Joseph, MI: ASABE.
American Society of Agricultural and Biological Engineers (ASABE). 2015b. Agricultural Machinery Management Data. Publication ASAE D497.7 MAR2011 (R2015). St. Joseph, MI: ASABE.
Andersen, P.C., K.R. Athearn, M.A. Olmstead, and J.G. Williamson. 2016. Sustainability Assessment of Fruit and Nut Crops in North Florida and North Central Florida. HS765. Gainesville, FL: University of Florida Institute of Food and Agricultural Sciences.
Andersen, P.C., and B.V. Brodbeck. 2015. "Yield, Tree Size, and Fruit Quality of Mature 'Owari' and 'Brown Select' Satsuma on Poncirus trifoliata 'Rubidoux' and 'Flying Dragon' Rootstocks in North Florida." HortScience 50(11):1-4.
Andersen, P.C., and J.J. Ferguson. 2015. The Satsuma Mandarin. HS195. Gainesville, FL: University of Florida Institute of Food and Agricultural Sciences.
Fake, C., K.M. Klonsky, and R.L. De Moura. 2008. Sample Costs to Establish a Mandarin Orchard and Produce Mandarins. Davis, CA: University of California Cooperative Extension.
Ferreira, G., and A. Perez. 2016. Fruit and Tree Nuts Outlook. USDA-ERS Report FTS-361. Washington, DC: USDA-ERS.
Ferreira, G., and A. Perez. 2017. Fruit and Tree Nuts Outlook. USDA-ERS Report FTS-364. Washington, DC: USDA-ERS.
Florida Department of Agriculture and Consumer Services (FDACS). 2016. Florida Citrus Statistics 2014-2015. Tallahassee, FL: FDACS.
Florida Department of Economic Opportunity (FDEO). 2016. Occupational Employment Statistics and Wages. Tallahassee, FL: FDEO. http://www.floridajobs.org.
Frazier, R.S. Undated. Comparative Energy Costs for Irrigation Pumping. BAE-1204. Stillwater, OK: Oklahoma Cooperative Extension Service.
Kay, R.D., and W.M. Edwards. 1999. Farm Management, Fourth Edition. New York: WCB McGraw-Hill.
Muraro, R.P. 2012. Summary of 2011-2012 Citrus Budget for the Southwest Florida Production Region. Lake Alfred, FL: UF/IFAS Extension.
O'Connell, N.V., C.E. Kallsen, K.M. Klonsky, and K.P. Tumber. 2015. Sample Costs to Establish an Orange Orchard and Produce Oranges. Davis, CA: University of California Cooperative Extension.
Parsons, L.R., and B.J. Boman. 2003. Microsprinkler Irrigation for Cold Protection of Florida Citrus. HS931. Gainesville, FL: University of Florida Institute of Food and Agricultural Sciences.
Parsons, L.R., and K.T. Morgan. 2003. Management of Microsprinkler Systems for Florida Citrus. HS958. Gainesville, FL: University of Florida Institute of Food and Agricultural Sciences.
Perez, A., and K. Plattner. 2015. Fruit and Tree Nuts Outlook. USDA-ERS Report FTS-358. Washington, DC: USDA-ERS.
Singerman, A. 2015. 2014/15 Picking, Roadsiding, and Hauling Charges for Florida Citrus. FE977. Gainesville, FL: University of Florida Institute of Food and Agricultural Sciences.
United States Department of Agriculture, Agricultural Marketing Service (USDA-AMS). 2017. Weekly Advertised Fruit & Vegetables Retail Prices. Washington, DC: USDA-AMS.
United States Department of Agriculture, National Agricultural Statistics Service (USDA-NASS). 2016a. 2015 State Agriculture Overview for Florida. Washington, DC: USDA-NASS.
United States Department of Agriculture, National Agricultural Statistics Service (USDA-NASS. 2016b. Quick Stats Database. Washington, DC: USDA-NASS.
Zekri, M. 2015. Resetting in Citrus Groves. HS1266. Gainesville, FL: University of Florida Institute of Food and Agricultural Sciences.