Female flowers of hops (Humulus lupulus L.), referred to as cones or strobuli, are used as an essential ingredient of beer to impart bitterness and aroma. In commercial production, hops are grown on a tall trellis, which is typically 18 to 20 ft above the ground. This article explains hop harvesting procedures for small-scale production (generally up to 5 acres). It is part of a series that examines the challenges and opportunities for hop production in Florida based on research at the UF/IFAS Gulf Coast Research and Education Center (GCREC). Corresponding tutorial videos are available at https://youtube.com/playlist?list=PL4qrjj3jZ6i5BwgylgUcb6fMI0z9FKCkQ. Additional videos on hop production and management are also available at the UF IFAS Horticultural Crop Physiology Lab YouTube channel (https://www.youtube.com/channel/UCMyYAfFZsib6d4ZI-eaxCTQ). The intended audience for this article includes growers, certified crop advisors, crop consultants, and county Extension faculty.
Phenology of Hops Grown in Florida
Hops are known as short-day plants because they flower when daylength becomes shorter than a specific number of hours, referred to as critical daylength (Thomas 1969). In general, the critical daylength for hops is 15 to 16 hours (Krebs 2019; Neve 1991), although it varies among cultivars (Thomas 1969). In low-latitude regions (<35° north or south of the equator), inadequate daylength induces hops to flower prematurely, resulting in poor vegetative growth and cone yields. Florida’s latitude is between 24° and 31°N. Therefore, flowering control using supplemental lighting is an important management practice to grow hops successfully in Florida (Agehara 2020).
Florida’s subtropical climate, along with flowering control using supplemental lighting, enable double-season production of hops (Agehara et al. 2021). Spring and fall growing seasons for ‘Cascade’ hops run from February to June and June to November, respectively. Plants go dormant in late December. The video describing spring and fall growth cycles of hops in Florida is available at https://youtu.be/_rAnXr3cQrs.
Determining the Optimum Time to Harvest
Hop cones produce small yellow substances called lupulin glands as they mature (Figure 1). Because bitterness and aroma of beer derive from acids and essential oils contained in lupulin glands, it is critical to harvest cones at the optimum maturity stage. The most accurate method to determine the optimum harvest timing is having cones analyzed in a laboratory. In general, ripe cones should have a moisture content between 75% and 80% (Mabie 2021) and a hop storage index below 0.30 (Nickerson and Likens 1979). In ‘Cascade’, the normal range of alpha acids is 4.5% to 7% (Hop Growers of America 2017). The ripeness of cones can also be inspected visually in the field. If cones feel soft or damp, they are still immature. Ripe cones should look bright green with some browning on tips, and they should feel dry and papery. Lupulin glands inside the cones should be obvious, bright yellow, and aromatic. The tutorial video for determining the optimum harvest timing is available at https://youtu.be/U6i8rh65jyU.
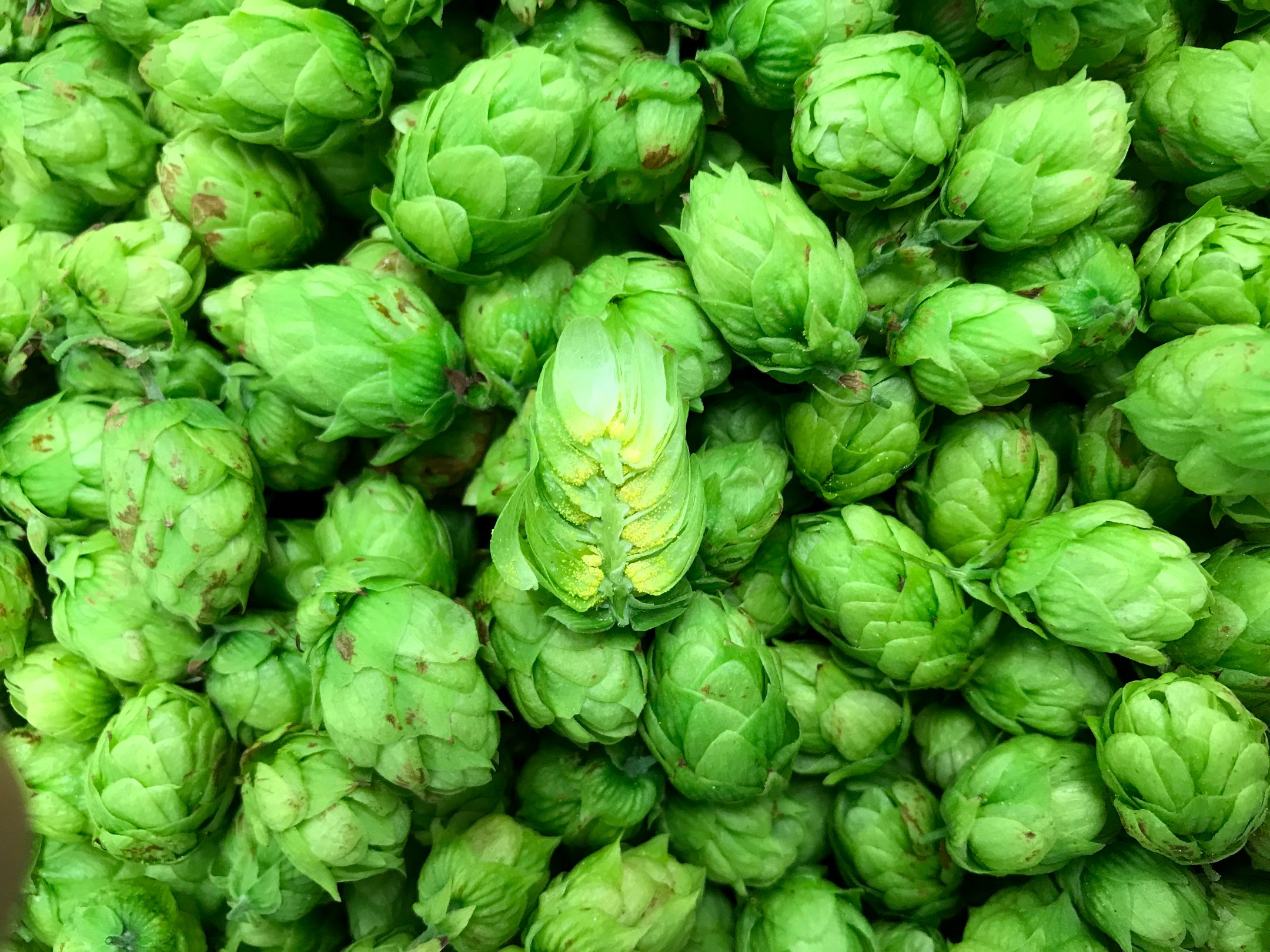
Credit: Shinsuke Agehara, UF/IFAS
Harvesting Procedures
In general, commercial hop harvesting operation involves two steps. The first step is to cut down bines from the trellis. The second step is to separate cones from stems and leaves using picking and sorting machinery. The harvesting procedures used at the UF/IFAS GCREC are described below. We use a mobile hop harvester (Hopster 5P; HopsHarvester LLC, Honeoye Falls, NY) (Figure 2), which is suitable for small-scale production (generally up to 5 acres). The tutorial videos describing the hop harvesting procedures are available at https://youtube.com/playlist?list=PL4qrjj3jZ6i5BwgylgUcb6fMI0z9FKCkQ.
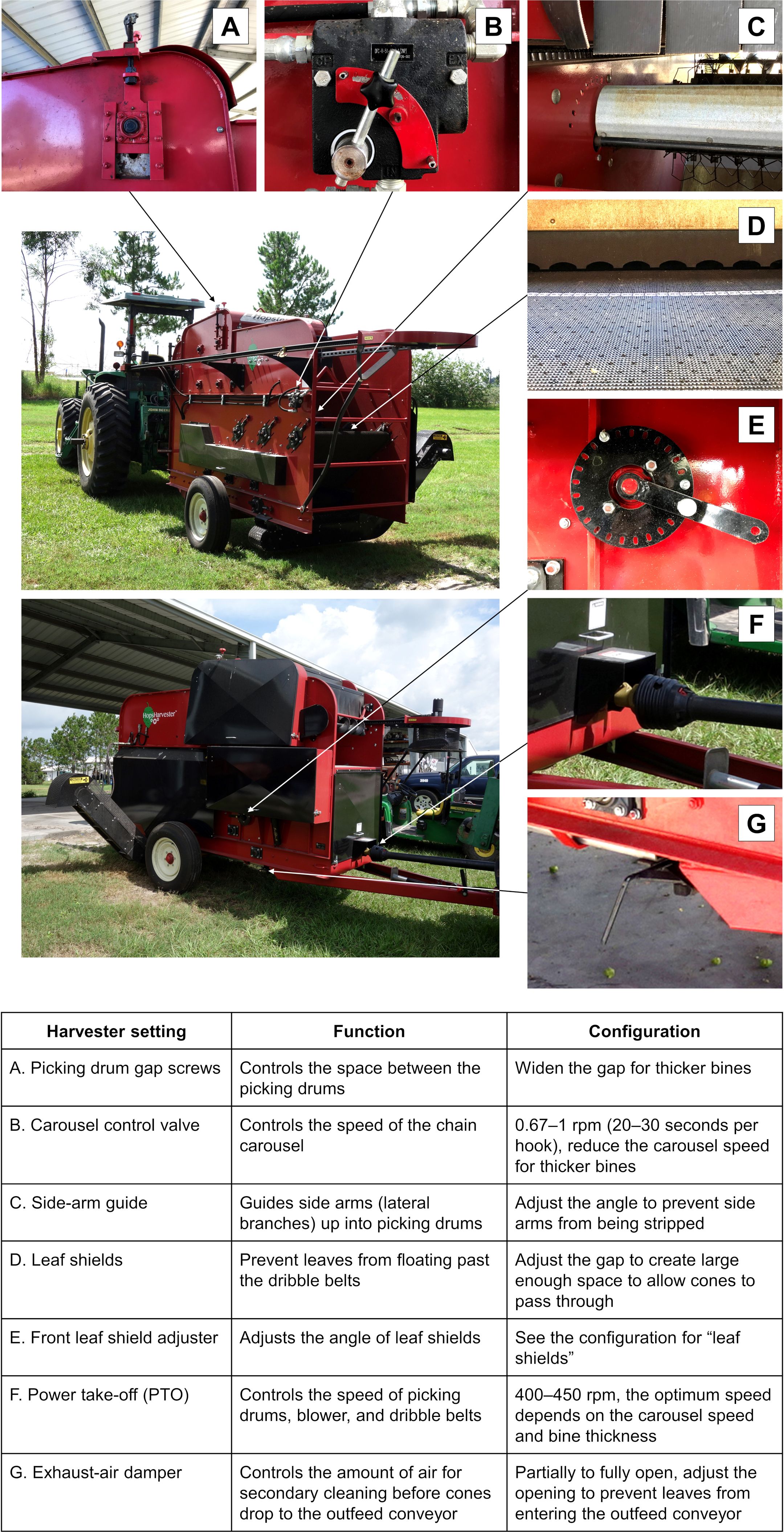
Credit: Shinsuke Agehara, UF/IFAS
Step 1: Cutting Down Bines
The first step is to cut down bines from the trellis using a pole hedge trimmer with a 24-inch blade. This step requires a scaffolding system or scissor lift.
- Cut bines and twines at 3 to 4 ft from the ground (Figure 3A).
- Cut bines and twines at the top of the trellis (Figure 3B) and pull them down (Figure 3C).
- Place the harvested bines on a tarp and transfer them to the hop harvester (Figure 3D).
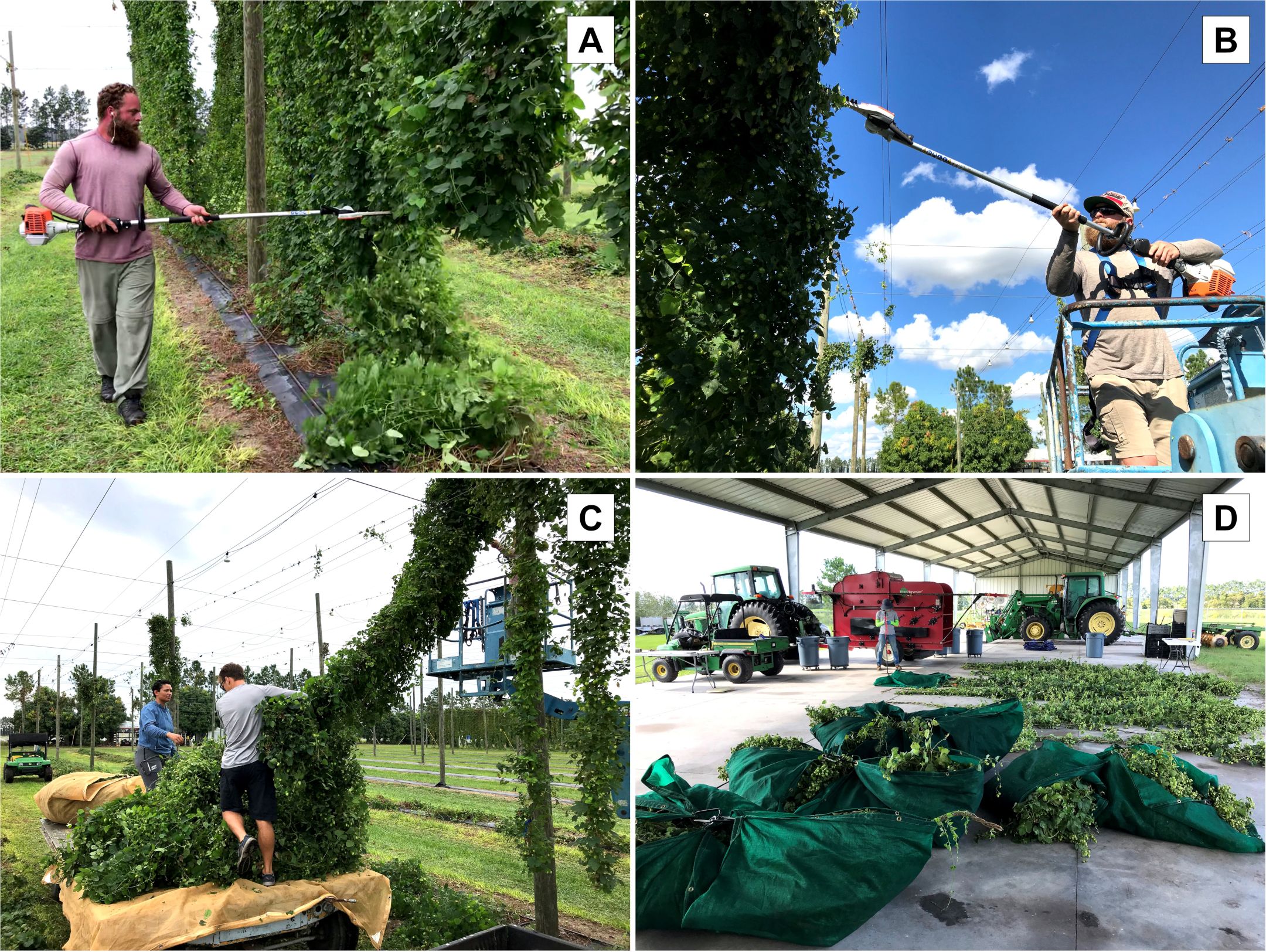
Credit: Shinsuke Agehara, UF/IFAS
Most hop plants produce very little cones on the bottom 3 to 4 ft of their bines. Therefore, leaving this lower portion of bines in the field does not affect cone yields, but it can make the handling of harvested bines and the subsequent cone separation process easier and faster.
Step 2: Separating Cones from Bines
The mechanical hop harvester used at the UF/IFAS GCREC (Hopster 5P) is shown in Figure 4. Its mobility provides flexibility in selecting the location to perform the cone collection process. This harvester requires an external power source: a tractor or truck equipped with both a power take-off (PTO) output and remote hydraulics. The picking drums, dribble belts, blower, and main conveyor are powered by the PTO, whereas the chain carousel and outfeed conveyor are hydraulically powered. According to the manufacturer, minimum power requirements include a 20-horsepower engine, 540 PTO, and one pair of remote hydraulics at 4 gallons per minute. We use a tractor with a 104-horsepower engine (John Deere 6410, John Deere, Moline, IL) to operate the harvester.
- Connect the harvester to a tractor.
- Start the tractor, engage PTO, and turn on hydraulics.
- Adjust the engine speed to run PTO at 400 to 450 rpm (Figure 2).
- Our 104-horsepower tractor uses 1200 to 1700 rpm for the engine speed to run PTO at 400 to 450 rpm.
4. Adjust the carousel speed to 1 rpm using the chain carousel control valve (3 hooks on the carousel chain).
5. Adjust the exhaust-air damper, leaf shields, and picking drum spacing based on the conditions of harvested bines (Table 1).
6. Attach the bottom end of the twine to the hook (Figure 4A).
- When working with thin bines, it may be possible to attach more than two twines on the same hook.
- Keep bines to the right of the triangle to increase the contact of bines with the picking drums (Figure 4B). The chain carousel will feed bines into the picking drums to strip cones and leaves from stems (Figure 4C).
- Leaves will be sorted from cones through a series of inclined dribble belts that allow cones to roll down (Figure 4D). Leaves will then be ejected from the rear of the harvester (Figure 4E).
- Cones will be transferred to the outfeed conveyer (Figure F) and ejected from the harvester (Figure 4G).
7. Remove stripped bines from the chain carousel once they have completely exited the front of the harvester (Figure 4H).
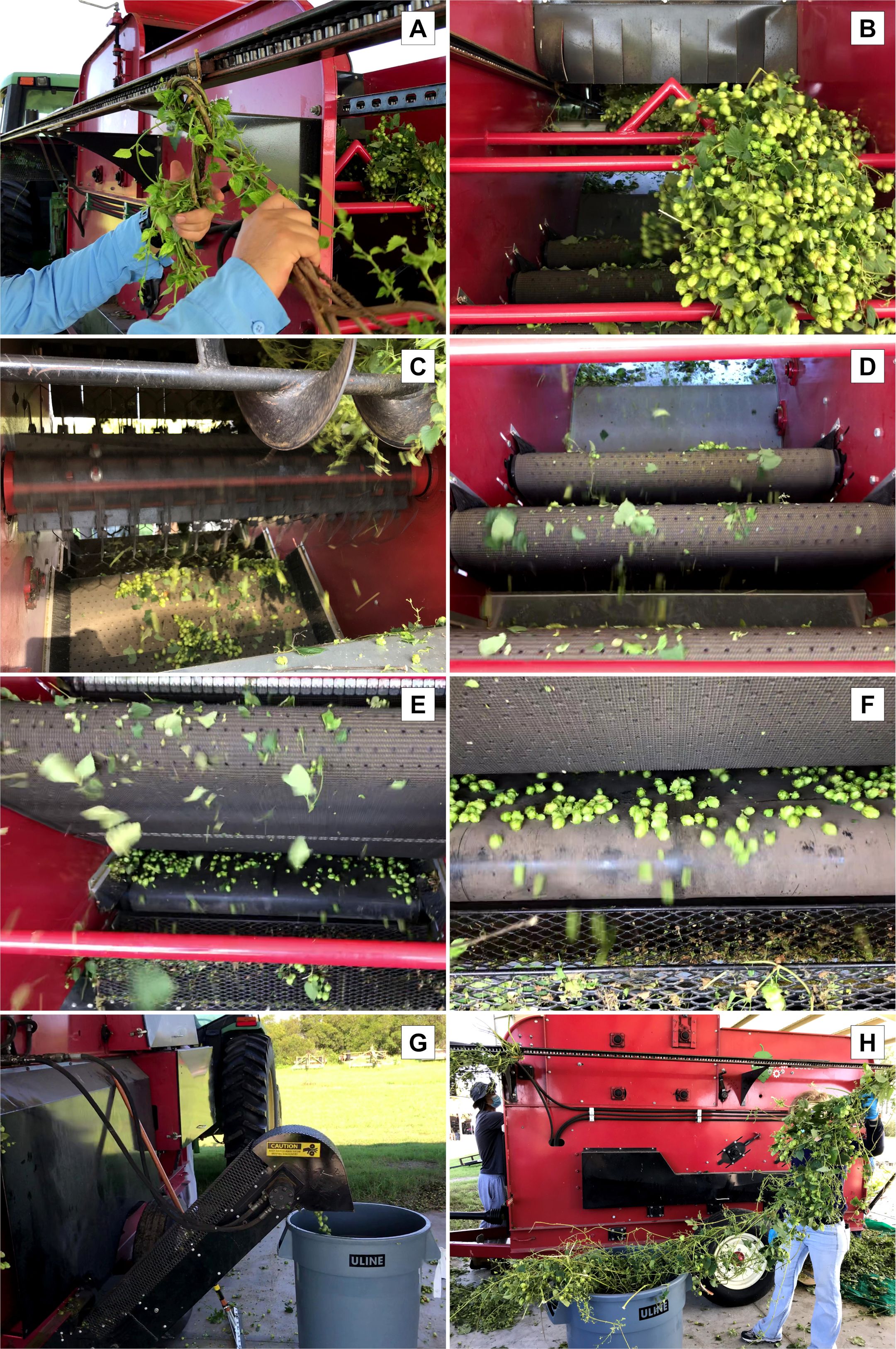
Credit: Shinsuke Agehara, UF/IFAS
The efficiency of cone separation is affected not only by these harvester settings, but also by wind and the angle of dribble belts. Under outdoor conditions, place the rear of the harvester on the downwind side to minimize the impact of wind. If cones cannot be sorted properly by adjusting the harvester settings, lower the front of the harvester by lowering the height of the tractor drawbar. This will make the slope angle of dribble belts steeper, allowing cones to roll down more easily. After changing the belt angle, readjusting of the harvester settings may be necessary to achieve the best results.
Remarks
Harvesting is generally the most labor-intensive activity of hop production, accounting for 42% to 51% (134 to 162 hours per acre) of the total labor input in our operation at the UF/IFAS GCREC (Agehara et al. 2021). The harvesting procedures described in this article are only suitable for a small operation (typically less than 5 acres). When the production scale is expanded, harvesting labor could be reduced significantly by implementing large-scale harvesting machinery.
Literature Cited
Agehara, S. 2020. “Using Supplemental Lighting to Control Flowering of Hops in Florida.” EDIS 2020 (2). HS1365. https://doi.org/10.32473/edis-hs1365-2020
Agehara, S., M. Gallardo, A. Acosta-Rangel, Z. Deng, J. Rechcigl, T. Luo, and Q. Qiu. 2021. “Crop Management Practices and Labor Inputs for Hop Production in Florida.” EDIS 2021 (2). HS1409. https://doi.org/10.32473/edis-hs1409-2021
Hop Growers of America. 2017. “Varieties Snapshot.” Accessed August 26, 2021. https://www.usahops.org/cabinet/data/USAHops_VarietySnapshot_2017_SinglePage.pdf
Krebs, C. 2019. “Hops: A Viable Alternative Crop for the Central/Southern Plains?” Crops and Soils 52 (4): 4–6. https://doi.org/10.2134/cs2019.52.0405
Mabie, D. M. 2021. “Assessment of the Effects of Airflow Conditions Related to Hop Drying.” PhD Diss., University of Nebraska–Lincoln.
Neve, R. A. 1991. Hops. Berlin: Springer Science & Business Media. https://doi.org/10.1007/978-94-011-3106-3
Nickerson, G. B., and S. T. Likens. 1979. “Hop Storage Index.” J. Am. Soc. Brew. Chem. 37 (4): 184–187. https://doi.org/10.1094/ASBCJ-37-0184
Thomas, G. G., and W. W. Schwabe. 1969. “Factors Controlling Flowering in the Hop (Humulus lupulus L.).” Ann. Bot. 33 (4): 781–793. https://doi.org/10.1093/oxfordjournals.aob.a084324