Introduction
Applying multiple pesticide products in the same application is common practice across many industries and is referred to as “tank mixing.” Tank mix components can include pesticides, adjuvants, fertilizers, and other non-pesticidal products. This practice can provide a variety of benefits including:
- Enhanced pest control
- Broader pest control spectrum (multiple target species)
- Reduced selection pressure for resistance if using multiple modes of action
- Increased efficiency by consolidating multiple applications into one
This publication is intended to help pesticide applicators and county Extension faculty to better understand proper pesticide mixing and to reduce instances of incompatibility. After reading this publication, readers should understand the causes of pesticide incompatibility, how to avoid incompatibility, and how to maximize the benefits of tank mixing.
Types of Pesticide Incompatibility
Legal
The Federal Insecticide, Fungicide, and Rodenticide Act states that all pesticides must be used according to their product labels. Not all product labels provide tank mix instructions. However, FIFRA Section 2 (ee) allows for mixing any pesticide, or fertilizer and pesticide, only if the mix is not explicitly prohibited by the product label. Some product labels prohibit specific tank mix partners or mixing at all. Always read and follow all product label instructions.
It might also be possible that a label does not explicitly prohibit mixing, but the rules of the product would make it impossible to mix. For instance, if a product required no more than 20 gallons of carrier mix, while another required a minimum of 50 gallons, you would not be able to mix these products. Applicators should also pay attention to any re-entry restrictions and always follow the most restrictive re-entry timeline. Additionally, all PPE (personal protective equipment) must be worn from ALL labels. As the Endangered Species Act (ESA) increases its impact on pesticide applicators, always be sure that every product you are mixing meets any restrictions or requirements as listed on the label. Given the increasing complexity of compliance with these rules, the more mixed products in the tank, the harder it will be to comply.
Chemical
Chemical incompatibility occurs following a chemical reaction between tank mix components that renders the active ingredient(s) deactivated. Indicators of chemical incompatibility may not be present during mixing. Therefore, this type of incompatibility may not be identified until after the treatment has been applied. However, some chemical incompatibilities may be identified by an increased solution temperature indicating an exothermic reaction. This heat can additionally cause damage to spray equipment.
Chemical incompatibility can also occur when a positively charged ingredient (cation) binds to a negatively charged ingredient (anion). For example, the herbicides paraquat and diquat are strong cations and are deactivated when in contact with anions such as organic matter or soil. The pH and total hardness of source water can have an impact on pesticides as well. For more information about source water specifically, refer to Ask IFAS publication PI-156, “Water pH and the Effectiveness of Pesticides.” Guidance for avoiding chemical incompatibility can usually be found on product labels (Figures 1 and 2).
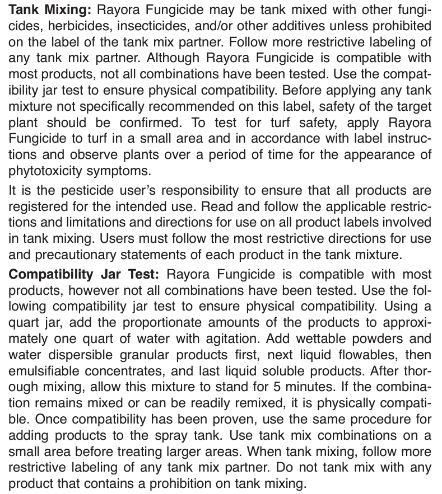
Credit: Rayora Fungicide Label, FMC Corporation, 2929 Walnut Street, Philadelphia, PA 19104
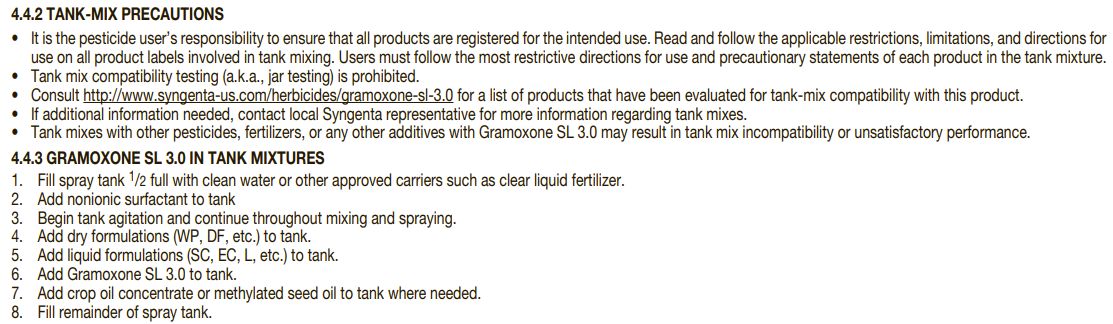
Credit: Gramoxone SL 3.0 label, Syngenta Crop Protection, LLC, P.O. Box 18300, Greensboro, NC 27419-8300
Physical
Physical incompatibility occurs when the components in the mixture do not mix well. Separation of components into layers (layering) (Figure 3), clumping, excessive foaming (Figure 4), and settling are all types of incompatibility. In some cases, different formulations might clump or form solids in the tank. Physical incompatibilities are usually easier to identify than chemical incompatibility. For example, some wettable powders and emulsifiable concentrates are physically incompatible without agitation and can form layers in the spray tank. This can either clog a spray system or provide inconsistent control because the products will not be evenly distributed during spraying. Cleaning physical incompatibilities out of spray equipment can be difficult, if not impossible, rendering the equipment inoperable. Avoiding this type of incompatibility will be discussed more in the “Jar Test” section.
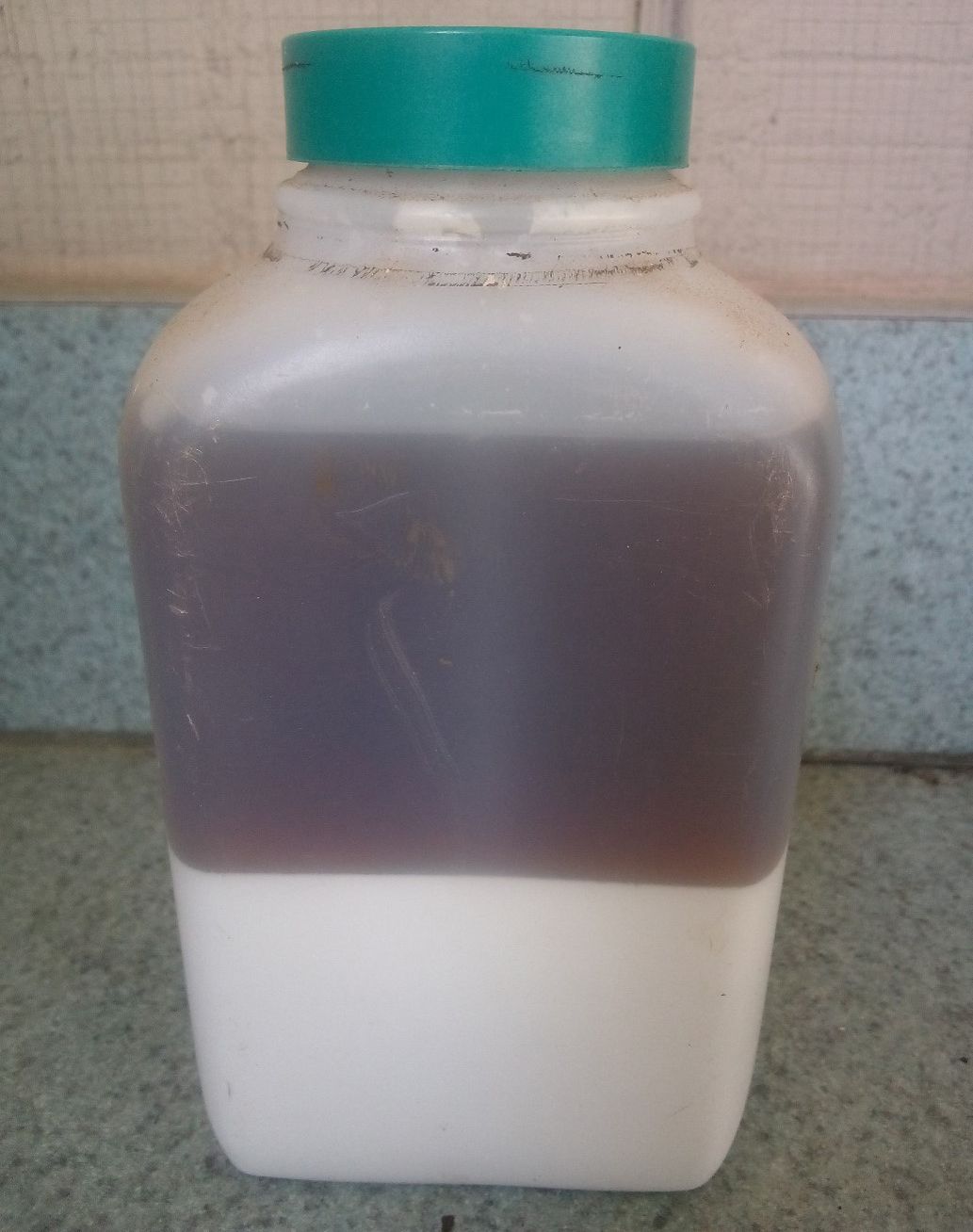
Credit: Ethan Carter, UF/IFAS
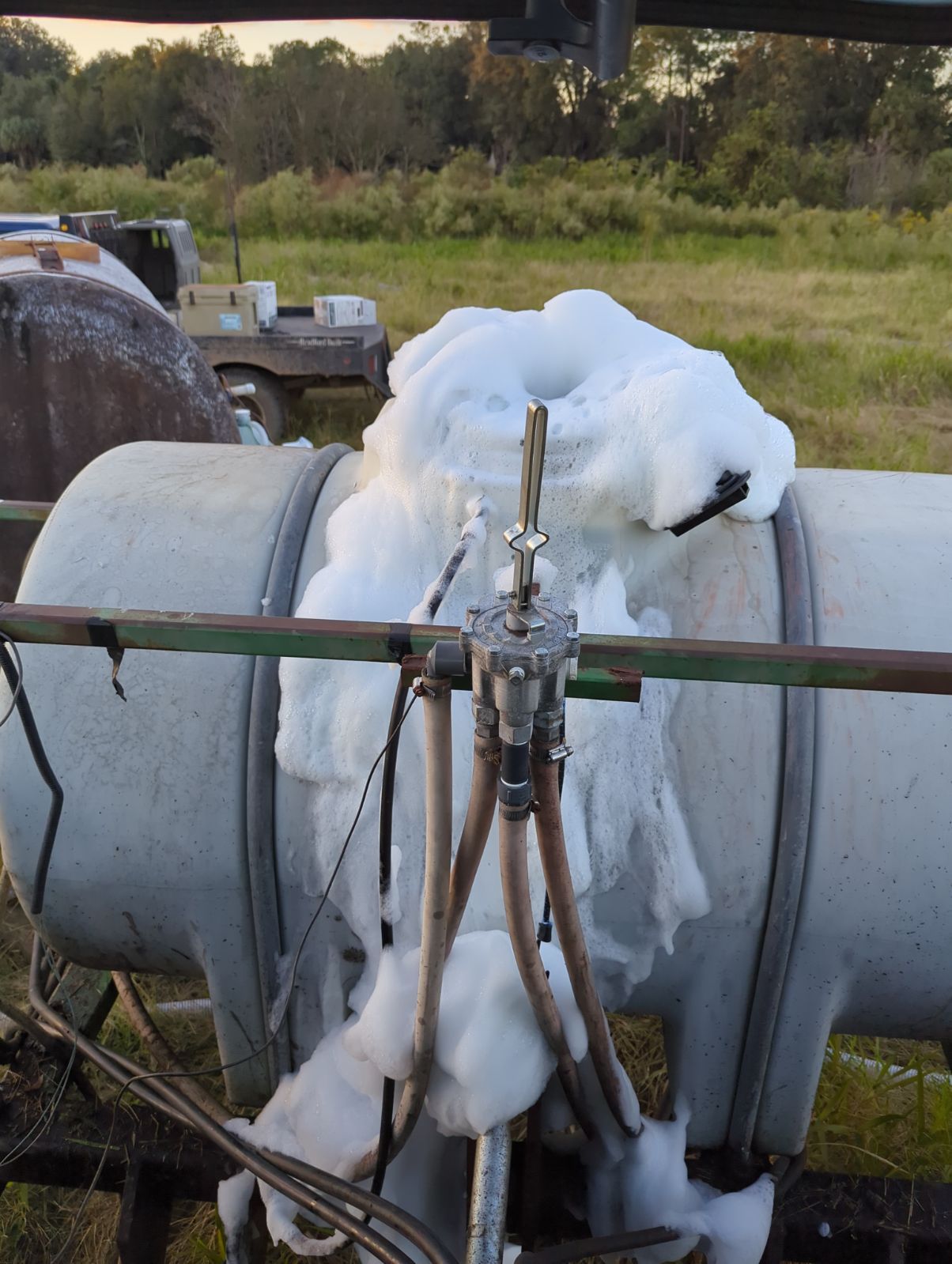
Credit: Prissy Fletcher, UF/IFAS
Other Considerations
Beyond classical incompatibility, there are additional considerations when mixing products together. Issues such as antagonism, reduced selectivity, and even crop damage can occur when mixing pesticides. The more complicated the mix, the higher the chances of unintended consequences.
Antagonism is when two different pesticides reduce overall efficacy compared to the products used alone. Reduced selectivity can occur when mixing multiple modes of action, such as mixing a graminicide (grass-specific herbicide) with an auxin herbicide. Auxins control broadleaf plants and ACCase grass species, so using them together in a lawn might control more species than intended; however, if the goal is a wide spectrum, this mix could be desirable. It is also possible that certain mixtures could harm non-target species, where individualized mixes would not. When organophosphate (OP) insecticides are used for insect control in corn, the OP reduces corn’s ability to protect itself (Hagar 2013). This means spraying a herbicide that is normally safe on corn is no longer safe and your crop could be damaged. Always check for sensitive non-target organisms and ensure there are no known effects from mixing products.
Although there are many advantages of successfully tank mixing pesticides, a major disadvantage is increased risk and associated cost of a mistake. Mixing too many products in an effort to avoid multiple applications can save time and money, but the cost of retreatment due to a failure or equipment repairs can outweigh the benefits of tank mixing correctly.
How to Avoid Incompatibility
Jar Test
The traditional way to avoid pesticide incompatibility is to test possible mix partners in small amounts, in a small container. This is known as a jar test, which can be used to identify physical incompatibility very easily. A jar test is conducted by mixing all products that will be in the tank in your appropriate carrier at the same concentrations to be used, shaking the mix (Figure 5), and observing any changes to the solution. This will reveal products that will gel, solidify, excessively foam, or create a mix that may clog or otherwise damage a spray system. Additionally, allowing the product to sit for an extended period will reveal any separation or layering that may occur (Figure 6).
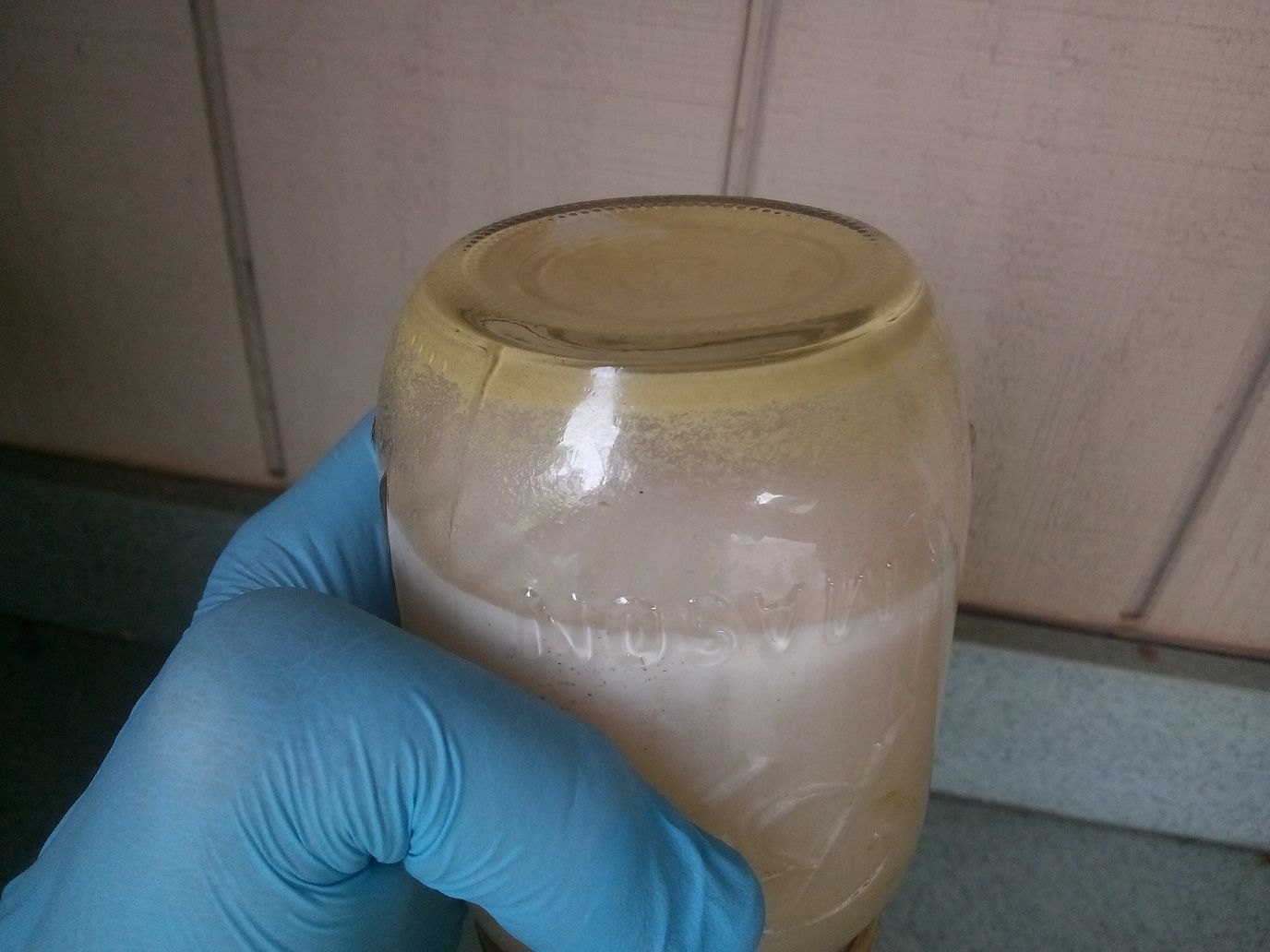
Credit: Ethan Carter, UF/IFAS
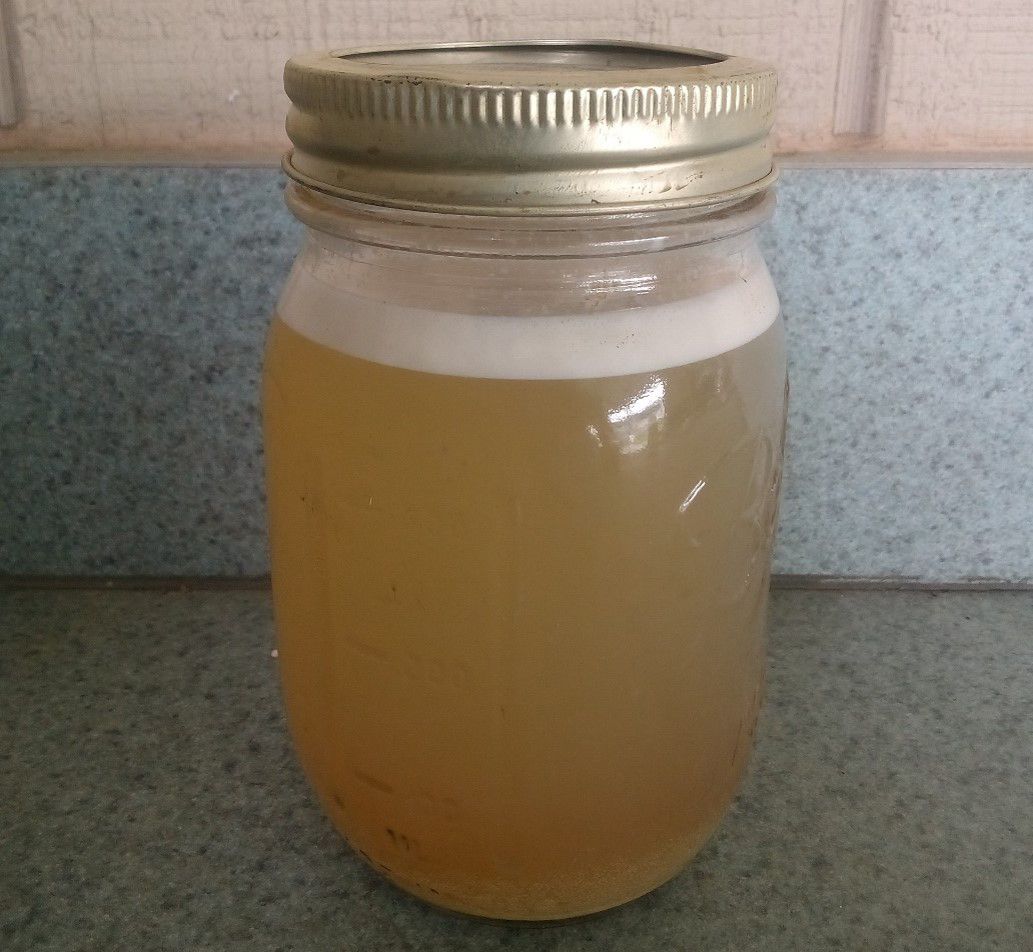
Credit: Ethan Carter, UF/IFAS
The jar test simulates the proportions the chemicals will be mixed in your tank, just in a much smaller scale. In order to do this, you will be using very small amounts of product, so proper measuring devices will be needed. A small scale, pipette, small graduated cylinder, and anything that can measure in milligrams and milliliters will be useful. Sometimes pesticide labels will provide guidance on how to do a jar test; if so, follow their instructions. During a jar test, be sure to wear the appropriate PPE as directed by the label. If no specific PPE is listed for doing a jar test (usually there is not), then follow the PPE guidance as if you were mixing and loading. If no guidance is provided by the label, a generalized jar test will include the following steps:
- Fill your jar half full with the carrier (water, fertilizer, oil, etc.).
- It is important to use the source water you use to fill your tank.
- Add each product, at the ratio it will be in the tank, in the order specified on the label, or as directed by the “Tank Mixing Procedure” section in this publication.
- Once all products are in the jar, cap, shake to mix, and let stand for 15–30 minutes.
- If no noticeable change has occurred, shake, then let stand for another 15–30 minutes.
It is important to note that a jar test will only test for physical incompatibility, not chemical or legal incompatibility. It is the applicator’s responsibility to pay attention to ALL forms of incompatibility.
Tank Mixing Procedure
The order and way in which you add products to a tank can reduce many incompatibility issues. In order to successfully mix, remember the A.P.P.L.E.S. acronym (Ammonium sulfate; Powder solubles; Powder dry; Liquid flowables; Emulsifiable concentrates; Solutions), and always agitate your mix.
- Fill tank half full with carrier (water, fertilizer mix, oil mix, etc.) and start agitating; maintain agitation throughout mixing and application. Add all the following ingredients in the order they are listed.
- A. Ammonium sulfate and any other tank conditioning agents like acidifiers, anti-foam, etc. Allow the mix to agitate for several minutes.
- P. Powder solubles such as dry fertilizers, soluble granules (SG), and soluble powder (P).
- P. Powder dry such as dry flowables (DF), water dispersible granules (WDG), wettable powders (WP), and water-soluble packs (WSP).
- L. Liquid flowables such as aqueous suspension concentrate (ASC), flowables (F), micro-encapsulated products (ME), soluble concentrates (SC), and suspoemulsion (SE).
- E. Emulsifiable products such as emulsifiable concentrate (EC), oil-in-water emulsions (or concentrated emulsions) (EW), and oil dispersion (OD).
- S. Solutions such as solutions (S) and soluble liquids (SL).
- Add all remaining surfactants such as crop oils, drift agents, etc.
- Add remaining carrier to tank while continuing agitation.
The key is to be deliberate and take your time. Ensure each product you add has had time to fully mix before you add the next product. Remembering A.P.P.L.E.S. can help ensure your tank does not clump or otherwise gel (Figures 7 and 8).
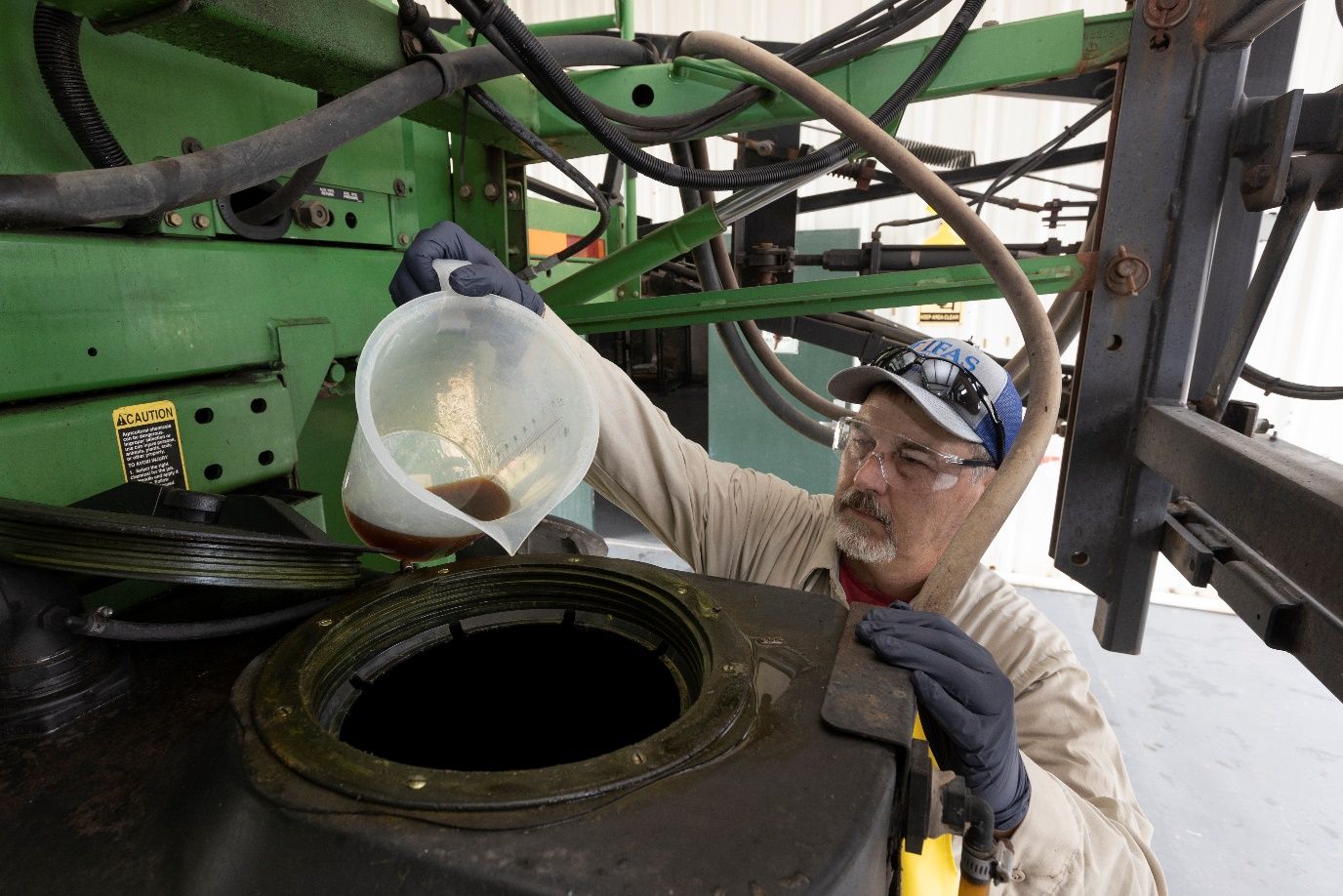
Credit: UF/IFAS
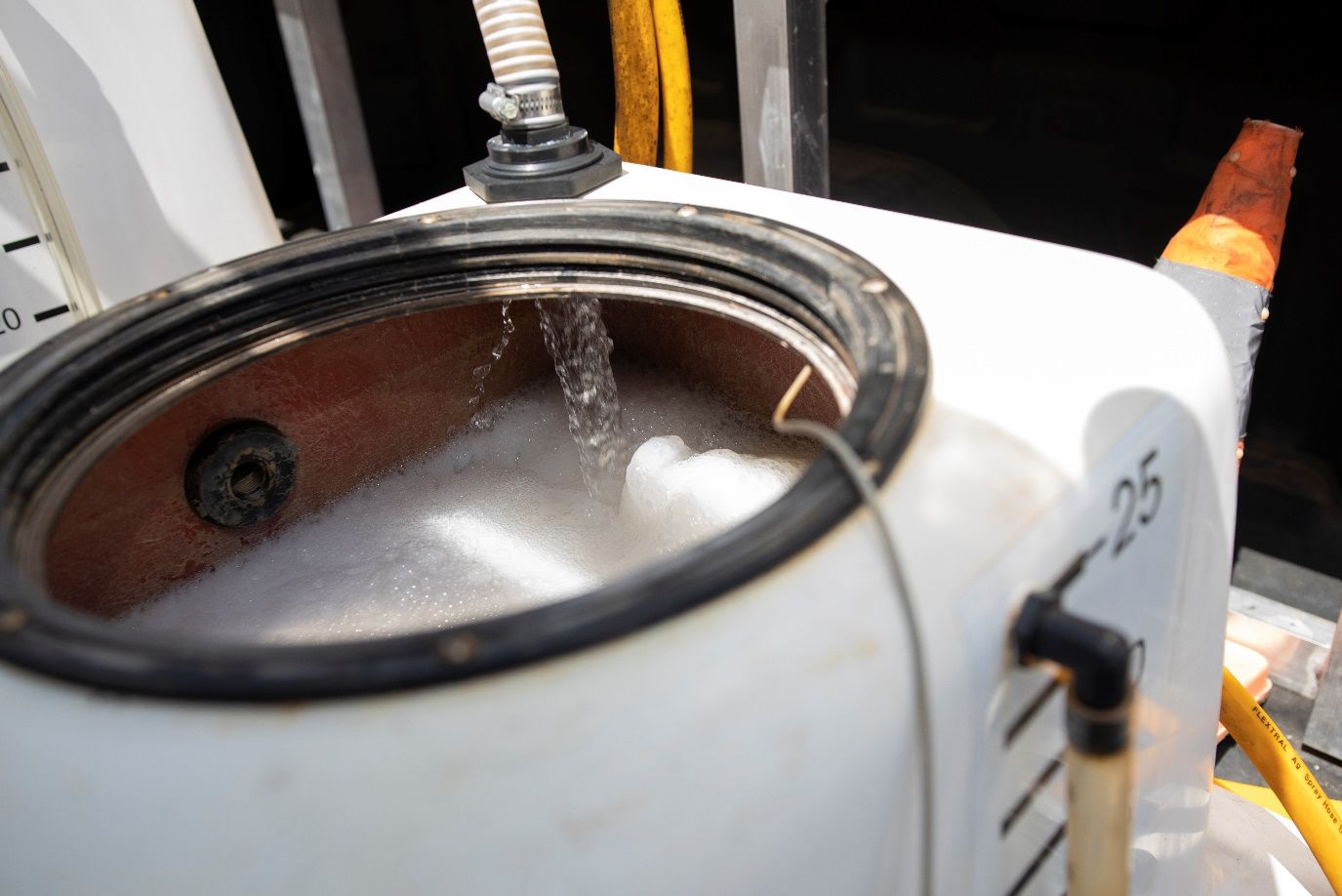
Credit: UF/IFAS
There are commercial tank-mixing tools that will show you the appropriate order in which to add your products. The most used is “Mix Tank” by Precision Laboratories (http://www.mixtankapp.com/). This app will help with mix order, known incompatibility issues, and jar testing, issue weather warnings, and provide other features. You simply plug every product you are using into the appropriate product category (products are alphabetized). The phone app has more features than the online app. Remember local water conditions may need to be considered and not every combination has been tested, so initial jar testing to account for local conditions is advised.
Another key way to avoid incompatibility is to ensure you properly clean out your spray equipment after use. Properly agitating will help to ensure the product stays mixed and will be sprayed out, but cleaning routinely will ensure no issues. Some product labels will clearly define when and how to clean out. For further guidance on cleaning out a tank, see Ask IFAS publication PI291, “Sprayer Cleanout Procedures: Protect Equipment and Crops.”
Conclusions
Tank mixing offers many advantages for pesticide applicators if legal, chemical, and physical pesticide incompatibilities are prevented. Jar tests and following the A.P.P.L.E.S. mixing order can prevent most physical incompatibilities. Always read and follow product labels.
References
Bultemeier, B. W., and B. Sperry. 2021. “Sprayer Cleanout Procedures: Protect Equipment and Crops.” EDIS. https://edis.ifas.ufl.edu/publication/PI291
FIFRA. n.d. “Section 2(ee) Recommendation.” https://www3.epa.gov/pesticides/regulating/section18-training/module-1/story_content/external_files/PREP_Section18_Training_Section2ee_Attachment.pdf
Fishel, F. M., and J. A. Ferrell. 2019. “Water pH and the Effectiveness of Pesticides.” EDIS. https://edis.ifas.ufl.edu/publication/PI193
Hagar, A. 2013. “Corn Herbicide/Insecticide Precautions.” Department of Crop Sciences, University of Illinois at Urbana-Champaign. https://farmdoc.illinois.edu/field-crop-production/weeds/corn-herbicideinsecticide-precautions.html