The purpose of this publication is to present suggestions and options for designing and operating a greenhouse for vegetable production in solid media systems. While developed through perlite and rockwool research, these recommendations also would apply to other solid media, such as peat, pine park mixes or coco fiber. The major design considerations are those pertaining to the floor design for the media system and irrigation system design. Suggestions also are presented for general greenhouse design and operation for tomato culture. Many of these design and management suggestions would apply to houses with other production systems, e.g., upright bag or peat-trough, and in most cases would be applicable for cucumbers, eggplant, and pepper. Additional details on crop culture (irrigation, fertilization, disease and insect control, etc.) can be found at the Florida Greenhouse Vegetable Production Handbook located at the Ask IFAS website https://edis.ifas.ufl.edu/entity/topic/book_florida_greenhouse_vegetable_production_handbook.
Introduction
Production of greenhouse vegetables using solid substrates has become standard practice in many areas of North America (Figure 1). Rockwool is a solid growing medium made of rock fibers (usually basalt). The rock is melted and spun into fibers which are used to make loose "flock" or formed slabs (Figure 2). Fiber binding and wetting agents are added to provide the structure and moisture retention attributes necessary for horticultural use. Perlite is a volcanic mineral which, when heated, expands (pops like popcorn) into small, white particles (Figure 2). Perlite is placed in polyethylene growing bags approximately 36 inches long and 6 inches in diameter containing about 0.5 cubic ft. of perlite, or into open containers with a solution reservoir (Dutch or Bato buckets).
Peat mix (Figure 2) growing media typically is composed of a mixture of horticultural peat plus perlite. The mixture is chosen based on water-holding capacity requirements for a crop. Peat-mix can be used in a lay-flat or upright bag configuration. Pine bark (Figure 3) is used in some growing areas where the bark is readily available because of the pine lumber industry.
Coco fiber (Figure 4), also called coir, is a relatively newer growing media for the greenhouse vegetable industry. Coir can be used in bags or slabs. The fiber is derived from the coconut outer husk, then processed for horticultural use. The processing typically involves washing and drying to reduce soluble salt levels in the final media. Coconuts are soaked in fresh or tidal salt water to soften the husk for easier separation from the nut (when the coconut of commerce is located). If soaked in saltwater, then the fiber needs to be flushed of the salts before processing into various coir fiber sizes (chips, fiber, or pith) and into either loose or compressed bales.
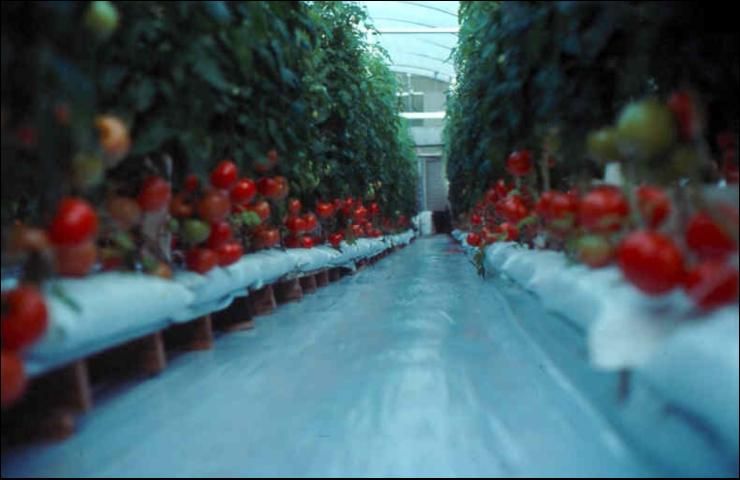
Credit: UF/IFAS
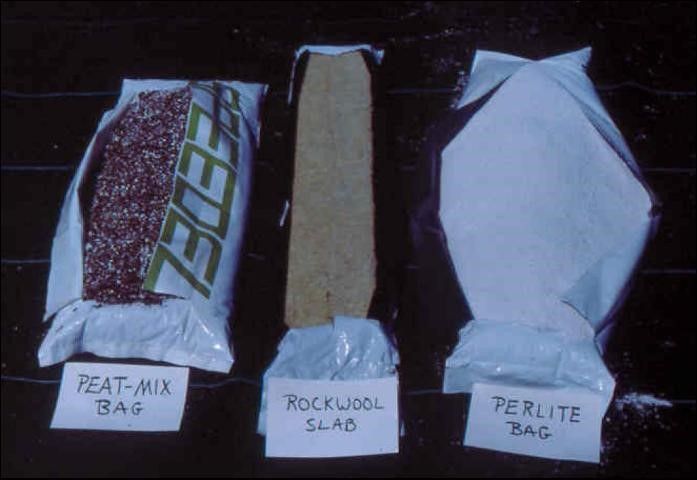
Credit: UF/IFAS
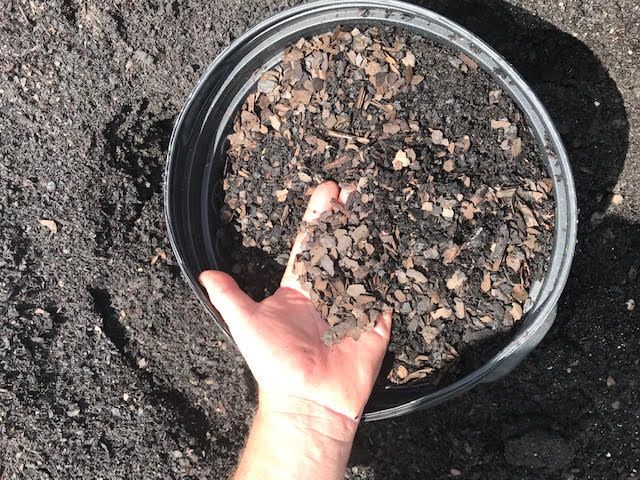
Credit: UF/IFAS
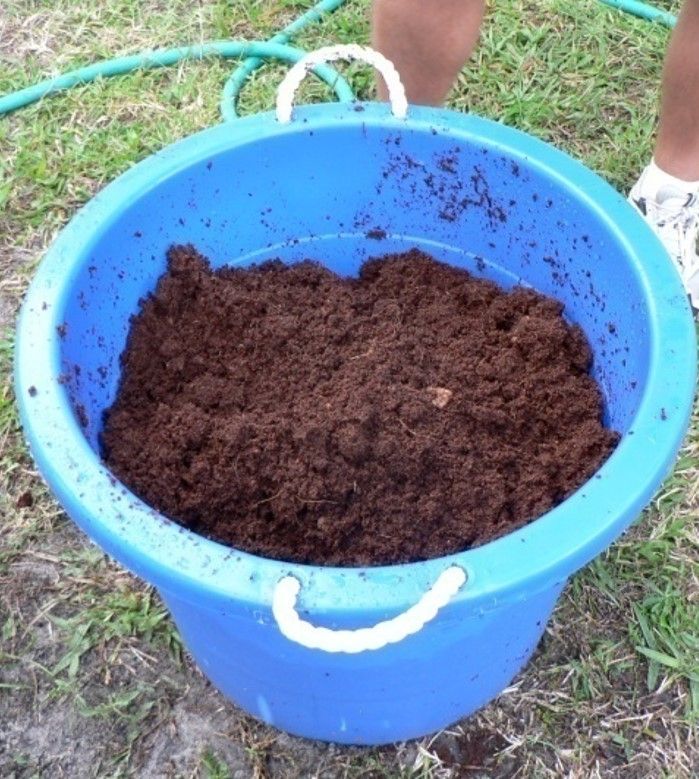
Credit: UF/IFAS
Properly designed solid horticultural media sources provide for a high degree of capillary movement of water and have a large proportion of air space. New solid media materials are pathogen-free and do not themselves provide significant amounts of nutrients to the crop. These media function as support for roots and hold nutrients in the solution around the roots.
Solid media materials can often be reused if sterilized by steaming or other legal means. Research in northern states has shown that reuse for more than one additional year is possible but not recommended due to potential variability among slabs or bags for water conductance and aeration. Extra handling of slabs damages and compresses the rockwool structure. Reuse of unsterilized media of any type in Florida is risky.
Solid media materials have major advantages in Florida over the PVC pipe nutrient film technique (NFT) because solid media production systems do not involve the recirculation of the nutrient solution. Plants are isolated to individual slabs or bags of media and the nutrient solution is applied to each container individually. As a result, nutrient solution that might be contaminated with Pythium spores is not circulated throughout the greenhouse as in NFT (Figure 5). Aeration of root systems also is better in solid media compared to the root systems in the modified NFT (PVC tube) system. The result with solid media is a cultural system that is less risky from a root disease standpoint compared to the closed NFT pipe system.
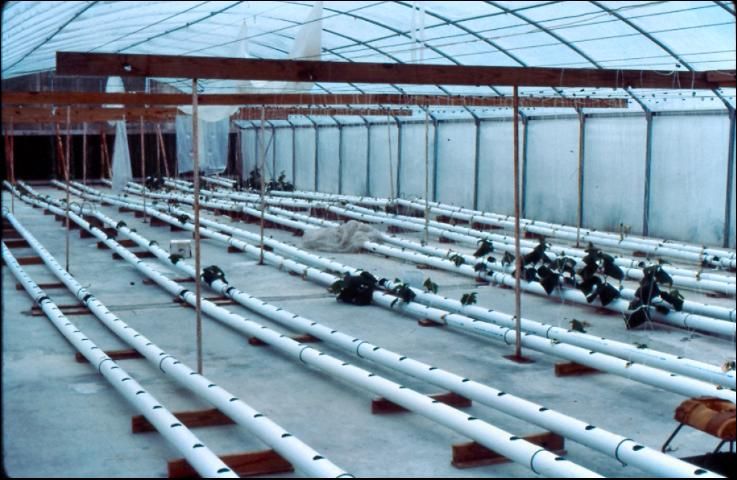
Credit: UF/IFAS
The major design challenge in solid media culture has to do with the design of the floor of the house to facilitate collection and removal of excess nutrient solution leachate from the media containers. It is not desirable, from an environmental pollution standpoint, to allow the leachate to pass into the soil beneath the greenhouse.
Research has been conducted at the University of Florida with solid media for Florida growers. Suggestions for use of these media have been developed from experience and research in Florida and from research in other states and countries. Some guidelines for designing and managing a greenhouse for solid media production systems is presented below.
Site Preparation
Site selection for greenhouses should be given much consideration for drainage, flooding probabilities, water supplies and water quality, shading from trees, etc. The greenhouse site should be raised above the surrounding grade to facilitate quick drainage of water due to heavy rainfall from thunderstorms or hurricanes. More information on general greenhouse design is available from the Florida Greenhouse Vegetable Production Handbook, Volume II.
The Greenhouse for Solid Media Crop Systems
Greenhouse structures are available in many sizes, styles, and quality levels (Figure 6, Figure 7). For cooling efficiencies, it is suggested that the greenhouse be no more than about 110 to 120 feet in length. Houses longer than this present problems in achieving uniform temperatures over the entire length of the house when cooling in early fall and late spring. The width for a single unit should be about 35 feet. This width allows for establishment of six twin-rows of tomatoes within the house and provides for open alleys around the inside perimeter of about 4 to 5 feet. Solid media containers are placed in two rows about 16 inches center to center with an alley between the twin rows. These alleys provide space for air movement and for easy access to the crop for harvesting and spraying. A house 35×120 feet provides growing space for about 1100 tomato plants.
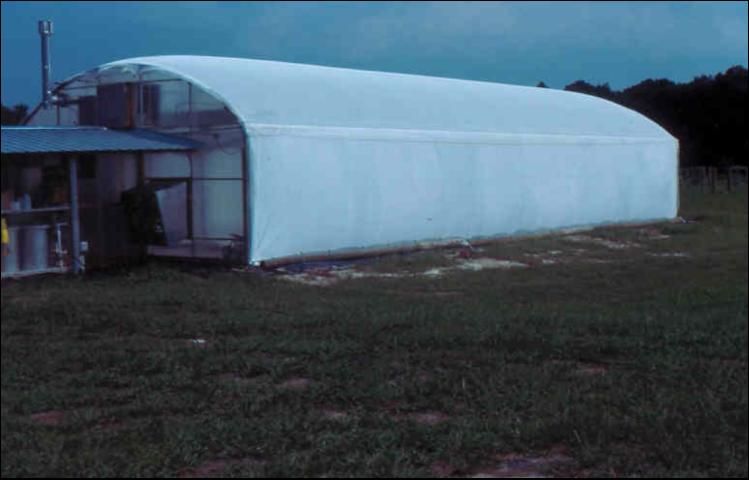
Credit: UF/IFAS
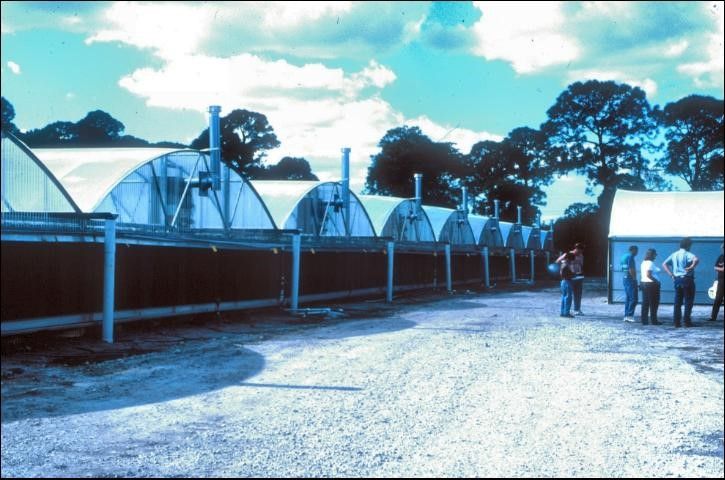
Credit: UF/IFAS
The house should have straight side walls at least four feet high, preferably eight feet. Side walls of eight feet are ideal if expansion to a multi-bay house is envisioned. Overall greenhouse height (ground to arch peak) need not to be more than 14 to 16 feet. Otherwise, an excess volume of air will need to be heated or exhausted which increases operational costs.
Structural components for the house (sidewall columns, arches, bows, purlins, endwalls, etc.) can be home fabricated or purchased as a kit. Either way, the strength and quality of the components must be kept in mind. Saving money on less costly components could cost the grower in the long run if a house must be replaced or requires increased maintenance. If a homemade house is planned, the pipe needs to be of greenhouse structural grade, and a high-quality pipe bending machine will be required. Pipework should be galvanized steel with a high yield and tensile strength of about 50,000 PSI. Sidewall columns should be about 2.5 inches outer diameter and arches should be about 1.6 to 1.9 inches outer diameter. Sidewall columns should be on 5- to 6-foot spacing and be anchored in concrete to a depth of at least 24 inches.
Cooling Pad Endwall
Endwalls should be fabricated from galvanized pipe which is about 1.6 to 1.9 inches outer diameter. Pipe provides more strength and life compared to wooden endwalls fabricated from 2×4 lumber. The cooling pad endwall consists of upright galvanized pipe on 5- or 6-foot centers anchored in the ground in concrete and attached at the top to the end arch. Cross members should consist of additional pipe or aluminum strips. Aluminum pieces are easier than galvanized pipe to drill when attaching the endwall sheeting. The pad endwall shown (Figure 8) has three framed openings. One opening is for the cooling pad and accommodates the 6×30-foot cooling pad. The bottom of the pad frame should be about 12 to 15 inches off the ground. The pad opening should be framed with aluminum poly locking extrusion so that a piece of poly can be placed over the pad opening to close off the opening during winter, unless the pad is equipped with a motorized shutter cover.
The other two suggested framed openings are each for 42-inch motorized inlet shutters (Figure 8, Figure 9). These aluminum shutters are recommended for use in the winter ventilation mode through which outside air can be drawn to cool the house. In this way, cool air is not drawn through the pad directly onto the plants at the end of the house. These shutters are closed in the summer when evaporative cooling via the pad is required. Each shutter is operated by an electric motor. Extra motors should be on hand for fast replacement of nonfunctioning motors. Each shutter is controlled by its own thermostat, or they can be wired so the shutters open simultaneously. It is a good idea to place each shutter on a separate thermostat or to wire the shutters through two thermostats because there is less chance of shutter opening failure. Shutters should be set to open one or two degrees ahead of the start-up of the first exhaust fan. For example, set the shutters to open at 75°F and the first exhaust fan at 78°F. These settings will ensure that the shutters are open before the fans start up.
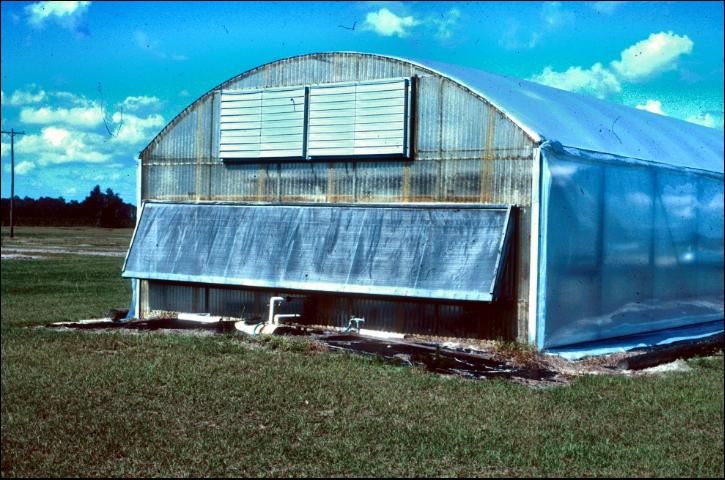
Credit: UF/IFAS
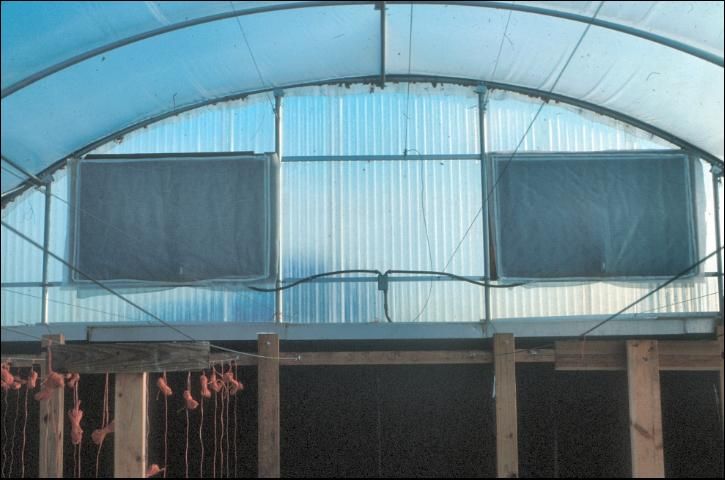
Credit: UF/IFAS
Both cooling pad and shutters should have plastic screen or an insect cloth placed over the openings to help prevent insects from being drawn into the house. Screening will exclude larger insects such as moths, bugs, and grasshoppers. However, most screens will not exclude small insects such as thrips. There is very little one can do to completely screen out these tiny insects without reducing the flow of air through the pad or shutter. If insect exclusion fabric is to be used to cover the pad, the air flow will be reduced. An alternative would be to construct a box frame over the pad area through which to draw air. This increases the surface area to draw air through.
Evaporative Cooling Pad
In Florida, extra cooling is needed in fall and spring over and above that achieved solely by ventilation. Drawing air through evaporation pads provides an additional few degrees of cooling which is important for optimizing tomato production in hot weather conditions. More cooling is achieved in low humidity conditions; less to none under high humidity. The standard method for evaporative cooling is with a cellulose pad system (Figure 10). For tomatoes, the pad should be 6 feet high, at least 4 inches thick, and span nearly the entire width of the house. The bottom edge of the pad should be about 12 inches off the ground or floor of the house to reduce potential for soil and debris to enter the pad.
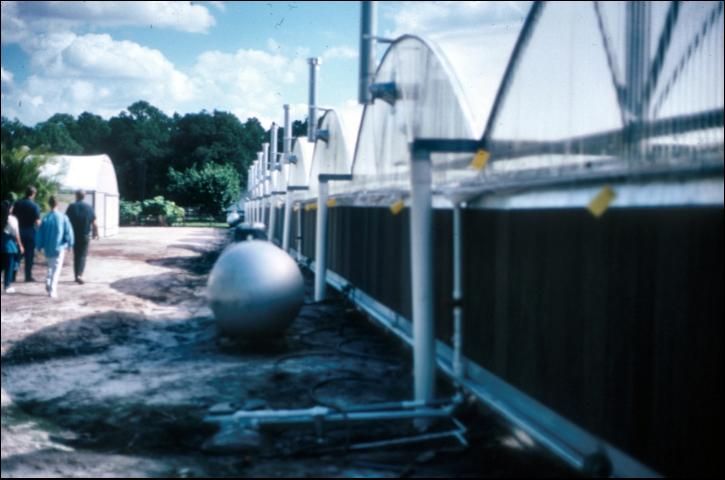
Credit: UF/IFAS
Most evaporative cooling pad systems come with complete instructions for proper installation and care of the pad. The sump tank should be sized to provide 3/4 gallon of water per square foot of pad area. Therefore, a 6×30-foot pad needs a tank with a 130- to 160-gallon capacity. A concrete septic tank or a heavy-wall polyethylene tank are suitable for use as a sump tank. The tank needs to be buried outside the endwall of the house so that the opening to the tank is below the level of the return trough from the evaporative pad. The sump pump should be able to deliver at least ½ gallon water per linear foot of pad per minute. For the 6×30-foot pad, the pump must deliver 15 gallons per minute or 900 gallons per hour.
The evaporation process in the pad uses a considerable amount of water. Therefore, the water in the sump tank must be continually replenished. To achieve this, a float valve should be installed in the sump and attached to a ½-inch (or larger) supply line or tubing that can supply water to the valve as needed. This line can be installed under the floor of the house at the time the floor is installed.
Algae will be a problem on the pad surfaces. Therefore, the sump tank needs to be covered to prevent light from reaching the water. Other helpful precautions are to treat the recirculating water with an approved algicide and to flush the tank periodically.
The Fan Endwall
The fan endwall of the house contains the exhaust fans, inlet shutter for the jet fan, and the entrance airlock porch (Figure 11). The fan endwall should be constructed with galvanized pipe uprights and aluminum or galvanized cross frame members. The fan endwall members support considerable weight, so care must be taken to build with strength and stability in mind. The framed openings include one for a 42-inch entrance door that will be the entrance to the greenhouse proper from the porch. Other framed openings are for the large exhaust fans. Two or three will be needed depending on the size of the fans. For a 35×120 house that is 12 feet tall at the peak, either two approximately 54-inch exhaust fans or three 42-inch fans will be required. If the three-fan option is used, the porch will be placed off-center in the house endwall.
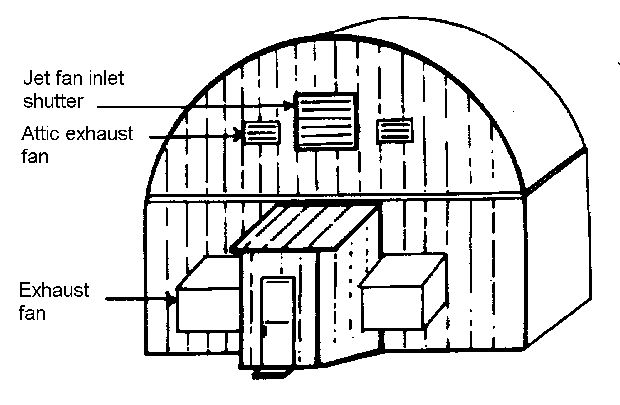
Credit: UF/IFAS
One of the remaining framed openings is for the motorized inlet shutter for the jet fan. This shutter can be opened on a timed basis to allow an inflow of fresh air periodically through the night when the furnaces are operating. Also, some growers might wish to use the jet fan to pull air inside to run through the heating ducts as the first stage of ventilation (before the main exhaust fans come on). However, the jet fan shutter must close when the large fans start to prevent the large fans from pulling air in short-circuit fashion through the jet fan shutter and immediately back outside. This situation reduces the amount of air pulled by the large exhaust fans through the pad at the far end of the house. For the 35×120-foot house, the fan jet size will be about 30 inches in diameter. This fan jet will require a shutter 30 inches square.
Two optional framed openings could be used for attic exhaust fans. Attic exhaust fans might be useful to remove heat from the attic air space above the shade curtain (see section on shading systems) if heat buildup there is a problem. Shading greenhouses in Florida appears to require both shade on the greenhouse film or a curtain that follows the inside contour of the roof and a shade cloth installed horizontally above the plants about 7 feet off the floor.
Where shade cloths are placed just above the plants, heat still builds up in the attic air space and is pulled down into the plant growing level by the large exhaust fans. In this type of shade system, placement of exhaust fans above the shade cloth could remove excess heat from the attic area.
With the two attic fans in place, cooling of the lower plant compartment would be made more efficient. The attic fans would be the first stage of ventilation by drawing air from the outside through the motorized vents above the pad. When additional cooling is needed, the large exhaust fans start up and draw air through the evaporative pad. The pad sump pump should begin the flow of water to the pad after the startup of the main exhaust fans. When the large exhaust fans start up, the motorized shutters should close so that all air drawn into the house must come through the evaporative pad. The attic fans could remain on but will be drawing their air through the pad as well. The pad pump should shut down prior to shut down of the fans so that pad surfaces will dry.
For all environmental control systems, the thermostats or sensors should be located in the center of the house at plant height (about 5 feet off the floor). If a thermostat panel board is used, then it should face away from the pad end of the house and be constructed with sidewalls so that the thermostats are not exposed to direct sunlight. White paint or aluminum paint should be used on the panel board to reflect radiant energy. Today’s greenhouse growers can avail themselves of a multitude of environmental control sensors and management systems and would be preferred over simple thermostats.
Entrance and Airlock Porch
When the large exhaust fans are on, they can pull a great amount of insects and debris into the house when the entrance door opens. Sanitation conditions in the greenhouse can be improved by not entering the house directly from the outside. The problem is alleviated by the addition of a small entrance porch on the front of the greenhouse. The porch allows the greenhouse operator to enter the porch and close the outside door before entering the greenhouse proper through the second door. This airlock reduces the amount of dust and debris that can make its way into the greenhouse.
The entrance porch also provides an area to place the electrical panel box, computer controllers, proportioned pumps, fertilizer stock tanks, and miscellaneous greenhouse equipment and supplies (Figure 12 and Figure 13). The entrance porch needs to be at least 6 to 8 feet square with a tight attachment to the greenhouse endwall to prevent leaks of air or water. The roof and sides could be painted white to reduce heat buildup. The ceiling should be insulated to reduce condensation dripping inside the porch.
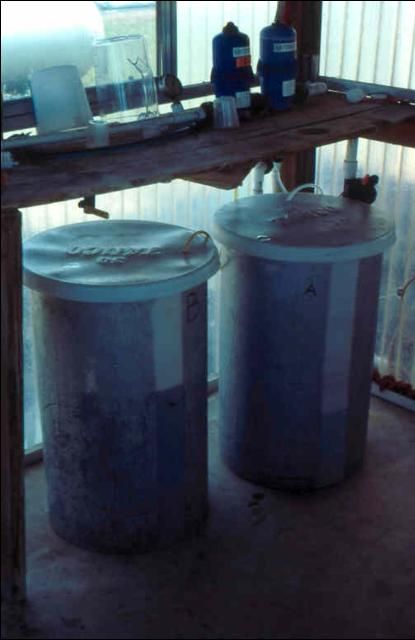
Credit: UF/IFAS
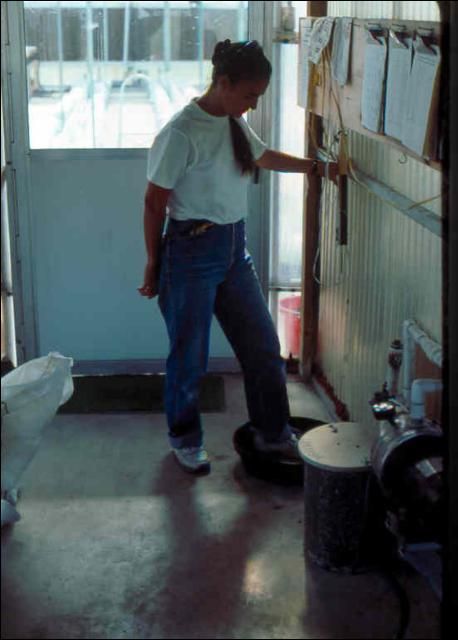
Credit: UF/IFAS
The main supply line for water should come into the porch area from the floor rather than through a side wall. In this way, there is less concern for freezing of the water line. In general, there is little concern for freezing inside the entrance porch. However, the door to the inside of the greenhouse can be left open on extremely cold (below 25°F) nights.
Greenhouse Coverings
Currently, most greenhouse construction in Florida uses a double-polyethylene film where the house is covered with two layers of poly film which are separated by an air layer. A small blower fan inflates the two poly layers with air, thus providing extra insulating value. The separation of the two poly sheets might be as much as 10 to 12 inches at the greenhouse peak. Air for the fan should be brought in from outside the greenhouse to reduce condensation between the poly layers and to minimize chemical damage from pesticides being pulled into the air layer from inside.
The poly films used for covering the house are 6-mil thick, clear polyethylene and usually last for at least 3 years, but rarely more than 4. With age, the poly begins to yellow, reducing light transmission, and it becomes brittle.
Various types of poly covers are available including standard films, anti-condensate films, and infra-red barrier films. The infra-red barrier films have been designed to trap infra-red (heat) energy within the house at night thus reducing heating costs. By their nature, they also increase the temperature during the day. Tests at the University of Florida in Gainesville showed little benefit of infra-red barrier films over the standard poly films for tomato or cucumber yields.
Anti-condensate films have special surfaces that encourage water droplets to form and run off. Condensation on the inner surface of the poly film is a problem in winter because it reduces light transmission until the condensate droplets dry. In addition, the droplets wet plants increasing chances for disease. Condensation forms from the water vapor in the greenhouse atmosphere condensing on the cooler poly cover at night. Anti-condensate films are useful in reducing the amount of condensate that remains on the inside of the cover.
Poly films are fastened to the house at the edges by special poly locking extrusions. On a greenhouse with an 8-foot sidewall, there will be 3 areas to be covered by double poly: the roof and the two sidewalls. The roofing poly is held in place by locking extrusions attached to the end arches and by locking extrusions that run the length of the eaves. The sidewall poly is held in place by baseboard extrusions, corner extrusions, and eave extrusions. Some brands of baseboard extrusions are wide enough to function as concrete pouring forms for a concrete greenhouse floor.
Many brands of extrusions for locking polyethylene are available. Most rely on friction via a clamping mechanism to hold the edges of the poly in place. The most durable extrusions are those made of aluminum. The main difference among extrusions for poly locking is in the specific details regarding the clasping mechanism and on how fast the poly can be released from the extrusion when the poly film is replaced. Some of the poly locking extrusions rely on an aluminum channel into which the double layered poly is locked by a tight-fitting strip or wedge. Some of these are designed so that the fit of the wedge strip becomes tighter in reaction to the natural pull of the polyethylene sheets.
The poly locking system for the house is a component that must be thoroughly researched before installation. The system needs to be simple, without many bolts and screws, yet it must be fail-safe. It is best not to cut financial corners with the poly locking extrusions.
Greenhouse endwalls are usually covered with corrugated fiberglass panels. The panels are fastened to the endwall framing by metal "tekscrews" with rubber washers; care must be taken to position the correct side of the fiberglass outward. Various grades of fiberglass are available with variable life expectancies before the fiberglass yellows and light transmittance is reduced.
After fastening the fiberglass panels to the endwalls and installing shutters and fans, the cracks and crevices should be sealed with aerosol foam to prevent water and air leakage. Rubber gaskets should also be installed behind the fiberglass panels, especially along the lower fastening supports.
Alternatives to corrugated fiberglass sheets include: polycarbonate, acrylic, etc. These are rigid panels that are more expensive than fiberglass sheets, but provide longer life, and are more thermally insulating.
Greenhouse Floor Design
Traditional solid media houses consisted of a soil floor with slight depressions into which excess media leachate drained. The floor was covered with black polypropylene nursery cloth and then with white-on-black polyethylene sheets (white side up) for light reflection. In this system, leachate drained into the trench, through slits in the plastic and nursery cloth, and finally into the ground below the greenhouse. This system of leachate disposal can result in pollution of the underlying aquifer and should not be used. Some system of collection of the leachate will need to be devised. This system will need to be included in the design of the greenhouse floor layout for new solid media houses and built into old houses retrofitted to solid media from another production system. At least two options are available: a raised, above-floor trough system or an in-floor trough system. Both trough systems can be adapted to houses with or without a concrete floor. Several options of both systems are described in the following paragraphs. Each system needs to be designed keeping in mind that the objective is to collect the leachate without having it recirculate from one media container to another.
The above-ground raised-trough system would work in houses with or without a concrete floor. It would be an easy system to install in an NFT house retrofitted to solid media. Media bags or slabs would be placed on inclining benches made from 2×4s and 1×6s (Figure 1, Figure 14, and Figure 15). A half piece of 4-inch PVC pipe is anchored on the floor between the benches and a plastic sheet draped over the benches and trough with slabs placed on the plastic-covered benches. Holes can be cut into the drape to facilitate leachate drainage into the trough. Leachate can be used for other irrigation purposes, e.g., pasture, lawn, garden, etc.
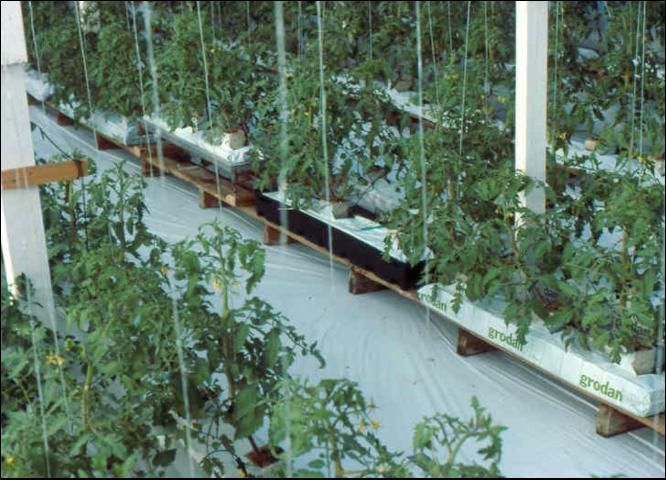
Credit: UF/IFAS

Credit: UF/IFAS
In-floor systems can be utilized in greenhouses with or without concrete floors. One system involves constructing gently sloping trenches in the floor soil of the greenhouse on 5-foot centers. Trenches need only to be 3 to 4 inches deep in the center, i.e., 3 to 4 inches below the level grade. A half piece of four-inch PVC is pressed in the bottom of the trench and the soil pressed (Figure 16). The pipe is placed on an incline so that leachate can drain to the cross drain trough. Black-on-white poly is placed over the trench with holes punched in the poly above the pipe. Solid media bags or slabs are placed on the gently sloping sides of the trench. Slope only needs to be great enough to move the leachate from the bag to the trough. A slope of one-half inch in 12 to 15 inches is adequate.
Another option for an in-floor system is to incorporate perforated drainage tile in the bottom of the trench (Figure 16). A gently-sloping trench is created and lined with 6- to 8-mil polyethylene. This trench needs to be about 4 to 6 inches deep in the center. A 4-inch perforated poly drain pipe is laid in the bottom of the trench and the pipe is checked for proper incline so that leachate will move from one end to the other. The trench is backfilled with small gravel and the whole system is covered with black-on-white poly. The top poly needs to be perforated so leachate will drain through.
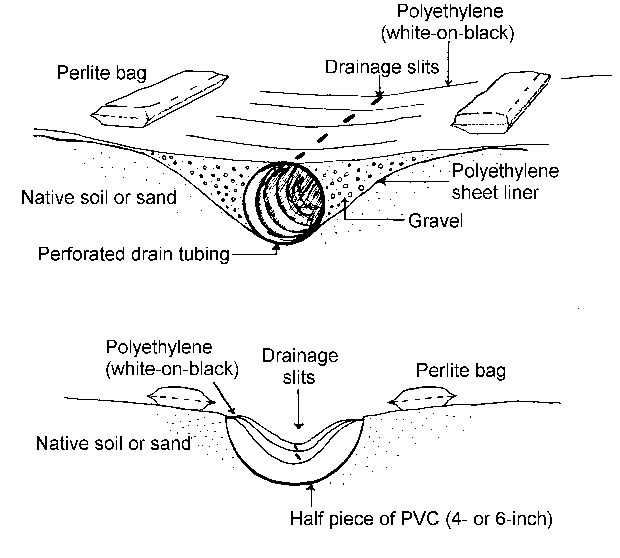
Credit: UF/IFAS
For new houses with concrete floors, the in-floor collection system can be designed into the floor. Two options for this and general layouts are presented in Figure 17. One option is to push a 4-inch PVC pipe partially into the soft concrete in the floor between the future positions for the twin rows of plants. Holes (½ or 3/4 inch) can be drilled into the pipe on both sides where the concrete floor meets the pipe. Pipes will need to be pushed into the concrete to different depths along the length of the pipe to create an angle so that the leachate will flow to one end. It is probably best to restrict flow lengths to 20 feet to minimize pooling. Also, runs no longer than 20 feet would minimize concrete floor thickness. Long runs would need thicker floors within which to bury the pipe on an incline.
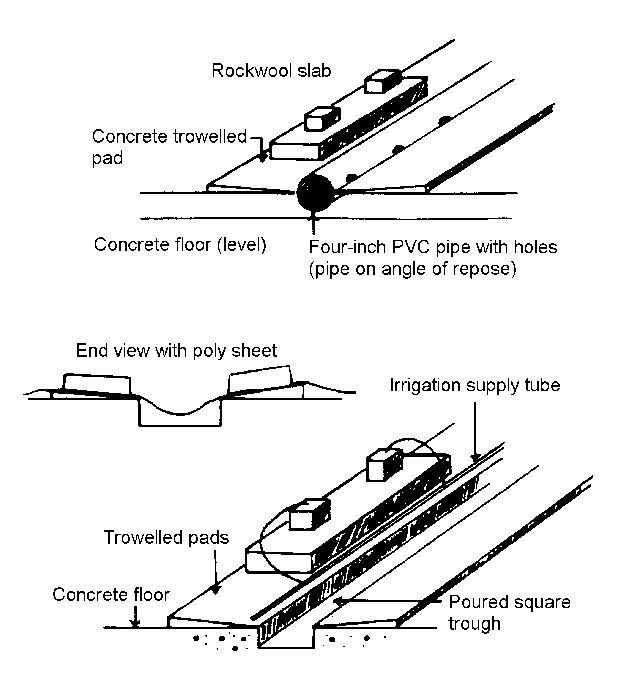
Credit: UF/IFAS
Two sets of collection pipes drain from different directions into a lateral trough. The trough needs to be on a slight sideways angle to move the leachate out of the house. This lateral trough could be simply an open concrete gutter in the greenhouse floor.
To move the leachate from the media containers to the pipes requires that the containers be placed on a slight incline toward the pipe. One idea would be to hand-fabricate a mortar incline on top of the level concrete floor (Figure 18). The mortar incline needs to be about 8 to 10 inches wide and be only 3/8 to 5/8 inch high. Inclines can be built using pieces of lumber and troweling in concrete to build the incline from the PVC pipe to the board. All concrete and mortar surfaces need to be finished smoothly and sealed to facilitate movement of the leachate in the trough.
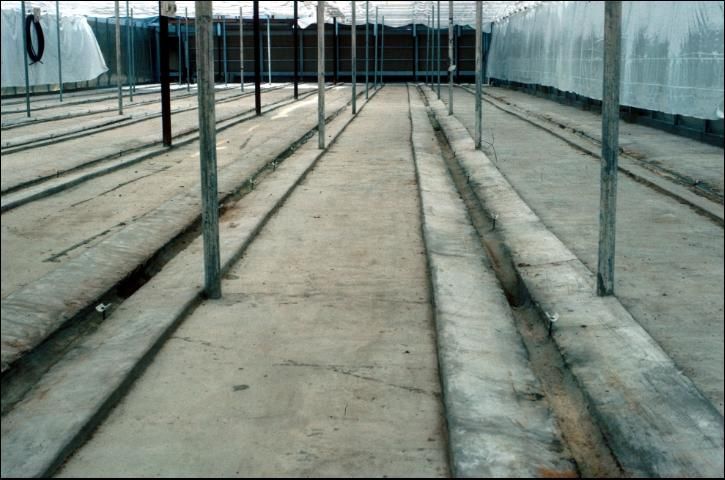
Credit: UF/IFAS
A second in-floor system for houses with new concrete floors would be to press two 2×4 pieces of lumber into the concrete and then remove after the concrete has set (Figure 19 and Figure 20). A small, thin board should be placed between the 2×4s to make it easier to pop the lumber out of the concrete. The depressions remaining will serve as the collection trough. The lumber needs to be pressed in at different depths along the length to achieve the drainage angle. Some individuals might find it easier to precision-place the 4×4 impression lumber prior to pouring the concrete. Mortar inclines are needed as above on which to place the rockwool or coir slabs or perlite bags.

Credit: UF/IFAS
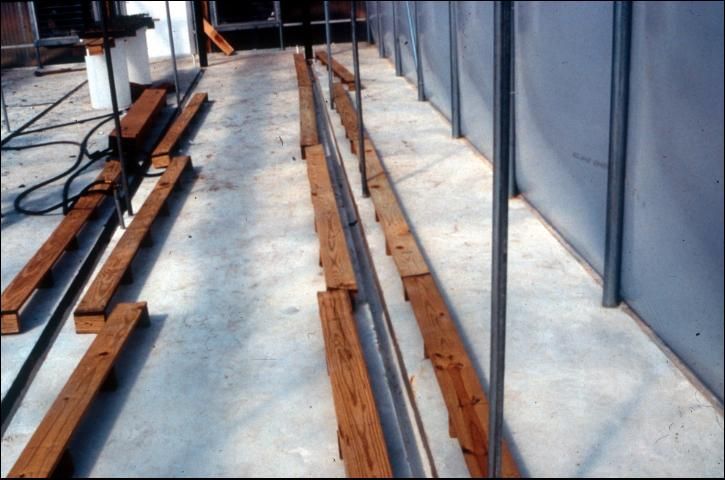
Credit: UF/IFAS
A third in-floor system for new houses is the lintel trough system. Lintel blocks are lined out in the sand floor, perhaps setting them in the floor so that 3 to 4 inches of the block are above the sand grade. The concrete floor is poured level with the top of the blocks. A half piece of PVC is placed on a slope (using wood chocks) in the lintel trough to serve as the leachate conduit.
In the systems above, one could install water supply lines under the concrete floor that supply water to an outlet placed at the high end of each trough. Clean water then can be run down the troughs for periodic flushing of algae and debris. Another idea to help keep the troughs clean is to drape a piece of white-on-black polyethylene over one set of slabs or bags and trough. Slabs or bags are then placed on top of the poly. Holes are punched in the poly just above the trough. Leachate flows from the media containers over the poly surface and funnels through the holes in the poly and into the trough below.
Systems other than the ones proposed above can be devised. The key is to design one that will effectively move the leachate from the house. The incline for the support for the rockwool slab or perlite bag should be no more than about one-half inch in 12 to 15 inches. Floor trough incline probably should be 2 or 3 inches in 20 feet to move leachate from the collection-trough to the cross-trough that takes the leachate to the collection tank.
General layout of the collection system is presented in Figure 21. The reservoir tank size should be at least 300 to 500 gallons and should be buried so the opening is lower than the return troughs. Existing NFT (pipe) houses can use the old nutrient sump tank as the leachate reservoir. The outdoor reservoir should be painted or covered so that light cannot enter the tank, thus preventing algal growth. A sump pump in the tank facilitates pumping out the leachate which can be used for fertilizing pastures, gardens, nurseries, or lawns. Leachate should probably not be reused in the solid media since the leachate might contain disease organisms.
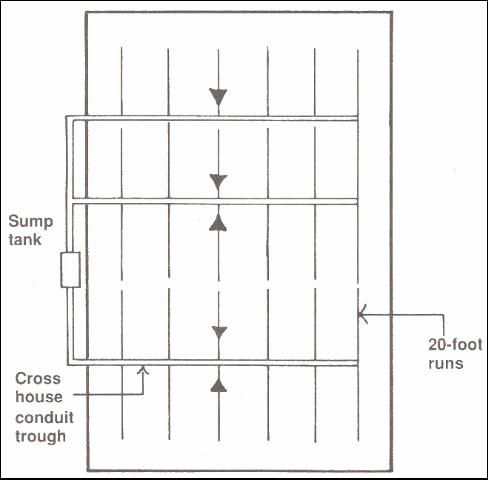
Credit: UF/IFAS
Trellis System
Tomatoes and cucumbers need to be pruned of side shoots (suckers) and trained on a trellis. The planting pattern in the house consists of twin rows of slabs or bags placed on the inclined leachate boards or mortar pads. The distance from the center of one bag to the center of the bag across the trough is about 15 to 20 inches. The distance between centers of one twin-row and the next set, i.e., from one drain trough to the center of the next, should be 60 inches. At the head of each twin-row, a 4-inch iron pipe is concreted into the ground and floor to serve as the main end anchor for the trellis. It is a good idea to attach (bolt or weld) a piece of angle iron or other suitable support between the end post and the floor as a counter support or "deadman" for each post.
Across the top of each post, a 2×4 board or metal bracket is bolted to which to anchor the trellis wires. Each trellis wire (4/32 in. or 5/32 in. airplane cable) is anchored to one endpost with an eye bolt and to the other endpost through a cable tightener. There is one cable for each row of plants. Each plant is trained to the trellis cables using polypropylene twine.
Irrigation System
In a solid media house, water enters the house directly from the well, is mixed with fertilizer stocks by proportioners or injectors and applied to each plant via drip or micro-irrigation emitters. A backflow prevention system (check valve, pressure relief, and low pressure drain) are required for systems in which fertilizer will be injected. The water from the well should be filtered (150 mesh) to prevent damage to the fertilizer proportioners. A union connection installed before all major components will allow them to be removed for maintenance. Proportioners usually operate on a pressure differential basis so that installation in parallel is probably preferred over series. Nutrient solution should be filtered (150 mesh) prior to application to the plants. A pressure regulator should be installed to ensure the desired pressure in the greenhouse irrigation system.
The solid media containers receive water from individual emitters placed at the base of each plant. Emitters can be upright stake drippers. Each plant is irrigated from a short length of spaghetti tubing plugged into a ½-inch or ¾-inch black poly lateral line.
Fertilizer stocks are stored in two containers (30 to 40-gallon size) under each proportioner. Stock tanks of this size will provide for 7-14 days of nutrient application. Stock tanks should be fitted with a lid through which the proportioner suction hoses fit.
Fertilizer formulas and programs that have been successful in Florida rockwool houses are presented in Appendix 1. More detail on fertilizer management for rockwool- and perlite-grown vegetables is presented in "Nutrient Solution Formulation for Hydroponic (NFT and Rockwool) Tomatoes in Florida" (https://edis.ifas.ufl.edu/CV216). These nutrient solution formulas work equally well for any solid media system.
In designing the fertilizer stock tank area, water lines and valves can be positioned above each stock tank for easy filling of stock tanks when mixing new nutrient solution. When mixing new solutions, the controller should be turned off so that proportioners will not remove unmixed stock solution.
Irrigation Control
Managing irrigation is important for two basic reasons: 1). Optimize crop production, and 2). Save water and nutrient resources. Gone are the days when irrigation was done by feeling the media or by some sort of regular, timed frequency. Newer systems are available to help growers manage irrigation systems including electronic starting trays and weather-based computer systems.
The irrigation system on/off cycles can be controlled by an "irrigation starting tray." The tray works well for media in slabs or lay-flat bags including perlite, rockwool, or coir. The starting tray should be placed somewhere in the center of the house. The tray is wired to a relay box which is wired to an irrigation controller that controls the length of each water cycle by opening or shutting the electric solenoid valve. The relay, controller, and solenoid can be placed in the entrance porch. Controllers should have battery backup so that programs are not lost during power outages. Growers need to be sure that the plants chosen for the tray are representative of the plants in the house (and remain so through the season).
To set up the starter tray, a representative spot with representative plants is chosen. It is best to choose a spot at least 20 to 30 feet away from the endwalls. The starter tray is positioned and leveled in all directions. For rockwool or coir slab, the poly sleeve is cut away from the bottom of the chosen slab, and the exposed media is positioned on the capillary mat in the tray. For perlite or other media bags, holes are punched in the bottom side of the bag on a ½-inch grid. Holes should be about to ¼ inch in diameter so the media will have good contact with the capillary mat in the starter tray. Emitters are repositioned at the base of the plants.
The irrigation system might need to be operated for a period to provide nutrient solution to fill the small "V"-shaped reservoir at one end of the tray. The electrical probe(s) is positioned so that the tip contacts the solution in the reservoir. Electrical connections and grounds are completed through the relay box and controller following directions supplied with the controller.
The basic irrigation scheduling theory revolves around applying enough solution to each slab or bag to fulfill plant needs and to maintain an acceptable electrical conductivity (soluble salt) level in the media. For most situations, this means that each irrigation event should apply about 4 ounces of solution per plant. Each irrigation event should result in a small amount of leachate leaving the media container, approximately 10 to 15%. The soluble salt reading of the leachate should be in the range of plus or minus 0.5 to 1.0 units from the applied nutrient solution. More or less nutrient solution can be applied to the plants to achieve this goal. Leachate for testing is collected from the media by a syringe.
Emitters for solid media crops should have an inner diameter of at least .04 inch to reduce the risk of clogging. The irrigation management scheme involves designing a system that applies nutrient solution in ample amounts and in uniform fashion. Depending on the chosen emitter flow rates at a chosen operating pressure, the greenhouse irrigation might need to be constructed in zones. Flow rates of proportioners, pressure regulators, and pump capacity need to be considered.
Once the properly designed delivery system is in place, the starter tray determines when an irrigation event is needed. The controller determines the duration, and this setting will depend on the emitter flow rate, the need for soluble salt control mentioned above; duration will change as the crop develops. It is important that growers monitor crop growth and adjust the irrigation period accordingly. A full-grown tomato plant will use 1½ to 2 quarts of water on a sunny day.
Probe placement depth in the reservoir helps fine-tune the time interval between irrigation events. Shallow placement will mean that the system will come on more frequently because the plants will draw the reservoir level down to the probe setting faster than if the probe was set more deeply. A shallow setting might be useful early in the season when roots are not completely established to make sure the young plants receive ample nutrient solution. A deep setting might be useful later in the season to prevent overwatering on full-grown plants. Immediately after planting and for 3 to 4 weeks afterwards, irrigation should be controlled by timer to ensure frequent irrigations until the root system is well developed and the plants are large enough to draw down the solution level in the starter tray to activate the irrigation system frequently enough.
There is no single, general-purpose program for setting up the starter tray and controller. Each grower will need to determine settings for each situation. Assistance is available from the UF/IFAS Extension staff.
The starter tray will need attention to ensure continued operation success. The probe tip will occasionally develop a salt deposit. This salt must be scraped off and any algae in the reservoir removed. Roots in the probe area should be trimmed back. Growers should periodically check to see that the system is properly operated. One idea to help is to place one- or two-gallon jugs throughout the house into which an extra emitter is placed. Growers can prevent back siphoning of solution from the supply line to the jug by making sure the emitter tube to the jug is placed in the jug so the end of the tube is above the level of the irrigation supply line. These jugs can help determine if the system is operating and if the applications are uniform in the house. Growers also should get in the habit of making a periodic emitter flow rate check.
More advanced irrigation management
Accumulated solar radiation.
Irrigation applications can be managed based on weather conditions at the greenhouse. Solar radiation accumulation can be used to schedule irrigation events. Greater radiation results in greater water and nutrient demand by a crop. Basically this approach involves the following requirements:
- Properly located and mounted solar radiation measuring device, the pyranometer
- Computer that can integrate the solar radiation information and translate into directions for operation of the nutrient solution delivery system
- Computer data collection system so changes and adjustments can be made in the system
Other methods
There are several other methods for managing crop irrigation. These include scheduling by crop water use (evapotranspiration) and media moisture monitoring. These methods are more involved, and in the case of media moisture devices, less well developed. Researchers are developing irrigation control strategies that involve direct water movement in the plant stem. Growers should investigate the various systems for managing irrigation as water and fertilizers become more expensive, and pressure from environmental regulations increases.
Winter Heating
Greenhouse vegetable production in Florida requires heating in the winter to ensure optimum production and freedom from freezing. Heating fuel can be from any source as determined by the grower. Most houses in northern Florida use LP furnaces. Other sources, if available, might be more economical than LP. Hot water requires the investment in the pipe distribution system. In designing the heating system for LP or gas heater, it is probably a good idea to place 2 heaters in the house. In the case of one heater failing, there will be a backup.
Heat is most economically delivered by distributing it on the floor of the greenhouse. For the LP furnaces, this means blowing the heated air into a plenum chamber attached to the front of the distribution fan. Make sure the fan is designed to handle the static pressure in the distribution system. Distribution ducts, both metal and polyethylene, take the heat to the floor ducts which run the length of the house under the plants. The floor ducts should be 8- or 10-inch poly distribution tubing with holes punched to evenly distribute heat down the length of the house. The tubing is placed on or near the floor between the rows of plants in each twin-row set but above the drainage troughs. Holes in the tubing should be positioned to distribute heat out both sides of the tubing upward at about a 45° angle into the plant canopy.
Placing the heat on the floor helps keep the roots warm and places the heat where its use can be maximized (in the plant canopy). If the distribution duct is placed in the ceiling of the house, then the attic must be heated before the plant area can benefit since hot air rises. In this system, air distribution fans would be needed to move the hot air downward. Floor tubes can be used for ventilation even if heat is not required.
In the floor heat distribution system, a heat retention cloth can be deployed on a cable system just above the plants to help retain the heat in the plant zone. If a polypropylene shade cloth is used as a heat retention cloth, it should be a thicker cloth (1.5 to 2.0 oz per yd).
Horizontal air flow fans also are a good addition to a greenhouse heating and ventilation system (Figure 22). These small fans are placed above the plant canopy to move air around the greenhouse to assist in heating and also in drying the plants. For a typical single house, four fans are probably needed, two to push air down one side of the house and two to move air back. The net result is a circular movement of air about the greenhouse. Air flow fans are especially effective during winter when condensation is high and ventilation by exhaust fans is not needed. With the paucity of pesticides for disease control, ventilation and air movement to manage the greenhouse environment are required to minimize disease outbreak.
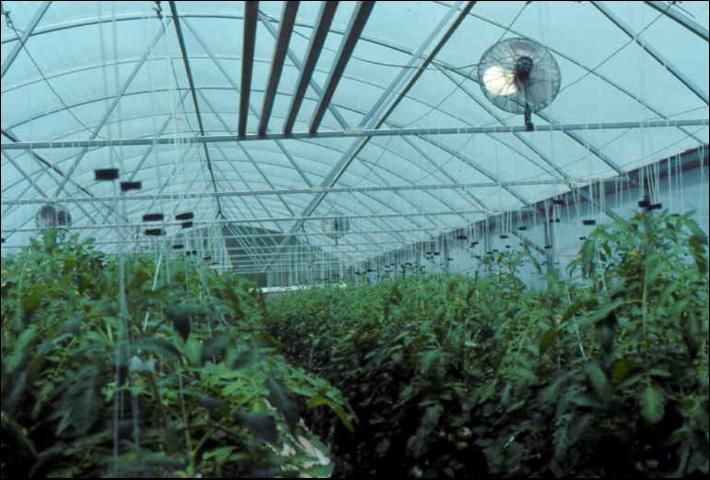
Credit: UF/IFAS
Shading Systems
Vegetable culture in Florida during fall and spring requires shading to reduce heat buildup in the greenhouse. One system is to cover the house from the outside with a shade cover (Figure 6). A more flexible option is a double shading system (roof and plant height level). To maximize flexibility, both systems should probably consist of shade cloths although shade compound paint could be used for roof shading.
The following information on shading is presented as a guideline since little research has been conducted in Florida to determine the best shading system and timing for greenhouse vegetables. Shade cloth thicknesses and management might need to be modified based on experience.
In the simple double-cloth system, a white cloth (polypropylene) could be anchored to a cable at the greenhouse floor and running the length of the house. The cloth can be pulled up by pulleys over additional cables following the greenhouse ceiling contour (Figure 23). This shade curtain could provide about a 30% level of shading when deployed. By placing the curtain on pulleys, it can be deployed or dropped depending on the weather. It can also be deployed to varying heights. Another option would be to place one cloth over the cables attaching it via grommets to the lower cables on each side of the house. The curtain can be deployed or removed by sliding it from end to middle of the house or moving it in halves.
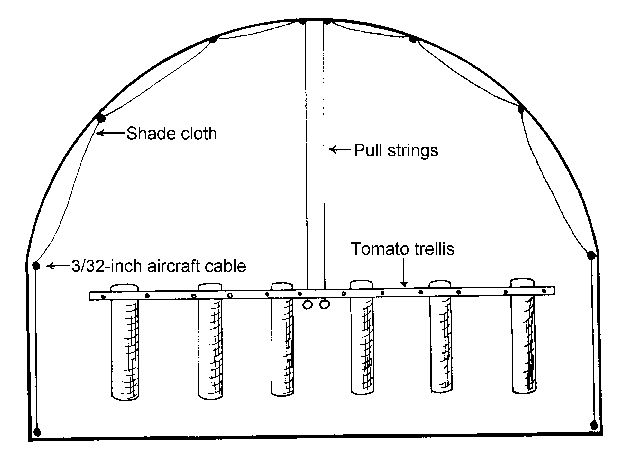
Credit: UF/IFAS
There are available commercial shade cloth systems similar to the simple, home-made system above. Some commercial systems are computer controlled and would be choice for larger operations seeking to reduce labor costs.
Alternatives to this ceiling curtain are greenhouse shading compound (that is applied to the poly cover like paint) and the outside (over-the-house) cloth. The drawbacks to these systems are that they are all-or-nothing options and would require more time to apply and remove than a movable inside curtain.
The second level of shading would consist of a plant-height cloth used over the plants at the 7- or 8-foot height (Figure 24). No detailed research has been conducted on a shade-cloth system for tomatoes in Florida. However, the following is offered as a suggestion for managing the two-cloth system. Modifications might be needed in some situations. These cloths (20 and 30% shade) are placed on 3/32-inch cables running the length of the house spaced about 5 feet apart. The 20% cloth would be used early in the season (March-April) and the 30% cloth would be used in May and June. The cloth is attached to the outside cables by grommets and rings so that the cloth can be moved back and forth. Moving the cloth is easier if it is cut across the middle and moved in halves, one half to the pad end of the house and one half to the fan end. The cable and grommet systems make it easy to deploy or remove the cover depending on weather.
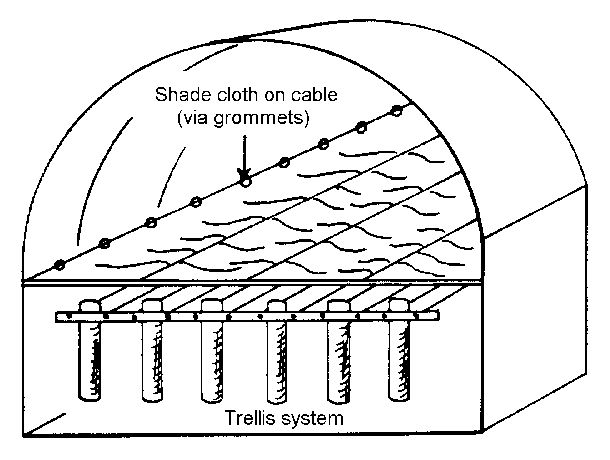
Credit: UF/IFAS
The plant-height shade cloth would provide a second level of shade when temperatures rise so high that the ceiling curtain cannot shade enough. With the plant-height curtain, optional attic fans could be brought into use to help remove the attic heat. In northern Florida, the time to begin shading would depend on temperatures inside the house. It is best to manage shading so that day temperatures are no higher than 88°F to 90°F for tomatoes. Maintaining temperatures in this range, or slightly below, if possible, will minimize fruit ripening disorders such as solar yellowing. In Florida, this means that shading will probably need to be started by early March in most years. A suggested scheme for managing the ceiling/plant-height cloth system is presented in Table 1.
In the fall, both cloths might be needed for August, September, and part of October. Shading can gradually be reduced through October and completely removed by mid-November.
Solid Media Culture
Although solid media bags and slabs can be reused, there is significant risk involved in multiple cropping of these media. Media to be reused should be inspected for damage or compression and any damaged or crushed slabs or bags should be discarded. Old media should be sterilized by approved methods such as steaming. Simple disinfestation will probably not be sufficient. For sterilization, the slabs are partially dried by letting the plants withdraw water at the end of the season. Slab covers are removed, slabs are stacked and sterilized. New sleeves are then placed over the slabs. loose media, such as perlite would need to be emptied from the bags and bulk-sterilized, then re-bagged.
Successful media reuse requires significant time investment and care to produce small financial savings. For many growers, the risk is not worth the savings. Some attempts to reuse rockwool slabs have not been successful. One potential problem has to do with irrigation management and Pythium root rot potential. If slabs are not well sterilized, Pythium root rot can be a problem in the second crop. Reused slabs also contain considerable organic matter (old roots). The organic matter might cause the reused slabs to stay wetter early in the season for the second crop. If roots for the second crop become waterlogged, root rot can become serious.
When media is discarded, it should be disposed of properly. Certain media could be ground up and used in potting mixes. Before doing this, the media should be tested to be sure it is free of pathogens that might cause problems for the crop to be grown in the mix.
Another disposal mechanism might be to remove the covers, spread the slabs on a crop field, and till the slabs into the soil. Rototilling breaks the slabs into small pieces and the fragments are unnoticeable in a year. Loose media can be emptied onto the soil in a field and tilled in or can be used in soil mixes for landscaping.
After the greenhouse crop is finished, the irrigation supply lines should be cleaned and readied for next season. In most situations, fertilizer deposits and lime scale can be removed by acid cleaning of lines and emitters. Emitters should be removed from the media prior to acidification (if media is to be reused) so that acid will not destroy the media. A 1% solution of acid, phosphoric or sulfuric, should be sufficient to cleanse emitters. After acidification, lines should be flushed.
Costs of Production for Tomato
A recent analysis of costs of production for tomato in coco fiber was conduction by Athearn et al. in 2018 for Florida. These workers found that the initial investment and annual noncash costs were $58,860 and $6,933, respectively with annual cash costs of $3,975. Total variable operating costs were $14,045 for a greenhouse containing 640 plants. High yields and a price of at least $2.50 per pound were shown to be needed for profitability. These figures are nearly three times those for the 1990s decade.
Athearn, K. R., R. C. Hochmuth, W. L. Laughlin, and J. L. Clark. 2018. Economic analysis of small-scale tomato production in Florida. Proc. Fla. State Hort. Soc. 131:99–102. 2018.
Additional Literature
Florida Greenhouse Production Handbook. University of Florida Extension. https://edis.ifas.ufl.edu/entity/topic/book_florida_greenhouse_vegetable_production_handbook
Appendix 1 - Fertilizer Formulas and Programs for Florida Rockwool and Perlite Houses
Tables 2 and Table 3 give general reference information for handling dry fertilizer materials. Table 2 is a list of approximate weight equivalents for dry measures of eight fertilizer ingredients. Table 3 gives handy equivalents between the weight of a nutrient and the parts per million provided when it is diluted 1 to 100 in a 30-gallon tank.
Tomato Nutrient Solution Formulations
Following are four fertilizer recipes that have been successful in Florida rockwool houses. More detail on fertilizer management for rockwool- and perlite-grown vegetables is presented in "Nutrient Solution Formulation for Hydroponic (NFT and Rockwool) Tomatoes in Florida" (https://edis.ifas.ufl.edu/CV216). These nutrient solution formulas work equally well for rockwool and perlite.
- Recipe 1 (Table 4, Table 5); Stock Solutions and Final Concentrations
- Recipe 2 (Table 6, Table 7); Stock Solutions and Final Concentrations
- Recipe 3 (Table 8, Table 9); Stock Solutions and Final Concentrations
- Recipe 4 (Table 10, Table 11); Stock Solutions and Final Concentrations
Appendix 2 - Estimated Construction and Operating Costs for Rockwool or Perlite Tomatoes
Table 12 and Table 13 present estimated costs to construct and operate a greenhouse for rockwool or perlite tomatoes. The house is a 120 by 35 foot house containing 1100 tomato plants. Labor costs are assumed as $5.25 per hour. Some of the cost estimates below were adapted from SVAREC 91-20 report by Hochmuth and Belibasis which deals with NFT. The major differences for costs between NFT and rockwool solid media systems are:
- No need for concrete floor with solid media systems.
- Less construction labor for rockwool or perlite house due to lack of need for concrete floor.
- Less operating labor for solid media due to automated irrigation system.
- Slightly more cost for irrigation system with solid media.
- Need to replace solid media.
In the final analysis, the total costs for NFT and solid media houses are very similar. The major difference is consistently high yields from rockwool or perlite compared to NFT with PVC pipe. This makes profitability with rockwool or perlite more consistent.
Appendix 3 - Partial Checklist of Equipment and Supplies for a Perlite or Rockwool House
I. Pump and well
II. Greenhouse structure
A. Galvanized pipe
- Side wall columns
- Arches
- Endwall frames
- Purlins
- Heater hangers
- Braces
B. Aluminum extrusion
- Arch poly locking
- Base board poly locking
- Eave poly locking
- Cooling pad cover poly locking
- Endwall cross members
III. Environmental control
A. Heating
- Two furnaces
- Jet fan and plenum
- Heat distribution tubing
- Inlet shutter for jet fan
- Heat retention cloth
- Thermostats or control system
- Furnace ventilator stacks
- Fuel tank and hook-up
- Temperature alarm
- Thermometers
- Electric generator (backup electricity)
B. Ventilation
- Exhaust fans (slant-wall) with shutters
- Attic exhaust fans
- Cooling pad and delivery and return system
- Cooling pad sump tank, pump, and float control
- Motorized shutter vents
- Thermostats or controller
- Insect screen or cloth
C. Shading System
- Airplane cables, eyebolts, and tighteners
- Shade cloth (20 and 30%)
- Pulleys, grommets, etc.
IV. Greenhouse coverings
- Polyethylene cover (roof, side walls) (double-layer) and inflating blower.
- Endwalls - fiberglass, polycarbonate, etc.
- Poly patching rolls
- Foam sealant
V. Entrance porch
- Concrete floor
- Covering - fiberglass
- Wall framing-pipe, aluminum, or wood
- Doors
VI. Contract services
- Electrical (lights, wiring), at least 100 AMPS
- Plumbing - well
VII. Greenhouse floor
- Sand, concrete, site prep.
- Framing for concrete
- Leachate trough system
- Plumbing
- Nursery cloth
- Black-on-white poly
VIII. Irrigation
- Proportioners
- Water supply-check valve, filters, pressure regulator
- Black poly distribution tubing (1/2 and 3/4 inch)
- Emitters
- Irrigation starter tray
- Relay box and wire
- Controller and solenoid
IX. Production supplies
- Rockwool slabs or perlite lay-flat bags (2 to 3 plants per container)
- Transplant seeding cubes and blocks, and trays
- Seeds
- Trellis lumber, posts, cable, and tighteners
- Trellis twine
- Soluble salt meter and standard solution
- Pollinator
- Plant clips, tapener machine, and tape
- Light meter
- Fertilizer stock tanks
- Mist blower sprayer
- Fertilizer, chemicals, and acid
- Spray suit and safety equipment
- Harvesting buckets
- Scales-measure fertilizer
- Record book
- Insect monitoring yellow sticky cards
- Pruning shears
- Heating fuel
- Vacuum cleaner
- Copy of the "Handbook for Greenhouse Vegetable Production in Florida"
Table 1. Suggested spring shade management scheme for the two-cloth shading system for Florida.
Table 2. Approximate weight (grams) for several measuring utensils.
Table 3. The ppm of a specific nutrient provided by a specified amount of a particular fertilizer material for a 30-gallon stock tank and a final dilution of 1:100.
Table 4. Recipe 1 - Tomato Nutrient Solution Formulation; Stock Solutions
Table 5. Recipe 1 - Tomato Nutrient Solution Formulations; Final Concentrations
Table 6. Recipe 2 - Tomato Nutrient Solution Formulation; Stock Solutions
Table 7. Recipe 2 - Tomato Nutrient Solution Formulation; Final Concentrations
Table 8. Recipe 3 - Tomato Nutrient Solution Formulations; Stock Solutions
Table 9. Recipe 3 - Tomato Nutrient Solution Formulations; Final Concentrations
Table 10. Recipe 4 - Tomato Nutrient Solution Formulations; Stock Solutions
Table 11. Recipe 4 - Tomato Nutrient Solution Formulation; Final Concentrations